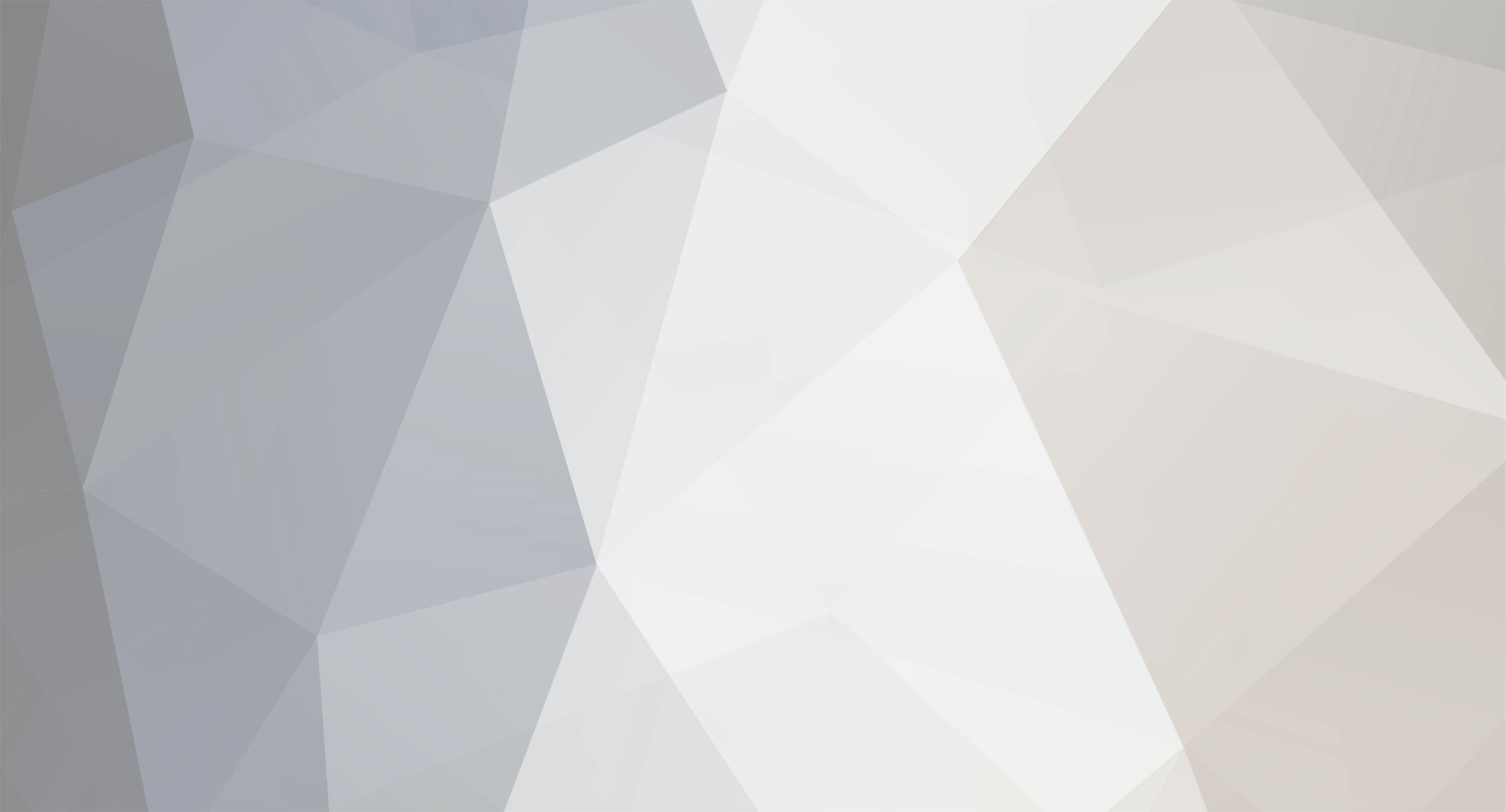
RHayes
Members-
Posts
61 -
Joined
-
Last visited
Recent Profile Visitors
The recent visitors block is disabled and is not being shown to other users.
RHayes's Achievements

Member (3/5)
11
Reputation
-
Insulate the void and then use a chipboard system like the Ambiente Jo Floor. This is the best on build up with your system as the existing 20mm chipboard is replaced with their jo floor system which is just 22mm plus 6mm over board. Alternatively use the Ambiente AmbiDeck 20 pro. Its 20mm insulation board so helps on floor insulation and its with 16mm pipe so ideal for heat pumps and has a very good output. I am sure you won't be disappointed in the system and I'm very confident that it will be cheaper than a rad system. Quantity of insulation and effectiveness of UFH is not linked. You don't have to have a certain thickness of insulation for UFH to be effective, I've got a very effective system at my house with just 50 EPS polystyrene between joists just like this and the system works beautifully.
-
Sounds like you have tried most options and with mains pressure flushing through I normally recon to get 5plus litres per minute when flushing a loop. That is with 17mm pipe mind and i guess you have a 10 or 12mm pipe being an overlay system so 4 may be more realistic. Have you tried removing the flow meter to see if there is annything stuck in there. If you can disconnect the loop first below the flow meter so that any debris that may be caught in the flow meter doesn't disapear down the loop when you remove the flow meter then I'd advise that. Otherwise not sure what else to suggest. Perhaps run that one loop by itself with heat and then trace the loop with a FLIR see if you can spot a kink or restriction? Not that it will help if you don't want to take the floor up but it may provide the answer to the problem.
-
Underfloor heating in Victorian terraced house
RHayes replied to Anthony Crown's topic in Underfloor Heating
Just run the DPM up the wall by 150mm. Done this on many jobs inluding my own place which has a highish water table and no issues. -
Agreed, pipes are robust but you'd be supprised what happens. The principle behind pressurising it (whether air or water) during the build is that you will be able to tell where it comes from as soon as it is puncture, either by escaping air or a pool of water. That way doing further testing down the line which isn't always as easy as hot water and flir isn't needed, even if you do deal with it at a later date. Anyway, why not leave it under pressure. Nothing to loose as far as I can tell.
-
Agreed, but still best to put under pressure at least when building, if not all the time.
-
A 2 port zone valve (motorized zone valve, there are a few variations of name for the same thing) does the same thing as a manifold actuator but is is for the whole manifold and goes on the pipework feeding the manifold. They will also have a micro switch on the that switches on when the valve is fully open and this can inturn trigger a pump or the boiler. If you don't have actuators on the manifold serving the main area then you will definatly need a zone valve for that manifold otherwise you will get heat to that floor when anything else is on. I recomend them for both manifolds to extend the life of the actutors on the manifold. Without it the actuators will be trying to hold back flow when just the main area is calling for heat and over time this can weaken them and you get water creeping past and heating rooms that don't need it. Would be good to know what the build up of the floor is and also the floor finish. We use armaflex insulation tape or a similar product to cover our pipes. I did an output excersise once and be aware that this was approximate as there aren't any approved figures on this, but using the surface temperautre after the insulation as the water temperature and plotting a graph of the tried and tested systems at different pipe centres, I reckon that with both flow and return insulated at approximately 50mm centres, this would give you the same heat output per square meter as 150 centres un insulated. I personally recomend doing the best you can to route pipework along different areas to reduce congestion and then insulating both flow and return transit pipework at least where there is congestion of more than 2 loops/4 pipes but why not all of them, it means the heat is being retained in the pipe until it gets to the room it is suposed to be heating.
-
@Russell griffiths agreed that the likely hood is low, but not zero. Nothing is impossible and in my book it is very bad practice not to leave the system under at least working pressure if not 2x working pressure. Screeders, other trades anything could happen to those pipes and they should be pressuretested and left like that until finaly flushed and filled for operation. Pipes can float if pressure tested with air (or don't have water in them) if it is a flow screed, however providing you have clips that have a good hold of the insulation at least every 300mm i expect it to be okay.
-
agreed, fit them its a lot easier to remove o deactivate than install retrospectively. Re a thermostat that is designed for a bathroom, concider the following. 1. If the thermostat is mounted in side the bathroom it will need to be battery powered or low voltage 2. If the thermostat is mounted outside the bathroom i'd advise having a air or floor probe to measure the temperautre inside. 3. A floor probe anyway would enable you to measure and control the floor temp, meaning you can be sure of having a warm floor for your bare feet unlike if you were measuring/controlling air temp.
-
Heatmiser Neo do a thermostat system where you can link a wireless battery powered probe. https://heatmisershop.co.uk/heatmiser-wireless-air-sensor/ I beleive you will need a thermostat- https://heatmisershop.co.uk/heatmiser-neostat-v2-programmable-thermostat/ and a neo hub https://heatmisershop.co.uk/homekit-enabled-heatmiser-neohub-gen-2/ There will be cheaper options im sure on other websites and with that Hub you can add extra thermostats to make your whole heating system smart Just a thought from what I have experiance in.
-
@JohnMo Understand and not saying it is safe, but a properly installed job is what we're looking at.
-
Why do you need to stretch the piep wall at 10 bar? Is this for a particular pipe or what. Would like to understand the principle of this. I know the risk of air test but again if you've pressure tested to a higher pressure and then dropped to 4 bar, if something still blows then its a poor instal. We've pressure tested our systems with air for most of our 18 years in UFH.
-
Morning Nice place you have there. I totally agree with your request to put the manifold serving the main area on the wall oposite the the fish tank and pipes running under that. However this is assuming you are going to have fish that are possibley of tropical origin as your fish tank will get rather warm (unless it isn't floor standing). Fish tank asside this would be a much better option for the hallway which has a massive bunch of pipes on that end. Also with that 1 manifold being controled by one thermostat you won't need actuators. Just a 2 port zone valve before the manifold which i'd recomend installing 1 for both manifolds anyway. The other thing I would recomend strongly is a separate loop and thermostat control for your master en-suite. Like they have drawn it will mean you don't have heat to the en suite without the bedroom being on and you can't have different temperatures. Also if you do put a thermostat for the en-suite id recomend having a floor sensor in the floor as then you can be sure of having a nice warm floor for your bare feet. If you just base this on room/air temperature you can't be sure of having a warm floor. I'd combine the 2 loops for the hall way to give you the spare port for the en-suite that way you haven't increased the size of the manifold. As to having both manifolds in the same place, this is an option (left hand wall) and then runn the pipes for the main area straight across and under the fish tank. This would remove the need for a separate loop in the plant room (if the need was there in the first place) as the plant room will be pleanty warm enough with both manifolds in there and you don't necessarily need an evenly warm floor in a plant room. What size pipes is being used for the UFH loops? Just a few thoughts. I'm sure there will be others and different points of view.
-
Thanks @vala I would be interested in the Grant temperature difference controller as I am due to be doing something similar at my place (when i have some spare time to finally set it up - ha ha).
-
Underfloor heating and hot water priority - potential issue?
RHayes replied to Jon C's topic in Underfloor Heating
Hello @Jon C, looks like the top pump is on the return leg judging by which side of the bypass valve is connected. I can't workout where the bottom red pump connects to. Hot water priority is typical with a heat pump so i expect you do have this set up. Regarding whether the pumps should both come on or not depends on what they are leading to. Not so easy to tell in the photo but it does seem like the bottom pump is on the flow and the top pump is on the return. I can only assume this was done this way as the pump duty was too much for the one pump. If the 2 port motorized valve for the UFH closes when the hot water comes on then there must be something that intercepts the signal from the UFH stats when the hot water comes on. The issue is that this doesn't then tell the UFH manifold pump to close and therefore it is effectively pumping against a closed valve, and can show a small increase in pressure gauges. To resolve this the grey and orange (micro switch) on the UFH zone valve will need to connect back to the UFH wiring centre (I assume you have one) to de energise the pump at the manifold. Do you have a UFH wiring centre? It should be possible to de energise the UFH manifold pumps this way but will be much more difficult to close all the valves too.- 3 replies
-
- underfloor heating
- heating system
-
(and 1 more)
Tagged with:
-
NRVs would only be required to prevent pumps pulling from other zones. For example the radiator pump pulling water back up the flow to the underfloor heating. However this is not likely to happen if you have zone valves for each cicuit. I would recomend putting zone valves for each manifold. This helps prevent the above happening without NRVs and also extends the life of the UFH manifold actuators. Most UFH wiring centres have a terminal for the zone vavle and therefore is often easier on the wiring to instal zone valves local to the manifolds