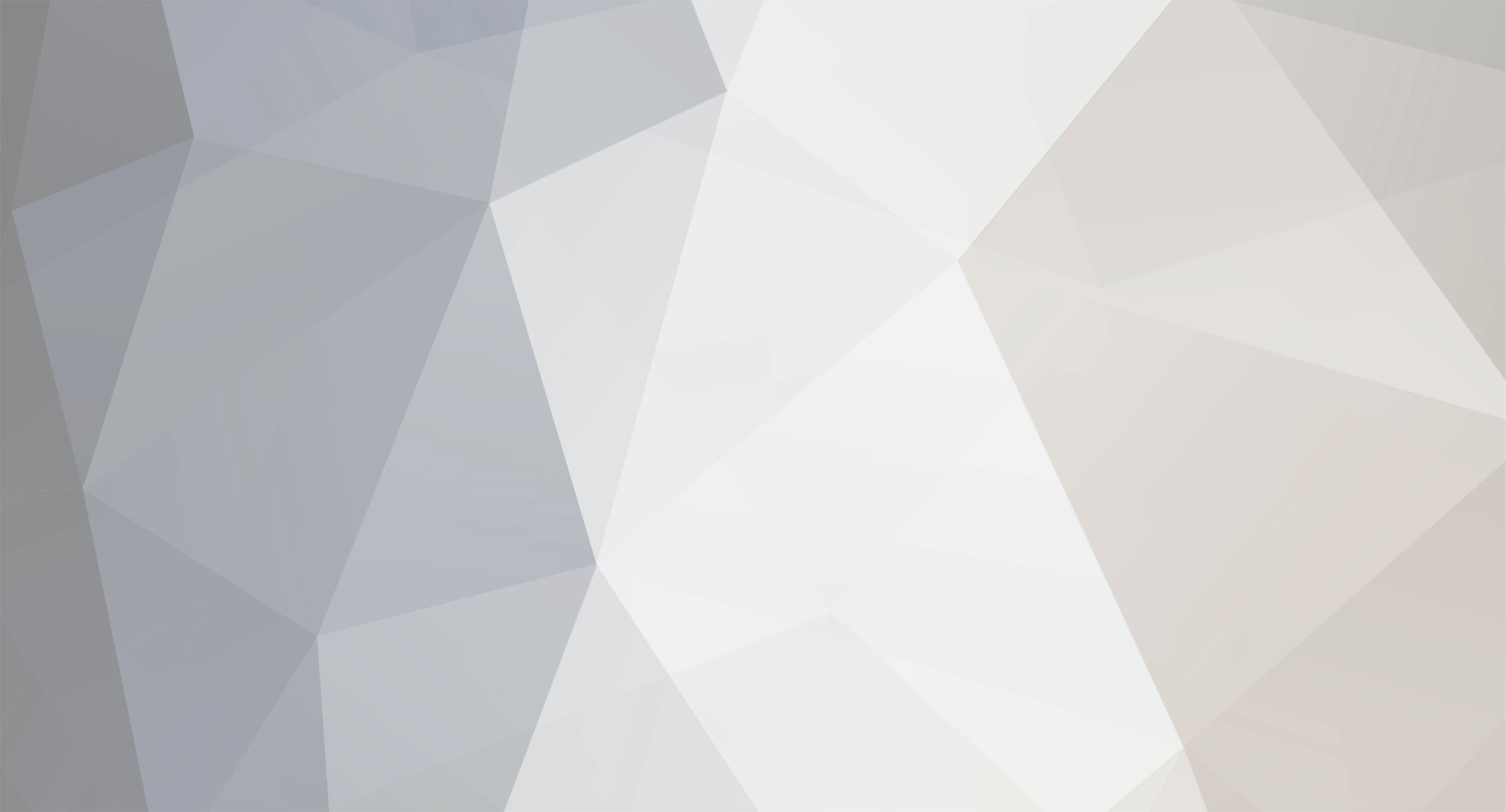
Makeitstop
Members-
Posts
321 -
Joined
-
Last visited
Makeitstop's Achievements

Regular Member (4/5)
78
Reputation
-
Thanks for the input guys. Interesting range of view Seems ally clad timber is the apparent choice if cash has recently rained a foot thick into our gardens. I see pvc features too, and that doesn't surprise me. Having read a bit of late, it would seem that pure aluminium isn't what many would lean towards. Questions around poor frame values seems to come up a lot when aluminium framed products are discussed, and I cant say that surprises me. From my own experience of doing a rear extension and fitting of Raynaers products, the level of condensation is simply unacceptable. Yes, it may well be in part due to install, and also, somewhat due to it being a kitchen with an occasionally elevated relative humidity to what might be the ideal, but, from past experience with pvc framed products, never have I noticed condensation as bad. It's massively frustrating. My question was simply to gauge what the good folks on BH thought to it, as I have been discussing this subject with son in law, in relation to an upcoming major rear extension to a late Edwardian house. Budget is a constraint (as it often is) but a sound choice is essential I think. My advice has been....... give pure aluminium a miss.
-
Thanks all. Blimey Mike, 1st choice there would hurt the pockets. Why never pvc? Steamy... never heard of grp in window frames, is it used? What would you choose? Nod, yes I get that re: your own selection. Ally is so expensive, and I'm not sure what the real world advantage is when sizes can be Don in alternative materials. What did you use and are you happy with it?
-
Jimbob, will you share what product you are referring to? No need to name business or company that supplied or fitted, just the product. No worries if not.
- 18 replies
-
- condensation
- windows
-
(and 2 more)
Tagged with:
-
Hi all. OK, so the question above is aimed at frame material for windows / doors, and, whether any future choice would be wood, pvc or aluminium framed products, whether they be double, triple or whatever glazing. This is obviously for products of the kind of dimension that all materials could handle, so no 20ft high mega sliders or suchlike. Thoughts, and why?
-
Well, I have to admit, my own, fitted in a kitchen / diner / living space of approx 40 sq metres, "does" suffer from condensation on lower part of frames. Now I appreciate that the relative humidity in this space can sometimes be above what might be ideal, but the level of condensation when it's very cold outside is quite startling. I have been pretty disappointed tbh. I have wondered whether the construction at the openings was adequate. It seems it may not be. The structure is cavity wall, of brick outer, 30mm clear cavity, 75mm pir and aerated block inner skin, with dabbed plasterboard and skim. The aerated blocks were returned at openings for window / door, with 30mm pir sealing cavity. I did question whether this was a smart choice and was assured it caused no issues using thermally broken aluminium framed products. That might have been utter bollocks, but I was unsure what to push for as an alternative. I appreciate that the standard of the above is not as good as it could be, and the initial plan was for wider cavity and concrete block internally, but this changed for reasons I wont go into. I haven't been thrilled with the performance of the Reynaers product on a thermal basis though. Frames feel freezing cold when it's very cold outside.
-
LVT flooring vs others - rough £ m2 supply and fit?
Makeitstop replied to LaCurandera's topic in General Flooring
Depends what lvt I guess though. -
Oops, hadnt read this, sorry.
-
Are you sure that not 7021? That's a dark grey that looks kind of "black..ish" but certainly isn't when you put a true black against it. 7016 is anthracite, and is more of a mid blueish / grey and nowhere near as dark as 7021
-
Can you tell me about brushed/rubbed wood finishes?
Makeitstop replied to Adsibob's topic in General Joinery
If you have a hard wax oil finish and would like it to have a "slight" sheen to it, you could try a white 3M scothbrite pad, on an inconspicuous piece to see how much it brings it up. As mentioned above re: burnishing, there is minimal abrasion to using a white pad and this will burnish the surface to some degree. -
Roger Bullivant Arsleff Van Elle Foundation piling All larger outfits and will know what they are doing. There are dozens of smaller companys of varying abilities from what I've gathered, and knowledge, experience and reliability can be variable, as can costs. One smaller outfit I was recommended towards was a company called Westbuild piling. While I didn't use them for my own needs, I found them useful and responsive to my enquiries.
- 1 reply
-
- piled foundations
- piling
-
(and 1 more)
Tagged with:
-
Maximum length of different worktop materials
Makeitstop replied to Post and beam's topic in Kitchen Units & Worktops
Yes, I'd say the quartz and sintered products like dekton are about as long as they get, which is approx 3.2 metres. -
Gripfill. Once stuck down, absolutely solid.
- 1 reply
-
- 1
-