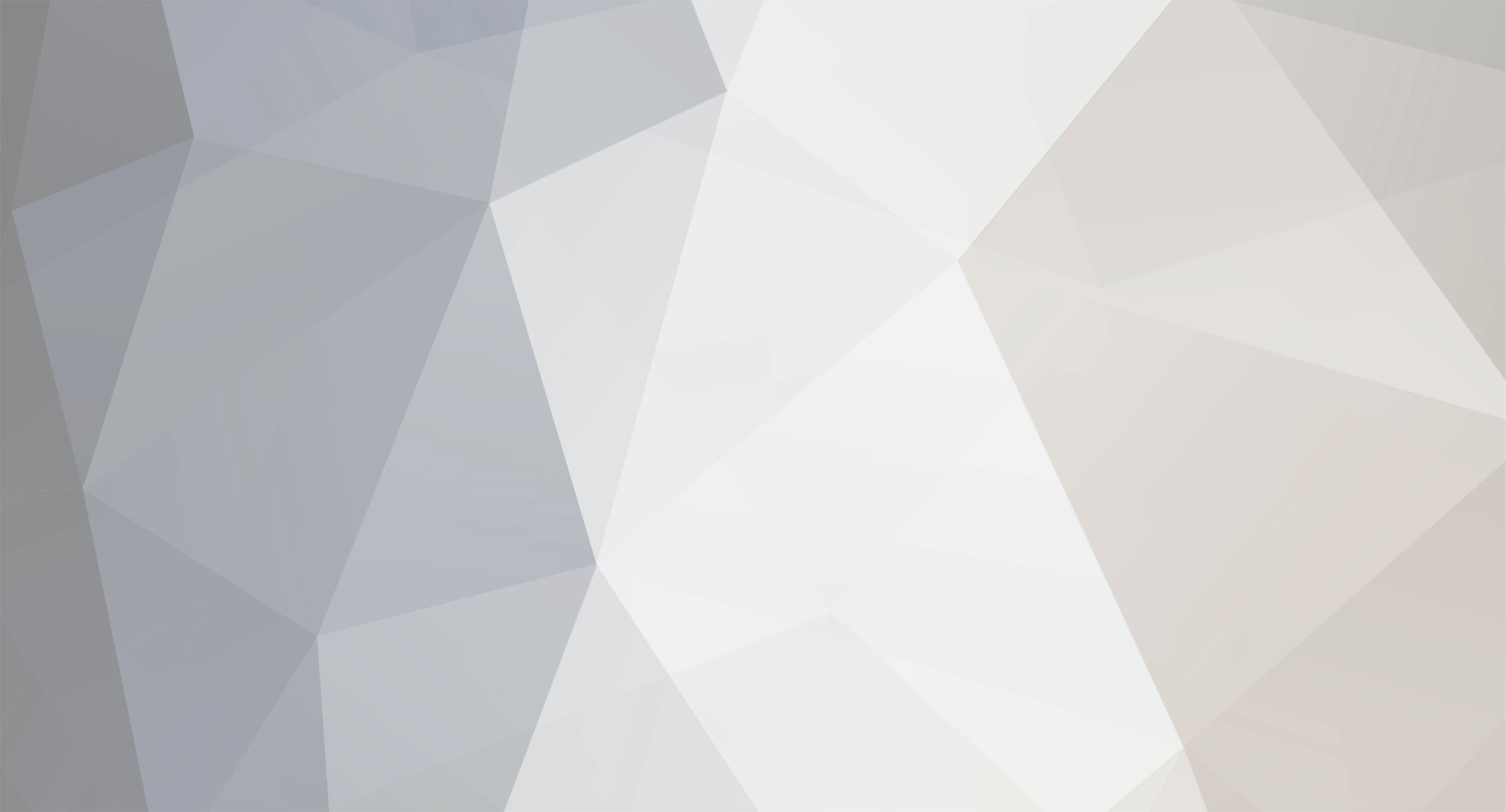
Gus Potter
Members-
Posts
1880 -
Joined
-
Last visited
-
Days Won
20
Gus Potter last won the day on March 30
Gus Potter had the most liked content!
About Gus Potter
- Birthday 09/20/1964
Personal Information
-
About Me
Signed up after having reviewed the questions, comments and responses. Very refreshing and positive. The enthusiasm and knowledge of the contributors to this site is infectious!
-
Location
Near Glasgow
Recent Profile Visitors
8263 profile views
Gus Potter's Achievements

Advanced Member (5/5)
1.2k
Reputation
-
Love this. Ok, first thing is if double glazing often the spacer bar will have a mark and date with the BS code, sometimes the year of manufacture of the unit. So you can bench mark that with the historic U value of the unit. If you can find that then we might explore more.
-
Wall for floating staircase?
Gus Potter replied to flanagaj's topic in General Self Build & DIY Discussion
@flanagaj That was a bit of tough love but go for it if you can. Post more info and some drawing details and if I can help I will, for free! Others will chip also as there are folk on BH that know about this stuff, have construction experience "boots on the ground" but are reluctant to post in case they get a slagging. To be blunt you have access to a great resource on BH so you need to give a bit to get something in return. Your floating stair really interests me and I would love to help but I'm not going to do that unless you share enough info that other BH members can benefit from. Just maybe you'll get some tips and you can go back to you SE and say.. I've read some stuff on BH and here is how you design it.. what do you think? -
Wall for floating staircase?
Gus Potter replied to flanagaj's topic in General Self Build & DIY Discussion
That is a good honest response from you SE and I often wish for this where folk say "it's not my bag" . As an SE from time to time I'll say the same, I don't have the expertise to take on this. This is a condition of our SE registration. To provide a bit of cost context to this, say you came to me and said would you, Gus design and sign off on a floating stair? I would first want to have a look at your drawings and see if there is a fighting chance of making something work. I would charge you £200.00 quid for that as there is no free lunch. If I think, yes I can make that work then the calculations are pretty straight forward if using natural stone, but if concrete they are not as you then need to design and detail the rebar which is a lot of work as you have torsional effects. The main part of the work is in the drawing detail and making sure you as the Client don't cut corners and that the drawings specify the construction sequence. I have to do that as if you cock it up you will might want to take me to court! My proposal is. If you want to pick my brains then you need to pay for that. I'll then walk you though and discuss how we might go about designing,constructing it in a buildable way . Then I will be able to give you a fee quote based on us working together. So long as you pay me a fair rate for a fair days pay then that is reasonable? -
Ok, that sounds like a valid reason. You have a height restriction. That's flag if they can't take this in their stride then oh dear! Radon is assocaited with granite rock. My gut feeling is that you are not paying your SE enought. Phone them up and have a frank conversation. Don't be afraid to step on your Architect's toes. Just say they ask you for an extra two or three grand to hold your hand. All they need to do is to save you a week of two men's skilled time on site + expenses. And how much are you going to spend! Then she should have told you to be the bad ass and knock heads together.
-
Agree John. There a loads of folk that use ICF as self builders and sometimes I look at ICF designs and think.. that does not stack up cost wise. It's forgivable as often folk convince themselves that it's right for them, but with my hard nosed hat on I know that's not the way I design as I can see it more expensive. But other times ICF is absolutely the right way to go. As a designer I often look at projects and think, how can I get this built at the budget? It takes experience, it's not that hard though. One of my key principles is to understand the Architectural design intent, identify what is important in terms the Client requirement, what matters to them, and then check to see if that fits with the planning requirement. That's the way I design as an SE and general designer. The big problem is that folk just don't want to pay for this skill. One skill a good SE should have is to be able "knock heads together" , bring discipline to the design process. Architects are not good at this in general. Because that is a Client requirement, what is wrong with realising your dream to have something that is different and a wow factor. Now fair enough, it might turn out that the detailing and buildability is going to be prohibitive cost wise but you have to explore all the design options. In summary folks if you are thinking ICF also look as how much extra performance you get out of it for a bit of extra rebar. It's almost free money!
-
A basic DPM gives you basic protection, it's taped anyway to stop damp. Where are you building? Why are you replacing the existing concrete slab? Myself and @saveasteading often look to see if we can retain the slab with a bit of clever engineering. You should by this time have an SE fully on board giving you practical building advice and showing you where the costs lie in terms of buildability, working closely with your Architect, guiding them and encouraging design discussions.. unless you want to lose money.
-
This is interesting from a design perspective. I clocked this as it's a good span in ICF.. and then we have a steel beam. My thought process is roughly as follows: ICF is basically an insulated reinforced concrete wall with insulation. Reinforced concrete, if you have a decent height of concrete over an opening can be really efficient structurally. The wall can't be too thin but say it's "normal" 150mm. We don't know what the loads are from above but the 457 deep beam is likely designed for deflection (critical design condition) rather than strength. So the SE has introduced steel. But I then think as designer.. what about fire protection, insulation detailing, cold bridging, insulation fixing to the steels, differential movement between the materials and impact on the external and internal finishes and buildability. All that is going to add to the cost. This is where you really need to think things through. Scenario.. often the SE, (after Grenfell) will pass the fire protection to the Architectural Designer and then they will put some random note on the drawing for the ICF folk to make it work and they will pass it on to you as the Client.. you see the problem? My gut feeling is to understand why you need steels. If you have a two story building then sometimes we can hang the beam over the door from the ICF wall above, even if there is a modest window above. If only single story then is ICF the right solution? And 8.4 m door is going to be big bucks so head deflections are critical. To finish. Your design team need to get together and say.. this is a big area of moving glass so let's start to talk to each other and produce a well thought out design. For the technical minded: On concrete buildings we can use a principle called a Vierendeel girder where we look at the whole wall say on a two story building. This is where ICF has advantages over say a timber frame. If it all looks good SE wise you then need to make sure someone can built it and ideally save money. Again the SE stuff for the steel is probably straight forward but the detailing is where is could all fall to bits. ICF is simple in this respect.
-
You kidding me? £383 for two dumb conditions
Gus Potter replied to Alan Ambrose's topic in Planning Permission
Ok in the round you can look at this in a few ways. But one is that the planning and building control function subsidises other public services. A BC officer told me that BC make a profit but that gets "hived off" to pay for other "stuff" that you may not have voted for at your last council election. To be fair, if you are going to pull folks trousers down you need to tell them what needs to happen to be able to pull the pants back up. But they don't even bother to tell you that. -
Hi Steamy. I've written a PM to you but can see you have PM's turned off. Can you PM me with your contact details? Gus
-
Much of this is above my pay grade.. but as an SE I can report the following: I'm using it as a tool to give me prompts in SE design. Prompts can be; suggestions and links to research papers, design code links and so on. This saves time thinking.. I have this info but can't find it in my large library of info. I always check the facts. I tested AI against some basic beam design, then pushed it a bit, chucked in some geotechnics.. which is a dark art. Again it served up a template that a student SE would get taught at uni. But it fell short of what is required of an SE which is the "art and craft of design".. but it still saved some time. I then thought I wonder is AI will write me some VB code (not just macros) that lies behind some of my excel spreadsheets and it made short work of that. If I have the will to live I'll ask it to write the VB code in excel that does a structural stiffness matrix which includes deflection. I wrote this a while back in excel for myself so I could check commercial SE software. I other words.. write me a basic frame analysis package in excel. Now you have a free basic SE frame analysis package! My better half is using and pushing AI a lot in complex areas and getting good results. For me, if you look at Grok it seems to be doubling in power every 4 to six months. That said, I feel AI is milking me for my craft so am wary that when I go off piste as an SE I'm in no hurry to give away my secrets avbout how you actually execute the art and craft of design.
-
Welcome to Buildhub and well done for posting a great question. What you have is a little different. Is your house circa 1950 to 1967? Here, after the war there was a drive for "non traditional construction" and the house builders were experimenting with leaner design. Conner, good spot! Agree with Conner in that this tie could be holding the external wall head in place and the toothing is there primarily to turn the internal wall into what we call a shear or racking wall. I can't say much more at the moment but if you want post a photo of your external elevation and put a line on it where you want to take the wall down that would generate more comments that might help you. Also changing the size of the opening in the external wall will lickely have a marked effect on the wall stability.
-
Tall upright radiator efficiency
Gus Potter replied to BotusBuild's topic in Central Heating (Radiators)
I think it's debatable. Both a low or tall radiator will still set up similar convection currents in the room. My own view is that the position of the radiator is more important and in a principle room appearance and position of the furniture will often lead to a compromise. Ok for a bit of fun to size a heating radiator system in the old days (35 years ago) when I was a building contractor .. still can apply when at the ball park quote stage. To get the customer interested I used to take them round the house and say... Imagine you had a one bar electric fire in this room ( 1.0 kW) or a two or three bar fire (3.0 kW) working on and off. Think of your Grans house. In this day and age we can use the equivalent of a fan heater. Most folk can relate to this. You run round the big rooms and as you go you say.. hey big window here and a draughty door say in a big hallway. You want to be able to make this room nice and hot if feeling like a duvet day? Now you add that up and with a bit of experience you can feel for the size of heating system you need. As an SE I use rules of thumb to size floor joists and steels and this is no different. OK so you now have a well insulated modern house. Take the above preliminary size and half it as condensing boilers work better at lower return temperatures. -
Fill your roof with in-roof PV panels instead of pantiles?
Gus Potter replied to Alan Ambrose's topic in Photovoltaics (PV)
Go for somewhere in between. Think maintenence and roof penetrations. Where you have eaves you need to think about roof access (and gutter damage) , something solidish to stand on. Verges, keep away from them as any disruption here can cause the roof to leak. Think about what service penetrations you might want in the roof. This could be a soil vent stack, any fan vents and so on. Keep a good margin around thec penetration flashings. If using tiles then think about the tile width so you don't end up with a funny width of tile.. the detailing is going to be hard and it gets harder when you have fewer tiles between the panles and the verges as there is less room for adjustment on the width as you lay them. Be careful folks as if you have not thought through the detailing and maintenence cost (risk of breaking things when you go on the roof) then it will come back to bite you. Remember that your house will not go up perfectly plumb as it will get built to a tolerance. -
Local topography can vary a lot. On my self build, Qouthquan, near Biggar we had Tinto hill and the upper part of the clyde valley that would move the "local" weather about. Yes, you will get a lot of different weather, four seasons in one day. You will no doubt be appreciating how dynamic the weather is at your house, but one thing... it's not boring! Parts of the south do seem to be suffering from a long term decline in the main aquire level. That said it could just be that the performance of the borehole has dropped off, got clogged. Some boreholes don't last forever and that I suppose has to be factored into the long term (maintenence) cost when buying a house with a borehole.
-
It's interesting. I hope I'm not identifying Kelvin's site but I've been there. About a mile or so down the road is a farm that I have a family connection to. This used to be a highly productive soft fruit farm and if you wander about you can still see the bases of the prefabs that armies of berry pickers would come to every year. The key thing is that this farm sits in the rain shaddow of the mountains but also the geography then further splits the weather and that doesn't get picked up even in the local weather forcasts. Go five miles further up the road and I think you would get a different output from your PV.