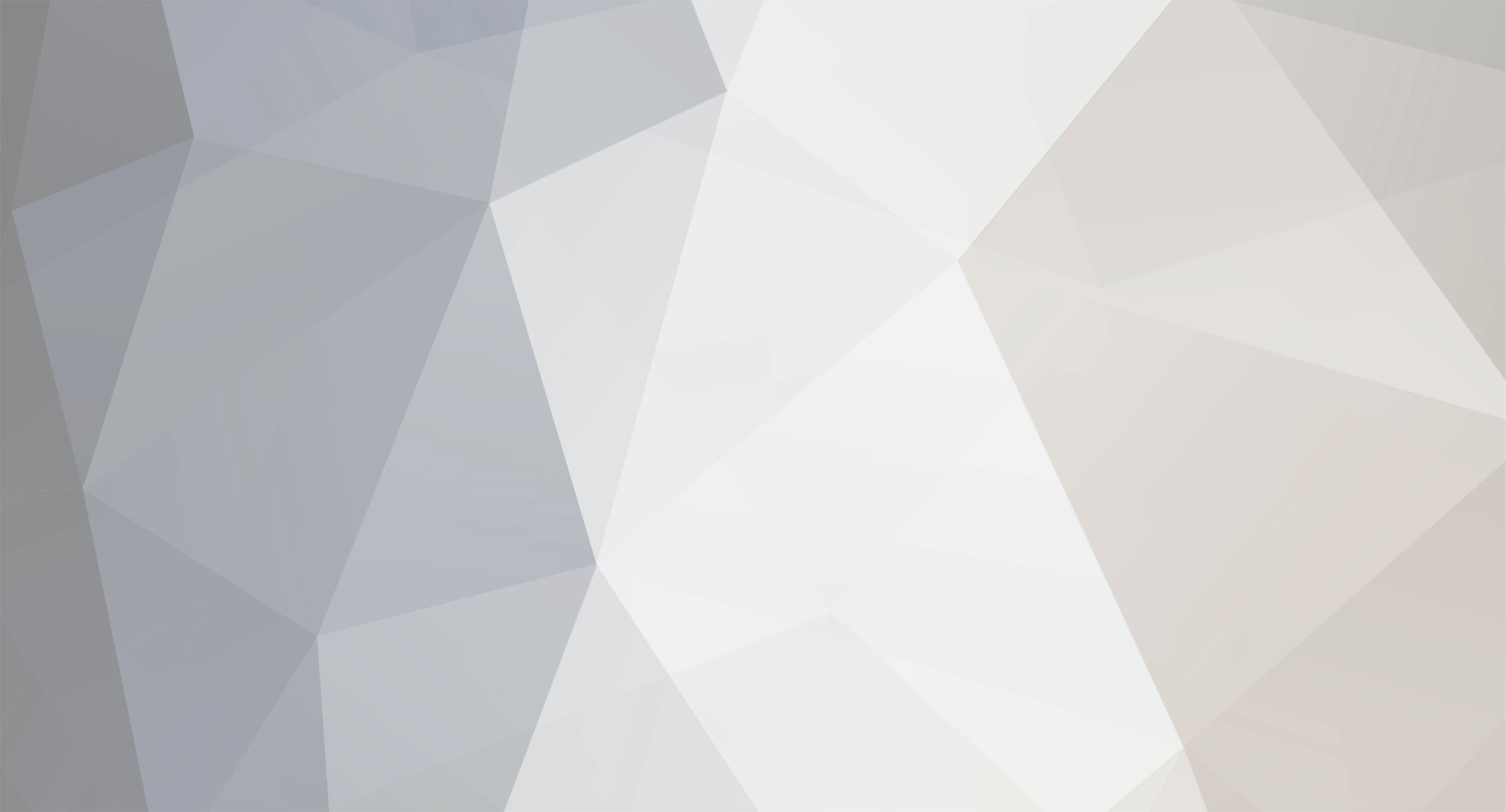
crispy_wafer
Members-
Posts
1030 -
Joined
-
Last visited
Personal Information
-
About Me
IT is my trade, Dad and husband,
-
Location
Lincolnshire
Recent Profile Visitors
The recent visitors block is disabled and is not being shown to other users.
crispy_wafer's Achievements

Advanced Member (5/5)
348
Reputation
-
Wall for floating staircase?
crispy_wafer replied to flanagaj's topic in General Self Build & DIY Discussion
Nice idea, yeah I'd run it past your SE for peace of mind, or even @Gus Potter might lend an ear for his thoughts. I cant help too much, because I've gone with central spine, however when time comes for manufacture, assuming you don't fabricate it yourself, don't be afraid to look up local fabrication firms and joiners for treads. -
downpipe at one end or in the middle of the run?
-
Leveling old ceiling with GypCeiling MF
crispy_wafer replied to Annker's topic in General Construction Issues
Would it be easier to just batten with 3*1 or 4*1, using the lowest spot as your zero point, and shim out the battens at the high spots. -
Wont lie, got two, one had to be swapped 4 times because of stone resin that had set on the underside of the drainage outlet that I wanted to use, I was unwilling to sand/grind it off incase I fubar'd the tray. The company I purchased from were first class in dealing with the issue for me, even though the tray had sat for 6 months or so without me unpacking or installing. This was the first time I'd actually rejected the replacements before they even got off the delivery van. All good in the end though. In terms of the tray, yeah it looks good, don't even notice it now!
-
Had the same issue - I ended up fitting a Kudos Connect2 tray to get me out of bother.
-
Ufh downstairs from the ashp, with separate ducted split ac, downstairs and upstairs - ducted AC in bedrooms, wet, or electric towel rads + electric ufh in bathrooms. Flexibility, heat downstairs cooling upstairs, or vice versa, cool in one bedroom warm in another… that sort of thing. How often this’ll be done though who knows.
-
MVHR and cooling
crispy_wafer replied to flanagaj's topic in Mechanical Ventilation with Heat Recovery (MVHR)
Not really following this thread too much, but if its a sales pitch, it's because it's true, air to water heat pump can heat as well as cool. They are designed to do just that, just like air to air. Customer just needs to choose a preferred method, make a choice of a wide range of emitter types for air to air, or mounted fan coils/underfloor for air to water system. In this country, it's more of a mindset and grant issue, rather than technological. Having one box outside is a cleaner/sleeker look, having two, gives some redundancy... -
I did Copper tails out of manifold to into hep couplers and 10mm sockets here. You can buy brackets like they use for UFH manifolds, cant see why this wouldn't work.
-
Wet plaster or dot and dab for my self build?
crispy_wafer replied to Berkshire_selfbuild's topic in Plastering & Rendering
Just sealing up of the blockwork, filling up the visible pores and sealing over the mortar joints of the inner face of blockwork with either a product called sound coat, or a sand and cement mix. Not needed if you go float and set (wet plaster). But if dot and dab its a secondary measure to cover your backside if the brickies haven’t been quite as diligent as they should have been. A couple of days labour for me and the mrs, but if paying someone I may have thought twice about it, doesn’t need to be neat! -
Wet plaster or dot and dab for my self build?
crispy_wafer replied to Berkshire_selfbuild's topic in Plastering & Rendering
🤣 I Parged, then I d&d because i didnt have anything better to do with my time. As above, ensure enough adhesive in the correct places. Work out your main hanging points so extra adhesive can be added here. -
Proper surround sound
crispy_wafer replied to Pocster's topic in Networks, AV, Security & Automation
Like what you’ve done there, save’s having to paint the ceiling I suppose. Pretty sure you can get sensors that mount horizontally, saves having to prop up that tile at the back. -
Proper surround sound
crispy_wafer replied to Pocster's topic in Networks, AV, Security & Automation
any good -
Not sure I’ve ever had a cupboard that I couldn’t see into,the only caveat I could think of is perhaps as above - under the sink, or those cupboards in corners where you may need to look round a corner if you didn’t want to open them up fully. So perhaps limited specific ‘that’s a good idea’ use rather than a blanket install.