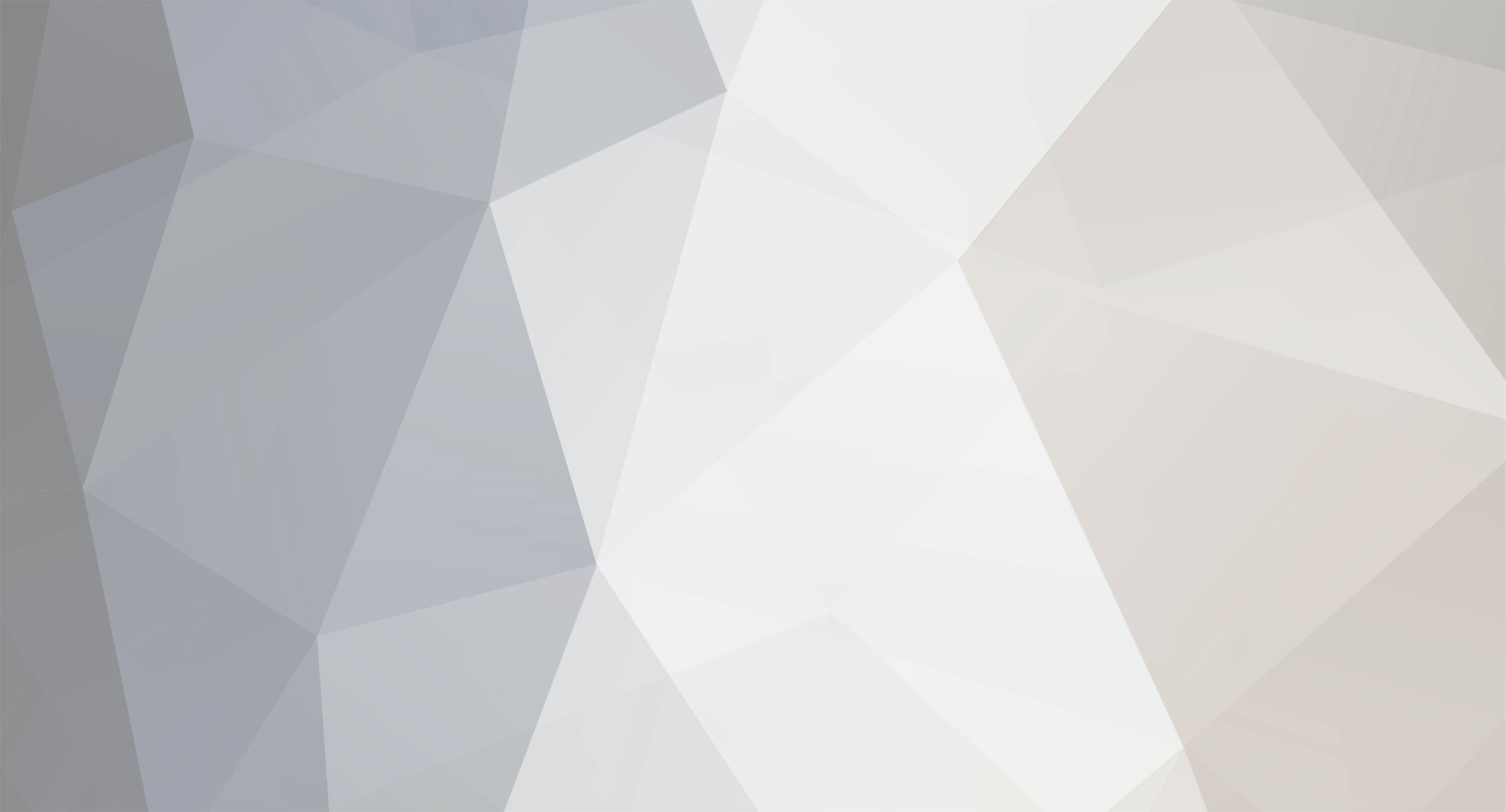
Alex C
Members-
Posts
250 -
Joined
-
Last visited
Personal Information
-
About Me
Check out my blog at www.passivehouseselfbuild.co.uk
Recent Profile Visitors
The recent visitors block is disabled and is not being shown to other users.
Alex C's Achievements

Regular Member (4/5)
85
Reputation
-
Yep paint the bottom edge before you install the skirting especially in kitchens and use a tiled skirting in bathrooms.
-
I imagine they would be best placed to answer that. 01535 650 770.
-
Rules for this sort of thing will change and may be dependant on other factors such as LTV. I definately did not have a minimum draw down with Ecology. They were very flexible but my LTV was very in my favour.
-
I would often email them in the morning and have the money in my account by the afternoon. No charges and no minimum transfer amount. Couldn't have been easier.
-
I think it was me. I drew down 10k straight off then used my savings before drawing down more months later. saved over 6 months interest on the full amount at the end of the 2 year period.
-
Any SAP assessor will surely be able to do a design SAP from Plans. Like @Bitpipe I needed one for ecology and did it myself but it would have been under £200 to get someone else to do it. When I got my mortgage Ecology wanted over 100, wich was perfectly manageable with a BMC build and 5.5kw solar pv.
-
In my slab there are 2 layers of mesh as it is actually a reinforced raft, I think there is normally only 1 in a slab. The pipe was laid on top of the lower layer as it would have been too near the surface if it was on top of the top layer. The pipes are about 100mm below the surface which is lower than in most slabs, but this has not been an issue and I suspect it actually means a greater thickness of slab is heated which then emits its heat gradually over a longer period of time. Seeing as heat rises would it be a good idea to heat upper floors and not lower ones? Personally given the low price of pipe I would be installing it and then maybe take a view later on connecting it up. Finding out later that the ground floor is cool would be annoying at best.
-
Whether to put in electric ufh in the bathrooms?
Alex C replied to Pete's topic in Underfloor Heating
In a passive house you will never want to heat the bathroom floor hot enough to dry it out as it will be like being in a sauna. We put in electric under floor in all the bathrooms in our passive house as we thought there may be a chill on the tiles but in 2 years I have never wanted to turn it on. You will only want to run your wet ufh 23-25 degree surface temp range. -
I bought a blending valve that is accurate down to about 20 degrees although I have found that running it at around 26/27 works best. The boiler is a worcester bosch greenstar 12i that modulates from about 3.5 up to 12kw. I have never had issues with short cycling and with just a wall mounted temp sensor it controls the temp well. I also use it to run 4 x 600w towel rads which is all the heating we have upstairs. I have these on for an hour in the morning in the winter and overlap them with water heating as their output is even slightly less than the lowest boiler modulation. The UFH comes on a max of twice a week mid winter and often only once for about 4 hours. It was a bit of punt as I sort of designed it myself but it is dead simple and has worked really well. My plumber didnt believe that the boiler would be powerful enough to heat the house. Getting a plumber that understands low energy housing seems to be quite tricky.
-
I paid less than £400 for someone to lay all the pipework over 145m2 and attach to the manifold. This was then connected to a small gas boiler by my plumber. No great expense or expertise involved and after 2 years of living with it am very happy. Has the benefit that on cool, sunny days like today I can run the pump with no boiler input and it spreads the solar gain from near the windows over the ground floor.
-
My experience with a slab with ufh and 300mm underneath is that the house temp is kept very constant. The slab both heats up and cools down pretty slowly and only needs to be heated to a few degrees above room temp giving a very comfortable even temperature environment. We have porcelain tiles on the ground floor and if the slab is allowed to get down to around 21 it starts to feel pretty cool to walk on without shoes, where as at 23 it is fine. This may only be a small differnence but definately noticeable. I agree if you had carpet or cork you would not notice this. UFH may be claimed to be an inefficient way to heat a house, but seeing as my heating bills are about £100-£200 a year it isnt really a major worry. I will take the couple £ extra bill for the benefits of comfort.
-
The OP was talking about an Isoquick insulated raft and that is what I was responding to.
-
That depends on what your idea of warm is. It would be crazy to build a new house with a concrete slab and then not put heating under it. Running some pipe in the slab to a manifold is cheap and easy.
-
This is the link to the video Finished floor was tiles over concrete. You are never going to get a very good standard of concrete floor from polishing a structural slab. Concrete thickness is dependant on the design of the slab and ground conditions. Mine is technically different to the majority as it is structural with more steel in and also thicker. I wanted decent insulation with no thermal bridge so didn't look in to cost for a 'normal' raft.
-
Take a look at my time lapse video that is on the mbc timber frame website. Shows pretty clearly one method of installing an insulated raft