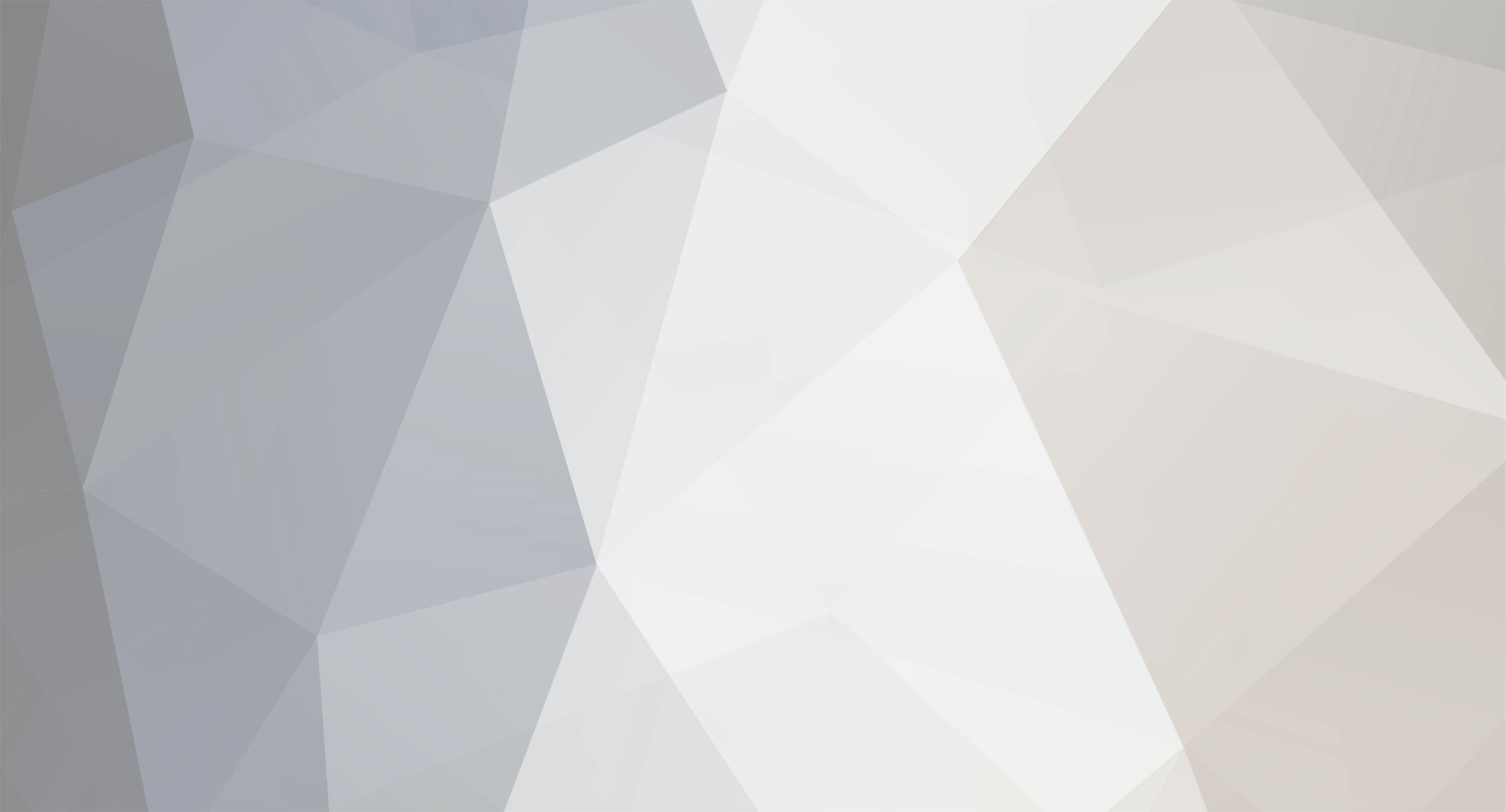
EdHat
Members-
Posts
35 -
Joined
-
Last visited
Everything posted by EdHat
-
1:40 gradient is good practice target, max gradient is 1:10.
-
Sounds like it won't qualify for the self build CIL exemption and you may also have to pay capital gains tax when you come to sell as it won't be your principle residence. Make sure you properly look into this as it's likely to be tens of thousands of pounds savings you are missing out on by not moving into the new build.
-
Structural warranty company dilemma
EdHat replied to Amateur bob's topic in New House & Structural Warranties
Hi Alan, I was reflecting on what Bob's post means for my situation. Having done my own drawings has not been an issue so far with warranty providers when asking them for quotes and fingers crossed it won't be as things progress. -
Structural warranty company dilemma
EdHat replied to Amateur bob's topic in New House & Structural Warranties
Hi Bob, Not much further for me. My lender wouldn't back down on insisting on a Structural Warranty over a PCC so I've had to reluctantly agree to get a Structural Warranty. I'm trying to deal with one thing at a time and right now that is my boreholes which cost £1000s don't seem to have given the engineer the information he required. I'm intending to act as Principal Designer (PD) myself, but I am suitably qualified, and am not too concerned about not having personal PI insurance as I feel the biggest risk is in the structure, which a Structural Engineer will be responsible for. Perhaps you could take on the role of PD yourself. If you've paid the structural engineer to do the technical drawings, and they turn out to be wrong, you would claim against them. All designers have a responsibility to ensure their individual design work is correct, not just PD. The PD isn't expected to be an expert on every aspect of the design, just have an oversight and ensure designers are suitably qualified. Architect's will principally take on the role of PD on a project, as it should be the person in control, but they won't have the knowledge to sign-off that all design work complies, i.e. structural, mechanical, electrical and now often fire protection. If you have delegated design to a suitably qualified professional, the engineer, then you've arguably done your due diligence as PD. -
Structural warranty company dilemma
EdHat replied to Amateur bob's topic in New House & Structural Warranties
How are you getting on with this? I've done my own drawings and am currently trying to get the self-build mortgage sorted. The lender has said i must have a Warranty, not Professional Consultants Certificate (PCC), because I've done my own drawings. The warranty is over twice the price of the PCC. Seems a warranty provider won't accept me doing my own drawings anyway though. I've made enquires with a few warranty/PCC providers. ABC+ didn't seem to mind when i said I'd done my own drawings so you could try them. If the structural engineer did the detailed design then definitely try them. The principle designer role is concerned with the detailed design for building warrant/regs not planning drawings. -
Has anyone used GSE Landscape trays? If so what panels did you use with them? Midsummer wholesale don't seem to sell the landscape trays. Easy PV doesn't give any options for GSE trays in landscape. I've found them on a site called TradeSparky but they come in multiple sizes, but none which look like they'll suit the standard 1722 x 1134 panel size. Are they compatible with standard size panels or is there another size panel I need to look at? GSE trays seem superior to the Solfit and Viridian systems with flashings and a lot cheaper.
-
£320-£350 for 16 ton grab lorry load for me at the moment but that's because the nearest place they can tip is about 30m miles away. Hoping a nearer tip site will reopen in the spring but still told to expect £260 a load. I thought you still had to pay VAT on muck away. I'm hoping someone will take the root ridden topsoil but I've been told if more than 5 loads go from a site paper work such as licenses and permits are required.
-
Are some snots and caps a problem on the inside of a new brick wall?
EdHat replied to Bounce's topic in Brick & Block
It is particularly important with this type of insulation that joints to the cavity facing side of the inner skin are struck of flush. Firstly, so that you do not get any air gaps behind between the insulation and inner skin which seriously undermines the thermal performance given in the design. Secondly, so the 10mm clear cavity between the insulation and outer skin isn't reduced. Generally, you need a 50mm clear cavity with insulation boards. Manufacturer's developed these products with a tongue and groove joint so that 100mm cavities could still be used after U-value requirements were changed. They were tested with a 10mm cavity and require this to ensure moisture doesn't pass across the cavity. Any gap behind will mean less than a 10mm clear cavity. -
Are some snots and caps a problem on the inside of a new brick wall?
EdHat replied to Bounce's topic in Brick & Block
Joints should be solidly filled with mortar. Not fully filling joints means the outer skin is less effective against moisture penetration. Excess mortar should be struck flush and droppings should be removed from the cavity. What insulation are you using as this effects how important this is? There doesn't appear to be many wall ties in the photos. -
Thanks guys. The broker fee is £1,300 and the lenders fee is £500 more than going direct, so going with the broker will only cost me £1,800 plus a worse interest rate of 6.4%. As you say a small amount in the grand scheme of things but not an insignificant amount. What I can't decide is whether the 1 year lock-in vs a 2 year lock-in will be worth the extra fee (although I suppose only I can decide that based on my build programme) and whether a 1 year lock-in is an uncommon offer.
-
Having a bit of a dilemma and would like to ask for peoples thoughts to help me decide. I've got planning and am in the process of securing a self-build mortgage, discharging pre-start conditions and doing the technical design. I always intended to use a broker as I am doing the design works myself, will be project managing the build and would like to do as much of the construction work myself, so using a broker was one less thing to worry about. My situation is slightly unusual as well, buying my parents garden below market value and using a Lifetime ISA. The broker I've approached is easy to talk to, seems very much on the ball and has a good reputation. They have found me an mortgage offer, however it isn't as attractive as I expected. The broker fees are £1,300. The lenders fee is £1,500. The rate is around 6.4% for 2 years with a 1 year lock in. I looked at what the lender offered direct and it's £1,000 fee and a 6.1% rate for 2 year with a 2 year lock in. And there are others offering 5.85% The paper work says the lender will pay the broker £4k (on top of the fee i pay the broker), and it seems to me I'm effectively paying for this through a larger lender fee and higher rate. I thought lenders would give brokers better offers than going direct as they save the lender time and bring them customers. The pros I see for going with the broker are: - Quicker, i haven't got to wait for other lenders to review. - Saves me time, I haven't got to have conversations with multiple lenders which takes me away from getting the technical design complete. - They provide a build cost estimate which they say the lender will accept. I work with Chartered Quantity Surveyors so should be able to get something acceptable for the lenders for not too much of a cost, or I'll need to spend time getting quotes/tenders (which i can't really do until the design is complete. - Only a 1 year lock-in on their offer. My high level programme is 15 1/2 months to BC sign-off and 18 months to practical completion and I'll be drawing down a small amount to buy the land. So this could potentially save a lot of money, as my understanding is it means I could remortgage to a standard residential mortgage if I complete in less then 2 years rather then keep paying interest only up to the 2 year point even if I've completed. From a quick look around, a 2 year lock-in seems most common. The cons are obviously the cost, but I'm wondering if I'm not fully appreciating the 1 year lock-in aspect. If I've borrowed £300K for 12 months, the difference in interest between 6.4% and 6.1% is less the £1,000. However if I borrow £300k for 1 month, that's £1,525 in interest, so could make a big difference if I complete before 24 months. I'd welcome peoples thoughts or stories of similar experiences and decisions, and also how long your builds took.
-
LPA requesting extension. Any pearls of wisdom?
EdHat replied to flanagaj's topic in Planning Permission
Agreeing to extensions is not your only option and don't feel pressured to. My advice is if you don't think they should get one refuse and say you do not want to lose your right to appeal due to non-determination. Although, if they are waiting for information from you then you then it is more difficult as you don't want to give them a reason for refusal. I had an application that I initially agreed an extension for as the officer gave me feedback basically saying it would be refused, which gave me the opportunity to heavily revise plans without having to make another application. An extension was therefore justifiable. They were approving of the revised proposal but ultimately took 2 years to send it to the planning committee for a decision. They then asked for another extension to do the officer's report and I refused. Partly on principle, as had I agreed it would of gone on the records as being decided within the target time, which it clearly wasn't, and partly as I would loose my right to appeal due to non-determination. Refusing didn't cause any further delays. In recent months I have had another application where the officer asked for an preliminary ecological assessment (PEA) a few days before the decision date. Which then caused delays. After I submitted a PEA report they asked for an extension. I refused, mostly because I was annoyed they'd asked for a PEA on a garden plot which was effectively a lawn and clearly didn't have any ecological value and also because I believe I'd loose my right to claim the fee back. I gave the reason as losing my right to appeal due to non-determination as I feel this puts pressure on them to keep the application at the top of their pile and make a decision. They decided it a few days after the end of the ecology consultation period. -
Warranty snagging points - are these common?
EdHat replied to Tony K's topic in New House & Structural Warranties
Even if you can get an insurance backed guarantee for the flat roof at this stage it's going to set you back more then the £100-£150 for the indemnity nod has mentioned, so your best bet in the first instance is trying to get them to exclude it. You mentioned the guarantee is from the supplier/installer. Is that supplier guarantees materials and installer guarantees workmanship or is it a "single point warranty". With the latter the supplier or manufacturer warranties the whole thing, design, materials and workmanship and depending who it is from, in my opinion is superior to an insurance backed guarantee. For one insurance backed is usually max 10 years whereas single point can be up to 25 years. Also, the big names like Bauder, IKO, SIG etc are massive companies that have been around for decades and are likely to be around longer then the firms offering the insurance backed guarantees. Regarding number 2, why didn't they do their own inspection if they are that bothered. Surely if they ask for 3rd party inspection of the drains they could ask for 3rd party inspections of everything they didn't inspect themselves. A simple CCTV survey shouldn't be to onerous but I'd be surprised if your local drainage firm hold PI insurance. -
Architects, ballooning fees and estimates
EdHat replied to Drellingore's topic in Costing & Estimating
I agree with others here and find it typical of many architects. £3,500 may not be unrealistic but their original estimate was. It sounds like they've designed what they wanted and given no consideration to your budget. I wouldn't be surprised if they aren't actually interested in doing the technical design, which looks like it's going to require a lot of consideration and bespoke details, and that's why they dropped that news now. I would get a QS to give you a proper budget figure so you know whether you want to/ can proceed with the project or if you'd be better off revising the design or even selling the plot. I don't think the standard online/broker budget costs would be suitable as they usually assume standard new build in terms of materials and details, yours seems more unique. I see no problem changing designer at this stage. In fact many architects themselves outsource the technical design, or at least pass it to a technician within the firm. I'd look for a technician or building engineer/surveyor who's much more likely to be passionate about spec and detailing then an architect whose passion decreases with each RIBA stage. Another designer looking at the plans may also have benefits as I wouldn't be surprised if an architect with no consideration of budget also gives little regard to practicalities of using and maintaining the building. -
I find extractor fans in the kitchen and bathroom make the biggest difference and keeping doors to these rooms closed. Consider ones with a humidistat. Activity in these rooms can cause big spikes in relative humidity (RH) and temperature. When the temperature then drops, after cooking and showering finishes or as the air moves to colder parts of the house, the RH raises further. If you have extract fans in the kitchen and bathrooms and still have issues then I too would advise getting a decent dehumidifier. You can set them at say 60% RH and they will turn on when it gets above this, preventing RH getting high enough for condensation and mould growth. Meaco is a good brand and their units are low wattage
-
Building regulations Discharge conservation area
EdHat replied to PSC88's topic in Building Regulations
@PSC88write a letter making your case, reference policies from the local plan that you are complying with, and give local justification for materials including photos and recent uses. I find planners stipulating materials a bit of a nonsense as it'll likely be permitted development for you to change your roof covering, windows, render afterwards anyway. I had planners tell me they didn't like mono-pitch dormers and wanted traditional pitched dormers. There was a reason I'd included mono-pitch in my design and i wasn't going to back down. I struggled to find local examples, but made the point that policy doesn't forbid them and they'd recently approved flat roof dormers, so if I couldn't have mono-pitch id go for flat, knowing they couldn't object to this. They backed down as they'd obviously rather anything but flat dormers. So what I'm saying is, even if you can't find examples of what you want, sometimes giving examples of something worse works. -
@Post and beam Which manufacturer did you end up using out of interest? George Barnsdale do look very good on first impression, they put a lot of information out there on their website which makes incorporating them in a design early on easy.
-
Box guttering with warm roof, is it possible?
EdHat replied to Tuppers's topic in New House & Self Build Design
I'm not sure if i understand your question. Do you want to build right up to the boundary and therefore don't have room for a normal gutter? With a warm roof you can form a gutter in the insulation, you only need to achieve a 1:80 fall. Roof manufacturers will have a standard detail for this. Alternatively is it possible for the roof to fall a different direction and then have a kerb along the boundary side so no need for gutter there? -
Just to drive home the point, as others have said, and hopefully provide some clarity, the original post refers to the principal designer (PD) role under the building regulations. This is a separate role to the PD role under CDM, but just to confuse things they decided to use the same titles. CDM principal designer Responsible for ensuring H&S has been considered in the design in terms of construction and future maintenance and any risks are designed out and preparing H&S file at the end of the project. Doesn't necessarily have to have designed anything themselves, as designers have responsibilities under regulations. CDM principal contractor Responsible for H&S onsite during construction phase. Prepare the construction phase plan, provide welfare facilities and coordinate contractors. Basically manage the site, individual contractors still have H&S responsibilities under the regulations. BR principal designer Responsible for ensuring and declaring that the design is compliant with the regs. Architects should really be doing this under there role in completing technical design stage anyway. The only real additional requirement is they must sign a declaration. Again, designers still have responsibility for there own portion. OP there should be no issue in architect continuing to act in this role during the works but you will have to consult with them if there are any changes to the design. BR principal contractor Responsible for ensuring construction is as per the design, and therefore compliant with regs. Has to sign a declaration on completion and therefore assume a lot of risk. PAS 8671:2022 is where to find the full details of the PD role but there is a brief summary of that and PAS 8672:2022 here: https://consultations.hse.gov.uk/bsr/building-safety-competence-information-pc-pd/supporting_documents/Building safety competence information for principal contractors and principal designers.pdf If you are competent you can be the client and fulfill all these roles. PD and PC roles under the building regs don't place any more requirements on the lead designer and main contractor then they would usually have contractually anyway. The purpose is basically to clear up the fact that it is not the building control's responsibility to ensure design and construction comply with the regs and if you manage to get something non-compliant approved and signed off, and it later comes to light, there is someone to be held responsible.
-
Confused.com regards next steps to treat and prevent damp
EdHat replied to MJP's topic in Damp & DPCs
As others have said, as it's a solid wall you want to use vapour permeable materials to allow moisture in the wall to evaporate. Use a humidity variable VCL on the warm side. Tyr-Mawr do some good systems. Don't leave voids, this will encourage interstitial condensation. If you can't lower the external ground level, take the DPM up the wall to 150mm above external ground level and fit a DPC here as well. Dry rods in the mortar bed are probably your best bet. Alternatively, waterproof render over the whole wall inside and then use a standard VCL and PIR internal wall insulation system. You will need make sure you get your VCL completely airtight and get a good seal with the floor membrane as well as introduce adequate ventilation elsewhere to keep humidity levels under control. My preference would be the former. -
Proper single ply membranes are often used on large flat roofs without complicated details for speed of insulation or pitch roofs as it presents a very clean look. These are usually PVC or TPO/FPO and are heat welded at laps which makes them very durable. I see some issues with puncturing where people walk on it, but electronic testing can locate punctures and they can be patched. Biggest issue I've seen is with poor installation where it wasn't adhered properly and blew off in a strong wind. EPDM seems to be a more DIY suited product for use on simple small scale roofs i.e. garages, garden buildings. While the membranes seem to have a long life expectancy I'm not convinced the adhesives and trims do. The EPDM trims do not seem durable to me as they sandwich the membrane and rely on foam for creating a seal. Laps do not seem durable either as they use adhesive rather then heat welding. They are especially vulnerable on corners where they often start to open up so belt and braces would definitely be wise. I see a lot of rippling with EPDM that I haven't noticed with other single plys. EPDM is also much more vulnerable to puncturing then other single ply membranes. Note the big manufacturers of single ply membranes, such as Sika, Icopal and Bauder don't produce EPDM membranes. The Alwitra one in featured in the Robin Clevett video is PVC. I very much a fan of bitumen felts for 'out of site' flat roofs for their durability and cost effectiveness. There are a lot of cold applied liquid systems on the market now with BBA certs to rival lifespan of other products which are excellent for complicated details and overcome many of the issues with GRP, but do come at a cost premium.
-
I concur with DevilDamo and would add, you should seek an surveyor/ technician/ engineer to produce the detailed drawings for a full plans submission. Ask that the drawings give a sufficient level of information to allow builders to quote. You will also need to consider whether you will want someone to tender the works for you and oversee the construction works as it will be worth getting a fee quote at that stage. It will likely require planning. The Local Authority won't necessarily get back to you to confirm whether it needs planning, they are under no obligation to. Have a read through the Permitted Development Rights guidance on the .gov site and see if any applies.
-
You'll need 140mm or 150mm depending weather it's refurbishment of an existing element or a new thermal element. When I've needed to keep the height down I've been able to reduce the 140mm down to 90mm by using a multi-foil insulation over the joists first. You could also look at Recticel Deck VQ which has a lambda of 0.008 and I believe you can meet the regs with 90mm but I expect it is expensive.
-
No building regs for existing porch for house purchase
EdHat replied to SilverShadow's topic in Building Regulations
If the porch is not within the thermal envelope of the building, i.e. external door between house and porch and porch is unheated, then building regs application wouldn't be required. -
Fill the footings then you're ok. The PWA only applies to the footing works so it will be too late once they're complete.