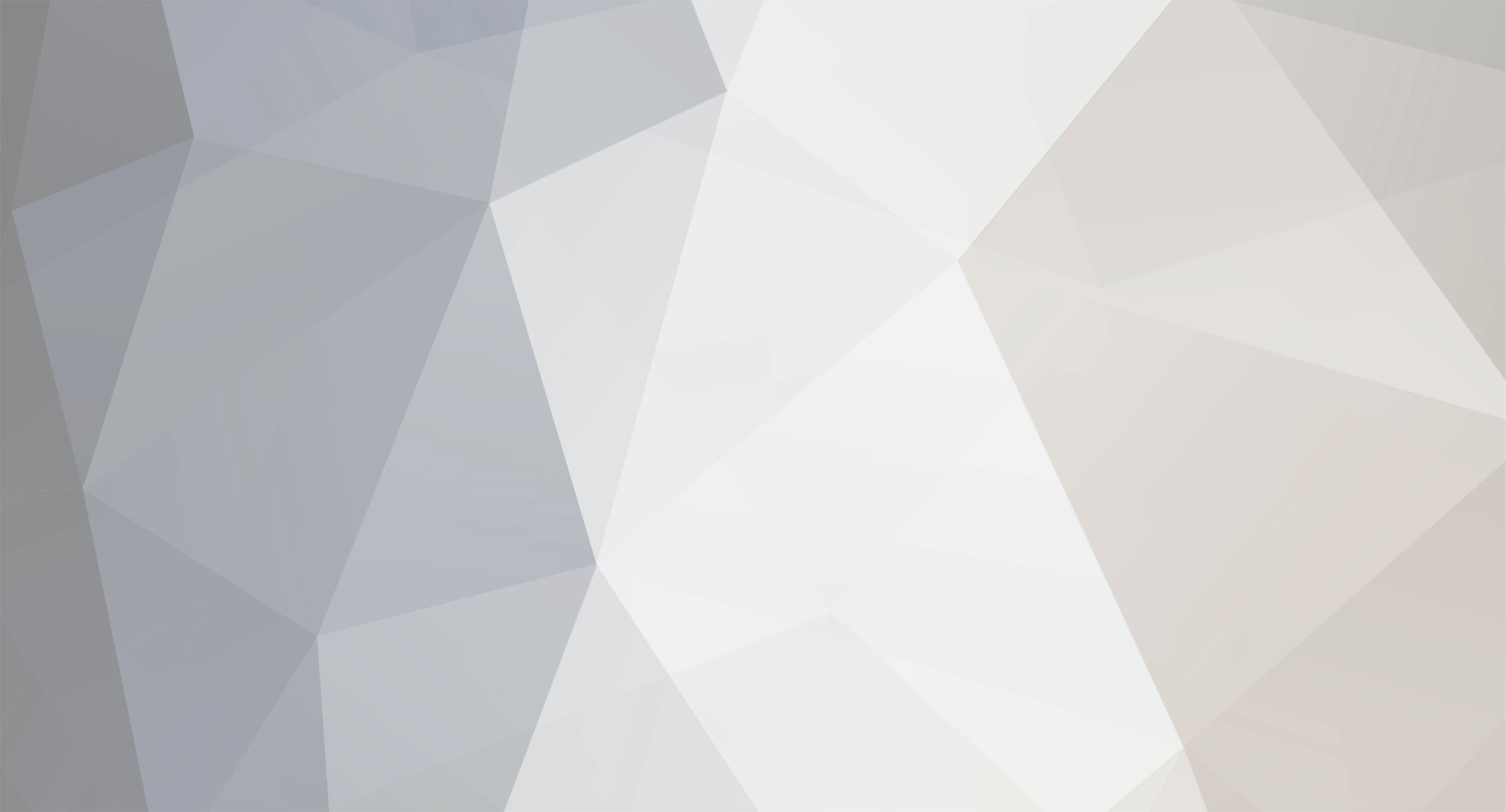
Paene Finitur
Members-
Posts
83 -
Joined
-
Last visited
Everything posted by Paene Finitur
-
Sorry for the massive delay in getting back to this thread. For what it's worth I thought I'd give an update. I took a sample tile to a local roofing merchant and a helpful guy took a look at it and the photos. His view almost immediately was that the tiles were at too low a pitch. Apparently Heritage are rated down to 35 degrees, but this part of the roof is more like 25 and goes down to almost 10 near the lowest point. He put me in touch with another local roofer who came over and took a look. After quite a bit of chasing I pinned him down yesterday on what he felt needed done: All the tiles on the lower section of the roof (see full picture above) will have to come off as they are unsuitable for this pitch He has recommended replacing them with slate. This is the cheapest option and slate would be fine for this pitch, but it is not at all in keeping with the rest of the roof and I'm not convinced that it would not look awful. The alternative would be to use a Planum Red concrete tile which will go down to around 15 degrees, though these are a lot more expensive than slate. The slates would fit the existing battening but the planum might need the the battening replaced in order for it to fit. There are a number of other items that need to be changed such as lead flashing and guttering, as noticed here. The price of this is likely to be around £5,000-£6,000 depending on the choice of tiles mainly. Obviously a lot of money but it seems about average based on what I've been reading. Haven't got any other quotes. I've a good mind to ring the original roofer and let him know all this, though what good it will do I'm not sure. Feeling a bit gutted TBH. 😒
-
Sorry - a bit distracted with Christmas and other responsibilities. To go through the feedback above (and thanks so much everyone for taking the time to respond) There's a confluence point (see pic detail) where an awful lot of water comes together. I initially thought that this was the problem and that the issue was that the guttering (open ended on the right) should be closed with a down pipe on the left side nearer the window (ugly, but if it works) I also thought the that existing down pipe not shown here but to the left on the other side of the window, should be directed further out on the roof in case the deluge was going under the flashing. However, I have stood in fairly heavy rain and observed what's happening on the roof. Yes, there is a lot of water coming together at this point but it didn't look as if the roof was failing to cope with it. The gutter certainly appeared to be coping with the downpour and was not overflowing, nor was there evidence that the gulley was too tight and the deluge was overwhelming it. That's just from my untrained eye though. I'm therefore disinclined to think that this is the root cause of the problem - though it may still be a problem, I agree - mainly because of the following: There does not appear to be any evidence of damp or water ingress around the area of the flashing on the inside of the house. I admit it may just not have come through yet and I also agree that the flashing - particularly at the bottom - is lousy. The issue of water dripping down behind the gutter onto the facias and rafter footings seems more or less consistent across the length of the lower gutter - not just at the far end above the side door, which implies to me that it's a issue affecting the length of the gable end, not just the valley on the left hand side. Even after very light rain, or when there has been no rain for a day or so, I can often find - like the original pictures - lots of drips and moisture across the footings when the tiles and gutter are relatively dry. This makes me suspect that there is moisture trapped behind the tiles/membrane. On one occasion, the roofer came back and lifted several rows (can't recall exactly how many) of tiles and laid another membrane. This did not make any noticeable difference. The lower guttering does not seem uneven or twisted. As you may see from the original picture, there's a bit of vegetation overgrowth from a neighbours side which I've tried to keep in check to avoid leaf blockage etc. Ideally, two downpipes on this section would have been sensible, I agree, though there is no room for a butt here and the only other drain is a foul from the washing machine/sink, which obvs I'd like to avoid running into. As for a rainwater/gutter calculation, I agree this should have been done. I've looked through all of the documentation that I have from the structural engineers but can find nothing giving such details. It seems odd, but I will have to assume that it was not done. ☹️ My plan is to get an independent roofer in once things start up again in January, and get an assessment of the issue. I will discuss the rainwater/gutter calculation - thanks for raising it. Finally, I agree that LABC would say that this has not been competently fitted. I would argue back that they had an inspection program that should have picked this up. Whether I am right or wrong in that, I would doubt that it will make a difference. My suspicion here is that the project manager did not pick up that the choice of rooftiles was not suitable for the particular pitch of one section of the roof and the roofer did not pick up on this. I could try to take either/both to the small claims court though again, I suspect I would be banging my head against a brick wall. In the case of the project manager, it seems there are a queue of customers and tradespeople with grievances/claims against him. I guess this answers my initial question of whether an LABC claim would be an effective move. I plan not to do any more on this until I get a detailed opinion on the issue from an independent roofer, with a view to how much it will cost to put right. If the cost to remediate is considerable, then I will have to weigh my options about how to proceed further. Again, I really appreciate all your feedback on this and I will keep the thread updated as things develop.
-
Yes, I suspect that is what is happening, and I am equally surprised - so much so that even though I suspected this for a while, I couldn't quite bring myself to believe it I will try to get another roofer to give an independent verdict, though if the pitch is the issue, they will presumably all have to be stripped back and potentially battened and rafter end replaced. I'm also rather pinning my hopes on the enclosed product which the roofing supplier indicated would be a way to get round this issue.
-
Yeah, I think that's a fair point too. The roof is pretty big above this point with a lot of water coming down off it further up from a higher pitch. I've added a couple of photos - one from the window and one from gutter level - which hopefully give a better idea of the issue. You can probably see from the second photo that the downpipe doesn't actually contribute most of the flow. In fact, most of it comes from, the gable end which drops from a higher pitch to a lower pitch and should be fairly constant across the 6.5m length of the guttering on the left although I agree that due to the confluence off the main roof, there will be more coming down on the far side. You can also see that there's moss growth on this part of the roof which tends to suggest excess damp retention in the tiles & cement board. Finally, you might be able to make out in the first picture that there's a roof-mounted extraction duct blended in there with the tiles. In very heavy rain, we also get rainwater flooding through the extractor fan into the utility below, which makes me feel that the pitch was too low here for this too.
-
Hmm, if the minimum allowable pitch for the tile is 35 degree and they are pitched at 25 degrees, that's surely a problem, right? It might not be the problem here, but I can't see it helping. As to whether it's the responsibility of the roofer, he was sub-contracted by the project manager. I did not (but should have) seen the terms of this contract, but I would have reasonably expected a roofer with decades of experience to spot straight away if a tile being used is inappropriate for a particular pitch of roof and at least raise questions/concerns - after all it's his reputation at stake - but nothing was ever mentioned. My warranty is with LABC but I agree with you about the likelihood of them paying out. Seems wrong t exclude defective work though when they had an inspector out regularly to check on it.
-
Thanks @joe90 Yes, you're right, I meant minimum pitch. I agree with your comments about the eave tray being too short and the guttering not extending. It was suggested to right angle it round the edge for good measure. The leadwork here is pretty lousy too - for a professional. I think these are good suggestions and I intend to implement them. However, the issue of water coming round the back of the eaves tray and guttering extends right along the length of the wall which is around 6.5m and there are parts where it was so bad that the painter could not paint it due to the wood being damp. I suspect that this will need more than just an extension on the eaves trays.
-
Hi All, I'm seriously considering my options, including making a warranty claim for a substandard roof in our 2 year old self-build. Just wanted to hear anyone's views on it. The project was run by a project manager who work closely with a local structural design company. The roof consists of hand made clay tiles and was fitted by a local roofer with decades of experience. All has been fine except for one section where we have had problems of water going behind the guttering and soaking the eaves and exposed rafter feet, which are now showing signs of damp damage. We have of course, had the roofer back on several occasions to look at the issue and he has done some work to remedy the problem, but to no avail. He's also not the easiest or most reliable person, in terms of keeping appointments so this has been over an extended period. Over the last few months, I finally lost my patience and did what I should have done a lot earlier; I did a lot of my own research and asked around the roofing trade online for some opinions. In particular, I got some great help from a local roofing supplier who stated straight away that he felt that the tiles are at too low a pitch on this part of the roof - these tiles should be no less than 35 degrees (in this part of the roof they are laid at around 25 degrees). He stated that the max pitch should be on the plans but I've not spotted them anywhere. He also gave me the name of another local roofer who I intend to ask to visit, give a professional opinion and quote for repair work. I am not expecting this to be cheap. Without mentioning my investigations, I also suggested to the original roofer that the pitch looks too shallow for hand made clay tiles, and that I'd have expected him to spot this. He replied that he didn't think that was the issue but in any case, the calculations were done by the project manager, not him. I should add that I had to let the project manager go since he made numerous costly mistakes, failed to bring the project in anywhere near on time or to budget and was absent for large periods without any explanation. I'm just wondering where all this leaves me. I am unlikely to get anything from either the roofer or the project manager without a costly fight - despite this problem likely being due to their actions/mistakes. That said, if it does prove expensive, I feel I will have to document a case to LABC - the warranty provider - and try to make a claim. Any thoughts or experiences you can share would be very much appreciated, as it's the first time I've considered going down this route.
-
Ah! But you'll always know that it's there!! Alternative suggestion: You could route a vertical dado channel maybe 8mm deep, 6cm from the top to the middle of skirting on each side. Then cut your battening so that the top 6cm is 8mm wider on each side. It then just slots in neatly. This would not only hide most of the profiling gap, but would also strengthen your battening joins to the skirting.
-
Plywood cutting and Machining - Carpentry.
Paene Finitur replied to JamesP's topic in General Joinery
£30K or so doesn't seem too unusual (I'm not saying it's reasonable) I've seen Sharps charging more than that with their 50% discount!! We had a local joiner to do some work and he moaned on about customers wanting bespoke work at Ikea prices! 🤣 I guess there is their time and skill to consider. He told us he had a lot of kit in his workshop specifically for large cabinetry, so I guess that all has to be paid for and maintained but, still, £30K is a lot. I have to do some cabinets but they will all sit within existing large built in cupboards so the external finish isn't quite so critical. I'm hoping to do most in MDF/Ply with a rolled or sprayed paint finish. I asked in a local Facebook group if there were any woodyards out there that accepted cut-lists and got some decent responses. What I could really do with is a design app that creates cut-lists, that's easy to use and at a decent price!! -
Level door access disaster. Advice needed
Paene Finitur replied to Paene Finitur's topic in Doors & Door Frames
I just found the part m document if it's any help: nhbc-part-m-disabled-access.pdf -
Level door access disaster. Advice needed
Paene Finitur replied to Paene Finitur's topic in Doors & Door Frames
Yes, Building Control did pass it in the end. I was toying with getting rid of it as I don't need it and it's a bit rough, but just have too many other jobs right now and it's been useful to get big things in and out of the house TBH. I think the rule was a 900 min square level area in front of the door and then something like min 1 in 12 slope. I think he might have let me get away with slightly steeper (1 in 10 maybe?) than that, but I'm fairly sure a step would have been rejected. The main thing he wanted was a permanent ramp, not a metal or wooden structure. -
Finishing basement (screed + UFH) - advice needed.
Paene Finitur replied to Paene Finitur's topic in General Flooring
No, I keep it fairly low. It's mainly - in conjunction with a HVAC - to avoid condensation/damp. That said, I don't want to put something that will block even that low level of heat. Being underground, it keeps a fairly consistent temperature, being slightly warmer in winter and cooler in summer. -
Finishing basement (screed + UFH) - advice needed.
Paene Finitur replied to Paene Finitur's topic in General Flooring
Thanks Conor. That sounds good. Would wood fibre go OK with UFH? Also, the existing screed doesn't quite come up to the wall in many places, but up to foam insulation boarding that surrounds the room. I'm wondering whether I should cut that back since, unless I raise the floor above that level, I'm going to find bringing the laminate up to the wall and fitting a skirting board a bit tricky. -
Hi all, we moved into our self build with the basement still not complete and would like to finish it off. As cash is tight, I'm planning to do the work myself, so ideally would be looking at a solution that is possible for the experienced DIYer. The floors are currently rough screed over UFH and I need to decide how to complete the floor, ideally, before taking the project further. The rooms are: 1. A fitness studio. Ideally this would be a spring wood floor but I don't think this would work well with the UFH. My initial thought would be to pour an initial self leveling latex screed and then finish with either laminate or karndean, if funds and experience allow. 2. A den/cinema room. This is also rough screened with the added complexity that there are two large manholes in the room for the basement sump pumps. So I would have to create an access hatch for these,i guess. Again, I think that a laminate initially would privacy be easiest and cheapest here, but open to suggestions. You might see from the photos that the screed doesn't come up to the wall in many places but to insulation boards, and I'm not sure quite how to deal with these. Should the insulation be cut back level with the existing screed, or should I foam any gaps and bring the screed up to the level of the foam? One particular corner has an elevated concrete block, which is a bit of a pain Ideally I'd have a completely level floor for whatever surface goes on to of it. I'd love to hear any suggestions or experiences with something similar. I'm lacking in experience and confidence and don't really want to make an expensive blunder. Many thanks!!
-
There are some great pinned posts on this subject. The 3 months is from BC signoff (6 months if after 5 December 2023) but there's been a few cases where HMRC have argued that the moving in date was more significant. As far as I can tell, this tended to happen when BC sign off was severely delayed and owners had moved in months or even years earlier. They do ask for the moving in date on the form. We'd had to move in even though there was still work to get the cert and this took about 4 months. Bit of a nervy wait but they paid out without question and only deducted a kitchen appliance - they were fine with the extractor. Definitely worth getting any VAT claimable supplies in for any jobs your hoping to do imminently. I chucked in a few of these, but to be honest I wish I'd kept better records and been a bit more savvy throughout our build - I'm sure we missed a few things that we could have claimed for.
-
ASHP / Octopus Cozy - any experiences?
Paene Finitur replied to Paene Finitur's topic in Other Heating Systems
Ouch!! Hope you're better now. Certainly not what you want to come home to. I suppose at least you weren't bothered by humidity on you return. My de-humidifier has recently taken to tripping the MCB, which saves me quite a bit! 😁 -
ASHP / Octopus Cozy - any experiences?
Paene Finitur replied to Paene Finitur's topic in Other Heating Systems
Thanks for all the amazing feedback. To answer some of the points: @SteamyTea I'm not sure that I can separate out the heating from the hot water in terms of energy use. There's a separate meter for the ASHP and one from the immersion for the header tank. We had a big spike last Christmas because the thermostat for the header tank got slightly dislodged resulting in the ASHP having to work much harder and the immersion kicking in to make up. Thankfully, that got solved. @JohnMo Yeah fair point, and you're absolutely right; when I was checking last winter, the non-heating/HW electric usage was around 22KWh/day so probably mainly not the ASHP over summer. @Conor I suspect that was mostly washing machine, and also the tumble drier, which Mrs Paene Finitur insists on using. There are 6/7 of us living here though, with two of us working from home regularly so I suspect it's probably not that unreasonable, though I will look at the stand-by issue. Thinking of getting this or something like it round the back of the TV. @ReedRichards I don't have a swimming pool, hot tub or electric Aga. We have a dual rangemaster and the oven will take a chunk but is infrequently used. I guess it's the washing and drying that will take up most of it. @joth I wish I'd known about this last year when they were setting the electrics up. I have 25 MCBs on my board so slightly too many and now the trunking is in, it might make it a bit difficult but what a great device! @Ferdinand I'm guessing you had visitors in June? 😁 -
ASHP / Octopus Cozy - any experiences?
Paene Finitur replied to Paene Finitur's topic in Other Heating Systems
Hmm, I kind of agree with you there. There's still too many places where we don't yet have curtains up to keep some of the heat in. But that can't be the full story. During the period over the summer this year, our consumption according to Octopus has never really gone below 150kWh per week. That's at a time when all the stats were switched to freeze protection i.e. the heating was effectively off. It seems that the ASHP is the culprit but I'm at a loss to know how it's taking up so much power for effectively just heating the hot water. -
ASHP / Octopus Cozy - any experiences?
Paene Finitur replied to Paene Finitur's topic in Other Heating Systems
I wish I had gone with batteries. Co-incidentally, I have basement sump pumps that are backed up with a decent but sump-pump specific, battery back up system. I was so focused on ensuring the basement didn't flood and focusing on the design of the water management for the basement that I didn't see the bigger picture of using a similar battery bank centrally to cover the sump pumps but also even out the peak periods. What a chump!! Well, you live and learn. Did you go with a specific battery system? At some point, when the sump batteries wear out, I'm considering changing to a central system, but that's further down the line. -
ASHP / Octopus Cozy - any experiences?
Paene Finitur replied to Paene Finitur's topic in Other Heating Systems
Thanks for the responses guys. Yes, I was going to enquire with Nu-Heat, who deigned/supplied the system, whether it would be possible to centrally adjust the system to go to low power during the peak period or something like that. I have Heat Miser controls in each of the rooms, but was advised to switch off the timer part and just set to a constant temperature. 24x7 steady running was the message that was drilled home to me when it was installed. Easy to advise when you don't have to pay the bills! 🙂 I'll take a look at setting the timers - would like to do that centrally of course, but can't figure out how to link them to WiFi. A project for another time I think - bills down first! More broadly, I've got to admit that having installed a big (and quite expensive) ASHP/UFH system, I'm afraid I still feel quite naive when it comes to getting the best out of it. Are there any guides out there for novices to all ASHP concepts (i.e. COP, flow, weather comp) that might help me get more au-fait and manage it better myself? -
Hi, after moving into our new house last winter and experiencing horrendous heating bills for the first few months, I'm looking at ways to keep the bills down this winter. We have a 16KW Nibe ASHP with UFH in the basements and ground and rads on the 1st/2nd floors. The usage was coming in at around 650KWh per week over last Christmas/new year period. Partly this turned out to be a fault with a hot water tank thermostat that was causing the immersion to kick in, but even when this was resolved the costs were still very high. Since about March, I've had the room thermostats set down to frost override to keep the bills down. I'm currently with Octopus and we're on the Flexible Octopus tariff which is 35.37p per kWh during the day for electricity and 14.84p per kWh at night (2am to 6am I believe) This doesn't seem great for a ASHP really since the accepted way of using them is to have them running all the time, so I get precious little benefit from the night rate. I recently found out about the Octopus Cozy tariff, which seems to have been designed with ASHPs in mind. Despite Octopus telling me that I was already on the best tariff available, I did some basic calculations downloading my usage and applying the rates from both tariffs. It looked to me as if it would be from 10% to 21% cheaper than the Flexible tariff. Has anyone else any experience with this or other ASHP friendly tariffs?
-
Tips on cleaning/de-calcifying pumps and sump
Paene Finitur replied to Paene Finitur's topic in Basements
Thanks Tony, I already have a float switch with a monitoring unit and battery backup so fingers crossed, we should not have a flood without prior warning. We also had a power outage of 3 hours last weekend and it coped quite well with that. I had a beef with the pump suppliers who would not warranty their own pumps because they weren't there for commissioning. I offered to pay for them to come out to do a full inspection, but they still wouldn't warranty them. They charge £300 + VAT for a service which they say needs done twice a year but that doesn't include cleaning the pumps/sump. They also do various monthly subscription call out packages but the costs are pretty. That might be the average cost for this kind of thing - I'm afraid I don't know - but I'm seriously thinking of just training myself up in it so I can do the work myself. I mean, I'd consider a contract for a 3rd party to do it certainly, but not at those prices. In the meantime, I'd like to be able to do basic servicing on the pumps myself and keep the sumps clean. -
I had a bit of a crisis moment a couple of days ago when the AlertMaxx unit which notifies me when there are pump problems started reporting a power failure on my primary basment pump. To clarify, I have a tanked basement with two sumps, ground and foul, with three pumps, one foul and a primary and secondary for groundwater. similar to this set up. Thankfully, it turned out to be a false alarm as my son and his friends had inadvertently leant against the isolator switches and switched one off! That said, when I lifted the manhole, I was quite alarmed at the state of the sump, which had a lot of limescale and sediment build up. Ongoing maintenance of the pumps and sump is something of a worry to me since the supplier PPS systems, refused to warranty the pumps on the grounds that they hadn't done the installation and commissioning (the pumps had been hastily but properly installed after a temporary pump failed a couple of times leading to floods) and their servicing and maintentence contracts are pretty expensive so, with money tight, I've not signed up so far. I'd like to keep the pumps going as long as I can and do any maintenance that I can reasonably do. Does anyone have any tips or advice on cleaning sediment and limescale from the pumps and chamber? It looks like a fair bit of effort might be required and possibly some chemicals although I'm aware that this is groundwater so I need to stick with something that's kind to the environment and the pumps of course! Any advice, tips, links etc very gratefully received.
-
Potential sagging on cupboard shelving
Paene Finitur replied to Paene Finitur's topic in General Joinery
The back should be supported by a full length back baton so I was more concerned about the front. I'm thinking of using a hidden steel support across the front (https://www.metals4u.co.uk/materials/mild-steel/mild-steel-flat/flat-black/2257-p) covered by trim, routed at the back to allow the support to sit in. I saw this on a Charlie DIYte vid (see below). Note quite the same, but I'm hoping it will give some measure of support. I'd be a bit concerned about the sheer weight of 36mm kitchen top; would probably need much bigger battening. Plus as I have to do six of these for different rooms, the cost is a factor too, although I did see 28mm for a reasonable price (https://www.diy.com/departments/28mm-matt-white-laminate-particle-board-post-formed-kitchen-worktop-l-2400mm/3663602636151_BQ.prd?storeId=) Yes, almost but never quite. 90% done and 90% to go! -
Potential sagging on cupboard shelving
Paene Finitur replied to Paene Finitur's topic in General Joinery
I thought of having several arched brackets across the back. Could even make a feature of it though I worried they'd get in the way of the hanging rail - would have to measure up properly. Also, as some of the cupboard backs are partition, I'd probably need two rows of back batons, one above the other, to fix the back of the brackets to. I also thought of a descending middle section to attach to the ceiling, not sure I'll go for that though.