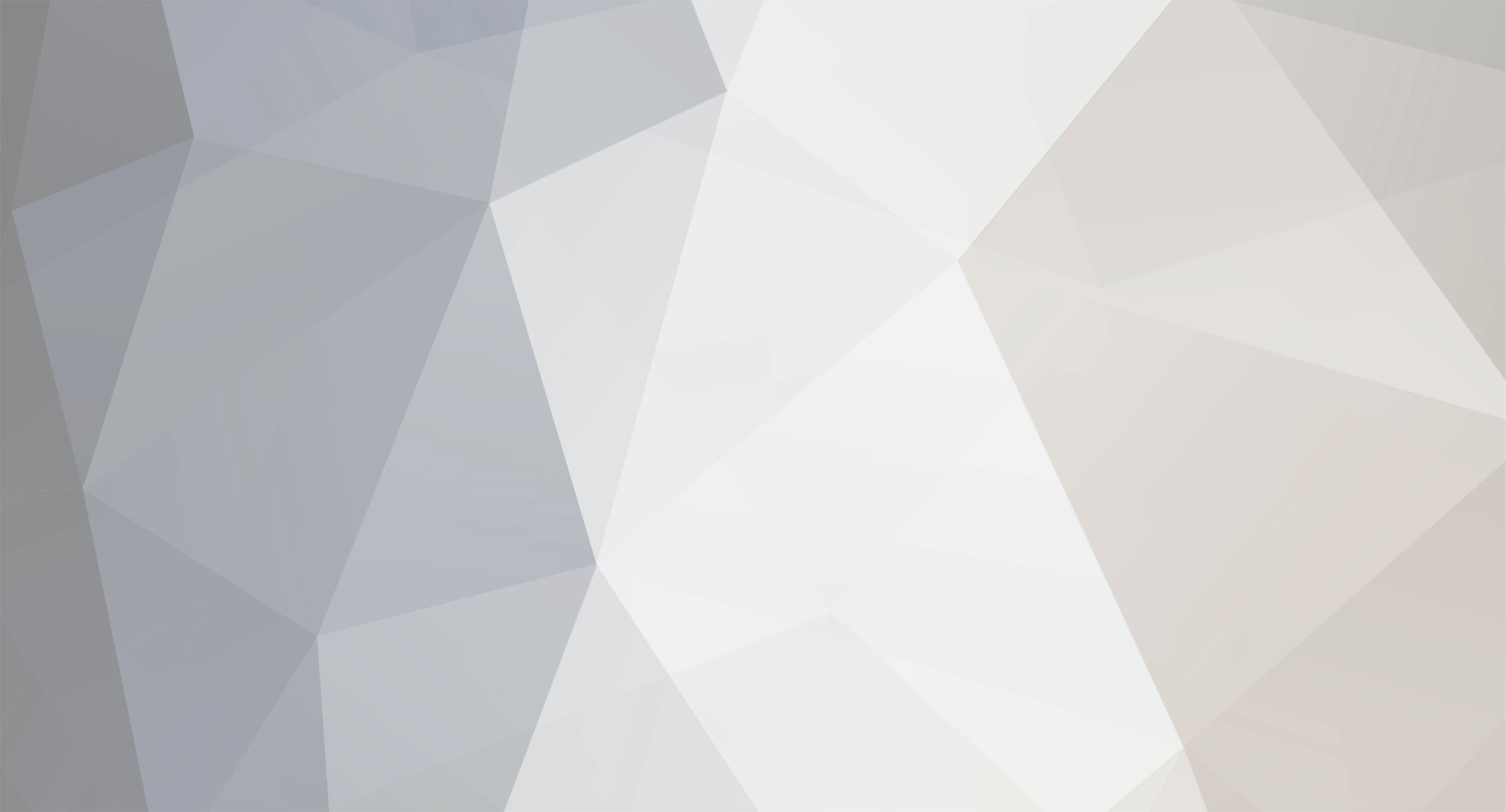
Gordo
Members-
Posts
243 -
Joined
-
Last visited
Personal Information
-
Location
N Ireland
Recent Profile Visitors
1244 profile views
Gordo's Achievements

Regular Member (4/5)
52
Reputation
-
The lintel seems over engineered but out of interest when working out any loading you should always include a "factor of safety" I generally allow a FOS of two but think 1.5 is the requirement for beams. I think for bolts and screws the FOS is as high as 7 or so. Where quality of workmanship is potentially suspect a greater FOS should be used. A structural engineer could confirm exact FOS required.
-
I would recommend 215mm solid common concrete block wall. 8 hours fire resistant and sound testing always works good (better than a cavity wall. Because there is no vavity you will not need to consider insulation to avoid thermal by pass. You will have to provide some returns to buttress the wall and limit flanking sound. otherwise it would be too slender and unstable, particularly in the event of a fire next door when everything starts collapsing. Structural timbers should not be built into separating walls to for sound resistance. If you want a stud wall it will generally have to be double stud construction with mineral wool insulation and two layers of 12.5mm plasterboard to each side. this stud wall will also require buttressing to be stable. The separating wall needs to extend to roof level and be fire stopped over to underside of cladding
-
how to discern which walls are load bearing?
Gordo replied to apricotandpearjam's topic in Building Regulations
You will need a structural engineer to work out the load paths, but i would imagine they are indeed load bearing. walls and piers supporting substantial beams and possibly concrete floors. If the walls support fire resistant elements they should also be considered structural. Building control will need to be notified regardless as you are changing the means of escape and possibly fire/sound resistant elements. I would imagine you will have difficulties with regards to the means of escape also under BS9991 for flats due to inner rooms situation. I assume the flat is accessed off a common protected corridor. Quite a few things will need consideration and likely too much for a simple forum question/answer. -
Cost for building regs: is £950 a reasonable price for this?
Gordo replied to Co1's topic in Building Regulations
Oh yes forgot about that -
Nonsense. The minimum guarding height at windows is 800mm in a dwelling (except for loft conversion skylights) edit scrub that. I wasn’t aware of part O in English regulations for overheating. Seem like tall openings are an issue for you guys without shading. Got to a have to look into that some time
-
For guarding as long as the opening is above 800mm fromFFL you could have a fixed pane below. To make it non climbable you need 600mm to sill or 600mm from sill to openings
-
A phased approach to BC drawings / approval?
Gordo replied to Alan Ambrose's topic in Building Regulations
Wow. They change regulations in N Ireland so Building Notices are only allowed for alteration works and extension under 10m2. Previous you could do even housing developments. Obviously removed it because it was such a shit show. -
I think guarding may not apply to MCU to a dwelling. Check schedules to MCU for a dwelling to see if guarding applies sorry I see this has already been answered
-
A phased approach to BC drawings / approval?
Gordo replied to Alan Ambrose's topic in Building Regulations
I don’t think phased/conditional approvals are recognised in the regulations. If BCO agrees to it it’s likely an adhoc affair that they may or may not agree to at their discretion. They would likely agree to approve with design details to follow for specialists works possibly like MVHR, PPC flooring, trussed, fire alarm etc -
Cost for building regs: is £950 a reasonable price for this?
Gordo replied to Co1's topic in Building Regulations
Do exempt buildings not have to be detached? The fees for extensions are based on the combined overall extension area. They are not separate fees for each extension -
Advice needed - should we change building control approver?!
Gordo replied to ARC Guitars's topic in Building Regulations
Don’t think BC would like this as fire foam is often limited to a small gap (maybe 1/2 inch) maybe cladding manufacturer could recommend suitable proprietary product or make up your own generic cavity barrier from suitable FR materials. See an extract from N. Ireland Guidance Document (English AD will be similar). Maybe compression fit mineral wool between a 38x38mm min. Batten and cladding or cement board/steel cut to follow profile and fixed to similar batten. Best solution may be If the intumescent strip cavity barrier is located close enough to cladding, it could fill the gap in a fire, while allowing for drainage and ventilation to rear of cladding. Check product details for max gap. Awkward junction to fill -
I’d say that would be good practice. Don’t think it would wick moisture much or any significant consequences, but you never know. Id guess not a big benefit in going much below level of floor insulation for cold bridging, marginal anyway. I often suggest 1st course of inner leaf from sub-floor/insulation level, should be in thermal block for the cost/benefit
-
anyone got any experience of sucking out blown fibre insulation I’d be interested
-
Advice needed - should we change building control approver?!
Gordo replied to ARC Guitars's topic in Building Regulations
It’s not an issue if the wall is far enough away from boundaries and not supporting a fire resistant element. -
Has anyone used https://www.buildingregs4plans.co.uk/ ?
Gordo replied to flanagaj's topic in Building Regulations
Past your bed time