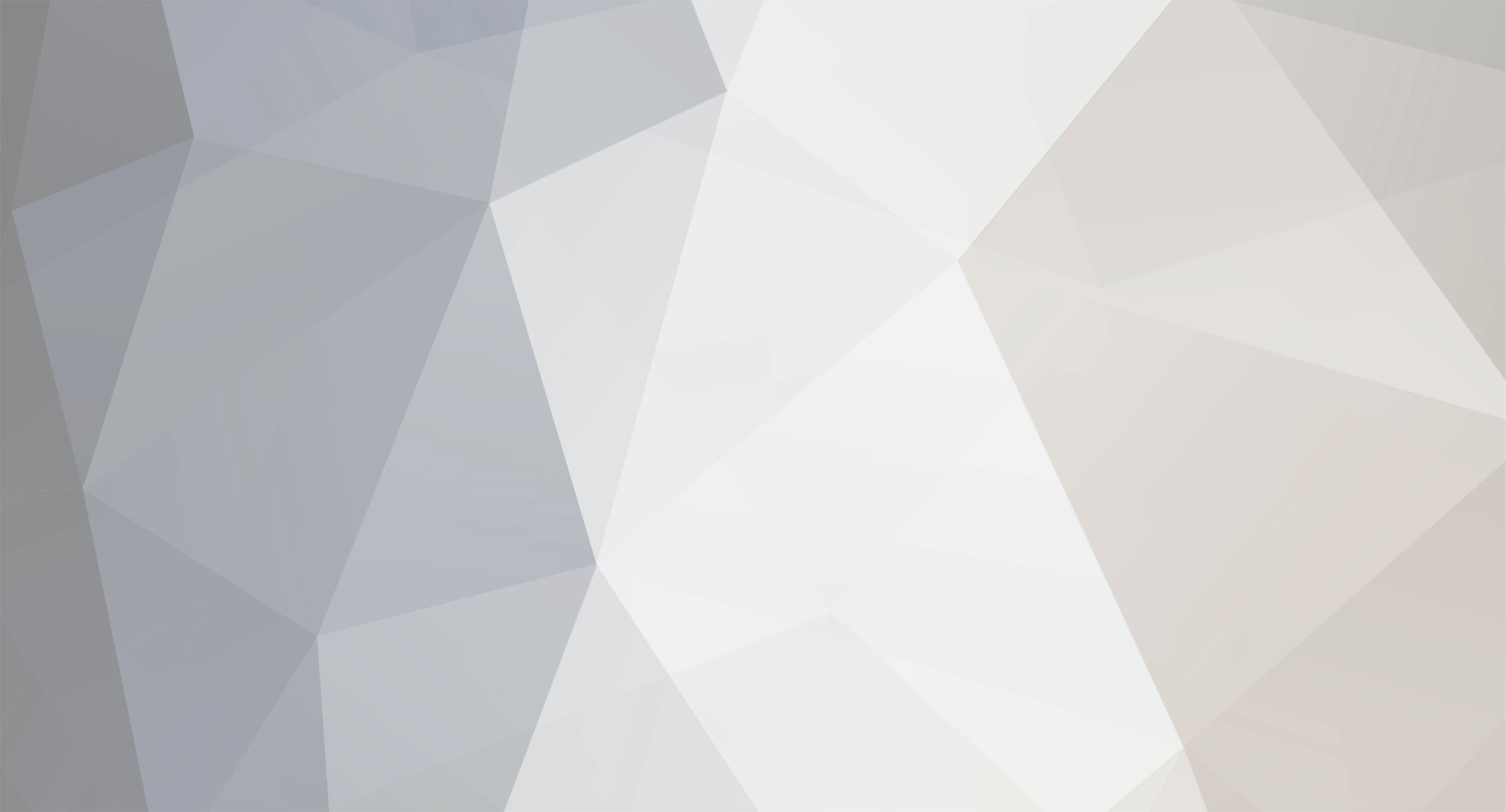
Kelvin
Members-
Posts
3846 -
Joined
-
Last visited
-
Days Won
44
Everything posted by Kelvin
-
Timberframe cladding - Cost of cavity barriers and insect mesh
Kelvin replied to AliG's topic in Timber Frame
Envirograf CV30/8 from here: https://passivefireproducts.com/category/passive-fire-protection-products -
I’d put in a request for a mains supply to Severn Trent to get confirmation whether it can be supplied or not and an idea of the cost. I’d definitely look to have my own water supply. In fact I wouldn’t buy a plot without it. I have an elderly neighbour who gets her water from another neighbour. That supply has run into a problem and she currently has no potable water. It’s been fine for years and now it isn’t. She can’t drill her own borehole as there are two very nearby and none of the companies are willing to do it. Boreholes can be expensive as it depends on how deep the hole needs to be and what needs to be done to secure it and what equipment is needed to pump it out and get it it into the house. Ask the farmer for details on the current borehole that provides the supply. It’s no guarantee that a new borehole will be the same design, ours is very different from our neighbour who is a few hundred metres away below us. For example ours is 147m deep his is 80m. To drill ours the vendor paid £18,000 and I paid £9000 for all the plant. A shallow hole with a simple install could be half that or less. I was chatting to a builder when I was in Stratford Upon Avon this weekend. He lives near Hastings and lives off grid. He has a borehole at 120m. Been fine for 10 years but ran dry last week. Boreholes aren’t a guaranteed water supply unfortunately. Personally I’d prefer to be on a mains supply given a choice. Water insecurity is a bit stressful. Another neighbour with a private supply loses sleep over it. I don’t so much as I’m relatively confident our supply will be fine but it’s not guaranteed and we don’t have an easy plan B.
-
Timberframe cladding - Cost of cavity barriers and insect mesh
Kelvin replied to AliG's topic in Timber Frame
Our architect put in metres of the stuff in the drawings. Thousands of pounds of it. I questioned it and then spoke with my BCO and we went through the regs and what he needed to see to comply. Saved us thousands of pounds. BCO was very pragmatic. -
I assume a full G99/G100 application rather than fast track? I have some options on adding a ground mounted array. I could add 20 panels on top of a cliff at the bottom of the garden. It has some complication being 80m from where the equipment is and has to cross a burn. Alternatively I have another couple of areas where I could add around 10 panels in two different groups which is beside the garage. Just need to do the sums on all the options. Alternatively I do nothing and just use what I have.
- 60 replies
-
- utilities
- electric bill
-
(and 3 more)
Tagged with:
-
Made from ‘the best quality recycled industrial plastic’ whatever that is. The LBC (large bastard cockerel) has signed it off so it’s all good.
-
Just assembled my second self-build. Only took 2 hours and no obvious structural problems. Still to fit the automated door. New owners not interested though.
-
What did you do to get the limit removed?
- 60 replies
-
- utilities
- electric bill
-
(and 3 more)
Tagged with:
-
We’ve got a 6kW export limit. The max generation I’ve seen is 7.5kW In theory in might go a touch higher than that but with an East/West array there’s only a small window where both sides of the roof are at their maximum output. The inverter can take four strings and I plan on adding an array on some ground in front of the garage and possibly another string behind the garage (both would be South facing) so we will then reach a point where we are generating more than the export limit unless I can get it raised. We did a fast track G99 application so I might have another go next year.
- 60 replies
-
- utilities
- electric bill
-
(and 3 more)
Tagged with:
-
Pretty much that. Nothing at foundation level or at eaves (1.5 storey building) We debated putting vertically at the corners but in the end just used wood battens at either side of each corner as that also gave us a better fixing for the cladding. This was all agreed with building control. The bigger issue for us was having to special order the stuff as it was an unusual size to fill our ventilated gap behind the cladding so we over ordered to make sure we had it then didn’t use a whole box of the stuff.
-
I just applied for outgoing so a few weeks away before I can start getting paid. At the moment I’ve mostly been self-consuming since 14 July when it was installed. It’s generated 1.01MWh and of that 227kWh has been exported. I could have reduced that a bit by having the EV connected all the time to consume some of the excess. I did put the system into AI mode for a while to see what it did. Starting from 100% SoC it exported the majority of the solar production. Then a few hours out from the cheap tariff period (Intelligent Octopus Go) it discharged whatever was left in the battery to the grid and charged it back up during the cheap period and the house load was grid supplied. It varied the times it did all of this depending on SoC of the battery and it seemed to learn our consumption pattern. One of the problems I see with this is it will cycle the battery much more so not sure I’ll use it.
- 60 replies
-
- utilities
- electric bill
-
(and 3 more)
Tagged with:
-
Most plots are sold with utilities nearby so up to the buyer to investigate how to get them to site and the cost. Some plots might come with utilities already brought to site. Some plots are just a bit of land with outline planning in the middle of nowhere and it’s entirely down to the buyer to investigate the feasibility. All of this is negotiable between the buyer and the seller. For example our plot was just a field with outline planning permission with no mains water or sewer connection. I made it a condition of the sale that the farmer had to find a source of potable water and I took responsibility for determining how to provide foul waste disposal and how to get electricity to the site. I had this written into the legals as a condition for buying the plot. If you can get the utilities to site for a reasonable cost then it makes the plot more valuable as less for the buyer to worry about.
-
Integrated/ flush solar panels on a metal standing seam roof
Kelvin replied to WisteriaMews's topic in Photovoltaics (PV)
Just keep in mind that if you have a detached garage as part of your build and the right orientation you can fit your panels East/West to avoid putting them on the roof of the house. It’s what I did after ditching the plan to ground mount them for a few reasons I listed above. My 19 x 445W array (10 on East elevation and 9 on the West) is working quite well and on a good day can generate over 40kWh. -
Danwood can also build to your design apparently.
-
There’s a Dan Wood bungalow near us. Went up quickly and it looks terrific from the outside. I’ve heard other good things about them. I also know someone considering using them.
-
We never had any mould but we did have loads that were knotted and bent. However given you have to cut some of them I used the worst ones for the cuts.
-
This is my favourite machine we’ve had on-site. Tank post basher. Fence round the house and boundary in. 300m of it! Next task is sell the Heras fencing.
-
Boiling water tap - Quooker alternatives
Kelvin replied to canalsiderenovation's topic in General Plumbing
Our softener is quite industrial but it’s in the garage but you can get relatively compact softener. If your water is that hard I’d definitely look into getting a softener installed. It’ll save a lot of grief down the road. -
Boiling water tap - Quooker alternatives
Kelvin replied to canalsiderenovation's topic in General Plumbing
Worth thinking about a wholehome water softener too. Limescale can cause all sorts of other plumbing issues long term. We have a Quooker and have had no issues with it. However I know of two people that both have had a lot of problems and they also live in hard water areas. Not a big dataset to draw any conclusions of course. -
Welcome. It’s doable but depends on a few things like what the ground is like, what’s the plot like (access, size, is it level or sloping) how easy (as in cheap) will the utilities be to get in, how complicated is the design, what type of build are you looking at, how much will you be doing yourself etc.
-
There are a few milestones for the self-builder - buying a plot, getting planning permission, the first spade in the ground etc. Taking the Heras fencing down is surely one of those. I took the last panel down today and the fencers are cracking on with the fencing and will be finished by Thursday next week.
-
Ours ticks all the wrong boxes and haven’t any problems insuring it for a reasonable rate. I’m not suggesting that it isn’t a problem just that it hasn’t been for us so far. But yes the more non-standard the smaller the pool of insurers and lenders there’s going to be.
-
The would certainly give you the upper end of the price scale to give you an idea how dear it could be. Dan Wood seem quite cost effective but still too dear for this budget. Here’s a 90m2 2 bed bungalow turnkey. https://www.dan-wood.co.uk/house-designs/bungalows/perfect-86e
-
80% of house in Scotland are timber framed although most are block and rendered outer skin. You also see loads of timber clad houses especially in the Highlands and Islands. They can’t all be cash buyers or tiny mortgages. It’s not something for us to worry about for 15 years+ and even then we’ll give it to the kids and they can not worry about it either.
-
Are there any modern basin wastes and traps that are reliable?
Kelvin replied to SimonD's topic in Waste & Sewerage
I like our Blanco kitchen one. It’s in two parts. A plastic but you twist to seal (or remove) and a stainless steel ‘pretty’ cap that you use turn the plastic bit. Not likely available for a bathroom sink but I like it because it’s just a plug so won’t fail and is easy to clean. The utility room is a more traditional push in plug which also works fine. Both bathrooms are pop ups for the sink and a lever for the bath. The bath one will inevitably fail eventually and I can’t get to the other end of the mechanism so will be replaced with a plug. -
One thing to consider that can be overlooked is furniture and furnishings. Obviously that has nothing to do with building the house and it’s something you can deal with when funds recover over a period of time. We intended just to use as much of the furnishings and furniture we already had to save money. However a lot of it just wasn’t suitable (our large L shaped sofa was too big for the open plan living room for example) or we didn’t like it in the new house. Consequently we’ve pretty much got rid of 90% of what we had and replaced it. Not a consideration for the house build but is potentially an extra cost down the line a bit.