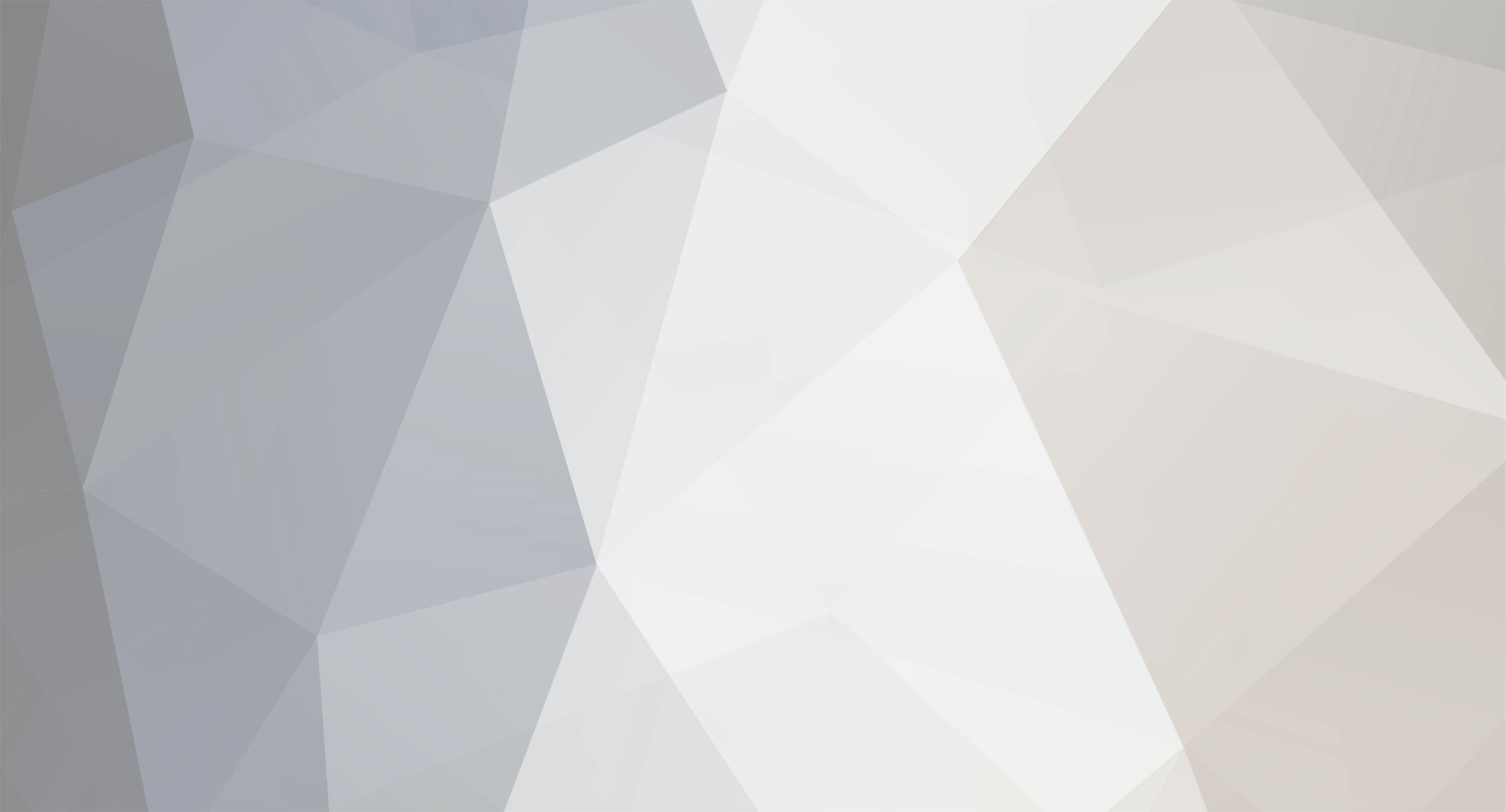
syne
Members-
Posts
58 -
Joined
-
Last visited
Personal Information
-
Location
S Yorks
Recent Profile Visitors
6662 profile views
syne's Achievements

Member (3/5)
12
Reputation
-
Did the prior owners give you any drawings? Obviously this was done with an intention to convert so it's likely got some kind of drawing somewhere.. I'm assuming the two white lines on the rhs are the current hip. Your likely going to have to: take the hip off and build your gable up, Have a beam, likely a steel from the gable apex to party wall, Continue the roof line to the gable, Build the dormer walls off the steel already in place, Get your stairs in Insulation, vcl, plaster, electrics ectect Not necessarily in that order. Firstly, Though get a tape pencil, A scale ruler measure it all, draw it as is then draw it as you want it - to scale. Send that to an SE and they'll likely send you a drawing with details of beam sizes and requirements
-
I'd say a self build is when you do more than 75% yourself. A true self build means hewing rocks from a cliffside a spinning 110drainage pipe from hand reared sheep .
-
So far: I had to have a SE for the calculation as the BC wouldn't accept my maths - grade c gcse:{ I've had a guy in to weld a post to a beam, and my neighbour gave me a hand with a steel that was bottom heavy on a ladder. I'll also have to have a spark connect a henley block and do the tests for bc. And the biggest expense will be a rendered as a simply cba to do that. 3 floor 7x4m extension and 8x 5garage . Digger came may'23 it's been a long tedious process when you're trying to carve out time around a full time job. But the end is in sight
-
You've made a good looking job of it so hats off. I suppose it's a case of who's going to put the effort/ time to make it good in the end. Imo, it irks when someone takes the easy way out and pushes the problem down stream for someone else to work around later it's not acceptable if your time saved is lesser than the fix to the shortcut. A prime example is footings being way off level, " Ahh it'll do, the brickies can fix that" = just spend a day slicing blocks to get the levels back.
-
So, I've gone with the super duper cheapo euro cell for my extension as I'm running out of money and well, they're cheap. But all the instructions state leave 5mm for expansion on each edge. But if I'm fitting them on the hottest day/week of the year is that 5mm actually necessary? Surely come autumn when they start to contract that five mill will become.. More.. Nothing like overthinking is there..
-
Well that's a bag of.... Paking's wasted. I might go become a professional window bodger, I'd get a gold star me thinks.
-
Just an FYI, acetone may damage upvc. My patio door frame did not respond well, the excess decking stain came off the frame easy but the areas touched by acetone are now different.
-
Too true, I've just started putting my windows in today and those cavity closers at now in the skip pile. 100mm of pir wedged in cavity and windows strapped to the internal leaf. I also used a 25mm pir below a cement board on the internal leaf for ridigity.
-
Sorry, never found out what they were called and no markings on them. i did see a couple of similar designs on modern bricks but the match was always 'off'. Best i can suggest is keep looking on fb marketplace. The reclamation yard in sheffield said hed buy as many as i could get him as he also struggles to get hold of them..
-
Very common on yorkshire housing estates in the 50s/60s im just north of sheffield and my ex council house is made of these. Couldnt find any for about 2 years then came across half a pallet of some similar ones on facebook. My rooftiles are a perfect match and came from Essex which makes me assume/hope that there are other matching bricks in other parts of the country. But i doubt it as bricks tended to be sourced locally back then. The garden wall bricks on the estate were made in kirkheaton which is fairly local. They're an absoute bugger to find matching ones for and i was tempted to go and buy peoples outhouses just to reclaim the bricks. Just keep scouring ebay ect. How many do you need?
-
Help with gf en-suite extension
syne replied to NorfolkingClue's topic in House Extensions & Conservatories
As its so simple, draw your ideas/ plans out and contactca local structrul engineer to do you calcs for lintels, joists, rafter members ect. I would go almost full width of the extention ion on the back(stop 20/30cm short of the downpipe) and come as far out as possible whilst keeping the pitch of the existing roof. If you built yourself.. <£15k + bathroom fittings... -
Before any of that, draw a measured (scale) plan of your house and property. Then get to drawing your extension yourself, imagine walking through it, how the existing rooms will be affected, stairs, landings windows ect. A lot of decisions will be constrained by the existing house (and budget) Do this with the people who will live in the house, get their input. Sketch different layouts ect, consider final finishes and landscaping. Then when you do call in proffesional designers youll have a much better idea of what you do/dont want
-
Anyone done their own building regs plans
syne replied to Professionally nosey's topic in Building Regulations
As said above, After planning is granted theres two paths to take; Building notice- where you'll recieve regular visits from the bco at certain stages of the build to approve whats been done and allow you to continue (or if you request them to visit site) Full plans submission- you provide a full set of plans on how its going to be built and the bco comes to check its been built as drawn. Between the SE and my own drawings i could have done full plans but went down the notice route because i wanted the bcos input on certain things. I will say though that the bco's are not consistant in their opinions, helpfulness or knowledge. I've had five visits and five different bcos. Some were very helpfull suggesting ways to do things and what would be acceptable, one was totally unintrested, and one completly clueless- clearly hadn't looked at the plans and was obsessed with insting on iwi for the garage! But overall a positive experience, suprisingly,likewise for the planners! -
If your building it yourself then whichever construction method your most au fait with, but as your getting a builder in then id say build it as you would an simple house. b Block,150cavity fullfill,block. Then its very simple and any builder can do it. Makes for easy render and easy internals. 45deg pitch will save a fair bit of hassle,Your going to have to build thay gable end up if you dont match the current roofline. Which leaves you a leaf magnet between the gable and the rhs pitched roof...
- 1 reply
-
- gym
- outbuilding
-
(and 1 more)
Tagged with:
-
Free CAD software recommendations please?
syne replied to marno17's topic in New House & Self Build Design
Bit late, but if you know any students... the whole of adobe creative suite is free. This includes sixth form students.