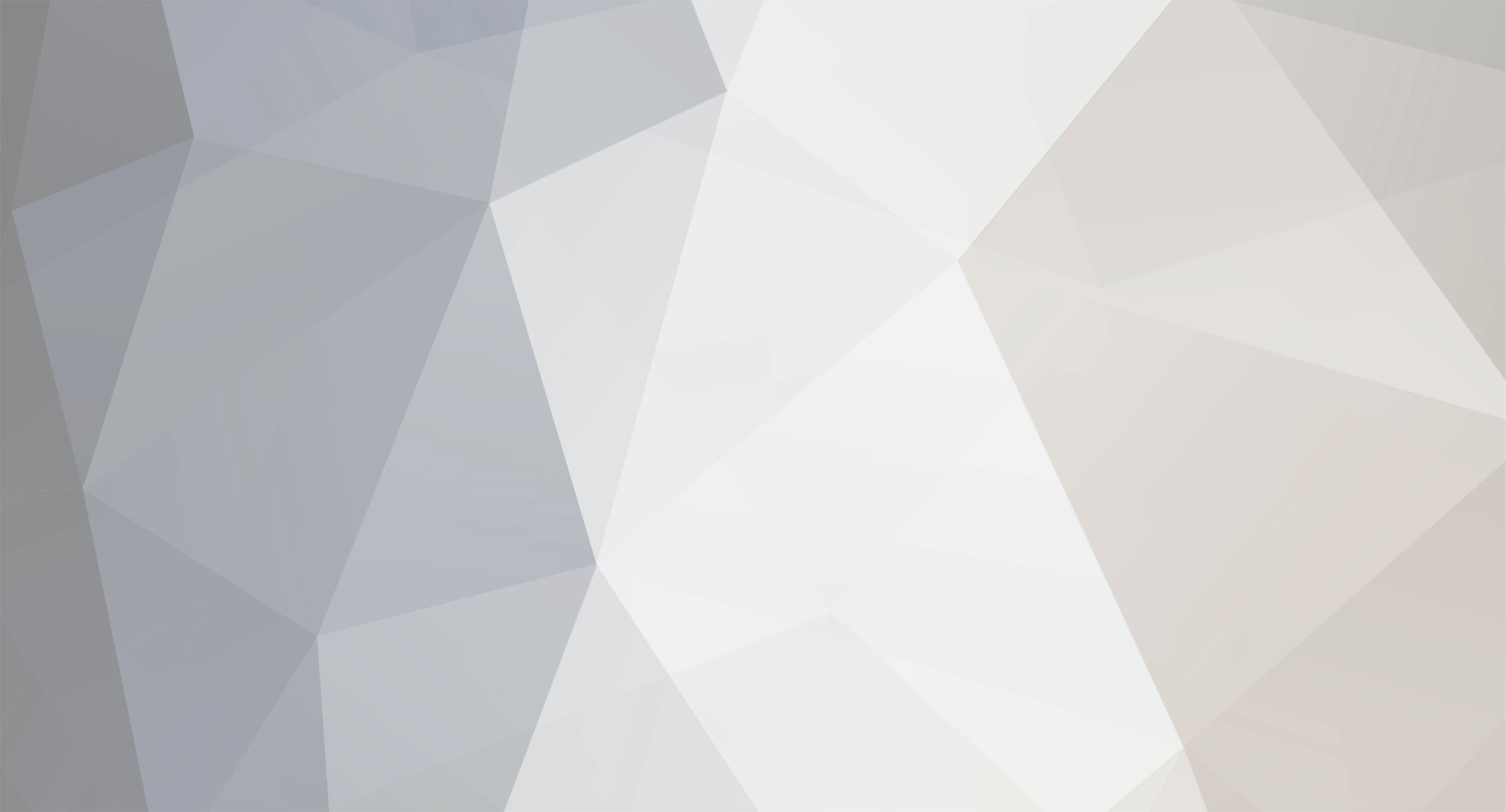
Annker
Members-
Posts
176 -
Joined
-
Last visited
-
Days Won
1
Everything posted by Annker
-
Posi joist - This install feels rubbish, thoughts?
Annker replied to boxrick's topic in Roofing, Tiling & Slating
Read a bit of this thread earlier in the week. Good to read you got that builder out the gate. Work at this stage can be rescued relatively easy. In this situation it's not essential that elements and connections look pretty, just need to be structurally sound and perform. In contrast bad work done at fitout stage can be much harder to rectified, and may forever look like a dog dinner You caught it in time, and have every opportunity to deliver a fine looking project now. -
Leveling old ceiling with GypCeiling MF
Annker replied to Annker's topic in General Construction Issues
Say with MF5 tophat section the primary support channel goes in a maximum 1200mm c/c. Can I ask what is the maximum c/c of support that GL1 requires, and therefore spacing of the GL6 support bracket? My plan is to install the GL1 perpendicular to the existing joist, and therefore put a GL6 bracket on every 4th joist which works out a little less than 1200mm c/c -
Leveling old ceiling with GypCeiling MF
Annker replied to Annker's topic in General Construction Issues
I found the BG spec sheet for the system. GL6 is the bracket. It's exactly the system I want. Simple, fast solution and easy to get right👍 Just to add for future reference BG only list the GL6 which has long leg, other manufacturer & suppliers offer a GL5 with a shorter leg which is a better option when looking to keep tight to existing timber joist. -
Leveling old ceiling with GypCeiling MF
Annker replied to Annker's topic in General Construction Issues
I actually think the 30mm is borderline ok. The only place I believe it could show up is any margins around joinery fitted in the alcove. And as the alcove are ~ 1/3 of the width of the room the ceiling in each of them will only be running ~10mm off. Can't see any issue for the plaster finish either, the ceiling is a flat plane. I don't care to remember how many concrete soffit/ceilings I battened out in the past. We did a lot of apartment blocks that way. 2x2 battens fixed to the soffit with express nails and then counter battened again with 2x2(without nail guns). Dusty, noisy, over head work. I hated it. -
Leveling old ceiling with GypCeiling MF
Annker replied to Annker's topic in General Construction Issues
Thanks Nod, I wasn't aware of that system. I'll have a look around their website, sounds like it could be a very good option. -
Leveling old ceiling with GypCeiling MF
Annker replied to Annker's topic in General Construction Issues
Just to add in another question for opinions. In one room the 1st floor joists are running 30mm off level front to back. There is no subsidence and it seems they were just installed this way; they aren't bowed down too much and otherwise the ceiling is flat. The ceiling is about 3m high and 30mm fall is along a 4.7m long run. I wonder if such a fall would be noticeable and should I go to the effort of level out this ceiling? 30mm is a decent amount to have installed a joist off level but I'm not certain this will be noticeable in the finished ceiling. (I may level the floor above though). -
Leveling old ceiling with GypCeiling MF
Annker replied to Annker's topic in General Construction Issues
I've sometimes used that method in the past but it is considerable more work and harder to achieve a level finish (I'm a carpenter so experienced at this sort of work) The other alternative is sister along the joists with 3x2, possibly could get away with using 2x1/12. This would be a little less expensive material wise (vs MF system) but more labour. I have 2x row of solid bridging therefore x3 sistering pieces per joist. Less work than counter battening below the joists but still more work than MF system options. -
Bit of a niche question. On my renovation project I have stripped back all lath and plaster ceilings to bare joists, in preparation for new plasterboard and skim. The underside of the existing joists are up and down, and in some areas two rooms have be knocking through to form one bigger room. Therefore I need to level the underside of the joists for the new continuous ceilings. I've previously installed MF ceiling in new build project however unsure of how to go about it in a renovation job. My plan to maintain ceiling height, is to screw the MF7 primary support parallel directly to the existing joists. Essentially the MF7 will be within the joist void and therefore the ceiling height will only be lowered be the thickness of MF5 top hat section. Is anyone familiar will the system and know if this an accepted arrangement?
-
Looks like a good solution but as I've only about a dozen pockets to do it's probably too expensive an option.
-
Yes the "Tony tray", I had it well researched but must have been rushing and its inclusion was forgotten. By top plate I'm referring to the horizontal top plate of the studded wall. Basically just end the VCL along the ceiling line, don't fit it in around the joists and tape it along the top plate of the studded wall. The option to have the VCL cut in around the joist will be a bit of a faff alright, however if its required I will do it.
-
Appreciate any ideas on the following issue to overcome. When constructing my stick build TF extension I mistakenly left out a strip of VCL that I believe is now (at fit out stage) needed to link together with the VCL proper. The design for the VCL was either going to be the PIR foil layer taped as required, or the addition of a sheet VCL. My designed TF build up is broadly as section below: I'm at the stage now of measuring up insulation and looking back at an old thread I see I missed installing a strip of VCL around the joist ends as per image below: So now I am wondering how best to detail/install the wall VCL at the ceiling/floor joist to wall junction as its now built Do squares of VCL need to be cut in around each individual joist void pocket and taped to the joists or can the VCL be simply taped along the continuous top plate? Similarly, at 1st floor ceiling/roof level I'm unsure how the wall VCL should be terminated. I have a VCL installed externally above the osb, so again I will not be now able to link it to the internal wall VCL.
-
Fine tuning my IWI Solid wall (Warm Batten) design
Annker replied to Annker's topic in Heat Insulation
Understood, that makes sense to me. -
Fine tuning my IWI Solid wall (Warm Batten) design
Annker replied to Annker's topic in Heat Insulation
Sounds good, thanks it's very useful to hear others experience in the absence of your own. I think I will still opt for insulation within the studwork for a couple of rooms. Namely two rooms that have bay windows. Here it would be preferable to keep the depth of buildup to a minimum around the bays otherwise the proportions of the individual wall panels start to look off. Here I may keep the studwork 10mm-15mm away from the brickwork and pack a little insulation behind the stud. -
Fine tuning my IWI Solid wall (Warm Batten) design
Annker replied to Annker's topic in Heat Insulation
My concern is that I have some large area walls, 3m high ceiling and almost 5m long. In such large areas do you think flexi batts would maintain their installed position long term? I have actually just ordered a bag of mushroom head insulation fixings, I was going to experiment with these to see if they may help keep either rockwool or flexi wood fibre boards in place. -
Fine tuning my IWI Solid wall (Warm Batten) design
Annker replied to Annker's topic in Heat Insulation
Not choosing rigid specifically over flexi on a material basis; rather that the rigid boards can be bonded to the brickwork in continuously layer as opposed to flexi batts that need to be fitted between studs and therefore the insulation layer missing at every 400mm c/c stud. Although perhaps the lower u-value of the timber stud vs insulation discounted? -
Posi joist - This install feels rubbish, thoughts?
Annker replied to boxrick's topic in Roofing, Tiling & Slating
Shocking work. I'd say if there are payments pending or about to be made to the builder halt them immediately. Unfortunately I imagine you are going to have some frustrating weeks ahead. -
Fine tuning my IWI Solid wall (Warm Batten) design
Annker replied to Annker's topic in Heat Insulation
Thanks for the pointers Mike, considerate of you. Being a carpenter I have many different types of saws mains, battery and arm powered! I'm still finalising the spec, only certainty is that gypsum plasterboard & skim will be the finishing layers. In terms of insulative performance and mitigation of interstitial condensation risk, I'm ranking rigid wood fibre board bonded directly to the brickwork with adhesive number 1. That choice will require the entire depth of studwork to be in front of the insulation depth, however it also then creates a service cavity of good depth, so this buildup would work well in the kitchen and bathrooms where services and domestic borne moisture will be most prevalent in the house. In rooms and walls where there are fewer services ran and less habitation, (guest bedrooms and hallways), I am thinking that flexie wood fibre or rockwool batts fiction fitted into timber studwork would perform satisfactorily. I had initially thought of using the same buildup throughout but I suppose I can "upgrade" to utilise natural fibres in the areas of the house where greater volumes of moisture are created. -
Fine tuning my IWI Solid wall (Warm Batten) design
Annker replied to Annker's topic in Heat Insulation
I find it strange then that Rockwool require the cavity space, although I think there is more joined up comprehensive knowledge in these forums than the technical departments of some of these companies! Furthermore I'm now leaning towards using wood fibre board instead of rockwool. Just monitoring RH levels in the house atm, and despite it being well dried out RH is at 70%, which is at the upper end of the scale. So I'm thinking the £1k extra opting for wood fibre over rockwool may be a worthwhile expense. -
Fine tuning my IWI Solid wall (Warm Batten) design
Annker replied to Annker's topic in Heat Insulation
Yes similar setup to your arrangement. The brackets are needed for that particular system though, as the studs are gyplyner type not C or I type. I actually called Rockwool tech dept with a couple of questions. The fella I spoke to recommended/was insistent that in IWI usage the rockwool batts are friction fitted between studs and that the studwork (and batts) are both stood 25mm off the existing brick wall. In effect creating a 25mm (unventilated) cavity space. @Iceverge in the example you shown earlier I understood that the rockwool batts were pressed up tight against the existing brick work. That arrangement makes sense to me, as otherwise the unventilated cavity is created and that seems like an environment where condensation could potentially form. Whenever I speak to product tech depts I invariably think I should not have bothered calling! -
Fine tuning my IWI Solid wall (Warm Batten) design
Annker replied to Annker's topic in Heat Insulation
I found a video on Youtube of a method of IWI installation that maybe of interest to some. Notwithstanding the absence of a airtight layer/parge coat and the inclusion of a vcl, otherwise it seems like a good arrangement to achieve a quality finish. The gyplyner stud keep the rockwall nicely in place, however one concern is cold bridging risk from the gyplyner brackets. I wonder if the brackets were separated from the wall with some manner of rubber gasket would that solve the cold bridging risk? -
Self installed Air Conditioner
Annker replied to Annker's topic in Mechanical Ventilation with Heat Recovery (MVHR)
Actually found a couple of threads here on the site and elsewhere and it seems to a regulated installation. R290 charged systems may be ok to self install but not R32 systems (which may be preferred?) Seems similar to installing a boiler, perhaps I could find an supplier/installer willing to let me do the grunt work of the install at which point they do the final connection, inspection, commission, etc. However that setup can get messy and I have a lot of other work to do, so I'm thinking this is a job I needn't get involved in. -
Self installed Air Conditioner
Annker replied to Annker's topic in Mechanical Ventilation with Heat Recovery (MVHR)
Thanks @joth, useful to hear your experience. I PM'ed a domestic project a few years ago, and there was as you call it a mini-split system installed. The suppliers/installer were very competent so I let them at it and didn't pay much attention to how it was done, hence questioning now. Like you I'd go for the minisplit system and good to hear it's not rocket science to install. Just had a quick look on Aircondirect.co.uk. was it one of the electriQ iQool units you bought? Prices look reasonable but I see it says that The unit must be installed by a F-Gas qualified AC engineer, but perhaps that is more or a recommendation than requirement...... -
Has anyone self installed an Air conditioning system on a project? I am considering a small AC system in my victorian refurb project, AC in the master bedroom and open plan kitchen/dining/snug area. On the face of it the ducting, containment and general fixing seems doable. I'm a carpenter so will be doing the required builder work myself anyhow, but I have no idea how involved the "plumbing" part of the system is. Is it just a matter of compression fitting together pipework and have my electrical liven the system up or will there be soldering and a more technically challenging installation. Perhaps it is an item where it is just much better to get the professionals in?
-
Fine tuning my IWI Solid wall (Warm Batten) design
Annker replied to Annker's topic in Heat Insulation
Bit more workable with soft sand, just as it would be in a regular mortar mix. Mix up a few different ratios and see how it goes, you can always recoat and the materials are pennies worth. -
@Iceverge Yes certification isn't a concern in any event as the project is a renovation. And yes, I had been wondering if air tight tapes were essentially strips of air tight membrane, certainly a cost saving to be had if they are.