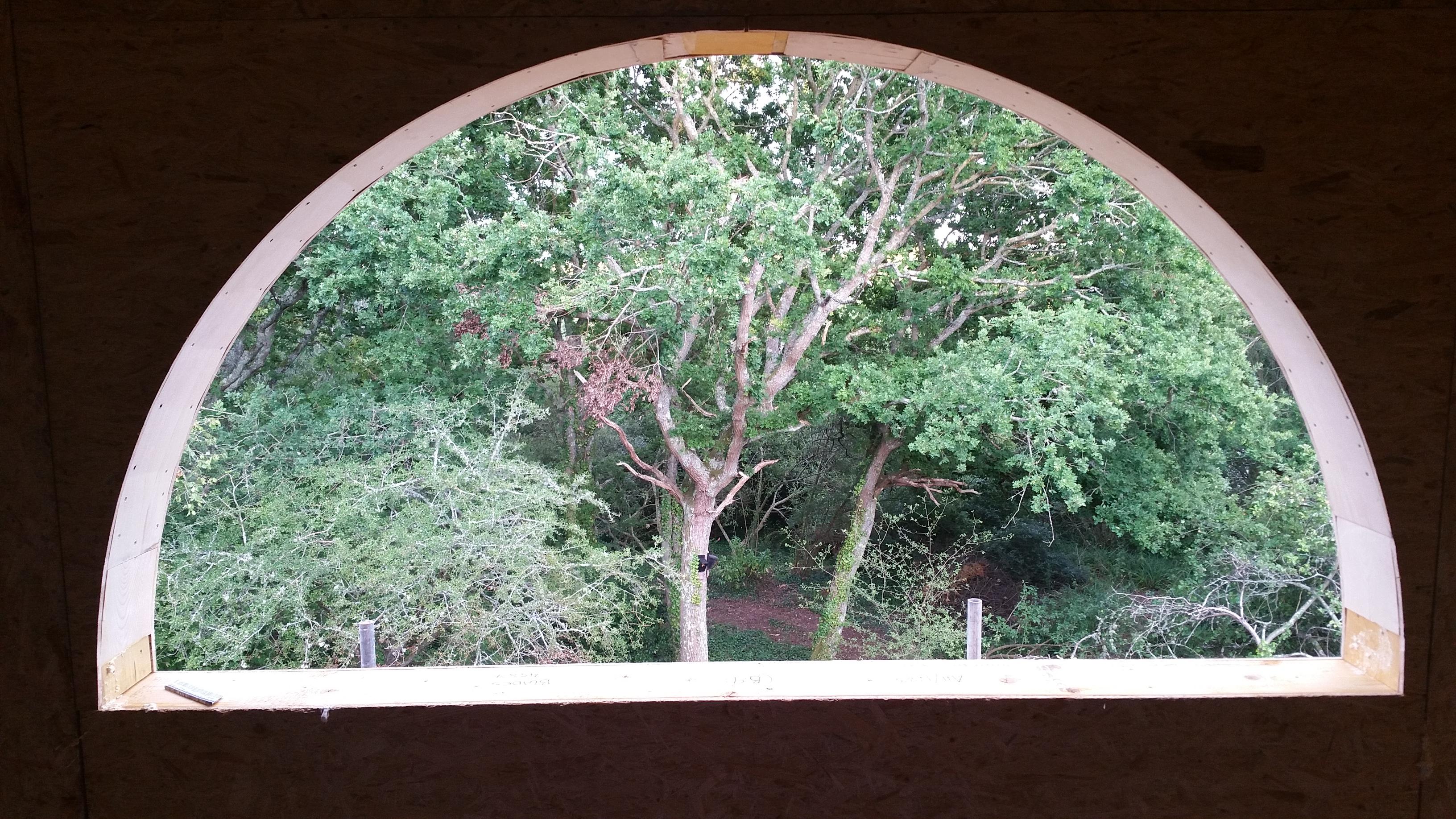
dnb
Members-
Posts
575 -
Joined
-
Last visited
-
Days Won
10
dnb last won the day on December 23 2022
dnb had the most liked content!
Personal Information
-
About Me
Building a SIPS panel house on the Isle of Wight, in the muddiest swamp I could find.
Just call me Shrek! -
Location
Isle of Wight
Recent Profile Visitors
The recent visitors block is disabled and is not being shown to other users.
dnb's Achievements

Regular Member (4/5)
331
Reputation
-
I put up bat boxes, but our local woodpecker population decided they were going to evict the bats. Guess they can't read the endangered list. We are working out the last few details for digging our pond. We have smooth newts so I am hoping they like it
-
Collecting the materials for finishing my roof
dnb replied to dnb's topic in Roofing, Tiling & Slating
The second bit I know... But this very sensivlke advice comes about 4 years late. I'm not changing anything now!! For the record the BCO and warranty folk were happy with the C24 graded 2x1.5 I sourced for reasonable cost, and happy with all of the fixing plans. My understanding is that the documentation has moved on a stage now so perhaps I wouldn't get away with it so easily now, but if that's the case then a product would have become available. @junglejim The BS document isn't freely available. The BSI like you to buy it from them! But you can usually find the useful sections from it in places like a LABC technical guide or NHBC documents. -
I have an rs485 based modbus connection working on cat5e for my solar inverter data. No problems so far.
-
Guessing that the problem here has come from the cavity side and it's only been noticed when the whole frame depth is affected. I am going for a similar theory to @ProDave - something is allowing water into the cavity and it's getting to the back of the frame. Another window (or something) above it without a drip cove on the sill that lets water track into the cavity? The pictures suggest there is no cavity closer for that window.
-
And I thought the 2 lift scaffolding staircase I had was posh! (and very useful for getting stuff up to the top) Is it just me, or did they spend all the money on scaffolding so couldn't afford labour to mix the brick packs up thoroughly?
-
Had a bit of fun playing find the good bits of metal with the MIG and the inevitable running out of wire on Easter Saturday. All together again and back to doing the landscaping. Going to need to do a few more repairs over the next winter I think but all OK for now.
-
Looking good! Finishing this job off myself and can say that Steico do indeed make a very detailed document saying what you can and can't do. I spent ages reworking the design to minimise joist penetrations and keep the holes away from the edges and the other (electrical) constraints - it was like doing circuit board design all over again.
-
I bought mine because I have a lot of work for it that I couldn't do all at once. I'm still "winning" over hiring because the flexibility is worth a lot to me especially when I've had experiences of weeks where there were zero available diggers for hire on the whole island. You can imagine how much they were costing to hire that month, and what the terms for "one more day" were... A bit of servicing and welding every so often isn't so bad if you have the equipment. It's worth highlighing that this sort of repair should be a consideration for running your own plant, especially if you buy an older machine. In hindsight a better cover for the worst of the winter months would have been a good idea.
-
But boring in the extreme! The weekend was the first fine weekend of the year where I was not working. So I put a bit of time into getting the digger serviced and ready for the spring groundworks. During testing it made a bad noise and on removing the battery that was more or less hanging on by the cables found the battery tray was slowly disassembling itself like a 1970s vintage Jaguar! Heaven only knows how the -ve terminal connected to anything through that rust! I resolved to fix the digger that day because it will be good for a biscuit or two in "House not finished anonymous" and the weather looks good for getting some industrial weeding done later in the week. Cardboard will work, won't it? Maybe not the cardboard. It's even less conductive than rust. I found some steel from the stores (read scrap heap). Bends formed with a bit of angle iron and a hammer. And it even fits in the hole. Welding and painting will be done next time I am not at work.
-
For the purposes of thread closure, I have managed to find a sufficient stock of obsolete parts to keep things going for a bit longer for not much cash outlay. In the end it was a degraded sensor wire shorting on to the case causing the PCB problem (they have been replaced and tied up properly), a sick pump start capacitor and a sticky part in the 3 way valve. All of them displaying intermittent symptoms. Cash flow preserved for the moment... Only a small gas fitter bill. I can now get back to all the other broken things I need to fix and think about a plan for insulation improvements and a heatpump should we decide to keep this house.
-
Some progress... we got the pcb working by swapping out the dead VDRs and a fuse. Everything works apart from the ignition spark. Needs new electrodes or coil but that's why there are gas fitters.
-
There is insufficient space between us and the neighbours, plus restrictive covenants to contend with. It's a non-starter unless I had a few months to sort things out with planning and the beneficiary of the covenants. All of it costs and we won't be living here in a few months with any luck.
-
Not been a good day. Our 20+ year old Glowworm Xtramax boiler has died. It made what I can only describe as a "selection of bad noises" when I was in the shower and when I got out to see what was wrong everything was dead - no LCD display, lights or faults. The fuses are all OK, even the one on the PCB but there's no apparent life. Are there any experts on antique Glowworm boilers here that could provide some insight? I would prefer to not have the expense of replacement given we're not going to be here much longer but it might just be better to accept that 20 years of relatively trouble free life is a good for a boiler since a cursory internet search doesn't turn up replacement PCBs (I'm assuming this is the problem given the total lack of life). What is a good economic make & model to replace it with? I dimly remember the spec as 28kW with 50 litres of DHW storage. I'm not convinced our 80s built house works with an ASHP for a number of reasons - efficiency and lack of garden space being the 2 most important - so I am stuck with gas.
-
Low loss headers and plate heat exchangers for air source heat pumps
dnb replied to dnb's topic in Boffin's Corner
Tell me something I don't know... It's one of the reasons I don't see the need to "penny pinch" with a solar diverter and an immersion if I can meaningfully sort out a few hours of storage. I can just take the benefit (small as it is) from offsetting. In the summer I will use the PV for the A/C as well as the DHW. Again, this drives the need to sort out some form of meaningful storage that doesn't hit efficiency too badly.