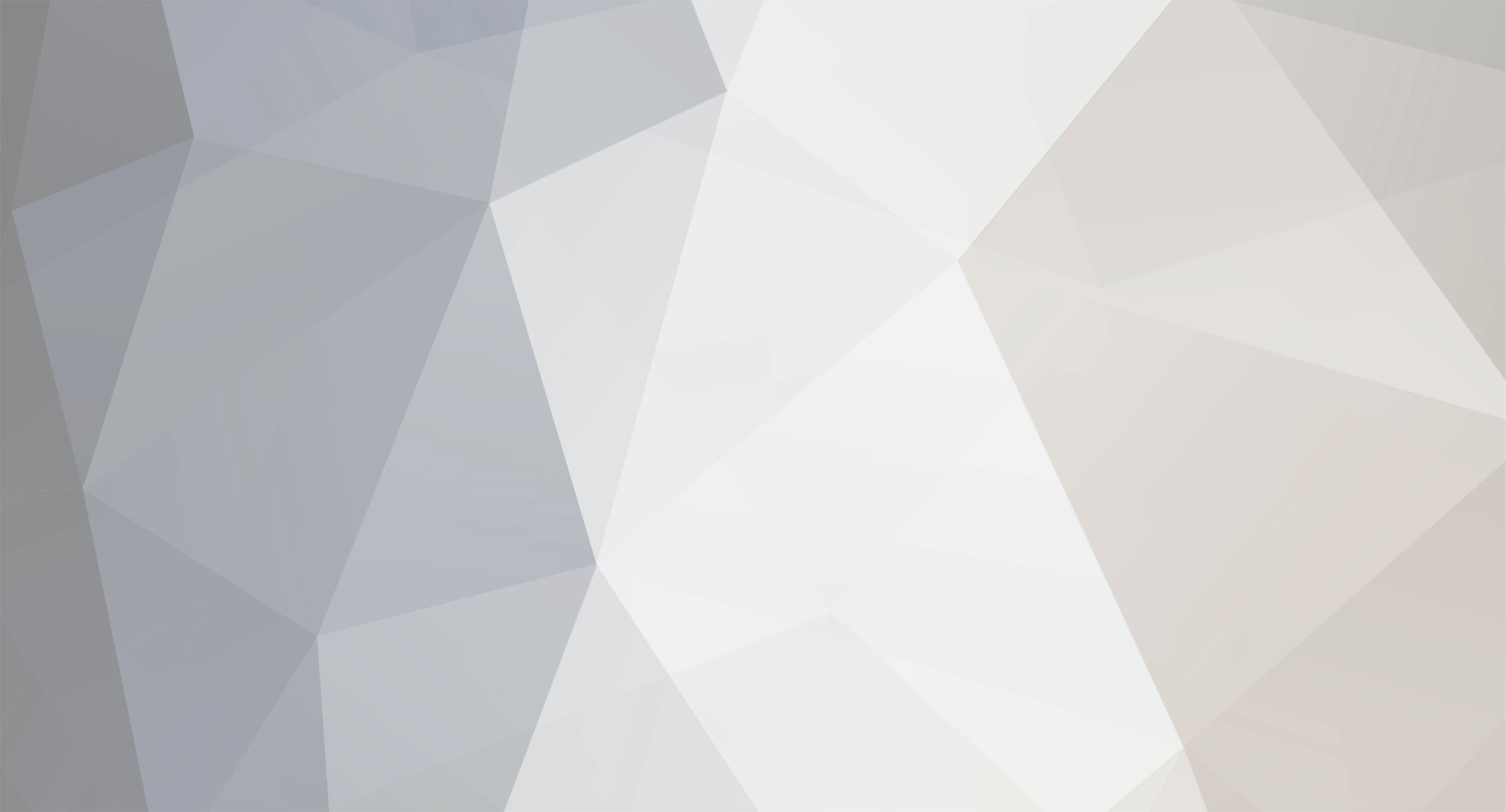
Nick Laslett
Members-
Posts
576 -
Joined
-
Last visited
-
Days Won
1
Everything posted by Nick Laslett
-
I believe the “commercial CEN Standard windows” certification is more stringent than the domestic version. Due to commercial windows needed for high rise office blocks. If you look at their domestic Ali Vu window U-value spec, they state: ”Using a domestic CEN Standard window, U-Values as low as 1.1 W/ m2K” PURe range is primarily intended for commercial use, so it makes no sense to get them certified for the less stringent domestic CEN standard. Good info here on some of the other lower U-value Aluminium windows with new types of thermal breaks. https://www.doorandwindowexperts.co.uk/13554/origin-twin-flush-window-with-aerogel/
-
Dust collection for handheld power tools
Nick Laslett replied to RichyB2024's topic in General Joinery
I guess this is where the Leros really shines, because it is such a large head and the speed control is very sensitive. The FST is still quite robust. Unlike sanding wood, I use very little pressure and let the orbital head do all the work. -
Dust collection for handheld power tools
Nick Laslett replied to RichyB2024's topic in General Joinery
I was lucky to find a 2nd hand Leros and vac on eBay. I used 180 grit for FST. Even for sanding the actual fermacell boards 80 grit is a bit aggressive. You have to be very careful or you will create tramlines at the board level. @Nickfromwales, is right that Fermacell is a real bugger to work with. Unlike plasterboard you are trying to fit the actual boards as accurately as possible. Otherwise it is very unforgiving. I picked up the Dewalt Grabo, which makes fitting the boards a lot easier. My substrate was either ICF wall or metal framing. For the stud walls, I used two layers of fermacell, with staples for 2nd layers, this greatly helps with getting a good fit with the glue. So the boards are already pretty flat. The trick is to use many thin layers of joint filler. Then FST to finish. Mix small batches of joint filler because it goes off very quickly. Impossible not to have some joints with 1mm difference in the boards. But you should be able to use the joint filler to build up the difference. We have boxing all around the ceiling for MVHR ducting. We used a lot of aluminium corner beads. In this picture you can see the massive amount of joint filler we used, but the sanding was minimal. Here is a YouTube playlist of three videos. The first one is from a French couple. Lots of good techniques shown across the clip. They have other videos. -
Dust collection for handheld power tools
Nick Laslett replied to RichyB2024's topic in General Joinery
@markharro, use less joint filler. The FST is for finishing and sands very easily. If you are spending a lot of time sanding the joint filler, you are putting too much on. Better to go over joints and screw heads twice, with less material. I bought a 2nd hand Mirka Leros with 1230 dust extractor. This worked brilliantly for finishing all my Fermacell boards. With a team of 2 we did 280m2 in about 6 days. You can skim Fermacell boards, but you need to seal the surface first, or the plaster won’t adhere. Talk to the Rep about the best method. For cutting Fermacell boards, I used the Mirka 1230 dust extractor with my Makita track saw, with a PCD Fibre Cement Cutting Blade. These tools did the whole job, no issues, no failures, we must have cut more than 150 boards. For sanding the FST The Mirka Leros with the 1230 dust extractor has been great, I was amazed how little dust was created. Sanded FST. Painted. -
Good discussion here about cold bridging, includes discussion of window reveals.
-
Not sure if this helps, but here is a wall plate detail from Beco Wallform: https://becowallform.co.uk/technical-data/construction-details/wallplate/
-
Boiling water tap - Quooker alternatives
Nick Laslett replied to canalsiderenovation's topic in General Plumbing
Drinking water quality… HUGE can of worms!!! We are in the safe hands of Ofwat and the commercial water companies for the quality of our drinking water! Here is a UK Government note on Water Hardness: https://www.dwi.gov.uk/consumers/learn-more-about-your-water/water-hardness-hard-water/ Document ‘G’ sets out the regulations. Here is an FAQ that covers the topic of “wholesome water”: https://assets.publishing.service.gov.uk/media/5a81a884e5274a2e8ab552a5/160321_Part_G_FAQ.pdf Here is a good primer on the topic of softened water from a water treatment specialist: https://watertreatmentservices.co.uk/drinking-softened-water/ Here is the standard for our water: https://www.dwi.gov.uk/drinking-water-standards-and-regulations/ You can check your local water quality on your suppliers website. Here is an example. https://www.stwater.co.uk/my-supply/water-quality/check-my-water-quality/ Use the Water company HQ post code CV1 2LZ for results. TLDR, Your main drinking water supply should be from the mains. Recommendation is not to regularly consume large quantities of water that contains more than 200mg/L of sodium. You will need to test the water provided by your water softener to see if it is below this limit. For a comparison reference, here is the water analysis for Buxton Mineral water https://www.buxtonwater.co.uk/bottled-water/still WHO paper on Sodium in drinking water: https://www.who.int/docs/default-source/wash-documents/wash-chemicals/sodium-background-document.pdf -
Boiling water tap - Quooker alternatives
Nick Laslett replied to canalsiderenovation's topic in General Plumbing
The one in our one bed rental flat is still going, installed in 2000. The one in our 4 bed house was replaced after 14 years. The engineer from Harvey quoted the 10 year average lifespan. -
Boiling water tap - Quooker alternatives
Nick Laslett replied to canalsiderenovation's topic in General Plumbing
We have used Harvey Twin Tank Water Softener for more than 25 years in Kent. Good for a house of four. They usually last 10 years. https://www.harveywatersofteners.co.uk/products/water-softeners/ The newest model is overkill as it has SMART functionality!!! We bought direct from these guys and self installed. https://newatersofteners.co.uk/collections/harvey-water-softener-range/products/harvey-twintec-s4?variant=44088604033260 -
Sounds good. But a bit busy with many social events. Early Sept will work better for me.
-
Anyone got a WUFI Pro licence?
Nick Laslett replied to Drellingore's topic in General Self Build & DIY Discussion
I came across this tool the other day. https://www.sbse.org/resources/opaque Might be off interest. -
@Wadrian, here are some useful links to previous threads discussing this topic. This is the best anti-MVHR thread. *Edit: Just had a re-read of this thread and it brings back many memories from the forum. Here is a good discussion from 2017. This thread from 2021 is the classic retrospective question. This is a more recent version of the same question. When I first joined the forum, I was very resistant to the MVHR concept. But I eventually saw the light. MVHR does add a significant cost to the build. You also need to design it into the fabric of the building as early as possible. You can DIY install an MVHR system and there is a lot info here to help. If you look at a lot of the classic BuildHub threads on MVHR, ASHP, Hot Water Manifold, Fancoils, etc you will realise that an optimum build possibly has a plant room in the centre of the house to hold all this kit. So sometimes I feel that the most pertinent question is, “how would you tackle the services and plant room aspects of your build differently, now that you understand all the trade offs?”
-
We’ve got a high water table and the groundworkers abandoned the first attempt at the STP, when the hole collapsed. We are in a former gravel pit, so the soil is not robust. The second attempt was a very serious affair, with another 3 man crew joining the three guys already on site. The shuttering hire, and associated plant, was an insane cost. Photo from the morning of the install. I have a lot of photos of each step, happy to share, if helpful.
-
I like @Nickfromwales two suggestions. I also think the EPS suggestion from @Russell griffiths is fine.
-
Jablite High Performance Plus + Insulation EPS70 vs Recticel Eurothane® General Purpose PIR Insulation 0.030W/mK vs 0.022 W/mk Jablite 3x200mm sheets @ £148.29 Ex-Vat = £49.43 per board Recticel 1x100mm sheet = £27.48 Ex-Vat 1x 75mm sheet = £22.57 Ex-Vat Total 175mm = £50.05 https://screedsdirect.co.uk/collections/recticel/products/recticel-eurothane-r-general-purpose-pir-board?variant=40556563300531 https://screedsdirect.co.uk/products/jablite-high-performance-plus-insulation-eps70?srsltid=AfmBOord9lW6rrH3pBXBluMjLWsRabq32G_jbK5bzgxaccxMfvfZJLZB I buy most of my materials from these guys, free delivery on purchases over £500. I’m sure you can find cheaper versions of the EPS, but I try to stick with established brands where I can. My vote would be for highest ceiling height possible with a U value 0.11, with 100mm of concrete for best decrement delay and heat capacity. Over the long term ceiling height trumps everything for me. No idea if concrete actually performs better than screed, I’m sure someone will correct me if necessary.
-
Nothing special. ASHP with UFH upstairs and downstairs. Solar Control glazing with moderately sized windows. MVHR with attention to air tightness. Small roof overhang of 50cm, which doesn’t do much and needs to be more like a metre. Back in 2019, when I first joined BuildHub, the house overheating issue featured in a lot of discussions. @Jeremy Harris’s ideas were very helpful on this topic. We have an ICF build with insulated slab foundation and insulated poured concrete first floor. The ICF core is 150mm. All this concrete gives the house high decrement delay. A good primer on the topic here. https://www.greenspec.co.uk/building-design/decrement-delay/ We also have the Zehnder Comfopost, but as the MVHR isn’t commissioned, very hard to tell what effect this will have. If it reduces the house temp by 2°, I will be happy with the investment. I worked in the Middle East for 12 years, and have developed an aversion to A/C, so that wasn’t going to work for my build. I didn’t discover Fancoils until too late in the design process. An ICF build lends itself to things like poured concrete stairs, poured concrete first floor, etc. These were very specific design choices that were a prerequisite for our build. Not a fan of timber frame construction and all the associated building movement and high levels of sound transmission. Which requires a lot more skill and attention to mitigate IMHO. The first floor UFH is specifically there for cooling the bedrooms, we have more pipework in this floor than downstairs. SWMBO didn’t want radiators, so that was also a design consideration.
-
I had a play last night calculating the Cooling required for my build using LoopCAD. The house is already in the software from the UFH loops and Heat Loss calculations. This is strictly US/Canada using Manual J. The tutorial is pretty good. https://www.avenir-online.com/AvenirWeb/support/tutorial/?productLine=loopcad You need a North American location as Manual J is US/Canada only. I choose Victoria Gonzales, British Colombia. This is a whole topic of its own, where else in North America has weather similar to London. Anyway, you then need to configure the walls, windows etc. To make it quicker, I just used the best U-Value defaults in Manual J. This came out with a peak cooling load of 4kWh, which is the same as my heat loss, whatever that means. Basically the two short heat waves we’ve had this year in my neck of the woods, all ready confirmed that my current approach to cooling delivers what I need. House is built so maybe a bit late for some remedies. Might have another play with the latest version of LoopCAD as I was using the 2020 release.
-
Here is a video from John Cantor talking about ASHP cycling in great detail. Might be too geeky.
-
EPDM - Viable for a full roof?
Nick Laslett replied to Mulberry View's topic in General Self Build & DIY Discussion
@Mulberry View, I have a similar product to @JohnMo for my flat roof also from Sika, Sikaplan SGK-15. https://gbr.sika.com/en/construction/roofing/flat-roof-productsandsystems/single-ply-roofing.html Sika have so many different roof covering products that I find their website very difficult to navigate. We used these guys, they were friends with the scaffolder. http://jcservicesltd.com/services/cladding-installation -
@SBMS, looking at your responses in the heat loss thread you had -10° as the coldest design temp and 4 Air Changes an hour in the spreadsheet. My understanding is that the 4 air changes per hour is the minimum air purge requirement in building regs for domestic dwelling. This is not the steady state figure you should be using for the spreadsheet. Also, are you sure -10 in the actual average coldest temp where the house is located? My house is a similar size to yours, with similar U-values, but my heat loss is around 4kWh.
-
@YodhrinForge, are you going to use something like genie clips for decoupling? Soundstop show their decoupled sound proof wall buildup having a sound reduction of 56 decibels. This is with a 36 db single skin brick wall despite what the picture shows. Metal has much better acoustic reduction properties than wood. You would need to adjust the gap to suit your insulation requirements as 50mm of rockwool is probably not enough. E.g. you would add timber battens to the wall first, then the genie clip with furring channel.
-
Air tightness advice required for masonry build
Nick Laslett replied to ruggers's topic in Ventilation
I didn’t use AeroBarrier. Not sure if they were operating when I was making these choices. I have an ICF build so the walls and floors already have good airtightness. My air test will be happening soon, so wish me luck! For my window installs I used Illbruck TP651 compriband tape, Illbruck FM330 foam and Siga Fentrim tape. I have Thermohouse roof boards, so used Illbruck FM330 foam and Siga Wigluv tape for the board joints. I used Siga Fentrim for the wall/roof junction. I have a steel frame roof structure, where the Thermoroof boards are fixed to the timber on top of the steel ridge beams, I used Siniat Foil Roll Intumescent Acoustic Sealant. For MVHR inlet and outlet, I used Illbruck FM330 foam and Triton TT Vapour Membrane paint. We have two dormer windows. For the dormer cheeks I used Pro Clima Intello membrane, with Siga Wigluv tape. -
Other members thoughts on different options from a few years back.
-
Air tightness advice required for masonry build
Nick Laslett replied to ruggers's topic in Ventilation
My airblower door test guy had just tested a house that had the AeroBarrier treatment and he was amazed with the results. To paraphrase him, “it was a no brainier.” My approach has been to keep it simple, if you can. The less steps, less trades, less materials, less things that can go wrong. Despite all the taping, sealing, foaming you do yourself, it is hard not to still fret about if you’ve done enough, or if the work is good enough. I have an ICF build, so the actual walls didn’t need any extra considerations, but all the junctions soon mount up. The material costs too.