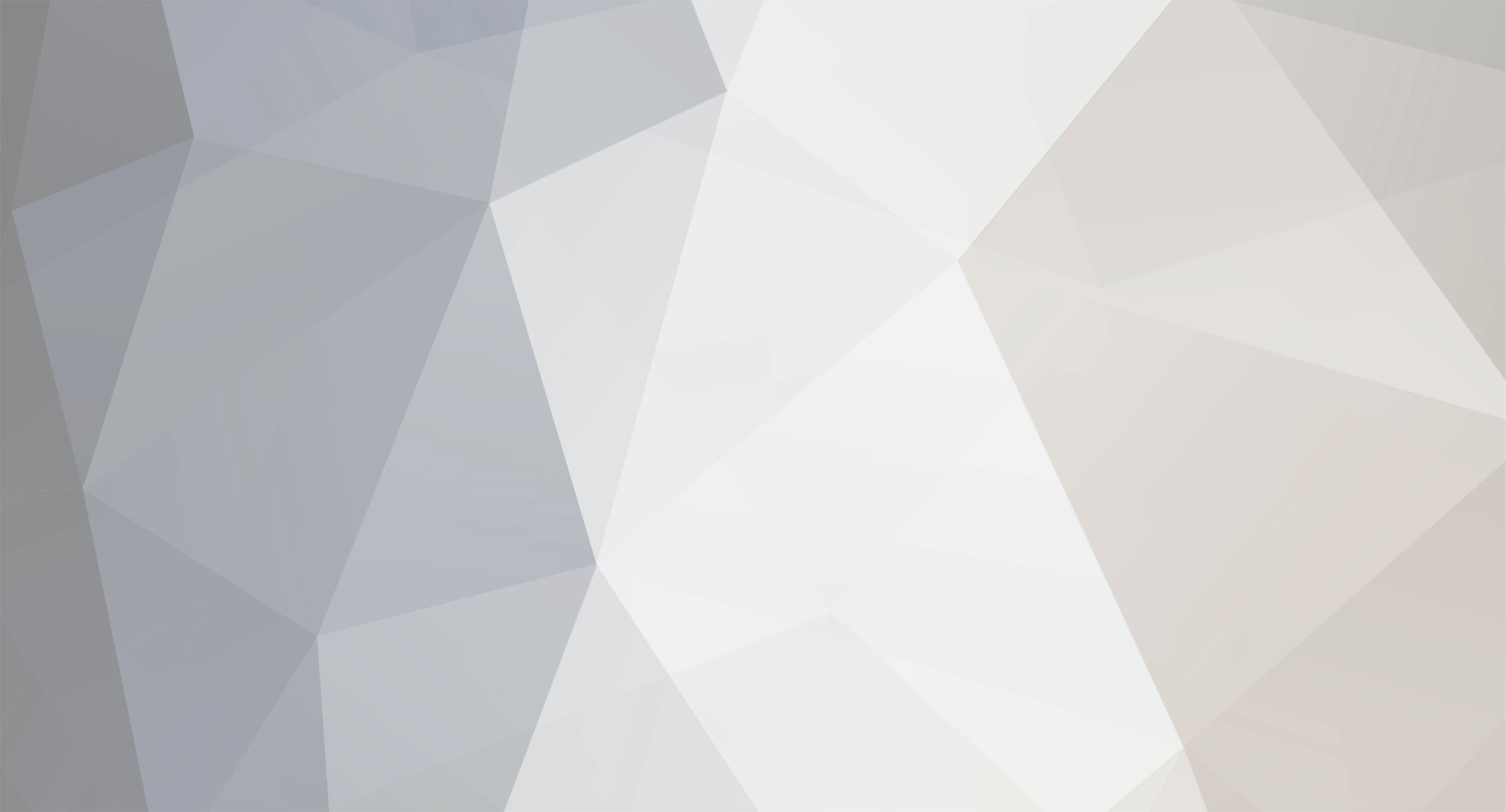
FuerteStu
Members-
Posts
373 -
Joined
-
Last visited
Personal Information
-
Location
Suffolk
Recent Profile Visitors
The recent visitors block is disabled and is not being shown to other users.
FuerteStu's Achievements

Regular Member (4/5)
173
Reputation
-
I did the garage conversion floor in dry sand and cement mix.. Mixed on the driveway by a volumetric mixer. I calculated I needed 1.8m2, asked for 2 to be safe. Used a laser level and wheelbarrow.. Got it done in about 3 hours. However, the guy must have just emptied his wagon... It was the day before Xmas eve. I had over 2m2 left over on the driveway. Filled up two tonnebags with it and built a ramp to the front door as well.. Had to get a skip in the new year to get rid of it all.. That was the worst part of it all. If you want tips on doing it yourself I worked out a few.
-
Do we get to name the podcast? I vote for "needs more duck tape"
-
In my experience, over tightening of bolts is the main issue in metal failure. Not only can it damage the thread on the bolt and cause it to fail, but the abrasion of over tightening can remove the protective layer around it causing another weak point. Torque wrenches are as much about preventing over tightening than they are about tightening to a minimum torque. And don't even get me started on split ring washers and them actually increasing the failure rate of bolts.
-
Door linings: narrower than the opening
FuerteStu replied to Post and beam's topic in Doors & Door Frames
Ah, so you mean wall thickness.. Mine was a couple of mm either side when I offered up the lining in the garage conversion, and I was tempted to fit it, then Architrave and caulk the gap.. I ended up trimming 5mm off the lining. Much better job -
3/4" to 1" Adapter on outside tap problem
FuerteStu replied to machtucker's topic in General Plumbing
-
3/4" to 1" Adapter on outside tap problem
FuerteStu replied to machtucker's topic in General Plumbing
I've got an irrigation setup with similar timer. I used a splitter on mine, which allows me to still use the tap without disconnecting the system! -
Starting my upstairs shower room and toilet.. Blank canvas. I've already got a layout that works, what I'm asking for are any tips and 'things that went wrong' or 'we wish we had'. Relatively small budget, expecting most of it to go on tiles to improve the 'look'. Maybe I'm just over thinking it, but thought I'd post in case anyone had any advice. It's in a timber frame loft conversion, pozi joists floor and ceiling. one external wall. My plans are roughly. Marine ply floor tanked, tiled. Tanked Tile backer walls, tiled. Centrally placed 4" humidity sensitive extractor, flexi to wall in ceiling. Tall Towel rad next to shower. Soil stack exits top right next to WC.
-
Smart thermostats - Nest thermostat losing many features
FuerteStu replied to JohnMo's topic in Other Heating Systems
Undoubtedly. But accountability is something we should be fighting for. Right to repair it's one thing, right to functionality should be in there too. Perhaps a legal precedent case, the public vs Google. Something sold as smart should remain so for the lifetime of the product (20 years seems reasonable) -
Smart thermostats - Nest thermostat losing many features
FuerteStu replied to JohnMo's topic in Other Heating Systems
Nothing will change as long as people keep spending money and nobody complains. Time to start drafting letters to MPs -
Smart thermostats - Nest thermostat losing many features
FuerteStu replied to JohnMo's topic in Other Heating Systems
Whilst I understand that companies projects must eventually be discontinued, if you buy a smart thermostat you don't expect it to be bricked by a company that can afford server space to keep it running. Smart devices should be backed up with a service guarantee for at least 20 years. It should be written into consumer rights. -
Density based stud finder recommendations
FuerteStu replied to BotusBuild's topic in Tools & Equipment
Magnetise some iron fillings and dust the wall with them? That will find your screws quickly -
making a bar from wood (man cave style)
FuerteStu replied to lord mud of the flyes's topic in General Joinery
20240612_192919_1.mp4