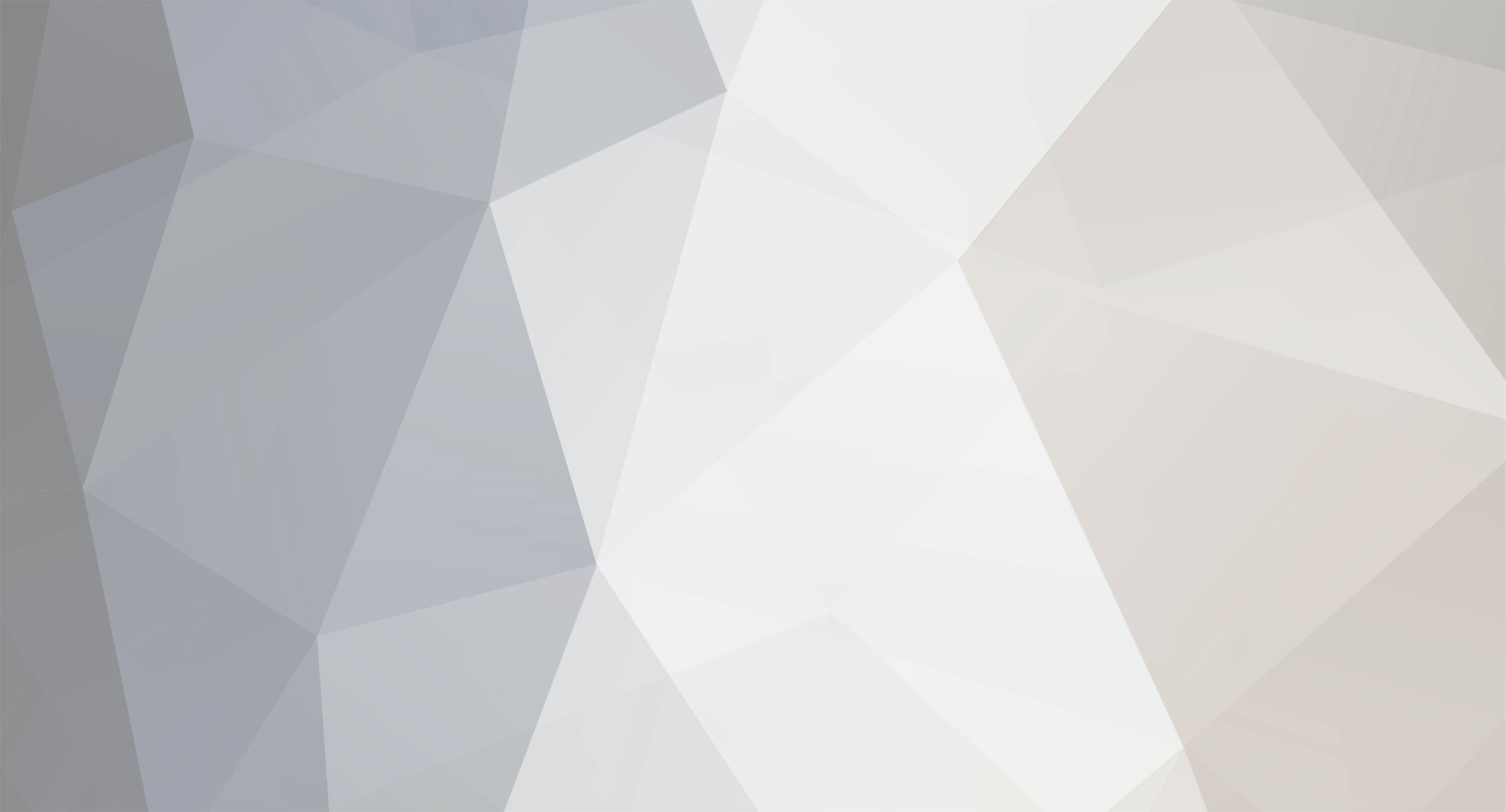
Dunc
Members-
Posts
55 -
Joined
-
Last visited
Personal Information
-
Location
Englandshire but migrating North
Recent Profile Visitors
2735 profile views
Dunc's Achievements

Member (3/5)
9
Reputation
-
One risk with silicone is that paint doesn't stick to it so if you end up with even a thin smear left on the adjacent wall and want to paint that wall in future you may have issues. Only because of that risk I'd go with CT-1 smoothed with a square cornered silicone profiling tool and then paint it.
-
Combining radiators with UFH - some surprising conclusions
Dunc replied to sharpener's topic in Air Source Heat Pumps (ASHP)
Forgive some daft questions: Why is Tret bottomed out at 20 when r is either 0 (Tret from UFH =20) or 1 (Tred from rads =20)? Again at the extremes of the graph, why are TretUFH or TretRads different from TretCombined when r is either 0 or 1? i.e. when the entire flow (r) is going to either rads or UFH alone why is the "combined" return temp not the same as the one open circuit? ta. -
Can I set up my site before building regs approval (Scotland)
Dunc replied to Dunc's topic in Building Regulations
Just to be clear, I meant "Building Warrant" rather than "building regs" - sorry I can't edit the post or title. In Scotland, Building Warrant approval is requierd before starting construction; this is different from England/Wales. I'm asking about what I can do to facilitate living on a site that has full planning approval but beofre starting construction of the hosue and before we have submitted our building warrant application. The Highland Council have a specific exeption in Planning Permission for temporary accomodation on site: "Living on Site During Construction: Self-builders often want to reside on site in temporary accommodation (caravans) during building works. Providing detailed planning approval has been obtained for the house, we consider this to be ‘permitted development’ during building works and you do not require planning permission for this aspect. We will however require the temporary accommodation to be removed once the house is built." From https://www.highland.gov.uk/downloads/file/22985/self-build_guide Sounds like Utilities are likely to be OK and that it's worth a phone call with Building Standards dept. to clarify stuff. In my case I have SEPA approval for a sewage treatment plant with direct discharge to a water course. @Jenki are you saying that installation of the STP was prior to BW sign off but the drainage field required inspection, or both STP and field were subject to inspection? thanks -
What can I do with my site before I achieve building regs approval in Scotland? We want to put a static van on site to live in during the build. Logistically it would be useful to have this in place sooner than later in the overall proces. So before we achieve building regs approval can I: Get and electrical connection made? Get a water connection made? Install the sewage treatment plant and outflow? Anything else it might be useful to do?
-
Technical Design Quote - sound about right?
Dunc replied to AppleDown's topic in Surveyors & Architects
Possibly not the same thing as we're in Scotland so must submit for building warrant before starting. Our architectural technician has quoted: Stage 4 Preparation of Building Warrant drawings based on Approved Planning package 3500 Submission of application, start forms ,completion 89 each Dealing with building warrant points 250 Engineer’s certification and design details in regards structure (Allow subject to quotes from engineers) Allow 2200 TBC Drainage Design Allow 675 SAP 375 EPC 190 CDM Pre construction Plan 350 all + VAT I think this assumes that the foundation and timberframe design will be done by the engineer and the TF supplier, respectively. We then have the option on: Constructional package, precast, steel, window schedule etc. 850 This provides construction based package for build combining engineers package to architectural technician's package So I'm expecting to spend £8675+VAT to get through building warrant. I suspect the submission of start and completion forms to planning will be 2x£89 that I can easily save. Other than that, I'm expecting to just pay the money to get it right. -
@kandgmitchell May I ask: how big is the raft (square meterage) and roughly what shape (simple rectangle vs something fancy)? I've just had my quote from MBC for ours and nearly fell off my chair... thanks
-
That looks stunning! Do you have a shot with that lovely kitchen island in as well?
-
I believe that is a non-aerated primary tank (i.e. just a settlement/septic tank) connected to a secondary treatment system based on filtration through fibrous media (peat/coconut husk) to bring it up to EN12566-3 (i.e. the same as a stand alone Sewage Treatment Plant). The secondary system is available stand alone: https://www.premiertechaqua.com/en-gb/wastewater-treatment/ecoflo I looked into it when we found we couldn't construct a suitable percolation area for a stand alone STP, but was told that it would still require a drainage field, as @ProDave found. I never found anyone who would clarify whether the purpose of the drainage field after an EN12556-3 compliant system is to provide further cleaning of the output, or whether it is solely to distribute "clean" outflow under ground thereby preventing creating a stream or puddle on the surface.
-
closed panel walls fixings Fixing to the internal walls of a passive house
Dunc replied to KevT's topic in Introduce Yourself
from the makers of one coated OSB3, smartply: https://mdfosb.com/en/faqs/smartply-propassiv Should fixings used to fix panel be taped over? It is not necessary to tape over the fixings used to install PROPASSIV providing that the fixings have not been removed and reinserted or predrilled. I take this to imply that if you put a screw in and leave it alone, then the integrity of the airtight panel should be intact. -
closed panel walls fixings Fixing to the internal walls of a passive house
Dunc replied to KevT's topic in Introduce Yourself
This is a question I have on my list too (although for the distant future). Surely the battening itself is screwed to the coated internal boards. If so, is the supplier sealing each screw hole or around the edges of each batten? Or is the screw itself sufficient to maintain the airtight integrity? -
Standard units to the wall for me. I did think that the two full height corner units were standing like menacing sentinels in the corner. I'd just blank off the opposite side as you've now got a kind of cubby-hole effect next to the oven unit. Or maybe blank it at half depth so that the kettle & toaster are behind the line of oven units, but the cubby-hole isn't a full 600mm deep. I'd want a large radius on all corners of the island unit, expecially if there are children around.
-
Hmm, not a strongly positive reception there. As most of the rest of the plot is covered in this stuff, I'm already OK for the driveway and a storage/unloading area. But I'm sure I could find some use for it. Was hoping it might save a bit of cash at this early stage.
-
Just trying to gather information so I don't get laughed out of the office when I speak to a SE about foundation design. Ground investigation reports "a safe bearing capacity of 75-100kN/m² will be available for foundations placed on the medium-dense, coarse sand found approximately 0.8mbgl." and "recommend trench fill foundations or strip foundations with a sufficient number of courses of under build to ensure that the dwelling is founded on soil with a sufficient bearing." All good. The site has previously been used and has a covering of some kind of MOT/hardcore/stone surface. The layers are, top down: Top layer is ~ 200mm deep Soft to medium - dense, grey/brown, slightly gravelly, silty, fine to medium coarse sand with crushed angular rock with an underlying white geomembrane liner. MADE GROUND. [what as a punter I think of as "hardocore"] Second layer is ~200mm deep Soft to medium - dense, grey/brown, slightly gravelly, silty, fine to medium coarse sand with crushed angular rock with an underlying black, hexagonal geogrid. MADE GROUND. Third layer is ~400mm native peaty topsoil which will have to be removed. Fourth layer is the suitable load bearing material - Medium - dense, grey, damp, slightly gravelly, silty, clayey, fine to medium coarse SAND with angular cobbles. Fragments of loosely bound clayey sand embedded with gravel. Occasional angular and rounded cobbles. I'm wondering if the made ground could be re-used as the base layer of an insulated raft. If I can strip that off and save it, remove the native peaty topsoil down to load bearing ground, could I stick the made ground back in, in compressed layers. An insulated raft is probably at least as deep (400mm) as the removed topsoil. Could I end up back at ground level without having to import much material other than the draining layer and fine support layer for under a raft?
-
I used worktop express for oak worktops. Seemed a good price and quality. I cut them to size on site (just in case their tape measure is different from mine!) but probably didn't need to worry as the 3m and 4m lengths supplied were within 2mm and spot on 635mm width. Occasionally there's a small knot or bit of filler in one of the timber pieces which can be exposed when a cut is made, which is presumably what the disclaimer is about. I never hit one, and the cut edges when coated with oil look exaclty like the pre-coated edges originally supplied. If the cut edge is against a wall it doesn't matter anyway. If you're using the cutting service don't forget to allow expansion gaps against walls/cabinets in your measurements.
-
I worry about corrugated steel. One timber kit supplier pointed us in that direction but I'm concerned about how poorly it ages. For example: as built 2011: https://maps.app.goo.gl/87Emx8RcxWQobNC49 10 years later rather rusty: https://maps.app.goo.gl/ZnLtrH7N5X3VUR8x9 maybe it's supposed to be "rustic"?