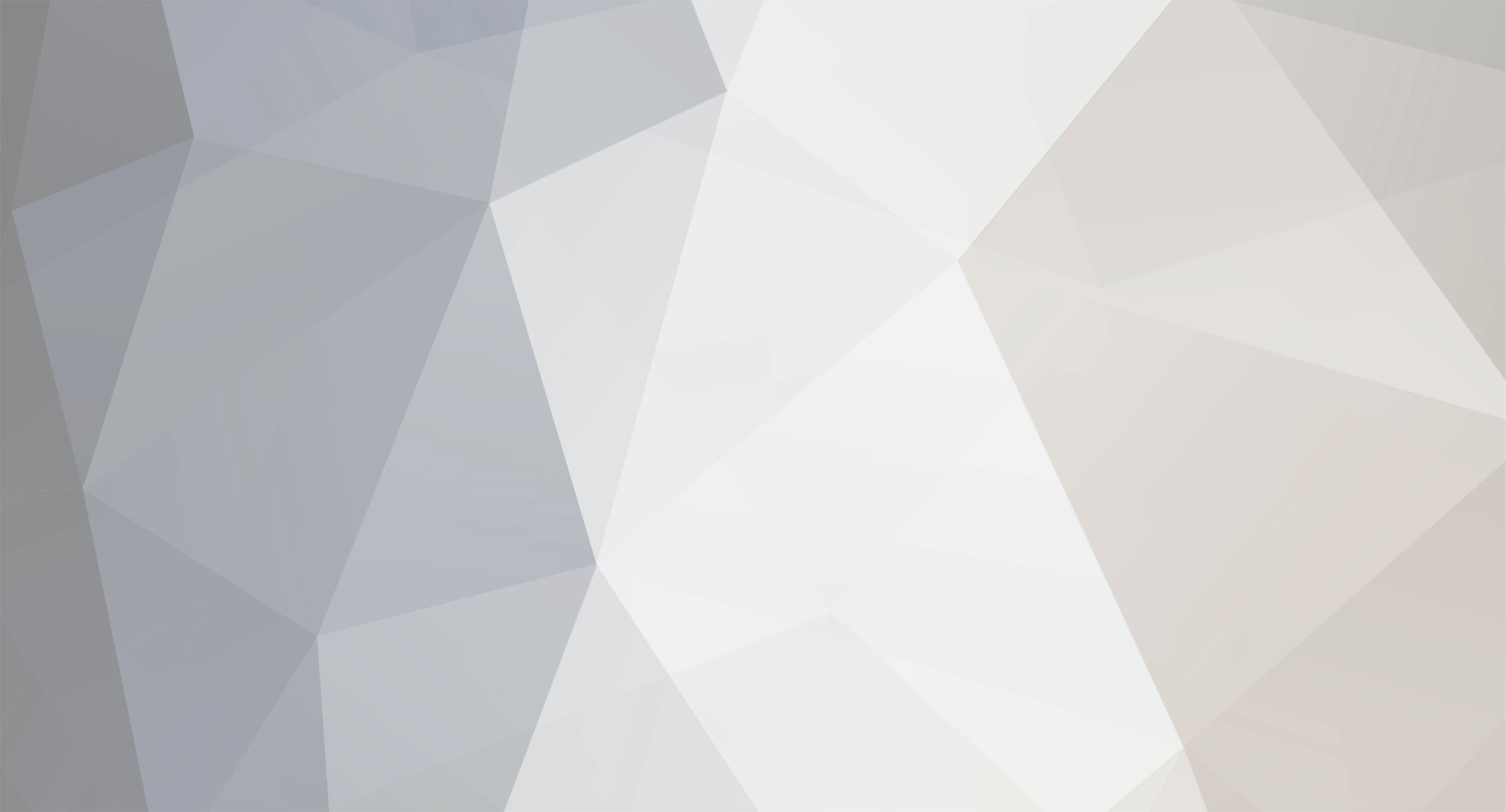
Tosh
Members-
Posts
162 -
Joined
-
Last visited
Tosh's Achievements

Regular Member (4/5)
37
Reputation
-
I have an old Air Arms TM100, used to be perfect for the job in hand. Unfortunately after a few years in storage (ahemm self build yawn) it won't hold pressure. I couldn't find anywhere to either get spares or repair and was about to throw in the towel but then found a place in stoke by pure chance that said they could repair it with seals made by a local company. Almost willing for them rats to come back!
-
Our formed cills were all folded but they did have to solder a few joints around our plinth flashing. They just took the coating off back to the steel, to the width of the solder and then painted afterwards with colour match spray.
-
Our new neighbours decided to put ducks in their garden. Within 3 months here the rats came. Chewed through the timber floors of our sheds and destroyed our belongings. Tried to politely reason with our neighbours and put poison down for 2 years but still they came. They just find different ways to break in. Explained that it was the food that was attracting them. In the end I just lost my patience and had a row with them. Coupled with the rat man telling them the same they eventually removed the ducks and food source. Although the council in our area did'nt offer pest control they did say they would do a visit and talk to the neighbour and ultimately we could file a nuisance complaint though it never came to that in the end. The chicken food IS the reason you have rats. Stop the food and they'll stop using your gaff as a hotel.
-
I have it as well https://www.ssab.com/en-gb/brands-and-products/greencoat/products/plx/pural-bt Can't see any technical reason why you couldn't use it to make cills, we used it for that but only because it was an integral part of the metal facade cladding. However we used aluminium cills everywhere else, supplied by the window supplier, was just easier to procure and cheaper. Metalsolutions are the Greencoat UK distribtor and looks like they will fabricate to order as well if you want to go down that route.
-
How to regain traction...
Tosh replied to Mulberry View's topic in General Self Build & DIY Discussion
Is there really an issue with the gutter? Ours is 150mm half round x 20m long, single outlet. Never had any problems. We also have issues with leaves but that's a maintenance task in my view. The size of the gutter is determined by the volume of water it has to carry not the material so not sure why VMZinc are throwing their two penneth into the mix. You also mentioned that you created a dam when you swept it into a pile. I think any gutter would suffer an overflow in that situation. In reality if you'd not touched it then the water would've likely worked itself in and around that debris and found it's way to the downpipe, carrying some of that debris with it. But ultimately you need to maintain it. Lots of ways - gutter vac, window cleaner pole with gutter head attached, etc. As mentioned before let the leaves come down the downpipe with a leaf guard on your gulley. Lindab do a nice version where it throws the leaves away from the gully but allows the water to run through. How do you plan to keep the rooflights clean and keep the upstand free of leaves? I can't tell from your window detail if there's a frame around the glass with drainage holes. If so and you have leaf problems won't they eventuially block up the drainage holes? If any of this is relevant then might be worth asking how the architect envisaged these things would get done. I believe they have a duty under CDM, and whilst might not be relalvant to these specific examples, it may open your mind to other aspects of their work that you've been unhappy with. I can't quite picture in my mind whats going on with the your upstand but I understand, can't recall for sure, BR determine height based upon roof pitch. If your upstand is too low why can't you just add another course of timber on your existing upstand, get a new roofing contractor to flash it in then drop your roof lights back on top? I must've missed something as I'm sure you would've thought of that? Note about your rooflights - if the installers plan to use sealant then do your own research into compatibility with Zinc. I know where the run off from a sealant used for a rooflight has stained a zinc roof and cannot be removed. Re the openings you need to get somebody to make that temporarily water tight. Cheap VCL sheet screwed down with battens onto your existing upstands - would that work for you? Any local small builder could do that for you. In terms of a SS roofing contractor I can pass on details of somebody. Send me a PM if you're interested. -
Had a surprising response from Premier Tech today when enquiring about a Solido STP. This is the letter they've sent to their sales team who in turn forwarded on to me. They never answered why they didn't make this clear on their website. **************************** Dear Valued Customer, We hope this letter finds you well. As you may be aware, Premier Tech Water & Environment has been evaluating our strategic direction in the UK market. After careful consideration, we regret to inform you that we have made the strategic decision to cease manufacturing and product sales in the UK, effective immediately. What this means for you is that, unfortunately, you should no longer specify Premier Tech products, as we will no longer be able to supply them. If you have placed an order in the last few days, please contact us through the usual channels to confirm whether we can fulfil it. Despite this change, Premier Tech Water & Environment remains committed to our UK presence. We will now focus on, servicing, maintenance, installing and commissioning off-mains wastewater treatment plants, supporting both commercial and domestic markets. We can also offer full turn-key projects if your customers require it. Please note that our company name, registered address, and contact phone numbers will remain unchanged Didn't see anything untoward on their website **************************
-
We used a telehandler for our sliders. We left it all strapped up as delivered on the pallet then got it as close as possile with the forks then unstrapped it and 'walked it straight off the pallet and direct onto the threshold with suction cups. Think it was in the region of 250kg, me on the telehandler plus 2 others. All other windows me + wife, except a few of the heaviest which were just over 100kg so roped in my son to help with those. If lifting from above maybe have a temp platform (spare pallets/blocks/etc) outside the opening to drop it onto and then walk it in?
-
Just an idea but is it worth exploring if a group action would be feasible, strength in numbers etc ....
-
I screwed backer board to the battens. This maintained an air gap at the bottom to ventilate the cladding above. Then fixed a steel mesh to stop 'things' getting up behind the cladding. I screwed temporary battens to support the slate and provide a consistent line (you can just see this on the left of the downpipe) then removed them later. My slate panels had clips prefabricatred into them for a mechanical support, not technically necessary in my case but I still found them useful. Ignore the downpipe connection, that was a temp setup whilst we waited for the correct pieces from lindab to arrive.
-
Is installing data cable conduits impossible?
Tosh replied to YorkieSelfBuild's topic in Networks, AV, Security & Automation
If you're going to run single cables from point to point then Kopex is the easiest and you could easily do that yourself. If you're not sure how many cables you need put a couple of extra in unterminated. They coule also double up as draw strings as well. You can also get split Kopex which can get you out of trouble sometimes. Another possible option is to run a backbone of trunking, something like 50 x 50 trunking in the ceiling, and break out to conduit drops maybe but a bit more thought required for this and without seeing your layout/obstacles its hard to say. -
We just put the skirting foam around the internal walls, external is ICF so not required. For the cost and ease it does help stop any screed escaping if you have a rip in the membrane upstand for example. If you want/need to put something in the doorways theres a couple of options. Just screw some ply/mdf/whatever it to one side of the door lining/studs and put the skirt foam over it so its easier to remove the ply afterwards then fill with expanding foam or just trim it down after the screed has poured. Even if there were a few cracks then just accommodate it in the build up under the finish e.g. ditra/flexible adhesive We had 140sqm 65mm gypsum, no joints - no cracks
-
Seamed Roof - what to have Zinc/Aluminum/Greencoat
Tosh replied to Caroline's topic in Roofing, Tiling & Slating
Very kind words @Big Jimbo, like many on here been a labour of love. Living off site, only working on it at weekends, kids, dogs blah blah. -
Seamed Roof - what to have Zinc/Aluminum/Greencoat
Tosh replied to Caroline's topic in Roofing, Tiling & Slating
We used Greencoat, that was based on the cost of Zinc at the time and the installer saying we'd never know the difference once it was installed. He said one of the main issues with zinc is due to its softness hence you tend to get more oil canning with it especially over large uniform areas. So he tended to use it more on complicated jobs with lots of detailing e.g. bandstand roofs. Bear in mind that some of the replies are based on Greecoat pre formed and diy/contractor installed whilst others, like me, are based upon specialist subbies with the coils arriving and formed on site with specialist kit. The difference in £/m2 will account for this so make sure you understand what you're asking for and getting. I don't think you'll have a choice with zinc, as far as I'm aware it will have to be formed on site unless a supplier has started pre forming it but not aware of any. -
What was the condition for the fence i.e. did they just want to know the details e.g. scale drawing with materials etc? They must of had a reason for this. Were your approved planning drawings lacking in detail and they want to mitigate concerns from neighbour? If you just want to sleep easy then just put in your application to discharge the remaining conditions. Just put in your application the details of what you've installed but without indicating you've actually installed them. If it makes you feel any better I'd purchased our windows/doors, cladding all before discharging the condition of prior approval. Risky - yes but then I didn't deviate away from what was on the outline planning drawings i.e. colour, design, shape etc. The only value add from the planning drawings were the window/door/cladding section details. They never contacted me or asked for physical material samples. From the LPA's perspective another £75 = cheers easy.
-
Stable block conversion - planning requirements query
Tosh replied to Mike Wynn's topic in Barn Conversions
Every LPA is different but our experience was the planner wanted to keep as much as possible of the old building whereas we wanted to remove as much as possible. Our LPA were dead against converting our building in the first place so our approach was to get full planning permission established albeit with a god awful design that retained just about everything we hated about the shed we were converting just to appease the planner. Once full planning was established we then went through a couple of S73's to refine the design to something more akin to what we wanted. Although S73 is effectively another full planning application its basis is on the principle that the dwelling already has planning approved for a conversion, it removed some of the conditions e.g. retain/repair the fibre cement roof and metal sheet cladding etc. We managed to get it back to just retaining the steel frame and the existing concrete slab to retain its conversion status. The slab is hidden and the steel is embedded into the walls so you can't see any of it at all, bonkers and a waste of everyone's time and my money. Your approach will no doubt be dictated by the officer and your LPA. There were a few benefits to conversion in terms of BR but we aimed to set the bar higher than that e.g. we used new build U values as a minimum.