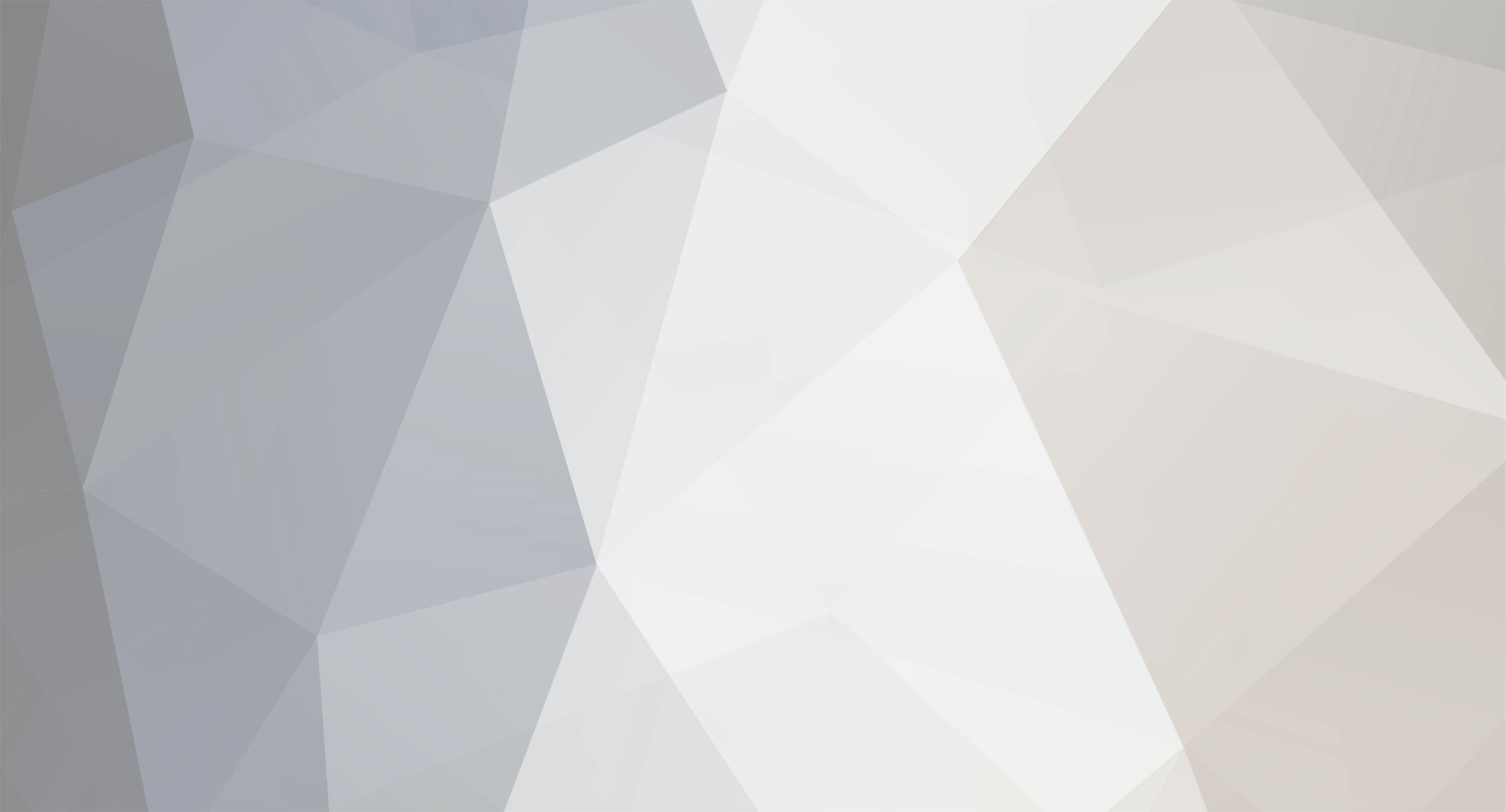
Glenn
Members-
Posts
48 -
Joined
-
Last visited
Personal Information
-
About Me
Small agricultural building conversion. Finally underway Jan '22 - 'In by Christmas...'
-
Location
Kent
Recent Profile Visitors
The recent visitors block is disabled and is not being shown to other users.
Glenn's Achievements

Member (3/5)
8
Reputation
-
Planning Approved - Feedback on proposed layout
Glenn replied to Owain1602's topic in New House & Self Build Design
Thank you for sharing with us. Quite a difference, some very interesting updates. I like the 'peeking' over into the lounge void, likewise looking down on the hallway. Also the bringing together of much of the water services. Couple of thoughts/triggers: 1. As others have said, corridor and hallway widths give luxury. pretty well any circulation path. So the wider the better 2. On the upstairs hall - if the MVHR could fnd a new home, that would allow a window at the end of the hall - very common architectural trick to draw you into the space, as oppose dto walking into a dead end 3. Entranceway and hallways - so many doors off them! No idea what that would be like in real life, but if some variety could be found, might be more interesting 4. The gym is marked as a potential guest space, but the nearest WC is on teh other side of the house, the nearest shower/bath a floor away? Maybe not an ensuite, but if the study is a bonus room (still getting over how vast some rooms like the playroom etc are), could it be repuposed as downstairs bathroom? That would eliminate the WC by the entrance,, group all your water and waste services all together. Short runs, etc 5. Kitchen/pantry integration. Maybe delete the door into the pantry from te mini-hallway, enter the pantry for the kitchen? SLiding or pivot door to hide it all away. Shortens journeys like kitchen <--> Pantry, Kitchen <--> outside 6. I'm terrible at reading plans, but wasn't your kitchen originally on the main entrance side, so that the lounge are was where the wraparound deck was? But now these are flipped? Does that put the kitchen on the west rather than east? Sorry for my confusion 7. As others have pointed out, some big spaces but a couple of strange proportions - eg upstairs bathroom 8. Depending on how adventurous you're feeling, that void combined with the huge amount of room you have to play with gives an opporunity to play with different floor levels to delineate areas, break the space up a bit 9. Woodburner gone? I think though this is a huge step forward in your design and I hope you're feeling much better about it Regards Glenn -
Planning Approved - Feedback on proposed layout
Glenn replied to Owain1602's topic in New House & Self Build Design
Hello, I am loath to believe that a registered architect would produce such a layout that ignored circulation, sun tracking, and practicalities like waste management. My own experience (small barn conversion) was the opposite - I was presented with multiple concepts based on the brief I provided the architects (brief was about feelings, not features) and each one blew me away. It was the process of rationalising your one that added value. In a similar vein, ETC kindly shared a sketch idea. Yes completely different, but great input into the mix, and some really interesting ideas.But no worries, trying some specifics for you to consider. circulation as others have pointed out, shopping from front door to pantry. easy to resolve by splitting the kitchen wall bench for a gap into pantry. choke point at foot of stairs with the boot room. Accessing snug past some hall doors in the way. Loads more. water and waste management: bathrooms in all 4 quadrants. The guest en-suite and family bathroom could easily be back to back. The downstairs WC could be on other side of hall to share with utility and plant room, or upstairs master en-suite moved fenestration: a biggie. One window between 3 upstairs bathrooms. Tiny bedroom windows. Lounge window covered by sofa. I’ve admittedly no idea why any of the windows are placed where they are. Do they frame views? Joy and drama and feelings and fun: all that space, but how does it feel? What do you want to feel when sitting in the lounge? What is going to be the drama of the double height - eg floor to vaulted ceiling bookcase with a wide corridor above for a library space (the bedrooms can give up some space). Definitely a wider corridor, for that luxurious feel. If you moved the guest en-suite you could then have a hatch in the bedroom where they could look down (and order coffee etc…) again, i am sorry for being so harsh. But you are going to put so much of yourself into this build. It’s more than just a roof over your family’s head -
Planning Approved - Feedback on proposed layout
Glenn replied to Owain1602's topic in New House & Self Build Design
Sorry for late feedback. First of all, many congrats on securing what looks like an exciting project! You will have great fun building it. but I think everyone is being too polite, so I will be less so. Please please please get some architectural input. I see no joy in this design, only a high risk of a huge amount of effort and time put into something that will end up being an echoey soulless box. You have a huge amount of space to use, have fun with it! You will be amazed at what a good architect can do to produce something ‘wow’. Let alone resolve the plumbing challenges of wages and water in all four quadrants and all the circulation challenges like I say, being brutal for effect. You’re quite within your rights to say “p..s off” in return -
Mandatory upstairs heating a really interesting one. For my (admittedly very small) house but well insulated and airtight house I had estimate/quotes from 3 suppliers. One did mention they wouldn't proceed without installing heat upstairs, the one I went with (and who processed the grant) was happy to go with heat calcs based on ground floor UFH only.
-
When is a self build house considered completely built?
Glenn replied to iMCaan's topic in General Construction Issues
Is this a self-build house or an extension? Assuming the former, you can get the grant before you complete the build. Grant rules specifically include self-build houses Regards Glenn -
Is it possible to expose ceiling beams while meeting fire regulations?
Glenn replied to MattD's topic in Floor Structures
I've been able to expose the beams on my small house no problem at all - size did go up a bit (per comments above) so that protection is about char rates, but not excessively - certainly not a doubling. I wanted exposed beams for a feeling of height and for character (even though they are painted) - both would have been lost if I boxed them in. In terms of sound transmission it's a bit of a moot point - there's a dirty great double height void in the lunge/dining area with open mezzanine and a stairwell. It's been about reducing impact noise not airborne Regards Glenn -
Living in static caravan during build
Glenn replied to Swiss86's topic in General Self Build & DIY Discussion
Reinforcing what others have already said - when I think about it the keys to me surviving/thriving on site in temporary accommodation, with sanity mostly intact: a) Separate storage space. Whether it be a shed or garage or another static b) Warmth and dryness. Wood burning stove in my case c) Tolerance. Not just of cramped conditions and a compost loo. That comes down to a shared dream or goal that all are involved in - not just tolerating your own dream to build Regards Glenn -
Do all windows have to be 1100mm from the floor to opening now?
Glenn replied to Papillon's topic in Surveyors & Architects
Hitting the news https://www.thetimes.co.uk/article/ditch-barmy-windows-rule-that-makes-new-homes-darker-ministers-urged-w8mld79j5 -
Thanks you, truly appreciated. I in turn will endeavour to be less prickly (and more precise in my language)
-
Casual language equals bragging? Wow. Maybe I will stick to enjoying this forum (which I have learnt so much from) as a silent participant. Offering opinions and common experience seems a little fraught. (BTW, no mention of 4m pours)
-
Sorry not to have sought your opinion before using my own experience (and the input of others, including the SE) to make what was at the time a rational, not risky decision. All I was flagging up was the 1m pour at a time seems to me to be the default for everything, whether it be an 18thC barn sitting on brick dwarf walls or a 20thC redundant agricultural building. SEs naturally need to cover themselves, it's their reputation and livelihood on the line.
-
As someone pointed out higher in the thread, I like many others started out as Class Q and moved to full planning for more flexibility. OTOH, my build has some similarities in that it was a timber frame on top of a very thick slab with no foundation (1977 fruit cold store, thick slab for forklifts and apple crates). Some learnings for me: 1. SE mandated underpinning based on soil (clay) and trees close by. Your local condition may vary 2. The SE specified the usual 'Pour 1m of underpinning at a time, joining rods between sections poured'. I thought blow that, it's a thick slab with a light and stable timber structure sitting on it. Luckily ground workers agreed after pouring an exploratory corner and it was completed in about 4 pours 3. The groundwork crew had a 'double bucket' on the digger which minimised the amount of manual digging out (and hence cost) under the slab perimeter Regards Glenn
-
Hello and welcome! Couple of immediate thoughts/queries - Whereabouts in Kent? I'm south of Maidstone and would happily recommend a builder and other trades if local - Speaking from personal experience, converting my Class Q into full building permission gave me more flexibility with overall dimensions. My friend and neighbour took it once stage further and was able to knock his concrete frame down and replace with timber frame. Would your build more economical to start anew as opposed to accommodate existing structure? Regards Glenn
-
Thank you all, brilliant assistance as always! Will wave around the relevant sections of the document linked to by Nick Thomas For general info, 5kw ashp and 180l tank, 50l ufh buffer, all plumbing and commissioning etc, £8.8k ie £3.8k net Regards Glenn