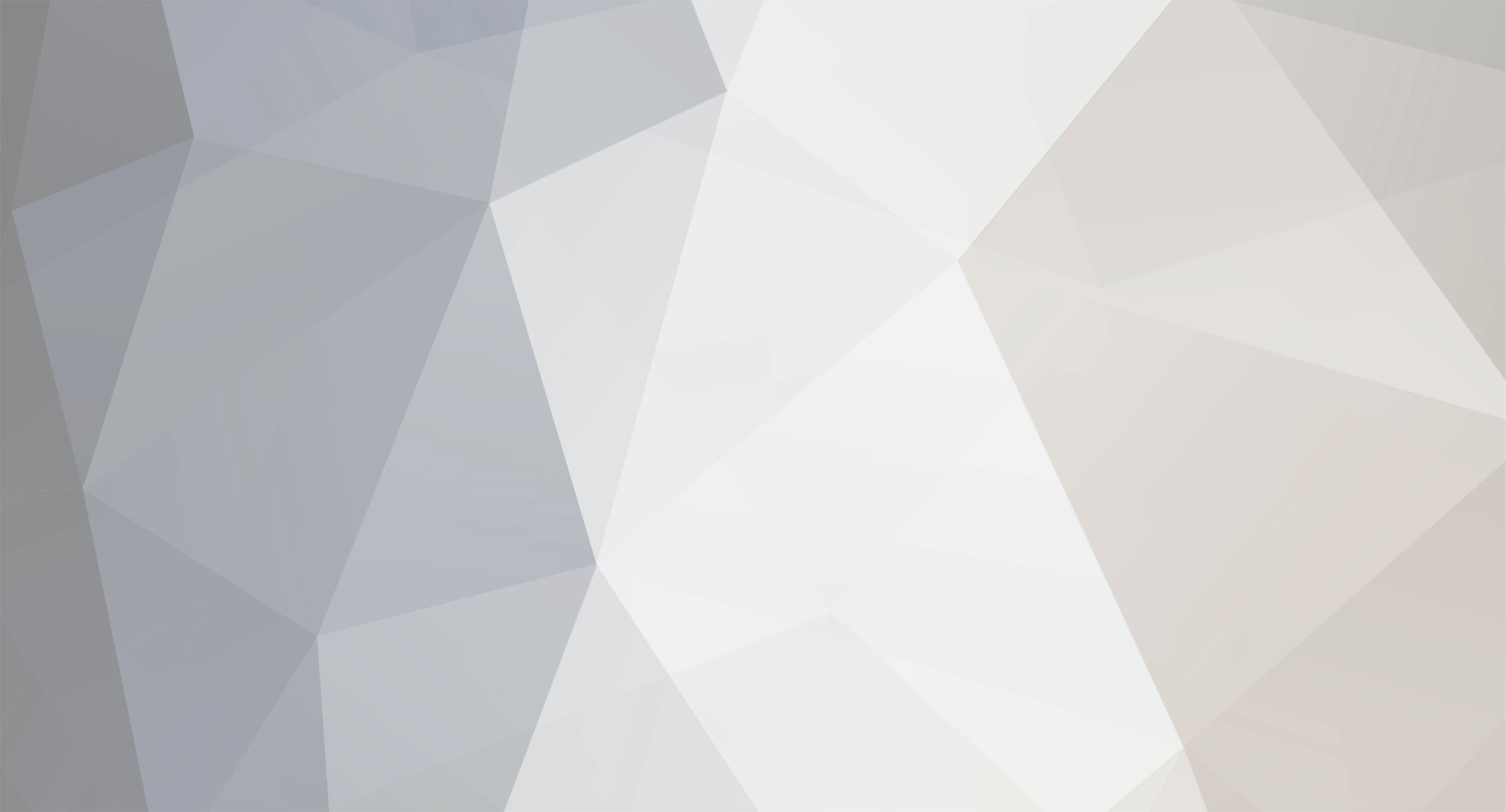
LionessHeart
Members-
Posts
11 -
Joined
-
Last visited
Personal Information
-
Location
Kent
Recent Profile Visitors
The recent visitors block is disabled and is not being shown to other users.
LionessHeart's Achievements

Member (3/5)
3
Reputation
-
ashp ASHP - how much ???!!???
LionessHeart replied to Robert Clark's topic in Air Source Heat Pumps (ASHP)
Hi @Robert Clark- can I ask how much you ended up spending for the supply, installation, and commissioning of your AHSP. Did you go with a ~12kW Mitsubishi ahsp? For a 4-bed house in Kent (approx 240 sqm with a double-height entrance hallway), I've received various quotes for between 12kW-16kW ASHPs. In fact, GreenHome Technologies has quoted £24K for a full package (supply, install, commissioning, excl VAT) - it seems a touch too high? -
MVHR is Largely Bogus
LionessHeart replied to DavidHughes's topic in Mechanical Ventilation with Heat Recovery (MVHR)
@Gone West - can you expand on this thought please? Would a plumber be able to specify and design such a ventilation system... ? Or, is it a specialist arrangement? Thanks. -
@pstunt - that's a beautiful and large home! We are also considering using Pagurek standing seam roof. Is your roof installed and are you happy with it? And did the installation of rooflights cause any issues?
-
MVHR is Largely Bogus
LionessHeart replied to DavidHughes's topic in Mechanical Ventilation with Heat Recovery (MVHR)
@PeterW Hoping the ASHP will serve UHF and hot water (there's no Gas on site, just electricity). Architect has been asked to take a fabric-first, low-energy, high-insulation approach. Hoping to have the uValues tomorrow.... will share when I have those numbers. -
MVHR is Largely Bogus
LionessHeart replied to DavidHughes's topic in Mechanical Ventilation with Heat Recovery (MVHR)
Hello David! We're embarking on a barn conversion project - it'll be our home in the country, so my husband and I will likely be there over weekends with the children and partners joining us possibly 3 times a year. We're seriously looking at NOT installing an MVHR - not only because of the cost, but to [a] minimise energy wastage (there'll be largely 2 occupants using the 4-bed house intermittently), and [b] keep things low-tech as much as possible. We will, however, have an ASHP, UFH, and solar PV. I've read your post with keen interest. - We'll install wall vents and good extractor fans in bathrooms and in the kitchen, as you suggest - But, are reluctant to bore holes into triple glazed windows for trickle vents My question is, how can we achieve the 1 ach if we're not using mechanically driven ventilation? Should we consider a Positive Input ventilation (PIV) and fans (for the hot days of the summer)? Thanks in advance for your input! -
MVHR Decisions...what to do?
LionessHeart replied to Thorfun's topic in Mechanical Ventilation with Heat Recovery (MVHR)
Thank you for that! So you got your MVHR (designed, supplied, installed and commissioned) by the Green Building Store? As it happens, I'm speaking to GBS about our ASHP, UFH and MVHR as well.... good to know you were happy with their service. Thanks again. -
MVHR Decisions...what to do?
LionessHeart replied to Thorfun's topic in Mechanical Ventilation with Heat Recovery (MVHR)
@Thorfun - can I ask who you eventually got to do the design of your MVHR? And, if you had someone install it for you (we'll be building in Kent, not too too far from you). Thank you! -
a BIG SHOUT OUT to all of you for your warm welcome and for asking me to be succinct! Note to @ToughButterCup: that was my scream @Thorfun: our brief re going low-energy (not Passivhaus) was obviously not clear upfront. Is there a u-value calculator for various construction materials available online? Have started reading Barry Sutcliffe's book. Mark Brinkley will be next. @JohnMo: Can a UVC run on electric (there's no gas). Stand corrected re MVHR. Meant to say ASHP-UFH... @Glenn: we're almost neighbours (or will be!) the barn's in Langton Green... Would really appreciate pointers to builders and tradies. @Tom: this build is under full planning, but on condition we keep the concrete posts, etc. @pocster: what can I say? You're ummm... gorgeous @joth: thanks for that suggestion. I've got in touch with a few Interior Climate specialists today. I'm thinking of the AHSP+UFH+UVC designed by the same person, if possible. Would you be able to suggest anyone? @gc100: thanks to you, I hope to save some money on our sewage treatment plant. @Temp: I'm aware of the tax savings and VAT431C, but hadn't come across VAT708... it's going into my black book. Thanks! @Jilly: ours is not Class Q, but I'm running against a personal deadline to move in by Aug 2024. That said, I've pushed the pause button for the rest of the week to do some reading, talking, and listening... so I can revise our plan. @SteamyTea: we'll be building up the floor for the UFH, but I don't know exactly how. Have made a note to ask our architect. We do have room for sewage treatment plant and PV (there's 1+ acre). We might go for more PV with planning, but in future. Thank you all again for your attention and care. I'll return with short, sharp questions soon! ciao
-
Hello Everyone! I've been following BH for almost a week now and am gobsmacked with the knowledge and helpfulness of all you kind people.... So here I am, hoping to learn (and in time, perhaps contribute) to this wonderful community. This is a long read (sorry!) We have planning permission to convert a shed into a 4-bed house in Kent. We've brought in mains water and electricity. There is no connection to gas or sewage. The barn sits on a cement foundation which we will retain. The main double-height shed is made from a pre-cast concrete structure (to keep). The 2 lean-to single storey structures on either side are built on steel beams (again, structure to keep) I am in charge of this project as I have the time and *some* experience with small renovations (extensions and loft conversions). My husband's work keeps him busy and out of trouble for the most part (it's my dream to build our home that got us here!!). We're very happy with the design drawn up by our architect. My challenge is to translate that design into a build we can afford. The QS (first pass, Stage 3 level) has come up with an astronomical build cost - more than double of what our brief to the architect was! Some serious value engineering along with compromises have to be made to keep costs down. We are prepared to part-build - focus on the main shed and west lean-to, leaving the east lean-to and landscape for a later time. Overall, we want to take a fabric first approach and make the home as low-energy and sustainable as possible (near Passivhaus standards). We would like to engage a local contractor in Kent (any suggestions would be most appreciated; we live in London, 1.5 hrs from the barn so don't know the local area well) Would it be cheaper to have the groundworks done by the local contractor, then bring in a Timber Framing company (Frame Build UK?) do the build before passing it back to the local contractor take charge of the rest? What hybrid model (if any!) would be best? What professionals are essential? Our architects suggests... - Building Services Engineer for heating/cooling/electrics.... We're keen to install ASHP (with UFH), MVHR, Solar PV (under PD, so just 9sqm), (Tesla?) battery storage. And they all need to talk to each other! Can a one-stop shop (e.g., Better Planet or Total Home Environment) who supply, install, and commission be a good substitute for a Building Services Engineer? - SAP consultant - we have one who can also provide Airtightness Testing if needed - Civil engineer to specify the sewage treatment plant... Again, can the folks at say, Graf be just as competent to specify the duct/pipe design? - Structural Engineer - already engaged - Building Regs Inspector - already engaged - QS - already engaged for first pass... We will likely need a Bill of Quantities before going out to tender. And wonder if using ProQuant would be more cost effective So far, Roof and Wall insulations have been specified.....Is there a way to gauge how close they will be to Passivhaus standards? Does there appear to be room to reduce costs here? Roof Insulation 1. Form new roof structure comprising; allow 150mm timber joists with 140 thick Rockwool Flexi insulation between joists; 12mm plywood decking; 100 thick Rockwood Hardrock insulation; breather membrane; form 50mm ventilation space from timber battens. 2 Fibre cement corrugated roof finish Wall Insulation 1 New external wall structure, comprising; 150 thick timber studwork structure with 120 thick mineral wool insulation; 12mm WBP ply; breather membrane; 50mm metal studs to form ventilation gap; vapour barrier and 25mm Rockwood RWA slab on 25mm timber studs to internal face; 2 Corrugated cladding; 3 Timber perforated screen on 50mm studs; 4 Insulated render Apologies for the long read and many questions! Any help, guidance, advice, will be deeply appreciated. Many thanks! L09P-Proposed Cross Sections.pdf L08P-Proposed Roof Plan.pdf L07P-Proposed First Floor Plan.pdf L06P-Proposed Ground Floor Plan.pdf L06P-Proposed Ground Floor Plan.pdf L07P-Proposed First Floor Plan.pdf L08P-Proposed Roof Plan.pdf L00-Cover.pdf