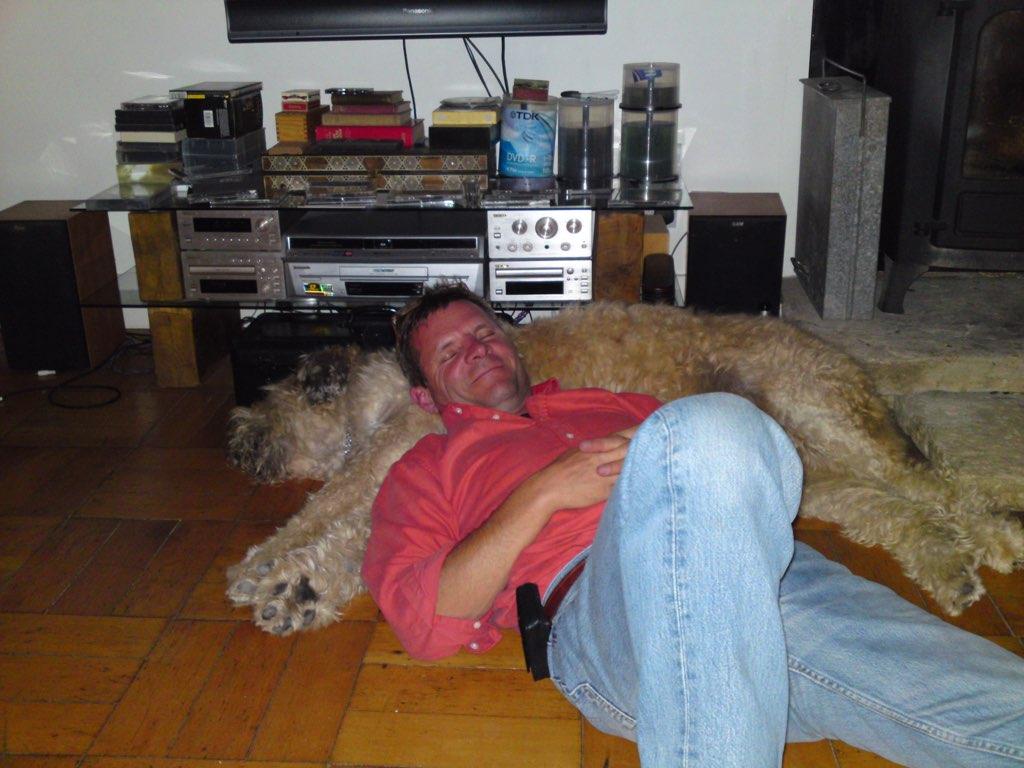
D Walter
Members-
Posts
116 -
Joined
-
Last visited
Personal Information
-
Location
Whippingham, Isle of Wight
Recent Profile Visitors
The recent visitors block is disabled and is not being shown to other users.
D Walter's Achievements

Regular Member (4/5)
41
Reputation
-
I agree with all the above. We have installed external roller blinds on the more W facing windows to cut out the solar gain from the low sun in the summer. In addition, the blinds act as mosquito screens so we can safely open the windows at night to allow for cooling. Unfortunately, I gave in to time/cost pressure and engineering complexity and did not insist on an opening window at the top of the atrium to vent warm air at night. That being said, the external blinds make the temperature manageable.
-
Hi, just wanted to check I have the Summer Bypass function right. The attached extract from the manual shows a "Maximum" and a "Minimum" extract air temperature setting. My reading of this is, if I want to maintain the highest level of cooling (minimum level of heat re-cycling) in order to keep the house as cool as possible in summer I would set the "Maximum" its lowest settings (20C ). Then, whenever the extract air temperature exceeds 20C the bypass will be activated provided the outside air temperature is lower than the extract air temperature. Have I got this right? As for the "Minimum" setting, I assume this is less significant as the indoor temperature will never drop below 19.5C in summer but setting it at 19.5C would give the best opportunity for cooling..... Thanks. David
-
Insect Screen Corroding
D Walter replied to Gone West's topic in Mechanical Ventilation with Heat Recovery (MVHR)
Slightly off topic, but is there any guidance on use of insect mesh on the air intake for an MVHR system. We are in a rural area and the air intake filter gets a significant covering of insects in the summer so I have fitted a mesh cover to the external air inlet. As this could could inhibit the air intake flow rate is there any guidance/recommendations other than keeping the insect mesh clear? -
New Year's Resolution?
D Walter commented on dnb's blog entry in Building in a woodland on the Isle of Wight
Congratulations, almost there and it looks great! We moved into our newbuild on the Island just over a year ago; the end of a decade of site clearance, planning and building. I am sure you are going to love it. -
Thanks Russell. About 10 years from starting clearing the site to finishing.
-
Well, you got the Trespa right so ?. I did look at the zinc but very costly and more dependent on the quality of the fitting than with the Tata.
-
Thanks Mr Punter. We spent lots of time looking at timber cladding all over the place and particularly in coastal enviornments like ours and so much had weatherd badly (uneven with lots of blackening) that we decided on the Trespa. Speaking to local builders the general impression was that timber cladding did not fare well in the Island. Yes, very pleased so far and hopefully it will wear well. The Tata steel cladding is also doing well so far but it is very early days.....
-
I have not submitted any pictures of our finished house so here are a few exteriors, with the landscaping almost finished. There is a bit of estate railing, steel edging to the drive and a bit more topsiol required. With the estate railing and the edging for the drive and flower beds we buy in the steel, my builders do the setting out and the heavy lifting and I do all the welding on site. Thanks again for all the assistance and encouragement. David
-
Hi, picking up on this old thread, is there a simple way to convert the airtightness results from a SAP test into the Passive House equivalent or will I need to do a volume calculation for the house first? Our SAP test has just been done and the I was told that the result is 1.71 which I assume is m3/(m2*h).
-
Yup, completed the survey. Hope it goes well.
-
Frameless Glass Balustrading on a steel structure
D Walter replied to D Walter's topic in General Construction Issues
Thanks Pocster. The risk of galvanic corrosion between alu and galvanised is relatively low in any event. -
Frameless Glass Balustrading on a steel structure
D Walter replied to D Walter's topic in General Construction Issues
Hi Pocster, Looking at your photo, have you used anodised alu channel for the frameless balustrade and was it bolted into galvanised steel? If so, what sort of bolts did you use and were you able to take any precautions against galvanic corrosion? -
We have just received certification of inspections carried out from our nominated CRL inspector, which is a hopeful sign...
-
Frameless Glass Balustrading on a steel structure
D Walter replied to D Walter's topic in General Construction Issues
Hi, Quick update - my Structural Engineer says that securing the bottom fixed alu channel with M10 Type 316 SS bolts into tapped threaded RHS 8mm mild steel box section is fine. On the issue of frameless glass balustrading moving out of alignment over time, this should hopefully not be a problem with most of the dry-fixed systems where the rubber gasket can be removed and spacers adjusted. Some systems requires a tool for removal of the spacers (usually also required for installation) and others have spacers which are adjustable by means of, e.g. allen bolts. If I experience any problems I will do a subsequent post. David