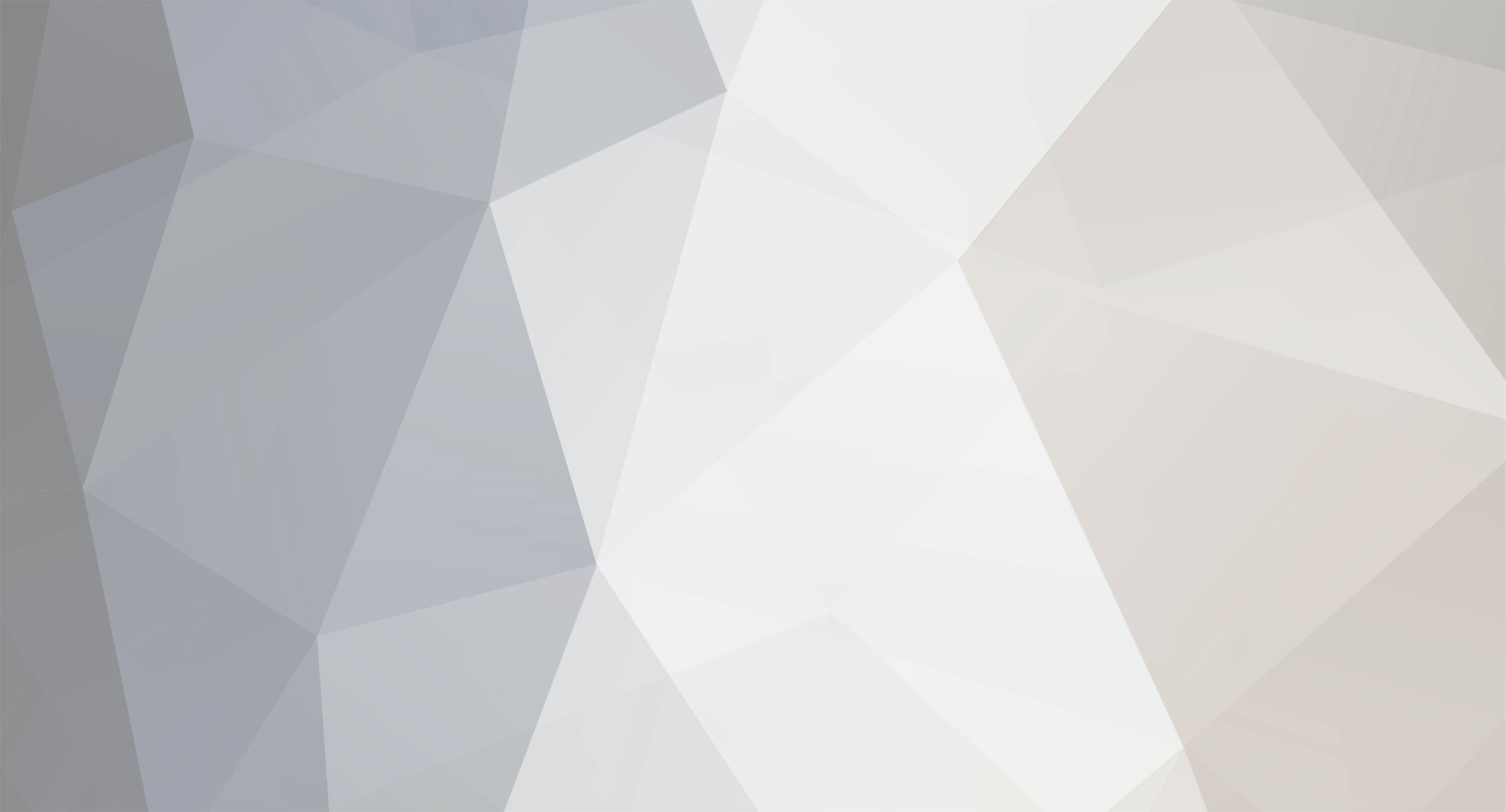
pudding
Members-
Posts
192 -
Joined
-
Last visited
-
Days Won
2
pudding last won the day on October 31 2017
pudding had the most liked content!
Personal Information
-
Location
Cornwall
Recent Profile Visitors
The recent visitors block is disabled and is not being shown to other users.
pudding's Achievements

Regular Member (4/5)
49
Reputation
-
https://amzn.eu/d/anJn0ET
-
Hmm weird. I've had my AC Mesh with the RJ45 plugged into the bottom for probably 2years now just outside on a 4x4 post about 2m high, completely exposed and no issues. Got any other plugs to try, cut the old one off and crimp a new one on? Just been outside to take these 2 pics of it, and remember the cable I used was outdoor rated CAT6, which had some gel stuff surrounding the 8 cores, maybe that makes a difference?
-
Whats in the plastic box, the Swiss army knife? Don't you just put the cable straight into it, and then mount it on a wall or post?
-
Absolutely no way you can you drill a hole through a wall somewhere and poke a CAT 6 out for POE and data and avoid the mesh? Makes it so much simpler. I've got an AC Mesh on my decking via POE and its worked great, nice long range coverage up to the garage.
-
Help with first solar PV system shopping list using Victron kit
pudding replied to Alexx's topic in Photovoltaics (PV)
Have a look on here. Expand the GB specs to see if theres a G100. https://connect-direct.energynetworks.org/device-databases/search-gen?manufacturer_id=66 -
Help with first solar PV system shopping list using Victron kit
pudding replied to Alexx's topic in Photovoltaics (PV)
Ah yes, no smart meter and no variable tariff changes things massively. Is that the case for you @Alexx or do you have a smart meter and can take advantage of variable tariffs? -
Help with first solar PV system shopping list using Victron kit
pudding replied to Alexx's topic in Photovoltaics (PV)
You certainly can expect to make decent money. I'm over £50 in profit this month already, that's with a GSHP& all electric house and an EV. Camelot forum might be better suited to your requests and plan, lots of similar setups and ideas there. -
Undercapacity A2A outdoor unit - possible? advisable?
pudding replied to puntloos's topic in Air Source Heat Pumps (ASHP)
Yeah, fire off an email to a technical dept address if you can find one to get clarification, then you can try and persuade any installer it'll be fine with hopefully a good email reply. If you can reassure any installer it'll all be fine and you're not likely to be harassing them to come back because the units are not all working full chat at the same time, then they'll hopefully be happy to go ahead with that unit. -
Undercapacity A2A outdoor unit - possible? advisable?
pudding replied to puntloos's topic in Air Source Heat Pumps (ASHP)
I think it'll be absolutely fine, even if Mitsi dont have the page like I had in the Daikin manual. With the 11.2kW outdoor unit you mentioned above with 6 connections, is it even possible to connect 6 units and stay under 11kW? Even with small 2kW indoor units, that's 12kW and over the 11.2kW max from the outdoor unit. All that will happen is the outdoor unit just wont be able to keep up with the demand on that 0.0001% chance all indoor units are running and demanding max cooling/heating at the same time. -
Undercapacity A2A outdoor unit - possible? advisable?
pudding replied to puntloos's topic in Air Source Heat Pumps (ASHP)
I installed a Daikin System a few years ago in my extension. I went for a 5kW outdoor unit, feeding 3 indoor units, 2x2.5kW and a 3.5kW, and its fine. Theres actually a page in the Daikin manuals that tells you what actual effective cooling/heating power you'd get if you were to run them all at the same time full power, which obviously is not the 2.5/3.5kW, but that just never happens and it's all good. Here's a screenshot - -
I installed an em3 last week. Fitted it inside the consumer unit, popped the power back on. Simply opened the Shelly app on my phone and it popped up straight away and said new device found & did i want to add it. Couldn't have been easier in my case.
-
Thanks. So it seems its an A3-2 form, and then as you say as its export limited to 5kW overall, there is an extra Export Limitation Scheme & Commissioning test form to do too. Has anybody ever done these forms themselves? I'm more than happy to do the physical swap of my inverters and setup as I did most of it on the current one as the sparky hadn't fitted a Sunsynk before so wasn't sure, (no extra cabling needed at all), but there's a few q's on these forms I'm not 100% sure of (of course I can just tick yes to each Q to satisfy it, as my 3.6kW inverter is installed and has been working fine for 2+years, so bumping up to the 5kW 'shouldnt' make a huge difference.) Hmmm, I'm just loathe to spend £100's for an install fee for nothing more than I'd do myself...
-
Well, the G99 approval was received this morning after I sent an updated A1-2 form with more details of the Export limitation scheme, and specified on there the 5kW export the guy at National Grid told me I can have. So nice quick response! He said to reply with the commissioning docs once its installed. Now, I've no idea whats docs these are. Any clues? Anybody have examples of refs for which docs are required after a G99 install?
-
Yes, the site plan/line drawing were the same, I just the changed the labelling of the inverter, and obviously sent them a different link to the inverter on the ENA register. I'm in Cornwall, so it was Western Power, but now National Grid.
-
I'm going through this myself at the moment. Currently have an old 3.6kW inverter, and added another 3.6kW hybrid with batteries a couple of years ago with G99 fast track and overall 3.6kW export limitation. Now looking to upgrade the 3.6kW hybrid to a 5kW and hopefully increase export limits, so have recently submitted the G99 form myself and plan on doing the straight swap of the inverters myself, so any docs used would be excellent.