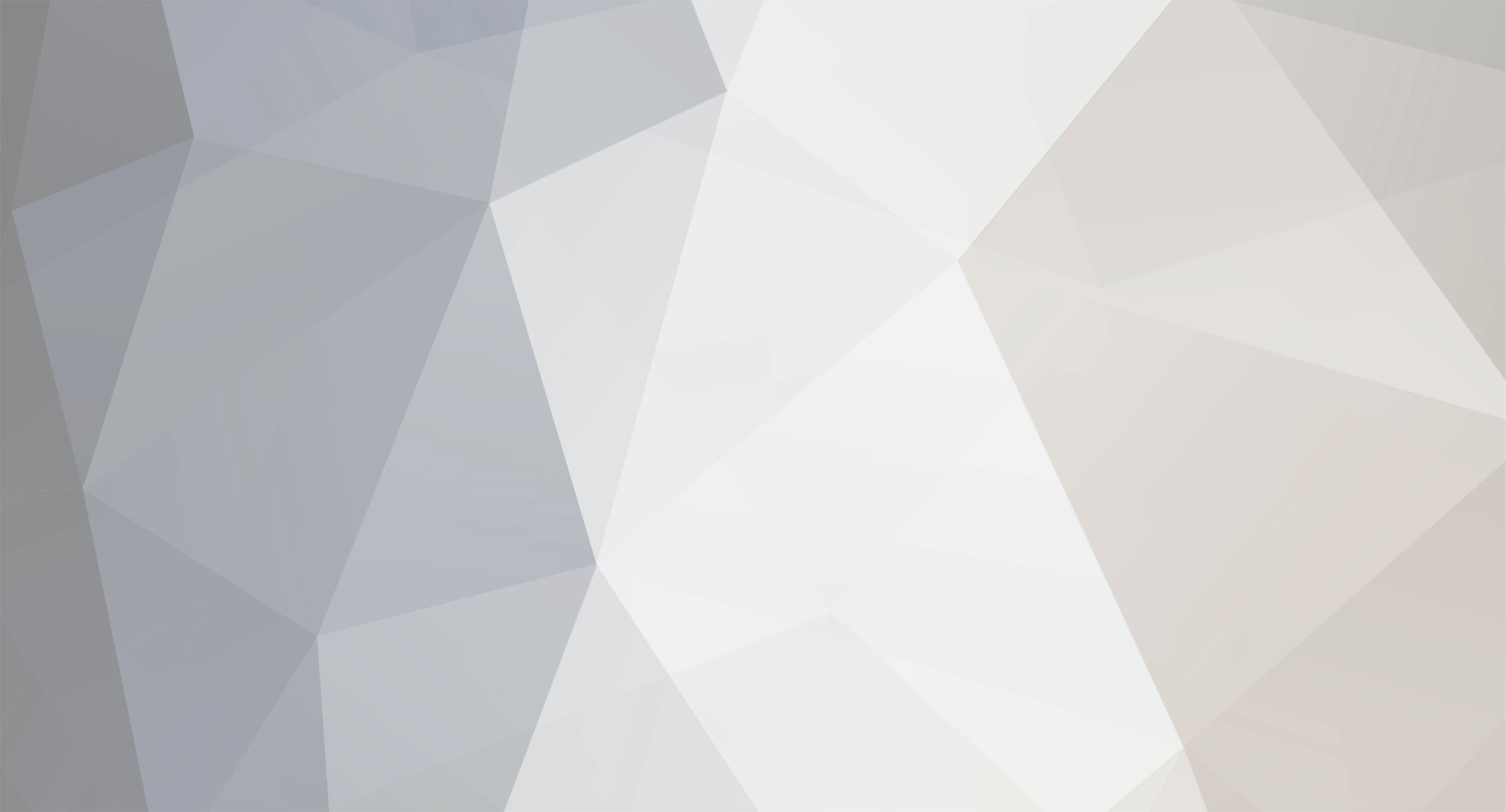
Dunc
Members-
Posts
137 -
Joined
-
Last visited
Everything posted by Dunc
-
thanks @JamesP so you took the DMP up behind the external insulation? No option on dropping the medite vent board - that's how it came from the factory. I might be able to put a fillet over the sole plate, but that's a lot of mucking about if it's not going to do anything beneficial. Option A: bring the breather membrane down to render level & ahere it (and the dpm?) to the render. Cladding over the top. Unsure what adhesive might work. If adhesive fails sole plate could become exposed to splash. Option B: take the DMP up behind the breather membrane. Breather membrane cut off at render level. If breather membrane fails or there is condensation behind it, this could run behind the dpm and affect the sole plate. But with the DMP lapped upwards, no risk of splash of the sole plate. In both cases unless I put a fillet of something over the sole plate, the membranes will have a bit (38x12mm) of free space to flap in.
-
Yes, photo is current condition: dpm under sole plate. Flap of breather membremane above. So if I cut the dpm fush, the breather membremane can flap over the sole plate. Maybe taped to the render?
-
So you'd just leave the sole plate exposed, other than the cladding?
-
Can anyone advise on how to tidy up the membranes at sole plate level on a timber frame? I will have a 10mm render applied to the block work under the sole plate. DPC & radon barrier flapping over this. Breather membrane covers the external board (Medite Vent board) of the timber frame. This external board overhangs the sole plate by it's own thickness (12.5mm). Architect suggested folding DPC up under the breather membrane then bringing the breather membrane behind the render to tie it down. Feels like a mechanism to allow water between the blockwork and render? Any risks with folding the DPC upwards? Frame will be timber clad with vertical counder battens then horizontal battens. Obviously the vertical battens will pin the breather membrane at the bottom of the external board, but not to the sole plate, unless I pack that out...wondering if that might be a good idea? any advice greatly appreciated
-
Posi joist - This install feels rubbish, thoughts?
Dunc replied to boxrick's topic in Roofing, Tiling & Slating
Wow! You seem to have dealt with a very very difficult situation calmly and extremely rapidly! Chapeau! Puts my stresses over having to get my window fitters back for a day's worth of snagging into a stark perspective - which is very helpful for me. So thank you, and best of luck! -
Box profile metal sheet maximum unsupported overhang?
Dunc replied to Dunc's topic in Roofing, Tiling & Slating
Anyone able to help with this? Thanks. -
I have a 45° pitch box profile metal roof which will intersect an EDPM-covered flat roof. The metal roof will be supported on 25x50mm counter battens and battens (to provide ventilation) on top of sarking boards. The EDPM laps up the sarking a good 500mm and my roofing membremane on the sarking laps onto this. To avoid screwing through the EDPM too low, how far up can I set the battens? i.e. how long can the unsupported end of the box profile sheet be? I can't find anything in manufacturer installation guides.
-
We're mid-build with MBC. They were the most expensive but the guaranteed airtightness was a big plus in my mind. However, the "integrated offering" of insulated raft, frame, and windows turned out not to be possible for us in the end. Early interaction with sales was very positive. The erection team were astounding to watch. Swift, without being rushed, and appear to be very competent. They should be having been at it for decades! It's not been completely smooth sailing. Communication with the design team had some slow patches (I suspect they were working at full capacity when we were in that phase). There were some areas of overlap between architect, SE and TF company which no-one seemed to really want to own. I had to push rather hard on a couple of things. There have been two structural/production errors that I identified post-erection. The measure of a good company is how they deal with these. So far solutions have been proposed with no wriggling or excuses, just a clear solution and timeline, which is as good as I could hope for. Overall, happy and would recommend. But for ANY company you go with, make sure either you are all over every little detail at every moment. It's astounding what "slips through the cracks" particularly during the design and engineering phase.
-
they are concrete bars which raise the reinforcing mesh to the required height within the poured slab. Yes, they just stay put in the slab.
-
That's the slab you can see there. There will be 220mm PIR on top then screed with UFH. Now that the timber frame company has left and it's just me and the Mrs, the build is progressing at glacial pace...slating is very very slow when you don't really know what you're doing 😆
-
No battens - this is nailed direct to sarking, as appears to be normal practice in Scotland.
-
Probably a daft question but...Can I cut slates short? (rather than narrow - I know I need ~150mm width minimum). Using 400x250mm spanish slate, pre-holed, nailed direct to sarking board. Unfortunately the first full course with a decent hang in to the gutter will line it's nail holes directly on the gap between two rows of sarking boards. Obviously there's an eaves course underneath this. Just wondering if it's reasonable to shorten the tails of the first course 25-30mm to move everything down and get the nail holes on to the boards. I can't set them higher as there won't be enough hang into the gutter. If I don't shorten them, then with the head lap and guage I'll end up on the edge of the sarking boards for several rows of slates before it all sorts itself out. I'd rather cut one row of slates than re-hole 7 rows.
-
Protek structural warranty quotation
Dunc replied to Amateur bob's topic in New House & Structural Warranties
? I didn't think I posted a link? -
Well, we're properly under way. Bare slab to all GF external walls, load bearing walls and steels in 12 hours! 3 joiners & 1 crane driver.
-
I am instructed by she who has more aesthetic nouse that me that we will have horizontal shiplap cladding round most of the house but the triangles of the gables will be vertical shiplap. Any tips on how to make the transition between horizontal and vertical cladding? I've seen a few builds round our way with some kind of break provided across the gable ends from eave to eave, even though they are vertically clad above and below this strip...no idea what material it might be or cross section though. I guess it might just be a PVC or aluminium L- or Z- shape profile? Might it have a proper name I could look up suppliers for? thanks.
-
Any ideas how to hide the Graf One2Clean control?
Dunc replied to DownSouth's topic in Waste & Sewerage
My pump and control unit is buried near the tank. Not sure what the groundworker used, possilby a valve box or a ducting access box with a suitable pedestrian rated cover. Gravel in the bottom for drainage. I checked with Graff in case this buried option doesn't work out (I'm worried about moisture/flooding!). You can locate the pump up to 18m away from the tank and the unit should have been supplied with 20m of hose. -
thanks for the reassurance! Yep, generally very happy with my groundworks team. Quick, efficient, adaptable and communicate well, and to the untrained eye seems good quality work. If anyone reading in future wants a recommendation for a groundworks team in the Highlands drop me a line!
-
I noticed that my groundworker has provided the soil pipe penetrations of the slab with a male end up-over (currently covered with a female blank). I had expected to have female ends up as I presume it's usual to have flow from a male end to a female to reduce risk of leakage...is what he's done normal? (am I worrying about nothing prior to setting all this "in stone" 😉)
-
Any tips on fixings/glue for installing compacfoam at door/window thresholds? The foam blocks are 100x150mm section and will sit directly ontop of concrete block work. They are 970mm long so I need to install several end-to-end to make up the 3m openings under some large windows.
-
Electricity Cable Connection
Dunc replied to HighlandHopeful's topic in General Self Build & DIY Discussion
Anything up-stream of your meter will belong to SSE, as far as I know, so they should specify. Others here may have better advice. -
Electricity Cable Connection
Dunc replied to HighlandHopeful's topic in General Self Build & DIY Discussion
Just lay some duct with draw rope in it if you need to go ahead before you have the specifiications for the pipes/cables. Water will have to be BLUE duct 110 external/90internal, minimum 750mm under ground. Marker tape in the trench ~200mm above this. Make sure you take lots of photos with tape measure to show depth as in my experience SW were fairly stringent in their track inspeciton. Electricity will need to be black duct. Make sure that there is appropriate separation between the ducts vertically and horizontally if they are in the same trench. -
Great to see! Must feel like a big milestone achieved? Hoping for our MBC frame up early May. I see they've moved away from the green-faced OSB internal airtightness finish.
-
Just to feed back on this in case someone else has this question: Marmox tech support (yes, I should have phoned them first!) confirmed that the sealant is only recommended where airtighess or DPM function is needed; there is no problem using the blocks without the sealant.
-
I don't see why not. Maybe need a bit of plastic down first to stop the screed running through any gaps? Are your joists engineered to take this load? Another alternative is laying the pipes between 25mm battens and surrounding with a dry mix.
-
Specifying a course of marmox thermoblock to break a thermal bridge in my foundation blockwork. Is there any value in using the sealant? Tech data from Marmox says "Marmox sealant should be used to seal the ends of the Thermoblocks together to prevent moisture creeping up between blocks and to ensure air tightness of the building." I don't need the air tighntess as that's dealt with at the timber frame/slab junction and the blocks are below this. It's outside the DPM so I don't need the blocks to be sealed to keep water out of the rest of the structure, just wondering if there's concern with water ending up bewen the blocks?