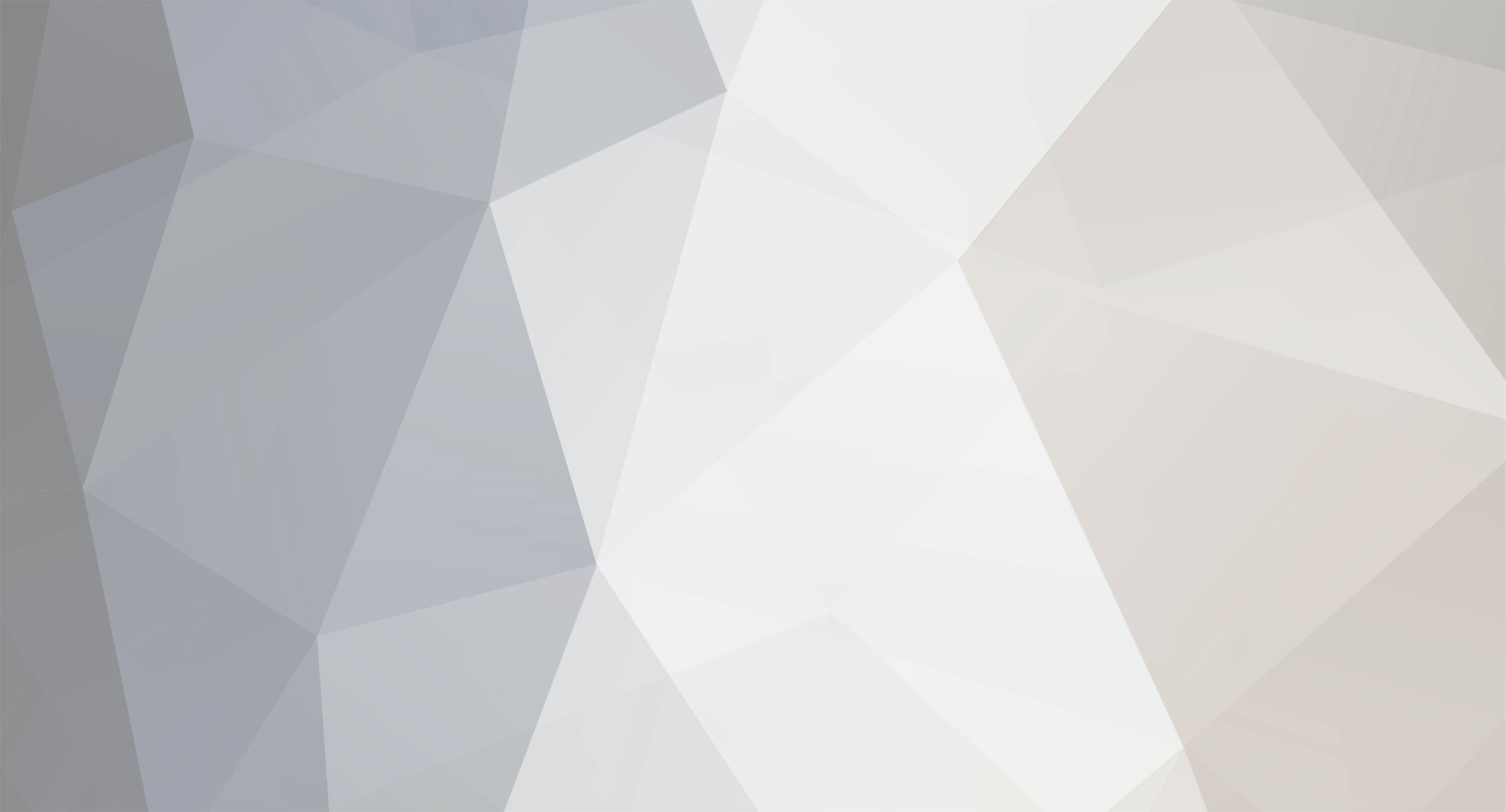
Dunc
Members-
Posts
140 -
Joined
-
Last visited
Personal Information
-
Location
Highlands
Recent Profile Visitors
3476 profile views
Dunc's Achievements

Regular Member (4/5)
37
Reputation
-
I hope someone can enlighten me on the need or otherwise for pumps in a wet UFH system with ASHP. Does each manifold require a pump? Is this in addition to or instead of the ASHP's own circultion pump? If in addition, how is this set up in the @JohnMo style using just flow/return temps to contorl the heat delivery with no thermostats to put a call on each manifold pump? If not, what parameters do I need to check to make sure the ASHP pump is up to the task. If specifics are useful: I have 1 manifold on each of GF and FF (lets keep any discussion of need for upstairs heating for another thread!). GF is 10 port supplying circuits of 40-100m lenght. FF is 6 port supplying circuits of 23-78m length. ASHP 6kW Mitsubishi. thanks.
-
Required in the void between the breather membrane of the timber frame and the external timber cladding where there must be a ventillation gap but also fire control. Vertically can be solid timber as no need for sideways ventillation however horizontally need to allow air flow but have fire stopping at first floor level, eaves and above/below windows/doors. Apologies to @kelvin for thread drift; back to the very impressive chicken housing 😉
-
@Kelvin can I ask what you did re: intumescent fire barriers behind your timber cladding? (sorry I can't find a previous thread you commented on) I'm guessing you put intumescent strip around at FF level and above and below windows. Anywhere else? Anything at foundation or eaves level?
-
thanks @JamesP so you took the DMP up behind the external insulation? No option on dropping the medite vent board - that's how it came from the factory. I might be able to put a fillet over the sole plate, but that's a lot of mucking about if it's not going to do anything beneficial. Option A: bring the breather membrane down to render level & ahere it (and the dpm?) to the render. Cladding over the top. Unsure what adhesive might work. If adhesive fails sole plate could become exposed to splash. Option B: take the DMP up behind the breather membrane. Breather membrane cut off at render level. If breather membrane fails or there is condensation behind it, this could run behind the dpm and affect the sole plate. But with the DMP lapped upwards, no risk of splash of the sole plate. In both cases unless I put a fillet of something over the sole plate, the membranes will have a bit (38x12mm) of free space to flap in.
-
Yes, photo is current condition: dpm under sole plate. Flap of breather membremane above. So if I cut the dpm fush, the breather membremane can flap over the sole plate. Maybe taped to the render?
-
So you'd just leave the sole plate exposed, other than the cladding?
-
Can anyone advise on how to tidy up the membranes at sole plate level on a timber frame? I will have a 10mm render applied to the block work under the sole plate. DPC & radon barrier flapping over this. Breather membrane covers the external board (Medite Vent board) of the timber frame. This external board overhangs the sole plate by it's own thickness (12.5mm). Architect suggested folding DPC up under the breather membrane then bringing the breather membrane behind the render to tie it down. Feels like a mechanism to allow water between the blockwork and render? Any risks with folding the DPC upwards? Frame will be timber clad with vertical counder battens then horizontal battens. Obviously the vertical battens will pin the breather membrane at the bottom of the external board, but not to the sole plate, unless I pack that out...wondering if that might be a good idea? any advice greatly appreciated
-
Posi joist - This install feels rubbish, thoughts?
Dunc replied to boxrick's topic in Roofing, Tiling & Slating
Wow! You seem to have dealt with a very very difficult situation calmly and extremely rapidly! Chapeau! Puts my stresses over having to get my window fitters back for a day's worth of snagging into a stark perspective - which is very helpful for me. So thank you, and best of luck! -
Box profile metal sheet maximum unsupported overhang?
Dunc replied to Dunc's topic in Roofing, Tiling & Slating
Anyone able to help with this? Thanks. -
I have a 45° pitch box profile metal roof which will intersect an EDPM-covered flat roof. The metal roof will be supported on 25x50mm counter battens and battens (to provide ventilation) on top of sarking boards. The EDPM laps up the sarking a good 500mm and my roofing membremane on the sarking laps onto this. To avoid screwing through the EDPM too low, how far up can I set the battens? i.e. how long can the unsupported end of the box profile sheet be? I can't find anything in manufacturer installation guides.
-
We're mid-build with MBC. They were the most expensive but the guaranteed airtightness was a big plus in my mind. However, the "integrated offering" of insulated raft, frame, and windows turned out not to be possible for us in the end. Early interaction with sales was very positive. The erection team were astounding to watch. Swift, without being rushed, and appear to be very competent. They should be having been at it for decades! It's not been completely smooth sailing. Communication with the design team had some slow patches (I suspect they were working at full capacity when we were in that phase). There were some areas of overlap between architect, SE and TF company which no-one seemed to really want to own. I had to push rather hard on a couple of things. There have been two structural/production errors that I identified post-erection. The measure of a good company is how they deal with these. So far solutions have been proposed with no wriggling or excuses, just a clear solution and timeline, which is as good as I could hope for. Overall, happy and would recommend. But for ANY company you go with, make sure either you are all over every little detail at every moment. It's astounding what "slips through the cracks" particularly during the design and engineering phase.
-
they are concrete bars which raise the reinforcing mesh to the required height within the poured slab. Yes, they just stay put in the slab.
-
That's the slab you can see there. There will be 220mm PIR on top then screed with UFH. Now that the timber frame company has left and it's just me and the Mrs, the build is progressing at glacial pace...slating is very very slow when you don't really know what you're doing 😆
-
No battens - this is nailed direct to sarking, as appears to be normal practice in Scotland.
-
Probably a daft question but...Can I cut slates short? (rather than narrow - I know I need ~150mm width minimum). Using 400x250mm spanish slate, pre-holed, nailed direct to sarking board. Unfortunately the first full course with a decent hang in to the gutter will line it's nail holes directly on the gap between two rows of sarking boards. Obviously there's an eaves course underneath this. Just wondering if it's reasonable to shorten the tails of the first course 25-30mm to move everything down and get the nail holes on to the boards. I can't set them higher as there won't be enough hang into the gutter. If I don't shorten them, then with the head lap and guage I'll end up on the edge of the sarking boards for several rows of slates before it all sorts itself out. I'd rather cut one row of slates than re-hole 7 rows.