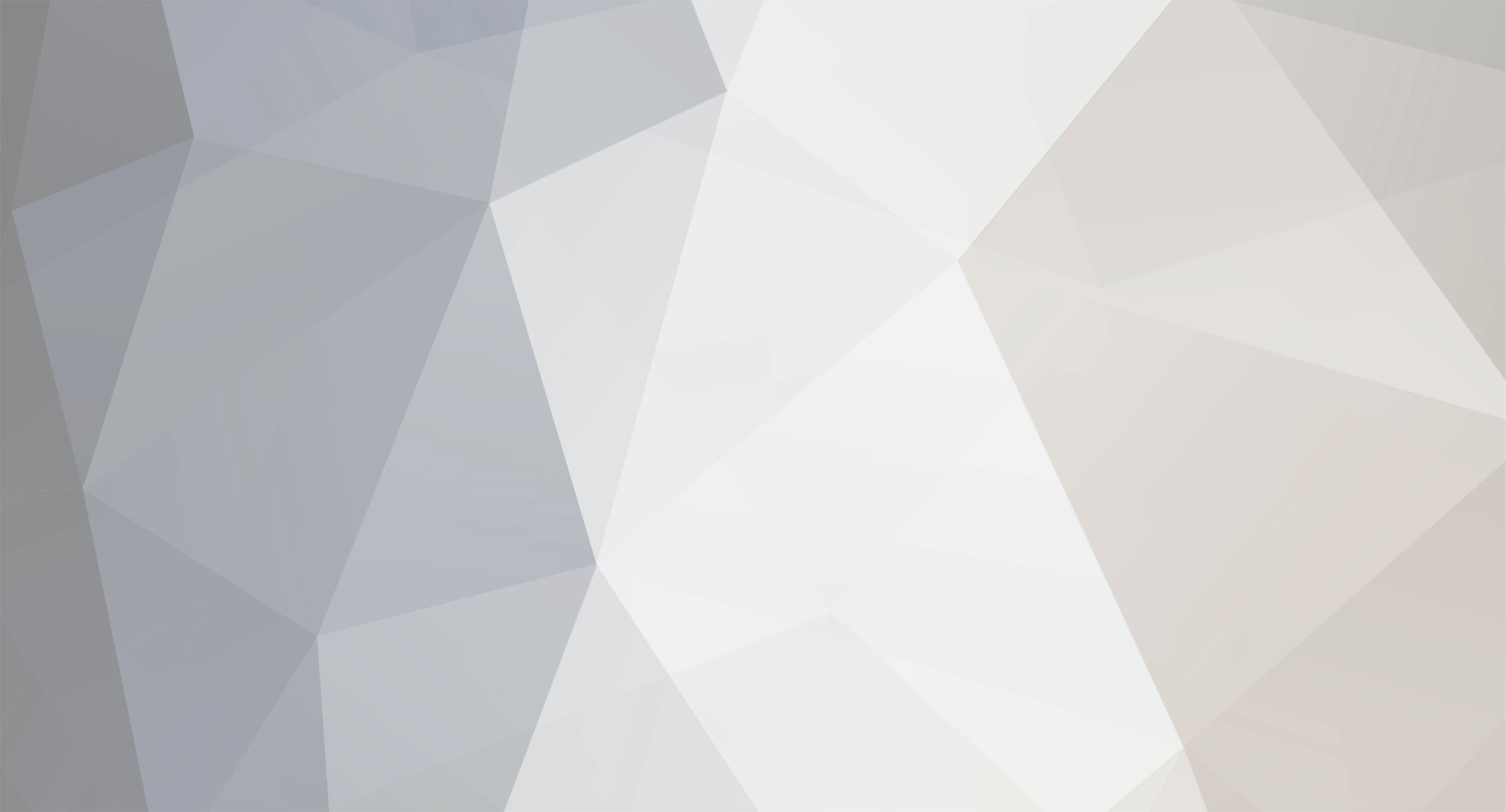
Fredd
Members-
Posts
29 -
Joined
-
Last visited
Everything posted by Fredd
-
i dont think you understated. only the very bottom of all the walls and studs are foamed to seal them. We dont use 435 cans foaming the entire walls haha! The tops of the boards are open to roof space in bungalow so need to be sealed. No drama. once plastered and skirted you would not be able to tell if it was or wasnt. it just passes the test. What you see on tv is when they have already skirted the walls so now they cant do a permanent job and foam, they have to tape - test - remove tape.
-
you cant do any work in the verge or road bud at least in our county, cant even drop your own kerb. Of course all the onsite is done to site boundary, goes without saying.....
-
So you liked my can eh. The issue with the eco tests, we know they well intended but in the scheme of things just not anywhere near the top of the list for the majoirty of buyers. Any regs add cost and its a balancing act giving value and nice house to the buyer at a cost they can afford which gets everyone paid. We are no differnet from any other builder, the walls get dabbed and boarded. They boarder is on a price just like everyone else. To add an eco tax to his wages just wouldnt fly. So the building gets foamed up and passes the test. In some ways its a good thing us volume builders dont use the small number of highly skilled trades as there just isnt anywhere near enough of them. There day rates cant be justified on normal homes, for 650+ homes of course. It's just how it is.
-
I see your 40k submersible air tight timber frame and riase you So its air test day. More £££ your first time buyer is going to have to work another 3 weeks overtime to pay. Make sure all the windows are mastic'd up including the under the cill which the fitters allways seem to forget as they cant get the nozzle in. Go round and foam the bottom of all plasterboarded walls, studs (both sides)the lot. Block up the chimmuck and air brick for the log burner if you have bothered fitting one for another £££ the hetas guy. tape up the loft hatch. 7 minutes later, you have a nice draft proof house and a pass no silly money spent and the first time buyer can still afford it.
-
morning you air tight eco builders! my point here is not to let your architect set your DPC height he wont be the one digging out the muck and paying for it to be hauled off. Let him set the ridge height (if needed) and you work it down from there. Too much ££££ at stake. You do not want to dig a big hole and put your house in it. This is my normal process now: 1. scrape off all the green crap 100-200mm. 2. laser to see what levels are like. 3. Hammer a spike into a corner, measure ridge height to adjoining and where DPC needs to be on the build, mark it on the spike. I use a leica D8 for this. cheap and brilliant little tool can even work out pitch. 4. Now if that mark is above ground, all well and good. if its the mark is minus more than 100mm then roof pitch it changed to accommodate. worst I've had is 550mm which we jiggered down to 220. Still a lot of wasted cash though. The 40k example wasnt just muck away cost (15k) we had to get an adopted sewer moved as the footings were so deep and too close. If we were 200mm higher then the sewer move would not have been needed. YOu drawn a diagonal line from your footing out into the build depending on depth and if it intersects sewer. ching ching. Oh yes the sewer company subs out the job, it gets costed by the subbie and you cough up. No other quotes obtained. Legalised scammery.
-
Set your DPC height to save you ££££ Plots are not equal. some are pigs, pigs have to be made into bacon. Generally, you want DPC to be as high as the planners will let you. Not all planners will be interested, mainly they will put condition on the planning where you have to tell them slab height. MEasure it up accurate and then add 2 bricks and send it in. We havent yet had them come back and question it (they have no clue how to measure it anyway) and it means you have 2.55 ceilings and a higher roof if need be. Dont tell them i told you. 1 or worse 2 bricks difference in DPC can be a 5 figure sum in groundworks and muck away depending on size of build. Tricks we have done in past, raise DPC by 3 bricks and dropp pitch of roof to keep ridge height with next door. £40000 saved.
-
yes your right. its the inside skin which is insulated by the cav, block, board, plaster and paint. ok it could be better but expensive. not worth the ££££££ to a first time buyer.
-
dont get me worng, i'd love to build houses with passive and fart tight. noone would be able to afford them. you lot here are a very lucky bunch, you getting amazing homes for life. most folks are not there, they are on the start of the journey.
-
jesting aside, the build we finished just before chistmas, the room stats reported 18 (underfloor heating). and i pulled the breaker chistmas eve. went in new years day and it was 14. them screen floors sitting on celotex hold the heat for bloody ages. but i'll not argue against being stripped naked !!
-
the beams and blocks are insualted from the rest of the build by the celotex, ill take a picture of the next one. there are no cold bridges. 100mm in cav. 400mm in loft. Floor is screed only after the shell and windows are in, pre-plaster.
-
well i thank you in a roundabouts way. Please tell me, why you went down the frame route and lets go from there.
-
whatever you paid the groundworkers to do that wasnt enough! work of art that. i'd sack the plumber who put the underfloor tails that high and spread out though. terrible.
-
ok well then i apologise as you is upset, and im the last chap youd meet who likes upsettting folk. i didnt read the whole lot, but if i upset you im sorry. it wasnt my intent and if we met in the local im not the not of chap who would upset you bud. yaki dah
-
you have hit the nail bang on the head here stoner. ive yet to do a build where there havent been compaints/hassle. it just goes with the territory. Crack on and be helpful where you can, delivery lorries are rarely there more than 20 mins. I only give notice where i will be preventing someone getting out when say concrete pump will be there for a couple hours. or a crane. if they kick off then (and ive had many) I just tell them to call the police. Not yet had the police turn up, have had council on phone though. explained the issue. notice given. no other way to do it. complainer being deliberately awkward and no wont move until its done which will be a matter of hours.
-
sorry i think you read it wrong, i meant pouring a slab and expecting it to be level is wrong. They just arnt that accurate. never are. there are no wrong choices in the building, some just cost more than others! block and beam is fully insulated against cold bridge mind. But again this heat your house with a hairdryer stuff is niche and not applicable to most folk as the economics of it just dont add up. im not that great at writing as you can guess, i definately wasnt saying they were wrong to choose whatever method they like!
-
this does surpise me as the shell is the easiest and cheapest part of the build. YOu only have one lot of blokes to manage - brickies. To give you an idea, the going rate is around 40p per brick laid, good brickie 180 a day. doesnt take long for a gang of 2 and a labourer to rattle up an average 4 bed. Again could you share you frame cost and labour and m2 to compare? Assume you bricked up the outside anyway so we are comparing a single course of blocks and some mineral wool.
-
this is where self builders cant see the wood for the trees. no offence. couple sheets of £4 plasterboard wasted make zero difference. Slabs is a hangover from the 60's! Block and beam, insulation, underfloor and a perfect level screed everytime. This is normal not an exception. You chose the wrong floor method and were lucky the slab pour was level, they usually are miles out. In fact it is cheaper for us to buy use tetris flooring system instead of blocks BUT its a pain in the arse to use as it cant be left until the shell is watertight until screeding. in other words it will get buggered up by stuff being dropped, dripped, machines etc. Yes of course there are ways to protect it but who needs the extra hassle for a few hundred quid saving. A self builder may though in fairness. You may have a point on some miner economies with larger sites, we find on sites of 5 there really arent many as utilities are a rip off whether its a single connection or 5. We have a bungalow build sewer charged £4k. We had a pair of 5 beds, charged £800. both were connections to road both around same length. No reasoning with them. If you dont mind, share your timber frame cost + labour and m2 fit it and I'll tell you how much cash you put up in smoke compared to trad build.
-
Why are most PV installed "portrait" rather than "landscape"
Fredd replied to DenkiJidousha's topic in Photovoltaics (PV)
this isnt the same supplier but they look the same, the trays are exactly the same ones velux windows use. Really easy to fit and flash. more importantly they dont look like an afterthought. https://www.energymyway.co.uk/products/roof-integrated-solar-panels/ -
Let me try to explain. For the 99% of buyers on a mortgage they need value. The supposed benefit to a builder of timber frame is speed and im yet to be convinced of that. The likes of Permissons, taylor wimpey love them or hate them etc crack them up very fast, much quicker than buggering about with wood frames. Now I appreciate self build is a niche market, and like kitchens everyone has a different opinion and requiremtn from the build. BUT if you are on a shoestring budget, do the math. Self builder wont complete a build in 4 months so even the dubious speed benefit is of no use. The eco side doesn't add up to me either. Back of fag packet: Extra cost of timber frame over brick and block for a 'normal' 250m2 house - £30000 Lets assume its twice as eco as a normal EPC cat c new build. What savings are we looking at ? Here is the EPC from the last build we did 180m2 Now lets say you can save half of that (which Is being very optimistic) £600 a year. You would be looking at 50 years to just break even! So in purely cost terms timber frame has no upside only downsides. Put that money saved into a larger build of better spec.
-
Why are most PV installed "portrait" rather than "landscape"
Fredd replied to DenkiJidousha's topic in Photovoltaics (PV)
the ones we fit do! and they look good as well as they follow the profile of the tile. -
Why are most PV installed "portrait" rather than "landscape"
Fredd replied to DenkiJidousha's topic in Photovoltaics (PV)
fixing. the rails that hold them run horizontal across roof joists. to do it other way you would need more rails and the load would not be spread over the roof. on new build they are inset into the roof and go into the same tray as a velux window uses between the joists. No room to do them the other way. -
Per m2 cost discrepancies, enthusiasts v. national figures.
Fredd replied to epsilonGreedy's topic in Costing & Estimating
A lot depends on ground. What are your footing costs, levelling, parking etc. Is the plot dead level ? Services easy ? All the above are out of your control and will cost what they cost (apart from the obvious digging part). They can have a big impact. We have had sites where 3 builds all the same 1 of them was 20k more as we had to dig silly deep on one of the plots. 170+vat for muck away gets expensive fast and you dont fit much on a 8 wheeler, less on a 8 wheeler grab. 1000m2 is about right for a normal box, average kitchen average windows/doors etc Get it quantity surveyed, then you can make better/cheaper choices on mats. Some mats will come with cheaper labour as they are faster. -
your right there! Too expensive cost point over a normal house. Everyone cant drive an aston right.
-
ah the real world. Builds have to work in brick, its silly otherwise. Plans are normally 1:100, i defy anyone to have eyesight better than 0.5mm reading accuracy or 50mm. Lets ignore the fact paper changes size when damp etc. If the plot has no building line to follow you arnt going to have a problem if you are in the general area, OS map accuracy is even worse. What we do is make sure the building line elevation is bang on, as this is the one planning enforcement will pick up on as its only one you can see by eye (same with ridge height). Then make it work in brick or block (if not using brick) in all other planes. Never had a need to go more than 100mm over as the architect would get the pi$$ ripped out of him for a crap design otherwise! Do same for openings, quarter cuts just look crap you want half bricks.
-
for what reason are you making life difficult and expensive for yourself by going down this route?
- 15 replies