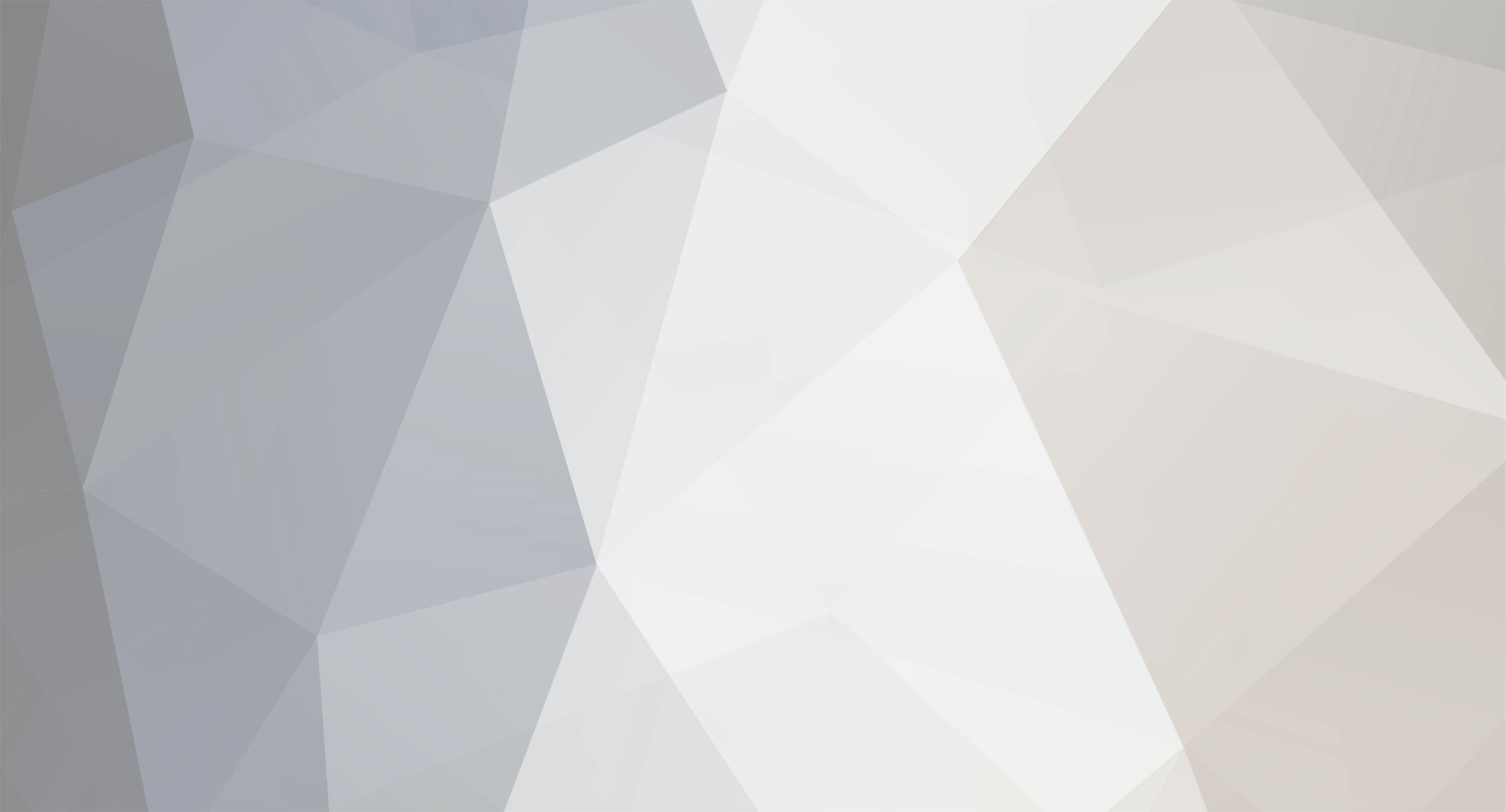
gcm
Members-
Posts
18 -
Joined
-
Last visited
Recent Profile Visitors
The recent visitors block is disabled and is not being shown to other users.
gcm's Achievements

Member (3/5)
3
Reputation
-
We looked (and debated with planning) these very windows V200 vs a Rationel FORMA+ Alu clad and some others. The profile is very different from most - the larger drainage/spider trap debated here and the metal being thrown a lot further forward from the window than with the Rationel. I think it may be the better design but can't really justify that with data. It's a lot more modern looking - clean lines - offices and apartments look - and their glazing bars solution (again for planning this was a thing for me) are quite different. Rationel is arguably a lot more traditional setting friendly. This odd profile came up. For our application (retrofit) when we took one old window out temporarily with the possible Velfac installer pre-purchase from Direct. We found that the greater depth to the timber was a problem in achieving the same front face / brick reveal depth (again for planning) and then siting the timber work and securing correctly on the established brick/block. So for us Rationel would likely fit and Velfac V200 would possibly not (at least for *some* of our apertures - unknown until old windows out and sat there with the expensive new V200 on the patio. Was glad I found out before I had a truck of bespoke sized windows. Horses for courses but a cautionary tale to check that specific dimension very carefully on the design or your building if retrofit like me Per the thread - we used the wider version of the ilbrook/tremco stuff and got on fine with it. Summer install from the fridge but mid 20s. Our gaps were mostly on the "wider" end most of our apertures are not in fact rectangles so poking it in wasn't too bad other than a few spots.
-
Indeed a 2008 installation - not planning its imminent retirement. Our Grant just had new expansion vessel this year so it's not dead yet. However we are planning full redecoration - window reveal apertures were redone to fit the new windows better and the ceilings need doing including very high stuff I don't fancy myself. So the pipe runs and rad changes for greening energy (and skirting where centres change, and spur for ASHP - belong upstream of paint along with electrical work for PHEV car charger etc. etc. Thus trying to work out if an ASHP is even a possible future goal - as that drives the need for rad changes if I have understood it. I can just leave well alone if not or make a couple of insitu "upgrades" where the design was locally weak in a particular corner of the house. I think i've got the basic idea now - electric inline heaters (Willis) for higher system temp or ASHP - not both at once. Diverter valves isolate. Same with the oil boiler hybrid. So I'll just work out if I can get to 2x size of rad panels via triples - size bumps and extra ones in not insane to plumb locations. If not - then the idea is dead anyway short of excavating the floors. But if I can I need to understand if this works as a set of preparatory changes while still on oil (doesn't break current solution adding the rads) and how to get a working control design appropriate for new TRV. Our old TRVs were unimpressive and yet the house is not an easy one for all matters wifi. We barely get a basic Siemens remote stat to work in a couple of spots and that has stronger specific RF than many a solution. So manual (but quality) may still be best. The Tank/bundage + soldered pipework is the "not refreshed as recently" stuff which will be needed sooner than the boiler - one summer - if there is to be a kerosene refresh in our future at all.
-
Looking ahead to next kerosene boiler replacement. Keeping track of what works and doesn't for retrofit to our site May have another Grant like the current 36kw condenser (perhaps with the hybrid and the RHI (if can qualify), replace tank, upgrade pipe work, bundage to current spec). I can't help but feel that these are like the car hybrids which are designed to the tax rather than to work as such. The 36 is bigger than it's rather terrible utility predecessor that I inherited and may even be a little over what is needed. I'll have the rads estimate shortly as I have been around measuring and thinking through how it could be increased x2 for t30 Question - on the Grant hybrid - how can it be long running burns and oil temp. And ASHP temp. And work together. On the same size rads ? If it only works in swing season for ASHP then it's a bit of a chocolate teapot with a potential subsidy attached reclaimed in pricing - may as well use our wood burner spring/autumn and buy the cheaper pure kerosene burner. Am I missing something clever ? Surely it won't do much on existing (half sized) rads and with the upgraded ones the room controls will become key with all that entails. In terms of alternatives - what is the maximum size for an ASHP solution in terms of annual kwh (or indeed peak days) for a single phase system with upgraded radiators to suit it (I am evaluating how close to 2x we can get on that - both per principal room to avoid colder areas getting worse and overall for the lower operating temperature. Don't have UFH and the retrofit is daunting to do properly the modern way , insulation, pad, excavation given wood and stone tile interior fit. So it's rads. Doubles become triples and/or bigger. And some new wall ones. I appreciate that at the moment oil is materially cheaper than the extra electricity for full ASHP but that may not always be so. I have eliminated skirting rads as the house is just all corners and I can't stomach so many o-rings/joints or indeed the cost per kw of dispersa being double rads. GSHP unattractive. sloping site without room for coils. So pit or not possible. ASHP or or oil hybrid can be sited easily in the existing input spot. Plant room for pellet and store but I find the energy density and lack of supply diversity offputting So is it ASHP + Willis for ultra cold days ? Or just kerosene and hope the regulatory changes aren't too unkind for the next cycle Air to Air units could be fitted instead/as well in a couple of places with dual outlets to major rooms but coverage would be incomplete. I worry these are an allergy monster as the filtration on the domestic units I have repaired (filters and remote batteries) for relatives was a bit risible. My wife will not be at all happy if the heating is marginal and then just gets worse in the coldest of weather. Any thoughts
-
Shop around. Yet depending upon where you are in the country - the choice of reseller installers who can travel to the site my not be that wide. Obviously it depends upon what you are doing - a slow 6 week renovation or a rapid install new build i.e. whether a local installer/incremental project matters. We were doing renovation with 27 different shape windows including some big multi-section ones - rip/install/make good was 6 weeks for us. Rip/fit 3/day and slower make good We did not find we could get much discount on the materials side for the Rationel job from a mobile SE outfit or from our two local regional resellers. They were very disinclined to race to the bottom against each other. So on materials it was significantly more £ than velfac etc. Regional reselller territory model. We had aperture technical issues which eliminated other some other cheaper profiles so ended up with Rationel. And in the end it was a good experience. And they look better in our traditional property. We used Rationel FORMA+ Alu 3G and the installer we picked did a good job on the renovation project - proved very adaptable to what was discovered. Did we overpay for the windows purely as materials - yes we did. But with the hours that went into supply+fit + particularly into make good they went a fair way over on their guess on estimated hours in the overall fixed install price - so I don't think it was a roaring success on margin for them either. So in the end - I was happy with my one and done contract. A quality site install team was a big priority for me. I am not sure it is the optimal brand for supply only but you may be luckier than I was with other resellers
-
Another Rationel Forma+ Alu clad + secondary cill detail Aftermarket cill sourcing and application does seem to vary. Not sure if this is optimal but it seemed to make sense for our application. We were dealing with "too flat" existing deep granite exterior cills in a refurb and we ended up like this. Windows sized to allow for aftermarket Alu cills. Upstand Groove to rear edge of cill only. No additional interlocking profile. 3 lines of arbo full length to cill top face far enough back to avoid visible gloop or compromising the drip/free air draining to front profile. Screwed cill up onto bottom of frame. Then Compriband trio around the cill and the frame as a unit. Fit to aperture (brick and a rough flat granite cill in this case). More arbo to front cill edge to granite. Insulation and Alu plate to arch as picture. We now have a sensible "drip" with no timber sat in the water on the granite so hopefully these windows won't rot as quickly as the old ones. The school solution would probably be a full depth Alu cill to come out to the front edge but it would look bad in this application hence the compromise in the photo.
-
Windows....which company did you choose and why?
gcm replied to Tom's Barn's topic in Windows & Glazing
Rationel Forma+ 3G Alu clad From the local Rationel reseller (Heswall) Barn refurb scenario - remove, replace, redo reveals. Very happy. It's early days for longevity but very happy with the installer support to design process and the attention to detail on the job. Memory of paying the final invoice is slowly fading. Rationel also did some custom multi-section windows for larger barn apertures for us. These were expensive and in hindsight likely could do better. They are OK and we sorted out the issues arising with multi-section and air sealing but I remain less than convinced that Rationel are good value where you go that far off piste. It did keep it all inside one supply and fit contract though. My reading here suggested they were a fairly safe but not a cheap choice and I do not disagree. For my outward opener traditional look (planning) and becuase of some size issues I didn't have a huge market to choose from in Alu clad timber. The install was refurb with profile change not fresh build so the installer who would take it on was also difficult to find. (Job too small for builders, too big for joiner with a van). -
Fitting American Oak interior window boards as replacements during a Rationel install. Various sizes from (750mm-2900mm) x (240mm-460mm) x (25mm) thick I need a bit of wise counsel with two issues to get it straight in my mind before I am stood there with the joiner looking at any exposed horrors. Q1 Fixing Are there any issues with using the right angle metal ties screwed up underneath the boards e.g. x3 (L CR R) for the normal sizes - or less/more) then to fix front to block below the aperture plastered over. This is an invisible alternative to top down drill screw and fill. We are damaging plaster getting the old boards out) so could do it - just not clear if it's a good or bad idea - safety, rules, oak specific issues if any warping etc. etc. Or what about screwed down mdf/timber batten below and glue the oak board to it as an alternative (depending upon what mess we find underneath what is there) Q2 Finishing interior american white oak with a clear stain/coat Would something like Sadolin Extra Durable Clearcoat do the job - sufficiently for UV (assuming I like the honey/yellow colour on a test patch) ? Another alternative seems to be a Danish Oil such as Liberon (ditto) I want to keep the colour light (for bouncing light in) and appearance - to see the wood, to have some UV protection against greying. A little water resistance (any condensation and pots). In a perfect world would go water based and have something lower voc for the job and venting later and not too difficult to apply - if such a thing exists Thanks for any advice
-
Chopping back reveal plasterwork without removing windows
gcm replied to gravelld's topic in Windows & Glazing
Similar experience to you with sourcing refurb Although it may not help directly - my experience was letting a refurbishment project moving from thinner profile softwood to Alu clad. Same requirement for cut back to get at straps to remove and then more generally clean up including interior sills out to create an appropriate detail to the new thicker window profile. When I set out I thought if all in one wasn't a thing - I would cut the job into "cut back" + "make good" contract (so cutting wisely for make good to be easy is incentivised) and "window source and install" (perhaps with supply separate according to system). Didn't work out so well. A lot of "if we must at a huge premium" pricing came back from window installers or they refused to get involved with make good. Finding a local joiner who wanted the work proved tricky too. One good thing I did pre contract was to get one potential installer (for cash for time) take one out speculatively and put it back - so I could get a look at "what is there" vs what is vaguely described on the drawings. That saved me a load of trouble with accidently buying windows that would not fit due to the brick line depth being constrained so the compriband would be too far back (that was velfac as it goes - nothing wrong with it just my particular brick/cavity/block in some arches) It was a hard journey to get a single supplier to do it at all but I got there in the end. Albeit for a premium due to not having 2 Most installer firms expect there to be clean ready to go apertures or a builder - Man with a van thought it was too big and wouldn't quote, most builders thought it was too small and fiddly and wouldn't quote and most installers didn't really want to get involved with this level of complexity. In my case the window installer's plasterer is unlikely to be my new best friend either. Will have to make him some nice cups of coffee. Midsize family firm with own crew seems to be the sweet spot where a few extra trades doesn't bother them Good luck. G -
Thank you - perhaps I should have been clearer on "easy" - what I meant was that I don't through lack of understanding want to miss some (arbitrary) threshold and lose what are for this building - precious points (such as to be eligible for incentives, to rent, even to sell (one day) - for want of an avoidable slight spec issue. We don't have an EPC at present (occupation pre-dates) but have read the media on renting, RHI eligibility etc so the concern is raised and I find it difficult to back trace EPC - SAP - WER - Uw to this or that specification of window as offered to manage that risk. Other than the <1.6 rule which is clear and binary. Still finding it odd that a 1.03 Uw triple glazed window like this one is simultaneously expensive (in Alu clad) has an apparently decent Uw (vs the BC minimum) and yet is still "four categories down" A++ A+ A B C" on WER) - that does however explain why they don't advertise it in that way. Either I am looking at the wrong window ? Or WER is a bit weird ? Or both ? 1.4 vs 1.03 x 45m2 x 16 deg = ~266W difference 2-3 people sat about - or an evil older plasma television 1kw vs 740W losses - worth having if cheap - draught proofing a better bet. Just don't want to be told - you should new better windows on the EPC when it is done - I need to replace due to blown units and expiring timber so want to invest in the right stuff. Reading 2012 SAP guidance - 3G didn't seem to buy you anything special. In some circumstances you could use the Uw actuals in the modelling (I was left unclear on the actual rules and practices as to when you can or cannot and which product documents or whole window estimates are proof) and indeed whether this helps to any material extent anyway. Actuals and assumptions used on walls and roof presumably matter a lot more. Marginal - I ran the one of the web calculators and it was £50 / £80 vs the existing 90's stuff (if performing to spec and well sealed which it now isn't hence replacement). My cost compare might in reality be a bit more favourable due to kerosene + wood burner heat inputs and if I put in my actual glazing some of which are on the large side as web calculators assumptions about walls + glazing may be off. Thanks again
-
One of my potential installers has suggested the following for alu clad timber to address a site difficulty with suspected insufficiently sloping granite cills. Is this a sensible design tweak or a case of everything looking like a nail if you are holding a hammer. Situation: Deep brick apertures, wall batt and block construction behind - rough granite exterior cils protruding (they are not flat yet could likely do with being steeper). See photo. The as is existing timber deflectors in front and the bottom of existing softwood frames have shown the worst paint loss and rot. Some water may well be being retained on the granite. It's rough so it runs off when there is a lot (from a jug) but surface tension holds a certain amount I have been uncertain about the merit of standing the new windows on the existing granite and relying upon the compriband at front timber line given the exposed edge along the line of the compriband seal. We have also looked at fitting some kind of "stub" cill water deflector (clipped or screwed to the face according to system) which will help run off, reduce direct volume, but not eliminate water retention on cill. Discussion with this approach has been on whether to silicone behind face mounted Alu stubs or not (i.e. making a bucket for water to sit in vs keeping it out). Have rejected full clip on Alu cills out across and down over the rough shaped granite edge as not a practical choice - too ugly although it would work. Grinding or even replacing the granite during the swap out was considered but undesirable on cost, logistics, difficulty with existing edges/finish etc. The fitter's suggestion is to use deep Alu cills for the windows to rest upon installed well back on the granite into the aperture leaving a lot of granite cill in front (appearance OK). Approx. 25mm of sloped down Alu in window finish protruding out from underneath the elevated window bottom sitting above the granite. The window being bedded onto the Alu cill behind and forward to the normal compriband weather seal line with some form of wet seal he used the phrase "arbo" and argued a special kind should be used for longer life. Then normal Compriband around sides/top etc. Thoughts on these two ideas, materials choice or alternatives to address the underlying constraint with potential water retention.
-
Selecting glazing - still rather a mystery even after some forum reading and googling I have the following back from Rationel on Alu clad FORMA Plus w.r.t glazing options Sample window 1.12 m2 area, side hung, twin outward opening sashes Data: Uw Gg Ug LTg WER 1 Glass (fillings) 4-24-4 Clear/Energy WE w. argon (1, 2) 1.4 0.64 1.17 0.82 -27.8 as a base cost from an earlier quote and discount offered thereon 2 Glass (fillings) 4-22-6,8 Toughened Clear/Laminated Energy WE w. argon (1, 2) 1.4 0.64 1.16 0.8 -29.5 at 5% uplift 3 Glass (fillings) 6-18-8,8 Tougenend Clear/Sound Laminated Energy WE w. argon (1, 2) 1.38 0.61 1.13 0.79 -29.4 at 12% uplift *4 Glass (fillings) 4-18-4-18-4 Energy/Clear float/Energy WE w.Argon (1, 2) 1.03 0.53 0.53 0.74 -13.8 at 2.50% uplift 5 Glass (fillings) 4-18-4-16-6,8 Toughened Energy/Clear float/Laminated Energy WE w.Argon (1, 2) 1.07 0.53 0.6 0.73 -16.5 at 9.30% uplift 6 Glass (fillings) 6-14-6-14-8,8 Toughened Energy/Clear float/Laminated Energy WE w.Argon (1, 2) 1.08 0.51 0.63 0.72 -19.8 at 15% uplift *Upon first look option 4 (triple glazed) - 4-18-4-18-4 at 1.03 Uw appears to be the "value" pick (based on their "offer") - this feels like a very small uplift on an already "high" base quote as this seems a rather trivial difference between 2G and 3G. My questions: 1 Verify my understanding of WER and categories and feedthrough (or not) to EPC. Option 4 at -13.8 WER is still category "C" (-10 to -20) if I have understood WER correctly and not been misled by the web - and options 1,2 would be "D" or worse on this calc but still "pass" for an install on u-value criteria. So the option 4 window has good (but not great Uw) (1.03) but it doesn't look so great on WER presumably due to its lower solar gain So is WER and the category actually significant in either real or "regulatory" world ? I am keen not to discover that I bought the wrong windows at a future EPC assessment (house doesn't have one). I am also keen to grab easy EPC "points" where I can - help ensure access to RHI/FIT and similar. If I get and keep the manufacturer glazing test documentation and the Uw numbers for each window presumably these can go into the EPC SAP estimator? (Scenario is NOT new build so will be working with the reduced "rules" on when "real" vs category estimate data can be applied and the allowed documents. 2. We have specified as safety requires - low level glazing etc. What's the rationale to upgrade from 4 to 5,6 above more generally. I am guessing more "secure" as in harder to break but that is not an especially critical requirement in our location. Also one of the options *may* be better acoustically (but how much vs a 3G base is a question) it seems it is mildly less good on energy (narrower units presumably) and it also seems a lot more expensive. Am I missing something as to why these latter choices and the 2G equivalent are a good idea ?
-
I have an old (perhaps >100+) stone flag/thick tile roof which is most likely to be kerridge sandstone as that is local - last refurbed ~80s+90s. Rather Heavy. Not too concerned about incremental PV system weight but it will need care and thought in terms of what and where it is anchored to in a barn conversion roof construction. A windy exposed site. I have reservations about a ballasted over ridge frame drop on and tie it down approach - solar sailing ! but I am open minded at this point about what would be the safest and least invasive approach in context. I am interested in others' experiences with installation approaches and suppliers for PV on barn conversions / this kind of roof. This is retrofit as a full renovation in not in progress and it was converted slightly too early for this to have been done at the time of conversion. I am cautious about disturbing an old roof outside of a broader renovation and perhaps uncovering latent requirements - it doesn't leak at present - it would be a shame to trigger this and accelerate wholesale roof works. The site has PV potential as there are a couple of large SE and SW aspects which could easily hold the maximum allowed FiT system or much larger 3x-5x in terms of roof space. It is very tall for a 2 storey building and the roof (and cars and everything else) are prone to moss growth. I am also slightly concerned about maintenance access for cleaning without scaffolding having not researched these aspects to retain output yet. Direct experience or thoughts on things I should be thinking about in up front in planning other than carefully considering suppliers (builders, roofers, sparky) with the right credentials for this type of building.
-
I have planning consent after 8 months (only done because of PD revocation) for a job which normally is PD and self-certified at that - rubbing salt in my paper cut wound compared to the pain felt by many here. I updated my plans to adjust to planners feedback along the way to move them from "minded to refuse" to "consent". Filed plans reflect the compromise not my original intent. They gave me the normal "to plan" and "to sample" stuff but also added back some of the things we had changed and which are now on the plans as conditions as well. As they are the same bar extremely minor drafting differences this is - "mostly harmless". My challenge now as a first timer in process is how to handle a couple of risks I have and the right approach to the paper chase with "consent with conditions". Now I can of course clearly go and ask the county duty planner - likely the easiest way to get to talk to one - which precise forms would they like locally for these. Before I go and do that - I feel a strong urge to understand the best and minimal approach - lower friction options - the boundaries of "unreasonable behaviour" - such as sending me off to start a full application once again for say "one glazing bar" Examples 1 Minor change to elevation plans As I procure and finalise product in light of planning conditions - I have the usual issues where some solution options drive minor configuration changes (the first is literally one pencil line on the elevation plan to illustrate a new sectional window break/glazing bar. Tactics clearly could be A) Ignore forever as too minor to be a practical concern or challenged. B) Bundle any of these up if there prove to be several and make an "NMA" once the job is well on the way to being finalised (albeit with a risk of an inconvenient refusal - costs are at the higher end for these components so enforcement risk of reworking them is low probability but high impact. Waiting or longer paper chasing before committing the work likely kill the 2018 weather window which I can do without. 2 Variation of an awkward yet explicitly listed planning condition I have a planning condition on an exterior finish both the usual "to sample supplied xx.xx.xx and also restated as a standalone condition listing the finish Having read the county plan sections referred to in the justification - the link between the broad strategy statements on character and the mandate to use this very specific finish is extremely tenuous. Clearly "because we say so" is good at least until an appeal or other process to vary the planner's decision. I am not currently aware of any other use of the mandated finish in the locality. Indeed I may yet find it fairly hard to find it in similar context in this colour - it comes up in darker colours more. This is my next move either to reconcile myself to it or to the necessity of fight. Some extra costs and an unhelpfully reduced choice of products being available in it are factors arising out of the condition. Options seem to be A) Appeal - I am in timescales to raise one - objecting to the conditioned consent and also a householder type application - but whether this type of condition varying appeal is a "householder category appeal" seems ambiguous to me in the what is used for what descriptions of appeal types on the planning portal. B) Make a new application - please no - the consent letter says generally as boilerplate that this is my option to change things. C) Go and see the duty planner with potential configuration and samples and try to gain agreement to go the NMA route - if they *can* change the condition that way. Does that work? Am I in fantasy land ? D) Ignoring it and doing something different job wide doesn't seem like a very sensible plan to me. Thoughts ? Graham
- 2 replies
-
- nma
- condition changes
-
(and 1 more)
Tagged with:
-
My areas for most active current research are: 1) Ideas and alternatives for dealing with a fairly full height barn aperture 270cm W x 333 cm H (to arch ~312cm to sides) Current thinking is around Alu clad multi-section window for on site assembly at installation based primarily on weight handling and site access factors and cost to overcome these for something huge in one piece. Never say never but sections appear to be the way to go unless experience says different. The existing softwood is 5 vertical strips arched (cheap and life expired embedded units inside exterior and interior frame - no horizontal break. Lots of frame - but adequate glazing. Don't want softwood again. Too much weather out there and too much faff on this window. So could be 5 strip or 3 strip vertical or a square (with bonded glazing strips) and an arched headlight above with matching strips albeit with an unwanted horizontal break but fewer joins. I have been shopping window suppliers one at a time and some find the strips too narrow (if there are five), some find the height a problem and others again don't fancy the curved top. Maybe there is something radical yet cost effective out there I haven't yet spotted. I do hope so. 2) Retrofit red brick+block timber to alu clad installer fitting experiences - lessons learned - "I wish I had known X before" and any suggestions generally borne of experience with Velfac 200, Rationel FormaPlus, Broxwood or STM where they are working up prices. 3) Recent Alu clad sq m high level supply rates and install fees vs job size and type (retrofit, new build) - whatever I can get to aid benchmarking what I get sent by resellers and fitters To the le-cerveau query the ~44m2 is all windows. No doors in that number. A mix of big and small from a tiny 0.3m2 to the 9m2 of problem child item 1 above.
-
BC question on trickle vents and stoves with external air supply
gcm replied to gcm's topic in Windows & Glazing
It has spurred me to think about it as background ventilation calc 23x8000mm2 existing background and for the room 5x 8k and reread the rules again. A simple retrofit fail on 7.3 - if they already have them then they must have them again at the same size. Not very helpful and it might also fail on "not worse than" depending upon the view taken on the other added ventilation and my hopeful sounding offset. Regarding Fensa - some of my suppliers want me to go LA BC route (as seemingly not members of and indeed sceptical of self cert). Not sure if this is the province of those using rogue sub-contractors or some of these and also those confident in their work vs BC. If I do go that way it may be worth tying them to some holdback to the BC signoff of installation matters if they are not providing it en passant. Thank you for your thoughts- 3 replies
-
- window replacement
- trickle vents
-
(and 1 more)
Tagged with: