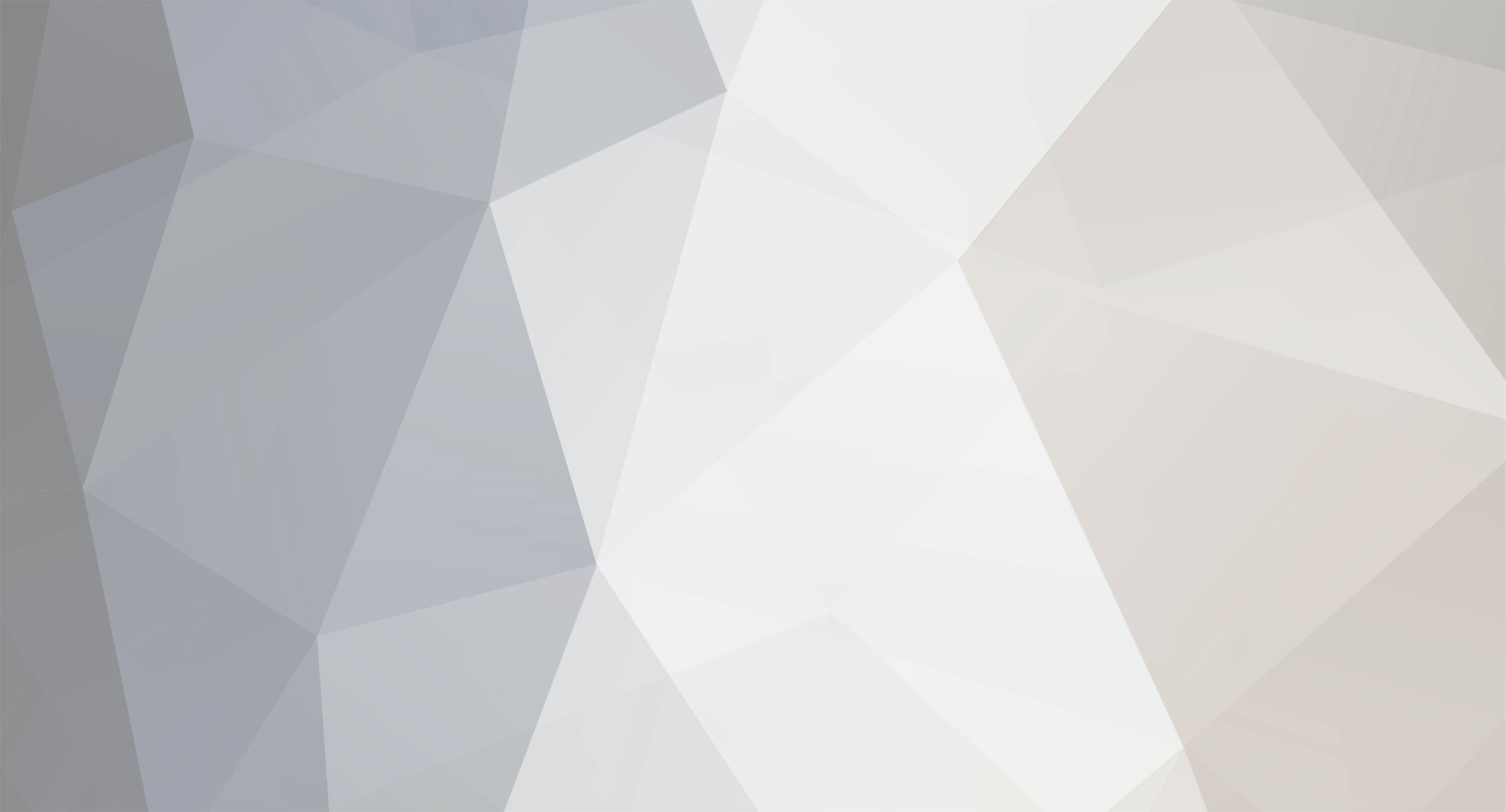
Hilldes
Members-
Posts
375 -
Joined
-
Last visited
Hilldes's Achievements

Regular Member (4/5)
54
Reputation
-
Loxone Wallbox - benefits for Loxone Integration?
Hilldes replied to Hilldes's topic in Networks, AV, Security & Automation
Thanks @Dan F. Much appreciated. My setup is simpler in that I don’t currently have PV or battery storage. I did google for reviews of the Loxone Wallbox but got no hits apart from Loxone marketing materials. -
Planning Condition - does this remove PD rights?
Hilldes replied to Hilldes's topic in Planning Permission
Thanks all for the replies. Basically got two 12'x36' static caravans in the back garden that won't fit through the side access and no other route out of the back garden 😯. So thinking about having one demolished and removed and keeping the other as a garden building (shed). But shielding it so it looks kind of like a shed and not a caravan. -
Can someone help interpret this wording please from a planning condition applied to an approval letter: " Notwithstanding the provisions of the Town and Country Planning (General Permitted Development) Order 2015 (or any Order revoking or re-enacting or amending those Orders with or without modification), no enlargement within Schedule 2, Part 1, Classes A and B shall be carried out on the dwellinghouse hereby permitted. Reason: Having regard to the size of the dwelling approved, the local planning authority wishes to retain control over any future extensions at the property, in order to safeguard the openness of the Green Belt and the residential amenities of adjoining properties. " Does this mean effectively that Permitted Development rights have been removed for the plot? More specifically, would it prohibit the erection of a garden building that would normally fall within PD rights?
-
VAT reclaim delays
Hilldes replied to Oldsteel's topic in Self Build VAT, Community Infrastructure Levy (CIL), S106 & Tax
Received a text from HMRC last week….. ”HMRC: Your DIY refund has been issued. Please allow up to 10 working days for it to reach you, don't contact us before this time. You'll receive a letter with more information on how your refund has been calculated.” Paymet received and a letter received this week. Claim was submitted 30 Nov 2022, so just over 4 months in total to process. -
VAT reclaim delays
Hilldes replied to Oldsteel's topic in Self Build VAT, Community Infrastructure Levy (CIL), S106 & Tax
I got a letter this week from HMRC DIY team to confirm receipt of my claim- which was submitted 3.5 months ago. Said they will endeavour to process with 6 weeks. -
No Structural Warranty (due to COVID!)
Hilldes replied to Joanna Susskind's topic in New House & Structural Warranties
@Joanna SusskindWe just got our structural warranty - 5 months after the building control completion "final certificate". Now off a self build mortgage and saving £700 per month in mortgage interest. This delay was due to the warranty provider technical auditors being a total PITA (warranty provider is Protek). So be careful who you choose if you do need a warranty. In your case, I'm not sure how you get by with just architect inspection and no warranty provider from the start - I guess it may be different in Scotland? Either way, our warranty provider, building control and mortgage lender valuers all continued site visits throughout lockdown. I think you have a case in saying your architect should have continued inspections too. -
I remember when I was looking for a piling solution a comment about investigating an insulated raft foundation with piles - it was you I think. I went for concrete piles with reinforced concrete ground beam, block foundation walls supporting and insulated beam and block floor. This has a number of challenges such as the need to ventilate the void under the beam and block floor and the depth of escalation required for the min 300mm depth of the void. Being yours is a raft so it sits on the ground and has no need for a ventilated void?
-
UFH controls - conventional or home automation?
Hilldes replied to Hilldes's topic in Underfloor Heating
Stupid question from me: how do you know if a gas boiler is short cycling? -
UFH controls - conventional or home automation?
Hilldes replied to Hilldes's topic in Underfloor Heating
Guess you would only need one room stat if you are not using devices such a Loxone Pure switches (or similar) a your room temperature sensor. -
UFH controls - conventional or home automation?
Hilldes replied to Hilldes's topic in Underfloor Heating
Good question, would need a zone valve at least for the DHW. For the UFH manifolds, if you switch off the pump will that block all water flow thought the manifold? I would assume not but others I'm sure will know more than me. Mine is a gas boiler, for a heat pump using the heat pump controller may be better - as per @JohnMo... -
UFH controls - conventional or home automation?
Hilldes replied to Hilldes's topic in Underfloor Heating
The Salus Auto Balancing Actuator sits on the return manifold on one of the longer loops - as shown in pic below - 5th loop from the left. It is only required because the WUNDA wiring centre I selected requires at least one actuator in order to enable the pump and boiler call for heat. With a different wiring centre the actuator could be omitted I believe. Yes, one zone per floor - the GF manifold shown. -
Great if that is working for you, but for my application planners were not concerned- main reason being the village has an ecclectic mix of architectural styles, which we stated in the design and access statement. Also on demonstrating how you meet policy and make it easy for the planners is kind of difficult in Green belt when the key policy statement is the replacement dwelling must not be “materially larger” - and nobody really knows what this means including the planners. Our planning consultant said it would be interpreted as around a 30% uplift in GEA, but that was not enough for a bungalow on a substantial plot with many larger houses on the same road. But apart from GEA uplift what does materially larger mean in terms of ridge height, eaves height, volume? - no one knows how to interpret the policy. Then you get into more woolly policy wording eg that it shall not impact openness of the countryside, which means… I think it does help if you can actually talk to the planners if your LPA will permit this. We put in two pre-application advice requests and one full planning application and never got to speak to a planner.
-
@jayc89 I have Velfac windows and bought a load of the proper lugs that Nick describes above. However, I did not use any of them and screwed through the frame in all cases. Whether you can use lugs depends on your wall build up. Mine is 140mm timber frame with 50mm deep battens then render board and thin coat silicon render (board and render about 20mm thick). If you want to set the windows back from the surface of the render by 40 to 50mm, then you may have to screw through the window frame because even the shortest lugs will be too long - with the lug screw holes missing the frame and extending over the insulation layer on the inside of the timber frame.
-
This week I finally received my warranty certificate of insurance - 5 months after I received the completion/final certificate from Building Control. While there have been many challenges with the self build (as we would expect) this battle with the warranty provider has required by far the most effort, frustration and out of pocket expenses. I estimate the out of pocket expenses being around £7K for this 5 month delay - compared to the cost of the warranty policy £1,435.