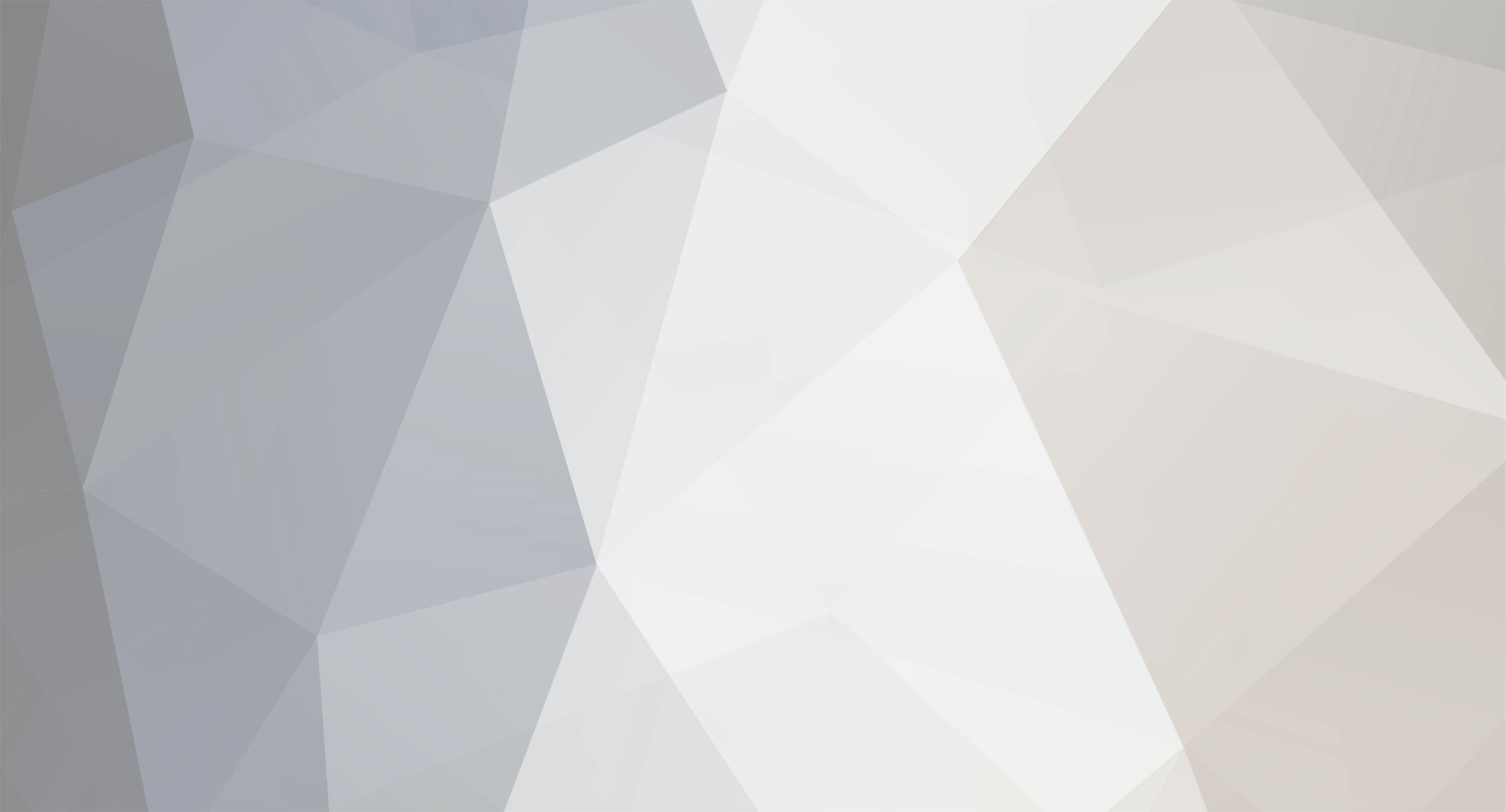
SBMS
Members-
Posts
943 -
Joined
-
Last visited
Recent Profile Visitors
6952 profile views
SBMS's Achievements

Regular Member (4/5)
199
Reputation
-
Have done đ
-
Hi Zelem Yes we have gone this route. I asked the very same question to both the fabricator and Senior themselves regarding the claimed Uw value. They use a standard calculation method using EN ISO 10077, for the reference CEN window. The window size they simulate with is 1.23 m wide Ă 1.48 m high. This reflects a standard window size as the Uw value is related to the proportion of glazing to frame. Remember - the larger the window, the closer the Uw value tends to the Ug value. We have larger windows than the CEN standard so will tend to a better U value - although we have some spacer bars on some windows that will wash this out. The problem with any claimed Uw value is it relates to a number of related components that won't reflect your window; and therefore all they can do is provide a reference size so you can compare between manufacturers. The calculation of the Uw value (I looked it up because I wondered) is actually remarkably straightforward. You need to know the u value of the frame, the glazing and the dimensions of the thermal transmittance strip. One of the reasons Pure's Uw is low is they use PUR -polyurethane resin (~0.022 W/m K) whereas many other manufacturers use Polyamide (~0.30 W/m¡K) thermal break. Thats an order of magnitude improvement in thermal conductivity. PUR is already commercially proven in large systems. So with this assumption, is their Uw claim reasonable? On average the frame area is around 15-25% of the U value heat loss, so the thermal break is going to improve the Uf value by around 30-40%, so I'd be looking at a reduction of around 0.2â0.5 W/m²K for a Uw value. That pretty much checks out with the difference between their standard Polyamide broken windows, and the Pure windows. Without independent verification then (which few glazing providers bother with because of the challenge of different window makeups - and the fact that the reference CEN window calc is pretty simple), you're left with looking at the reliability of the fenestration provider itself. Senior are prevalent in higher specified commercial glazing - not massively prevalent in domestic glazing. I see this as a benefit - they're a 34 year old company, which imparts a good degree of confidence. Check out the NBS Source Case Studies (https://source.thenbs.com/manufacturer/senior-architectural-systems-ltd/dVSDoRHE7zaprhEbgnigyf/case-studies). They've installed Pure in Grantley Hall Spa & Hotel, the main welcome building in RHS and the Castle Park View scheme in Bristol - tallest residential building in the city and it achieved level four standard in the Code for Sustainable Homes certification. These are the typical installations Senior does - high specification, high end commercial glazing. I think they are one of, if not the, largest privately owned fenestration provider. We're not talking safestyle UK here. Do I trust that they are putting PUR not Polyamide thermal breaks in? Yes. So from this, do I trust the claimed U value of the window? Yes. Did I look into Senior (ÂŁ50m annual revenue last year, profitable, well reviewed?) Yes. Are the windows fabricated to a high quality? Well that's down to the fabricator selected which I can't comment on, but I visited the factory where our fabricator is based, spoke to their MD, spoke to a seasoned installer who has had no issues. So all in all, I'm pretty comfortable with the claims and my decision.
-
I think theyâd have a hard time justifying commencement just with presence of machinery. If you werenât actually using it in the context of commencement of development (which is defined in the t&c act) itâd be a hollow challenge. CIL commencement is defined by the acts definition of material commencement. So demolition works, digging trenches for foundations, pipe laying, road layout etc. âdigging holesâ would trigger commencement if those holes were clearly in relation to the development the CIL relates to.. I would always submit a start notice anyway there is literally no reason not to!!
-
Tax and self builds
SBMS replied to nod's topic in Self Build VAT, Community Infrastructure Levy (CIL), S106 & Tax
Ah didnât realise that was who was offering the 30%⌠Why sell though? -
Our joiner did it. Stapled a bit to hold but then the battens are the actual thing that mechanically fixes the membrane to the sarking. The staples are almost temporary and I think could be skipped if itâs a still day and youâre battening as you go??
-
Tax and self builds
SBMS replied to nod's topic in Self Build VAT, Community Infrastructure Levy (CIL), S106 & Tax
Why did you sell @nod? Why not take the 30% uplift guaranteed? -
Fan coils instead of ac connected to your ASHP? They can be a bit more immediate then the slab?
-
24v lighting circuit - good or bad idea?
SBMS replied to SBMS's topic in Networks, AV, Security & Automation
Thanks all. Im a bit worried wiring two 12v mr16s to 24v and was already concerned about putting non standard lighting circuits in.. I think it sounds like I am probably best off with mains downlights and trailing edge dimmers. The loxone 4 channel mains dimmer is ridiculously expensive so Iâll probably go for the whitewing dmx. I think Iâm better off going for gu10 fittings and then getting something like a Philips master DimTone? -
24v lighting circuit - good or bad idea?
SBMS replied to SBMS's topic in Networks, AV, Security & Automation
Is MR16 not 24v? I assume the 24v dimmers wouldnât work? -
Looking at loxone home automation. Seems that life would be much easier and cheaper with regard to downlighter dimming if I went for 24v lighting circuits for downlights. Has anyone else done this? It seems very difficult to find 24v fittings but I assume I can use 230v fittings that donât have lamps, add my own gu10 24v lamps and then can dim from the 24v loxone dimming relay (4 channels for ÂŁ70 odd). Any downsides to the above?
-
Whatâs your approval say? Is it conditioned stating you must build to a drawing that has an internal layout? If yes, by the letter of the law you should apply for a NMA. But who would check? If you change the layout internally in such a way it affects anything external then definitely apply. weigh up the chances of enforcement (low probably) from shifting a few walls (after all, youâre allowed to post build).
-
Interesting that the 10 modulates lower than the 12 in heat mode (and outputs higher) but in cooling mode the maximum output is identical. (Page 5) makes me think itâs the same hardware but software is range setting in heating mode but allowing the compressor to run full speed in cooling mode. Which actually is a useful thing for me as there is no additional cooling output with the 12kW but the 10kW is possibly better suited for my heat loss requirements đ¤ˇââď¸
-
Does the 10kW modulate down to same level as the 12kW? Whatâs the point in going for the 10kW then??
-
Itâs 9kW at -4 in total. Sorry - the installer originally sized 12kW but they werent accounting for heat recovery so had a higher heat loss. I thought you were saying the heat loss calculation was wrong. They donât have the calcs yet for updated heat loss. Interestingly heatpunk which produced the same output picked the 12kW as well, not the 10⌠I guess I have to account for DHW as well
-
What is your current approach to cooling?