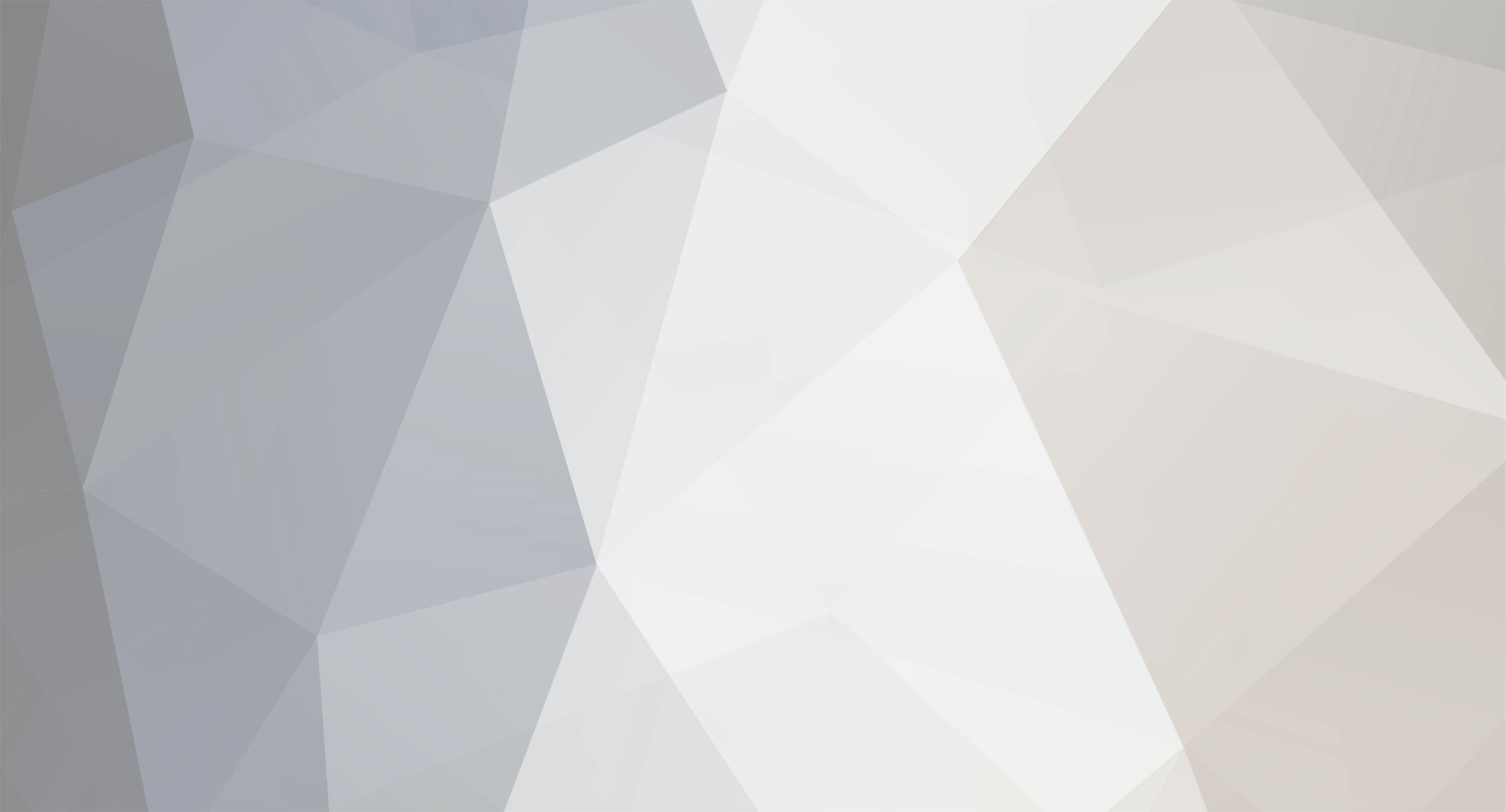
Babak
Members-
Posts
24 -
Joined
-
Last visited
Everything posted by Babak
-
Hot water might become an issue on colder days and nights if I were to use the heat pump for it. But, on the other hand, even with today’s prices I reckon using immersion heater for a week or so every year to supplement the pump will be cheaper and faster than getting a bigger heat pump that will cost around £1,000 upfront and likely will fail earlier due to more frequent cycling. in theory at leat I should also be able to use subsidised immersion heating for HW on coldest days as I have PVs. Just a thought though.
-
so in the end I have just signed the paperwork for the smaller unit. The larger unit modulates down to 4kw and the one I went for down to 2kw. demand at -1 is 6kw with the unit maxing out at 6.8kw. I may still get a low loss header for defrost purposes though. HW is a potential issue. The unit I am getting is a Hitachi Yukati S Combi with a pre plumbed tank all within the same enclosure as the heat exchanger for the internal unit. The original decision was to go for a 260 litre version. However, as of June they have improved the model by changing the capacity down to 220litres. This is probably still OK for my family of 4 plus the occasional guests. The new version’s tank is a heat reserve, so hot water is heated on demand and cyclical heating to 55c is not necessary. I guess there is also slightly less available hot water due to exchange efficiency losses. On the other hand the unit is ultra super insulated and so if I time the water heating well, I could actually save money. I have about 4kw of solar PV’s (inverter size, actual PV’s are higher rated), so paradoxically enough may be able to use direct (not pumped) electric heating on the coldest days as they tend to be clear and cloudy days slightly warmer. With some tinkering I could potentially use immersion heating only when it is coldest so the heat pump just warms the house, assumption being the water stays hot until the next morning, ignoring intermediate use. thank you for your note about your 5kw ASHP. I was beginning to have my doubts about the heating specs given the entire planet and their dog wanted to upsize the heat pump and the UFH. It is good to read persistence does pay and that low energy designs actually work.
-
I would possibly have gone for the bigger output, but the outside unit is double the size as it jumps to two fans. But is also a point of principle. There is a design with certain calculations and also a largish built-in margin for errors, inefficiencies, etc. which was being ignored. unfortunately it became a point of principle when he decided to ignore a big part of the calcs for a very weak reason. He might have thought something in the lines of “what if the calcs are not right? What if the MVHR ends up recovering only half the heat? Etc etc”. I would have resisted those less on the basis of an SME going for gut feeling. But that was not the case….
-
We got our as-built EPC
Babak replied to Conor's topic in Energy Efficient & Sustainable Design Concepts
Agreed, TH should be more open and upfront about their roofing system so the work that needs to be done is planned in advance. We have used aluminium tape over most of the panel joins internally. To top that off we are using double foiled bubble wrap as an extra layer of insulation and barrier before plaster boarding. I think if we do not do this there would be a very high risk of condensation through small gaps between panels where glue may not have been applied. To illustrate, we had a LOT of water coming in after the panels were set up. Huge amounts were due to dormers edges, which were formed by cutting the panels and glueing them together, not being fully water tight (and hence not air tight). But a couple of places we could actually see light coming in from the sky where there were no dormers. Just panels not being put up properly. We wised up to this only because we read the technical manual and had water ingress early on. The installation was done by TH, so we could easily have missed it had we relied on them fully. But also bear in mind you can lose air through door and window reveals not being properly sealed…. See the videos below for fun! We only managed to stop the leaks once the roof membrane was fully on, no amount of PU foaming inside or out was working. Fortunately there was enough rain in May and and June to realise we had an issue!! IMG_1421.MOV -
To be fair to all installers, common sense is only common amongst those who have been through the problem and solved it already. It is surprisingly uncommon otherwise. to illustrate, I had similar issues with UFH designers and kept moving on after the first conversation. They mostly could not understand the low heat losses and wanted to stick with statistical heat loss factors for UK new build UK housing… I actually registered as an installer with one of the larger suppliers and got access to their online tool for working out heat requirements and pipe spacing based on floor and fabric types. Also had issues when looking for SE (found a really good one though - no prior experience of my ICF and roof, but with open mind). And ground works guys .… Majority just wanted to stick with how they done things, and only a few willing to listen and do some thinking /research (also found a really good groundwork’s guy!)
-
…. But there is a positive to all this….when looking through the forum for similar issues I came across a discussion of switching the heat pump to chilling mode. Looks like it is a little more complicated that I first thought, so can plan for it better…. 🙂
-
He has changed the numbers for anonymity. He is also saying it is for ‘him’, even though he is the installer. The actual numbers are just over 6 and just over 8kw, which are just below the two heat pump models output at -1. When you go from the smaller model to the more powerful model, the external unit gets an additional fan and becomes almost twice as big. Also a no no for us! Fyi this is the gentleman’s comment as he forwarded the MCS reply to me. I suspect his other installers have not actually installed in a house with MVHR. Dear Xxxxxx Please find forwarded the reply that I received from MCS regarding my question about using heat pumps with MVHR. I followed their recommendation and spoke to three accredited contractors, including Joe from Xxxxxx, who all said that when working out heat losses of buildings to size a heat pump they do not include the affect of MVHR. I personally agree with this approach particularly when using a modern intelligent modulating heat pump model like we are proposing for you. Best wish
-
So taking the above approach, when the MVHR fails, a couple of windows open. If it gets too cold, a couple of electric heaters kick in. Now try convincing my installer of it. TBH timelines are a bit tight (as with any new self build) and I have too much invested in the make and the installer, otherwise would just move on….
-
It is medium sized company and he uses a software for heat loss calculations. The issue is that he wants to exclude the impact of heat exchanged in the ventilation system, yet include the heat lost through outgoing air. I actually think he is genuinely interested in protecting me, but just does not quite get it. This is what he wrote to the MCS and the MCS reply (he changed numbers as I have for anonymity). He says he has consulted with three other installers as suggested by MCS below, but I reckon t(e installers are also unaware of the difference between MVHR and central ventilation. Query to MCS: I am thinking of buying an Air Source Heat Pump (ASHP) and having Mechanical Ventilation and Heat Recovery (MVHR) installed. The heat loss calculation for the house confirms use of a 16 kW heat pump without MVHR but reduces this to 12kW with MVHR. My concern is that if I have the smaller 12 kW ASHP installed and the MVHR breaks down or stops working for some reason then the heat pump will not be powerful enough to satisfy the heat demand for the house. Is there any MCS guidance about this to help me choose the correct size of heat pump when using MVHR ? MCS reply: What you are asking is to do with design guidance, and unfortunately our technical team are unable to provide this. So we would recommend that you speak to at least three contractors and see what their response is. I can refer you to our best practice guide, which I have attached. There is a very small section on MVHRs on page 13. But the best route would be to speak to some of our installers. If you have any other questions please don’t hesitate to ask. Kind Regards
-
it’s the ASHP installer who is specifying the heat demand, not the MVHR supplier. SAP efficiency 95%. I need to get hold of the calculations, yes. They are not room by room though, if I remember correctly.
-
LOL, yes certainly looks like he is not comfortable with this additional factor. We did talk about the failure scenario, when we need to open the windows. But yes even then it is unlikely the ventilation losses would be as much as he would have as default in his calcs, which probably assumes trickle vent as well as through the fabric losses.
-
I wish I knew. I think his line of thought is that should the MVHR unit fail, I should still have all of my heat demand met through the primary heating system. But thank you, I will also argue with him that the ASHP is more likely to fail.
-
Hi, have a question about incorporating the impact of MVHR when calculating heat loss. Background: New ICF build near completion. My Heat pump installer has calculated I need 8kw of heat at -1/21. However, after incorporating the 90% efficiency of MVHR into heat loss calculations, this drops to 6.5kw. This was done by reducing heat loss through ventilation to 10%. This also synchs with my UFH room by room heat demand calcs. Theoretical efficiency of the MVHR unit is over 95%, and my u-values are conservative, eg I have double bubble-wrap foil under roof but have ignored its additional R value. Same with impact of plasterboards, render etc. So fairly confident about the stated heat losses not being more. Issue: My heat pump installer INSISTS that I should ignore the MVHR because it could fail and if that happens in the middle of -1 degree winter I need to have additional capacity for heat. He wants to install a bigger system to suit the 8kw demand. The change to the bigger unit means my outside unit will double in size, which I absolutely do not want unless I really have to. My arguments has covered the following, none of which has convinced him: - extra cost of bigger system (£1,000) will take years to be recovered through multiple failures of MVHR just when outside is really cold - even ignoring the upfront costs, having to supplement heating with electric radiators/fans for a couple of weeks every few years (IF the MVHR fails), is not actually that huge. - MCS has been non-comittal on this and says it is a design issue for the installer to decide - What happens if the heat pump fails? What happens if there is no power for 10 days? Why do we need to assume the MVHR fails? But not anything else? What am I missing here? I realise I am a little on the borderline with the 6kw system which only has a couple of extra 100 watts of power at -1 outside, but I am quite prepared to supplement that with normal electric heating when I have to. MCS have not objected, and it is my risk to take. Any advice? Is there a rule about excluding the impact of MVHR when calculating heat losses? It is just so incredibly odd that my installer wants to disregard the heat recovery impact when working out ventilation heat losses, which sure.y goes against the spirit of MCS. Thank you!
-
ICF window details - Be VERY careful
Babak replied to magnethead's topic in Insulated Concrete Formwork (ICF)
Yes its odd how different installers (and manufacturers) have such differing ideas about what should be best practice. My Windows and doors (Rationel) are also designed to rest against check reveals which I guess is why they insist on having the render done first - so they can pressure seal against those extra lips on installation. But in my case I had to remove the check reveals that come with TH. At 2.5cm plus the 8mm of render they would have been too wide for the frame to sit against and still have enough frame left between the sash and the external opening. Plus my frames would sit a little further forward so the TH lips would have been in the wrong place. I am a little worried about the DPC. I think the order of things as they will happen in my case will be 1- Render all the way up to the opening maybe slightly lower, 2- put DPC/DPM on reveal base and use CT-1 or similar to seal against the render 3-Fix cill 4 - Install windows. Just keeping my fingers crossed that following Rationel requirements will at provide an installation assurance. The cill will be cut to go round the reveal (like normal installations) rather than into the polystyrene as suggested by TH. But if I am right, the cill was not the problem above, it was the lack of full DPC/DPM all the way below the cill? Not sure if it helps anyone else, but below is a hand drawn detail of how it should work in my case, except for the DPM and cill detail which will be slightly different (credit to my XXX for sharing properly drawn originals from elsewhere!). The cill will not turn back onto the render to close the air gap. What is Illbrook 295? I can find Illbrook, but not the 295. Is it tape or silicone type? -
I am using TH and the fabric has been built. Rendering using EWIPro silicone in a few weeks. So this is what has and has not worked well: - Do a lot of research about getting a building warranty if applying render direct to walls. A couple of large insurance companies (eg LABC warranty) now all but refuse to insure this except under some impossible conditions. See example here. - I have opted for an architectural warranty which covers direct render to ICF. - I did have the option for leaving a vent gap between the wall and the render using battens and render boards but somehow that defeats the purpose. Plus with 150mm EPS there will be a lot of long and thick screws into concrete, both expensive and slightly impacting insulation values. - my EPS walls are all scratched (seriously), pushed in, damaged, etc. not in a big way of course. Any serious damage can be fixed with low expansion foam. But when different renderers came for quotes, they were not worried at all whatsoever. They said the first base layer will smooth everything out. - I understand you can hose wash the silicone render within reason. So it is water resistant enough. However it MUST be applied well. EPS is NOT waterproof, I have seen it in action. It is not porous like plaster at all, but water will get through it eventually. Remember the old white foam coffee cups? - very critical to make sure openings are sealed well. Goes without saying. Remember there is no air gap like a two leaf wall, so sealing has to be much better. - I plan to glue plasterboard direct to EPS with some screws into galv steel for good measure. But remember, if you were to fix heavy stuff, the plasterboard and the glue may take the weight, but the EPS could get ripped. Very unlikely to happen with normal loads though. With thermohouse there is only 50mm EPS inside the house so is easier to reach the concrete core where you have to. I have also used sterling board for heavier stuff as suggested already, fixed to concrete using thick hammer fixing for my plant room walls. - for external render I have the option of using double scrim for additional strength. But just can’t see too many cars driving into the walls, so am taking a small risk… - thin coat silicone appears best for EPS. - if you have neighbours across the fence when you design the house, make sure the architect looks at fire spreading regs. - for windows, thermohouse is not really the most impressive out there in terms of product support. Most other providers offer their window jamb system and kit. - for doors and windows, make sure you choose a system which integrates well with ICF. Assuming you will go for low u value windows, they are often different from standard windows. So do not make assumptions. Eg with my Rationel windows, they want to place the entire weight of triple glazed windows on the base, possibly over a few spacers. ICF EPS is not designed to take that type of load and will give over time. My solution is to replace the EPS above the concrete on openings with thinner EPS 300 or 400, with a 10mm layer of cement or timber on top of it. To take the point load of the spacers. - think what you want to hang outside and allow for it at concrete pour time. Also for any holes in the wall, etc. - good luck. - on a separate note, if you are aiming for low u value house, then be prepared to argue with heating engineers who will (likely) use standardised parameters to work out your heat demand. I ended up registering as a reseller with a main brand so could enter my own house parameters. Yes, those with 30 years of heating design may still want to use heat demands from 30 years ago (no disrespect to those good advisers, but personally I gave up with JG and NuHeat for underfloor heating, though I am sure it was my bad luck. same with boiler/heat pump. I had to insist over several calls and after emailing informative documents, before my heat pump guys incorporated MVHR efficiencies into their air volume change calculations….
-
ICF window details - Be VERY careful
Babak replied to magnethead's topic in Insulated Concrete Formwork (ICF)
Hi I recognise those ICF blocks from TH! I have also used TH on mine. The roofers are almost done (tiling the roof panels installed by the same company) and renderers will come afterwards and then the windows. I know the TH technical manual states you must have the dpc all the way to below the cill and into the EPS at the sides and render and then cut, but my window suppliers have their own ideas and say that is not necessary with (aluminium) cills. But they do insist that rendering must be done first, so they can seal the window frames against the render (I am using aluclad wood by Rationel). Thank you for sharing - looks like I have only a few weeks to do research and make any necessary changes. -
Thank you for all the comments. my takeaways are: - loops not zones! - maybe two zones upstairs and downstairs - marginal extra cost of 1 thermostat - take the risk of wood floor damage through managing ASHP output (aiming for 35 degrees) - MVHR not a big player and rooms can still have diff temps - manage this through flow rate adjustments - yes, i have also thought of getting autobalancing actuators. Thanks again. 🙂
-
Zoning only to the extent that there are maximum pipe lengths so have to divide the floor space into manageable areas. But if one thermostat manages all the actuators on the manifold, I guess that is what I need! edit- to correct my phraseology, multiple loops, but only a single, and now maybe two zones based on comments above.
-
Hi Sorry if this has already been responded to as it must be an obvious question and indeed I have read a few discussion which are somehow related. Self build house, two floors, both will have UFH. House is well insulated and will have MVHR therefore I am guessing most of the house will be roughly the same temperature. Question is, to manage pressure drop, max pipe lengths, etc, I will have multiple ufh zones on each floor and one manifold per floor, and hence as many actuators, which I guess will connect to the room thermostats. Is there a way I can control multiple zones/rooms with just one thermostat? I am assuming this must be possible? Next level of complication is that upstairs I will have wood floor and so will definitely have floor sensors. So the question now is, can the wiring centre handle having a “master” thermostat which governs the air temperature, but also take a queue from the individual floor sensors and shut off the actuators if the water gets too warm for any reason. My thoughts are (and not sure it will work) that I will have basic manual thermostats in each room to protect against overheating air and floor, but will have a completely independent whole house thermostat to do clever stuff like heating demand curve, etc, which I will somehow have to connect directly to the heat pump or somehow manage to use as a master for the wiring circuit. Has anyone done this? Is it possible at all? I just think this must be such an obvious ask, or am I crazy here?!
-
Hi, just bringing this subject back up with a quick q. Self building bungalow with habitable first floor (attic) level below 5m height. Lots of steel in attic for purlins and to support dormer walls. I have installed metal stud frames for walls, the top railings of a couple of which I glued to the lower face of the beams with the idea that when we plaster board we will also cover all steel for fire protection. Rockwool to go inside walls. Plaster boarder visited yesterday for quote and says I MUST take the railings off to first box in the steel. Is that right? Does not make sense to me given what I have read. I kept asking why the impacted beams must be boxed in rather than be enclosed within the wall space but best he had was it was British Gypsum training/work requirement. FYI I also ended up arguing with him about not needing to double board for boxing in(but happy with fire rated). Also wanted to double board the ceiling as have some thin steel C-sections used as rafters. Still think 15mm or fire rated boards should be fine for the ceiling. It is my own house and will have kids living there but at the same time i don’t want to do something which is completely unnecessary. 30-45 mins is plenty to escape through windows (and we are also fire rating/protecting the stair case for extra measure) but just do not want to listen to someone saying I MUST build it like a 3 storey block of flats if I don’t really have to. Thanks in advance for any advice!
-
Detailed design after planning permission
Babak replied to Babak's topic in New House & Self Build Design
LoL, yes I am sure there will be a second home somewhere! Regarding the soil pipe, I will have a run of about 24 meters from the manhole near the site boundary to the furthest vertical section. Therefore I will not have a huge margin to play with the slab level, given the drop ratio of about 1:50 ish. As I have a height restriction and trying to maximise floor area in the attic, I just need to make sure the slab level is just right to accommodate a soil pipe underneath but not be too high to reduce the ceiling headroom. I think the calculation is pretty easy, but is one of those things I would like a professional to do - no room for errors involving a soil pipe here!!!! Looks like I have to cough up the £4K, thank you! -
Detailed design after planning permission
Babak replied to Babak's topic in New House & Self Build Design
Southeast England in Maidenhead. -
Hello I have the planning permission and am planning to proceed to the build phase. My own architect cannot help the end of August at the earliest and I would like to book the builders ASAP given the lead times. I plan to use ICF for walls and a related product from the same guys for the roof structure (Thermohouse). I also know the material types to be used elsewhere (eg type of render, first floor posi joist depth, opening dimensions, etc. Please can anyone help with the following: - Apart from the structural calculations and drawings and the building regs, what details are necessary before I can proceed to build the house fabric? - The only things that I can think of I need ASAP is where the services (electricity, water only) get in, and the waste pipes going under the building to connect to sewage, in particular the relevant elevations, etc, to make sure the sewage/waste pipe downward gradient is maintained all the way. Also possibly the height/elevation calculations so that with various layers added to the foundations, (floor/isolation, screed), my ceiling to floor distance is maintained at 2.4m. - I can deal with the wiring, socket locations, MHRV ducts, etc at a later stage and have thought of the potential issues, and how to solve them. - My thoughts are that the structural engineer will calculate based on my chosen material and their specs (type of ICF, roof, etc), work out where the support beams will have to be, then the foundation requirements, etc, and then draw the design to enable the build of the foundation and the building fabric, and this should also include where the waste pipe goes/its gradient (my biggest concern). - I have contacted two other firms of architects, and they are quoting £4K and £15k (yes) for a complete design drawing package, the latter of the two will also a little project management as well. These exclude structural engineer fees, so am baffled why the costs are so high. - I just cannot understand what it is that will take such huge fees to design though. Please, what am I missing here?! AM I being stupid for thinking £4K is silly? If anyone has suggestions in terms of who I can go to to get my drawings finalised I will hugely appreciate. Finally, one of my planning conditions is not to commence development above the slab level before external material has been approved. Am I right in presuming that I can still demolish? Thank you!