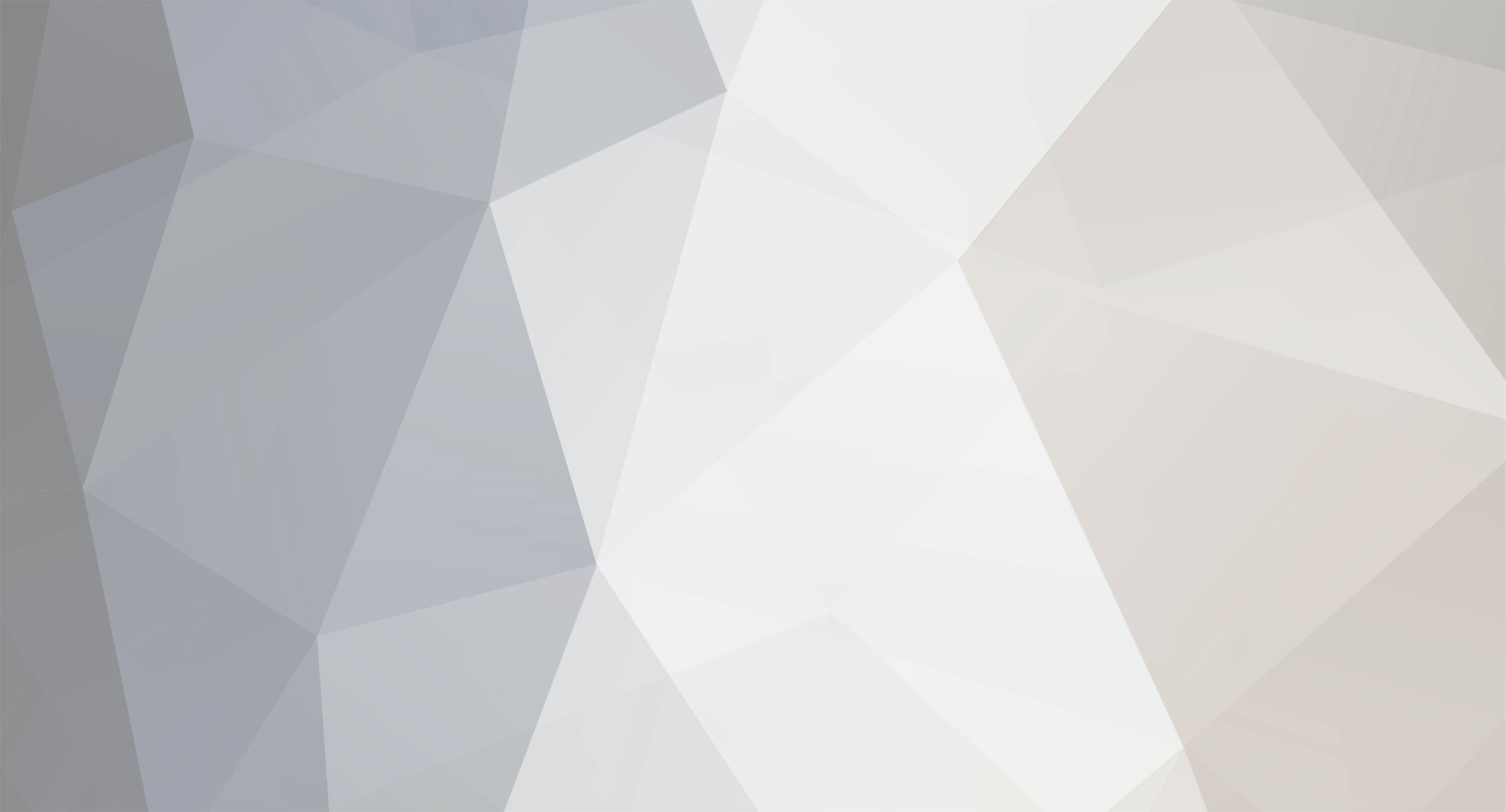
magnethead
Members-
Posts
100 -
Joined
-
Last visited
Recent Profile Visitors
The recent visitors block is disabled and is not being shown to other users.
magnethead's Achievements

Regular Member (4/5)
17
Reputation
-
Electric meter box on ICF
magnethead replied to Chanmenie's topic in Insulated Concrete Formwork (ICF)
This is what I did, I was terrified of touching the external insulation, so I put the meter box on the wall beside the house, and ran the ducting in under the rising walls, straight into the plant room, I had about a 1M to play with along the side shoot here. -
Yes, you are right, it looks like the fitting, I asked the plumber again and he said something about it being hard to seal the plastic and copper together (The upper insulation is wrapped around copper pipe that goes directly to the HP)
-
Hi There, I was wondering if you could see the issues with this? I found a small leak of glycol from my geothermal loop, just behind the heat pump. I think the glycol fill is supposed to last 10 years, but it would have trouble doing that I'm guessing even with a small leak. Is there an issue with oxygen getting into the system too, interfering with the glycol? Thanks for any information It might be hard to spot the small puddle of green glycol in this picture but it is there.
-
ICF window details - Be VERY careful
magnethead replied to magnethead's topic in Insulated Concrete Formwork (ICF)
The sill at the start is not my house, it was just an example of what happened after 6 years of life without the right detail. you are right it has next to no overhang, about 1c0mm, mine overhang a little about 40mm but not much -
ICF window details - Be VERY careful
magnethead replied to magnethead's topic in Insulated Concrete Formwork (ICF)
Cheers @ToughButterCup, sorry about the delay, fitting all my door handles the last few days. I'm in awe at this site, It's provided with me so much useful information, from when I was back throwing drawings together for the council, most of my first floors are poured concrete but a good section is rafters, and a guy suggested dropping them by 40cm which I did, gave me a lot more room on the lower end the Monopitch Roof. Just to spell it out about the Above, in case someone like me comes along here, the DPC should absolutely come out under your sill, then the render guys render up to it, and it's cut clean with the sill after that!! definitely not cut back inside the insulation. I was trying everything to stop this, leak, firing sealant into every little space. I wasted so much time on this. and in the end, this big dirty blob of silicone is what proved the leak was coming in the side of the reveal where it meets the sill -
Hi There, I just wanted to share my experiences with one of the biggest stressors for me on the self build, leaking windows - I had 3 of them and it drove me mad. I'm here to share the experience and ask opinions on potential fixes...First of all I didn't want moustaches on my windows like this: I can moan about the detail but in fairness......At least it's watertight Here are my leaking windows, the Stone window/Doors have a different detail which is working perfect(thank God, don't fancy ripping off stonework) You can see I jumped to the conclusion that something was wrong with the window because the only leaking windows were the windows with a fixed glass panel below an opening window..there is a more complex drainage system in these windows (Aluclad-PVC) ... Anyway after so many tests, it turns out it was the sill after all and you can see there is no DPC on the sills either below(It was cut short to allow the sills be stuck in place). you can see the window on the right was ripped out last Month in an effort to address these leaks. (DPC sill in at the moment) This is the install effort unfortunately I trusted the window installers who said once the DPC was past the concrete core, Everything was good (sweet Jesus) and I didn't know any better Sill was CT1 to the window support....That actually was fine and watertight as I later found out. Here is the final install: I extended the window side drip edge because the window company did not manufacture the sills the way I had asked...I guess they were going for the mustache look? Also they didn't know anything about drip edges under the main sill either? So I bent little strips of zinc and powder coated them and stuck them to the Sill. Here's a really bad front profile of the sill, the edge of the sill is actually bent around in a C shape up until my little zinc add on above. The leak is coming in on the seam where the render comes down onto the narrow little bit of aluminum. It was maybe 6mm-8mm wide. All of the other windows seem to be unaffected here's some of the water leaking in under the concrete cold joint the floor makes before the second Floor walls. and here's some lovely salt lines on the head of the opening below the leaky windows (about 1.5 years of leaking) I never respected that ICF was like a sponge for water, I should have sealed up the foam before the sill was put in That product mentioned by @Russell griffiths Illbruck 295 is absolutely great stuff, super sticky and seem quite durable too.
-
I'm not sure about Isotex, but I had quotes from Izodom and Thermhouse (just down the road from you)..and there wasn't much in it, I think THermohouse was slightly more expensive. (but the carriage costs on Izodom coming in from Poland would have made them equal) Thermohouse have a good few clients in the Kerry, Cork area. If you are going ICF, make sure you visit another house that is being poured first, to get an Idea about how important bracing is, I wish I had done that instead of trusting the installers supplied by Thermohouse, great product but the guy they put forward thought he was gods gift to building, but didn't internally brace one of my T walls, leading to a large bulge.
-
ICF integrated Garage Threshold details
magnethead replied to magnethead's topic in Insulated Concrete Formwork (ICF)
Just finished laying all my insulation in the rest of the house apart from the Garage. Thanks very much @AliG I love your Idea of bringing the flag stones under the Door, That Look like a Runner. I'll use a Good DPC under them to carry water to the outside and it should be Good. -
ICF integrated Garage Threshold details
magnethead replied to magnethead's topic in Insulated Concrete Formwork (ICF)
HI Guys, Thanks so much for your replies, It's my first time building and I don't have much exposure to this industry apart from a few summer jobs onsite. I got a lot of Solace from @AliG post, that's a very practical/experienced look at things and it's helped me get a bit of sleep on this. I had a close look at the door, and even in the joints between the panels, you can see gaps to the outside where you would nearly put your finger through. This garage will only be used as a workshop for me, so without thinking I ordered up all the insulation for the house, It's Kore100 insulation. I was told by the screed company, I would need higher density stuff for the garage if I ever wanted a car in there(I won't but if I sold the house, the new owner might, so I've asked them to exchange that bit of insulation) which is delaying things a bit, not a bad thing as I still need to sort out this threshold. So leaving aside Thermal issues for now, I see I have a massive NEW problem as I measure the door, and the front surface is actually recessed back 40mm from the insulation ICF insulation I'm going to need some kind of tray to carry water out side, I wasn't planning on putting an ACO drain outside the garage but maybe I need too. Here is the threshold at the moment. I am an amateur welder, so something made up out of stainless steel would be an easy option for me. @Russell griffiths I checked out a company selling fibreglass angle here https://glassfibre.ie/product-category/roofing-trims/ They seem to have only 75mm x 75m angle.......... THen I got onto a guy who makes surfboards, who said he could make up something custom, might need to make up a aluminium shutter first to make the piece. I was hoping to leave a little trough for the bottom of the garage door to go into, you have an almost flush design which makes better sense if the garage is being used for a car to drive in and out of I'm going to need some kind of tray(see large area outined in red at the bottom of the attached dsrawing) to carry the water away from the underside of the door and under the stone slab...I have plenty of Fibran insulation left over, I was using that under the screed where the stairs lands. so I stuck it in the gap in the updated drawing Thanks for any advice you can provide Garage_Threshold1.pdf -
ICF integrated Garage Threshold details
magnethead replied to magnethead's topic in Insulated Concrete Formwork (ICF)
Thanks @Russell griffiths , Would you mind making out a little sketch of what you had in mind please? I saw your comment at the end of @Vijay thread. Do you mean, you would put the Fibreglass angle under where the door would come down, and that would created a backing rod, to hold back the screed while it sets? Vijay was talking about putting a galvanized T section in the middle of the core? But it's more then likely a door would be mounted on the inside face of the ICF and thus come down just inside the wall like in my photo above (correct me if I'm wrong Vijay) -
ICF integrated Garage Threshold details
magnethead replied to magnethead's topic in Insulated Concrete Formwork (ICF)
Thanks @Vijay Just read the whole thread. Yes, the channel would be a problem, but I don't plan to have the door open much, hardly ever. It would be better to have a gradual slope tapering off, something you could do with a tarmac finish, but I'm going for Stone just outside the building. I take it you haven't pulled the trigger on your build yet? I'm under serious pressure to come up with a detail fast We'll see how it turns out like...I'll report back here either way ? -
ICF integrated Garage Threshold details
magnethead replied to magnethead's topic in Insulated Concrete Formwork (ICF)
Here's a quick knock-up, The way I have it at the moment, there would be a cold bridge with the flagstones coming up to the Door sitting on the Concrete core (or maybe that is not something worry too much about? My main concern is the heated garage slab(With is thermally isolated from the rest of the house ground slab(120m2) having a cold bridge with the outside. Anyone want to make a guess ? you could get to see your idea become a reality, as this all has to happen in the next two weeks, even though the screed lad is dragging his heels about getting over here to have a look. The 'garage' will never have a car in it, It's more of a workshop Garage_Threshold.pdf -
Spray foam on hydrodare heavyduty water pipe
magnethead replied to magnethead's topic in General Construction Issues
Well they are in place now ? they are about 30cm below ground and probably OK to not even insulated them.. But just wanted to give it a Spray, I was talking to a lad at a plastics manufacturer and he said the polyurethane pipes are unlikely to react with most things.... Pvc would be a different story -
Hi Guys, I've ordered up all the insulation for my house floor, should be coming tomorrow, I meant to get these details sorted before now but I'm not really sure how the garage door threshold is going to work...I originally wasn't going to heat it, but now I've decided to give it a go with underfloor expanded from the rest of the house. The garage and the room above it are cut off air wise from the rest of the house, airtight line is between them and the rest of the house. Anyway, Does anyone have any threshold details as, I now have to isolate the screed in the garage from the outside, you can see here my Door line comes down just inside the wall. Thanks for any words of wisdom and even more thanks for any schematic details. This is just to get the ball rolling, I'll knock up a CAD drawing later for this and put in any suggestions you make. I scooped out 50mm concrete in the core before it set, and the plan was to cut the foam upstand bits off, and lay some kinda flagstone paving up to the door line.