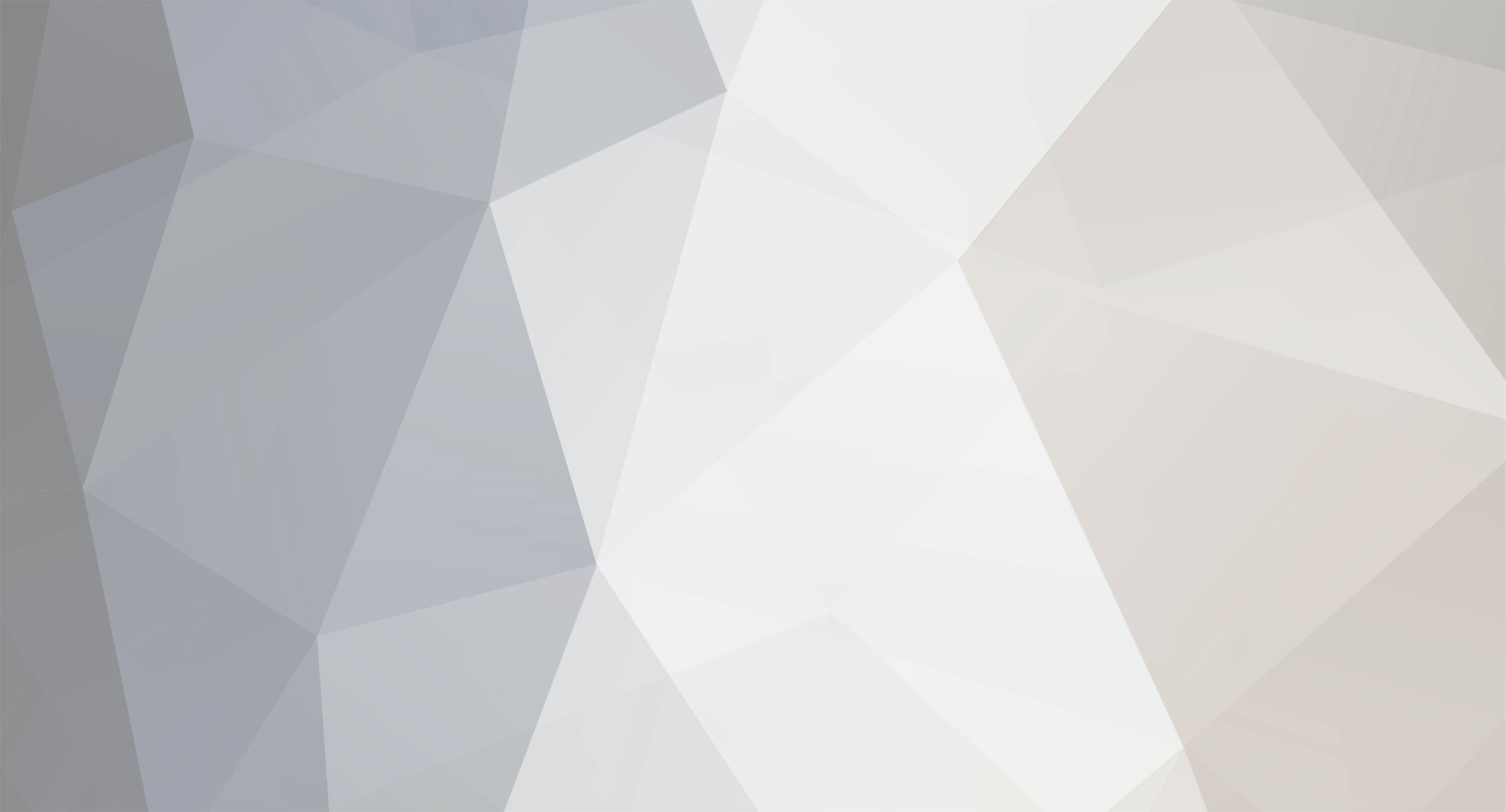
Pord67
Members-
Posts
24 -
Joined
-
Last visited
-
Days Won
1
Pord67 last won the day on July 5 2021
Pord67 had the most liked content!
Recent Profile Visitors
The recent visitors block is disabled and is not being shown to other users.
Pord67's Achievements

Member (3/5)
26
Reputation
-
Morning all Does anyone know how long Temporary Occupation permission lasts, both initially and with time extension(s)? TIA.
-
Thanks Mark. Yes, flat bottomed tank. Presumably still worth using rebar with a C20 mix?
-
Thanks for that Mark. Is a C40 mix overkill?
-
No, just me and a wheelbarrow. Getting the mixer up our track is unlikely anyway.
-
Thanks, appreciate the replies. The pad is sized to keep to the tank manufacturer's recommendations, ie 600mm wider than the tank diameter (2135mm) and 100mm thick for tanks up to 2500l or 150mm for tanks of 4000l plus. I've plumped for 120mm for our 3000l tank. They say their warranty is invalid if concrete isn't used, and presumably also if these dimensions aren't roughly adhered to. They don't specify the mix, I just assumed our tank to be similar to a septic tank in weight and size. Having said all that, I'd very happily grab any opportunity to reduce the size/cost/work involved. Our site is difficult to access up a potholed track and even then the mixer truck wouldn't get closer than about 30m to the pad location, which is why I've resigned myself to mixing myself.
-
Hi all I'm about to put in a concrete pad for an external water tank that will weigh 3 tons when full. This will be the biggest concrete job I've tackled and I'd appreciate your input please. The top soil has been dug away and the pad will sit on the surface of very heavy clay sub soil (currently also supporting the foundations of our self-build house). Dimensions of the pad are 2700mm square and 125mm thick. A C40 mix seems to be best for septic tanks so I'm assuming the same for this. I'll be mixing it myself, and I plan to add grid rebar. My questions are: 1. should I put down membrane and gravel layer first? If so, can I use a random mix of rocks and stones (we have plenty on site)? 2. there's currently a layer of soupy churned up clay on the surface, is it best to remove this first? 3. I've found variations online for a C40 mix, can anyone tell me the correct mix? 4. If necessary could I pour the slab in two sittings? TIA, any other suggestions welcome.
-
Bad idea not having overflow in kitchen sink?
Pord67 replied to Pord67's topic in Kitchen Units & Worktops
We're trying to keep costs down, hence looking for something used. Anyone know if the lack of overflow can/does impact on the rate of draining? -
Bad idea not having overflow in kitchen sink?
Pord67 replied to Pord67's topic in Kitchen Units & Worktops
Thanks, that's an option. It would be easier just getting a sink with an overflow, though. -
We're scouring the 'pre-loved' market for a ceramic double-bowl kitchen sink. Quite a few are appearing which have no overflow, including from manufacturers like Thomas Denby. Is this asking for potential trouble? I understand that as well as the obvious benefit the overflow can also help speed up draining.
-
Urgent - Any pro upvc window fitters here in central belt Scotland?
Pord67 replied to Pord67's topic in Windows & Glazing
Thanks Craig, done. -
Bit of an unorthodox request, but here goes. I'm looking for a professional upvc window and door fitter with experience of Compriband (and an open and adventurous attitude...!) We're currently self-building a strawbale house near Aberfoyle and have 3 sets of French doors and 4 windows to order and install. I need someone to - double-check dimensions - advise on pre-installation preparation - install at least one window and door so I can see in detail how it's done - generally act as 'consultant ', ie hold my hand... We've gone through the pre-order process with Colin's Sash Windows (Spectus units) and need to get the order placed and installed asap. Anyone willing and able?
-
Self build offgrid strawbale house in Scotland
Pord67 replied to Pord67's topic in Introduce Yourself
Strawman, we bought our scaffolding sheeting from Actavo Direct. For insulation in our suspended timber floor we used mainly offcuts of sheepskin to a depth of 300mm. It had already been washed and tanned (twice), and we added borax.- 48 replies
-
- 1
-
-
- straw bale
- offgrid
-
(and 2 more)
Tagged with:
-
Understanding building regs about stoves (Scotland)
Pord67 replied to ProDave's topic in Stoves, Fires & Fireplaces
Thanks for the replies folks, I've found the appropriate section in the Scottish regs. Because the vent is non-mecanical it's not clear whether it automatically needs a spillage test, but I think our fitter will carry out one anyway. -
Understanding building regs about stoves (Scotland)
Pord67 replied to ProDave's topic in Stoves, Fires & Fireplaces
Chaps, I'd appreciate a revival of this thread in relation to installation of the log burner in our strawbale build please. We had a site meeting yesterday with an installer for the living room log burner and he asked me to check regarding the location of the stove and kitchen vent in the same room. Apparently there are Scottish regs potentially involving costly tests around the movement of air in the room. Ours will be a Passivent stack system (ie non-mechanical) and he thought this might be a different situation from having a mechanical extractor, and therefore possibly exempt. I could of course ask the Building Inspector and in previous situations he tends to say that if it's been approved then it's ok. However I'd much prefer to avoid drawing attention to things, and our installer seems to want reassurance (possibly because he'll be responsible for signing off the installation?). Anyone have experience of this? -
Self build offgrid strawbale house in Scotland
Pord67 replied to Pord67's topic in Introduce Yourself
Thanks for the kind words Red. Yes, I'd love to do a blog but unfortunately it will have to wait until later.- 48 replies
-
- straw bale
- offgrid
-
(and 2 more)
Tagged with: