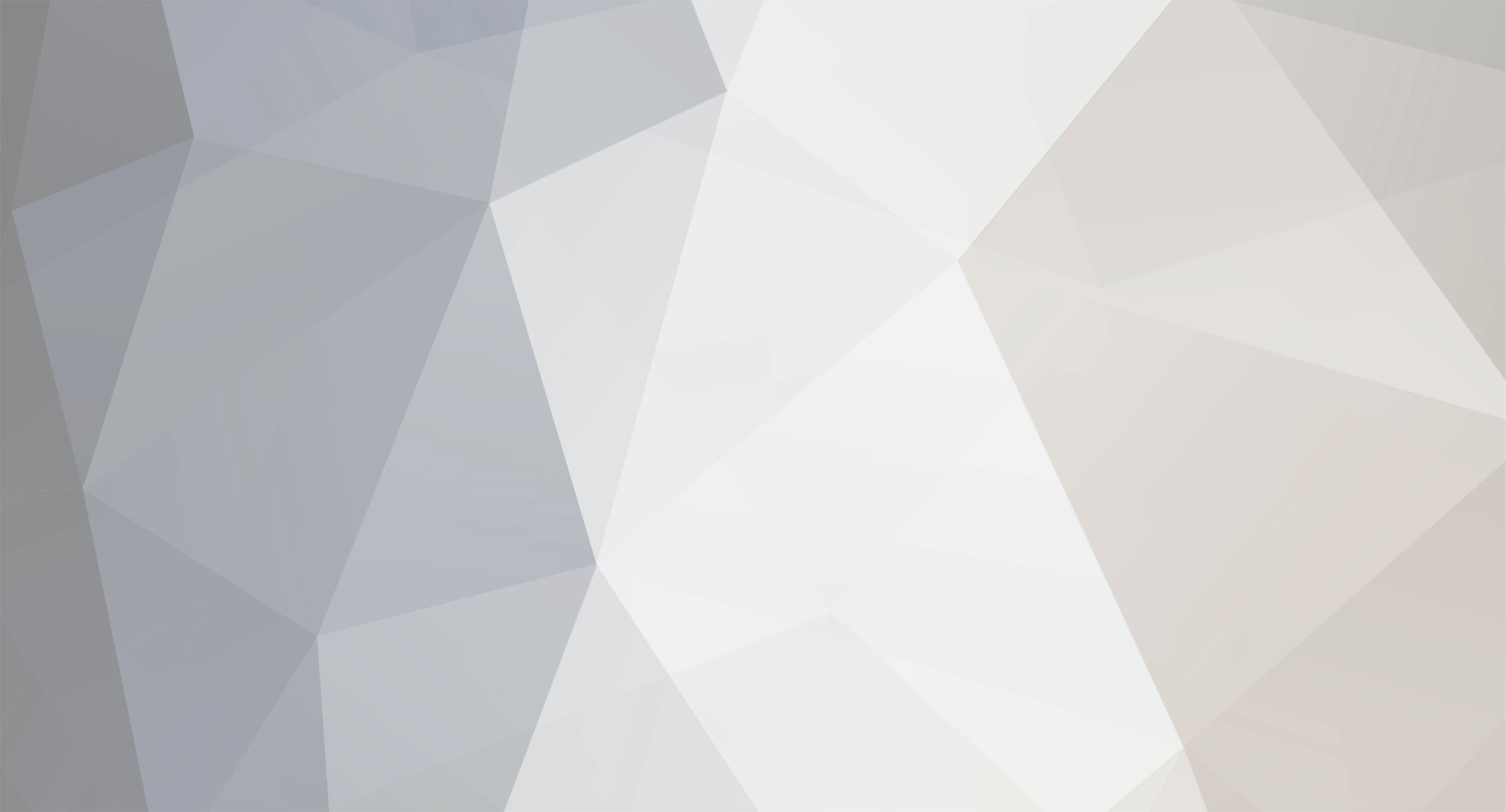
Annker
Members-
Posts
176 -
Joined
-
Last visited
-
Days Won
1
Annker last won the day on April 19 2024
Annker had the most liked content!
Recent Profile Visitors
Annker's Achievements

Regular Member (4/5)
39
Reputation
-
Posi joist - This install feels rubbish, thoughts?
Annker replied to boxrick's topic in Roofing, Tiling & Slating
Read a bit of this thread earlier in the week. Good to read you got that builder out the gate. Work at this stage can be rescued relatively easy. In this situation it's not essential that elements and connections look pretty, just need to be structurally sound and perform. In contrast bad work done at fitout stage can be much harder to rectified, and may forever look like a dog dinner You caught it in time, and have every opportunity to deliver a fine looking project now. -
Leveling old ceiling with GypCeiling MF
Annker replied to Annker's topic in General Construction Issues
Say with MF5 tophat section the primary support channel goes in a maximum 1200mm c/c. Can I ask what is the maximum c/c of support that GL1 requires, and therefore spacing of the GL6 support bracket? My plan is to install the GL1 perpendicular to the existing joist, and therefore put a GL6 bracket on every 4th joist which works out a little less than 1200mm c/c -
Leveling old ceiling with GypCeiling MF
Annker replied to Annker's topic in General Construction Issues
I found the BG spec sheet for the system. GL6 is the bracket. It's exactly the system I want. Simple, fast solution and easy to get right👍 Just to add for future reference BG only list the GL6 which has long leg, other manufacturer & suppliers offer a GL5 with a shorter leg which is a better option when looking to keep tight to existing timber joist. -
Leveling old ceiling with GypCeiling MF
Annker replied to Annker's topic in General Construction Issues
I actually think the 30mm is borderline ok. The only place I believe it could show up is any margins around joinery fitted in the alcove. And as the alcove are ~ 1/3 of the width of the room the ceiling in each of them will only be running ~10mm off. Can't see any issue for the plaster finish either, the ceiling is a flat plane. I don't care to remember how many concrete soffit/ceilings I battened out in the past. We did a lot of apartment blocks that way. 2x2 battens fixed to the soffit with express nails and then counter battened again with 2x2(without nail guns). Dusty, noisy, over head work. I hated it. -
Leveling old ceiling with GypCeiling MF
Annker replied to Annker's topic in General Construction Issues
Thanks Nod, I wasn't aware of that system. I'll have a look around their website, sounds like it could be a very good option. -
Leveling old ceiling with GypCeiling MF
Annker replied to Annker's topic in General Construction Issues
Just to add in another question for opinions. In one room the 1st floor joists are running 30mm off level front to back. There is no subsidence and it seems they were just installed this way; they aren't bowed down too much and otherwise the ceiling is flat. The ceiling is about 3m high and 30mm fall is along a 4.7m long run. I wonder if such a fall would be noticeable and should I go to the effort of level out this ceiling? 30mm is a decent amount to have installed a joist off level but I'm not certain this will be noticeable in the finished ceiling. (I may level the floor above though). -
Leveling old ceiling with GypCeiling MF
Annker replied to Annker's topic in General Construction Issues
I've sometimes used that method in the past but it is considerable more work and harder to achieve a level finish (I'm a carpenter so experienced at this sort of work) The other alternative is sister along the joists with 3x2, possibly could get away with using 2x1/12. This would be a little less expensive material wise (vs MF system) but more labour. I have 2x row of solid bridging therefore x3 sistering pieces per joist. Less work than counter battening below the joists but still more work than MF system options. -
Bit of a niche question. On my renovation project I have stripped back all lath and plaster ceilings to bare joists, in preparation for new plasterboard and skim. The underside of the existing joists are up and down, and in some areas two rooms have be knocking through to form one bigger room. Therefore I need to level the underside of the joists for the new continuous ceilings. I've previously installed MF ceiling in new build project however unsure of how to go about it in a renovation job. My plan to maintain ceiling height, is to screw the MF7 primary support parallel directly to the existing joists. Essentially the MF7 will be within the joist void and therefore the ceiling height will only be lowered be the thickness of MF5 top hat section. Is anyone familiar will the system and know if this an accepted arrangement?
-
Looks like a good solution but as I've only about a dozen pockets to do it's probably too expensive an option.
-
Yes the "Tony tray", I had it well researched but must have been rushing and its inclusion was forgotten. By top plate I'm referring to the horizontal top plate of the studded wall. Basically just end the VCL along the ceiling line, don't fit it in around the joists and tape it along the top plate of the studded wall. The option to have the VCL cut in around the joist will be a bit of a faff alright, however if its required I will do it.
-
Appreciate any ideas on the following issue to overcome. When constructing my stick build TF extension I mistakenly left out a strip of VCL that I believe is now (at fit out stage) needed to link together with the VCL proper. The design for the VCL was either going to be the PIR foil layer taped as required, or the addition of a sheet VCL. My designed TF build up is broadly as section below: I'm at the stage now of measuring up insulation and looking back at an old thread I see I missed installing a strip of VCL around the joist ends as per image below: So now I am wondering how best to detail/install the wall VCL at the ceiling/floor joist to wall junction as its now built Do squares of VCL need to be cut in around each individual joist void pocket and taped to the joists or can the VCL be simply taped along the continuous top plate? Similarly, at 1st floor ceiling/roof level I'm unsure how the wall VCL should be terminated. I have a VCL installed externally above the osb, so again I will not be now able to link it to the internal wall VCL.
-
Fine tuning my IWI Solid wall (Warm Batten) design
Annker replied to Annker's topic in Heat Insulation
Understood, that makes sense to me. -
Fine tuning my IWI Solid wall (Warm Batten) design
Annker replied to Annker's topic in Heat Insulation
Sounds good, thanks it's very useful to hear others experience in the absence of your own. I think I will still opt for insulation within the studwork for a couple of rooms. Namely two rooms that have bay windows. Here it would be preferable to keep the depth of buildup to a minimum around the bays otherwise the proportions of the individual wall panels start to look off. Here I may keep the studwork 10mm-15mm away from the brickwork and pack a little insulation behind the stud. -
Fine tuning my IWI Solid wall (Warm Batten) design
Annker replied to Annker's topic in Heat Insulation
My concern is that I have some large area walls, 3m high ceiling and almost 5m long. In such large areas do you think flexi batts would maintain their installed position long term? I have actually just ordered a bag of mushroom head insulation fixings, I was going to experiment with these to see if they may help keep either rockwool or flexi wood fibre boards in place. -
Fine tuning my IWI Solid wall (Warm Batten) design
Annker replied to Annker's topic in Heat Insulation
Not choosing rigid specifically over flexi on a material basis; rather that the rigid boards can be bonded to the brickwork in continuously layer as opposed to flexi batts that need to be fitted between studs and therefore the insulation layer missing at every 400mm c/c stud. Although perhaps the lower u-value of the timber stud vs insulation discounted?