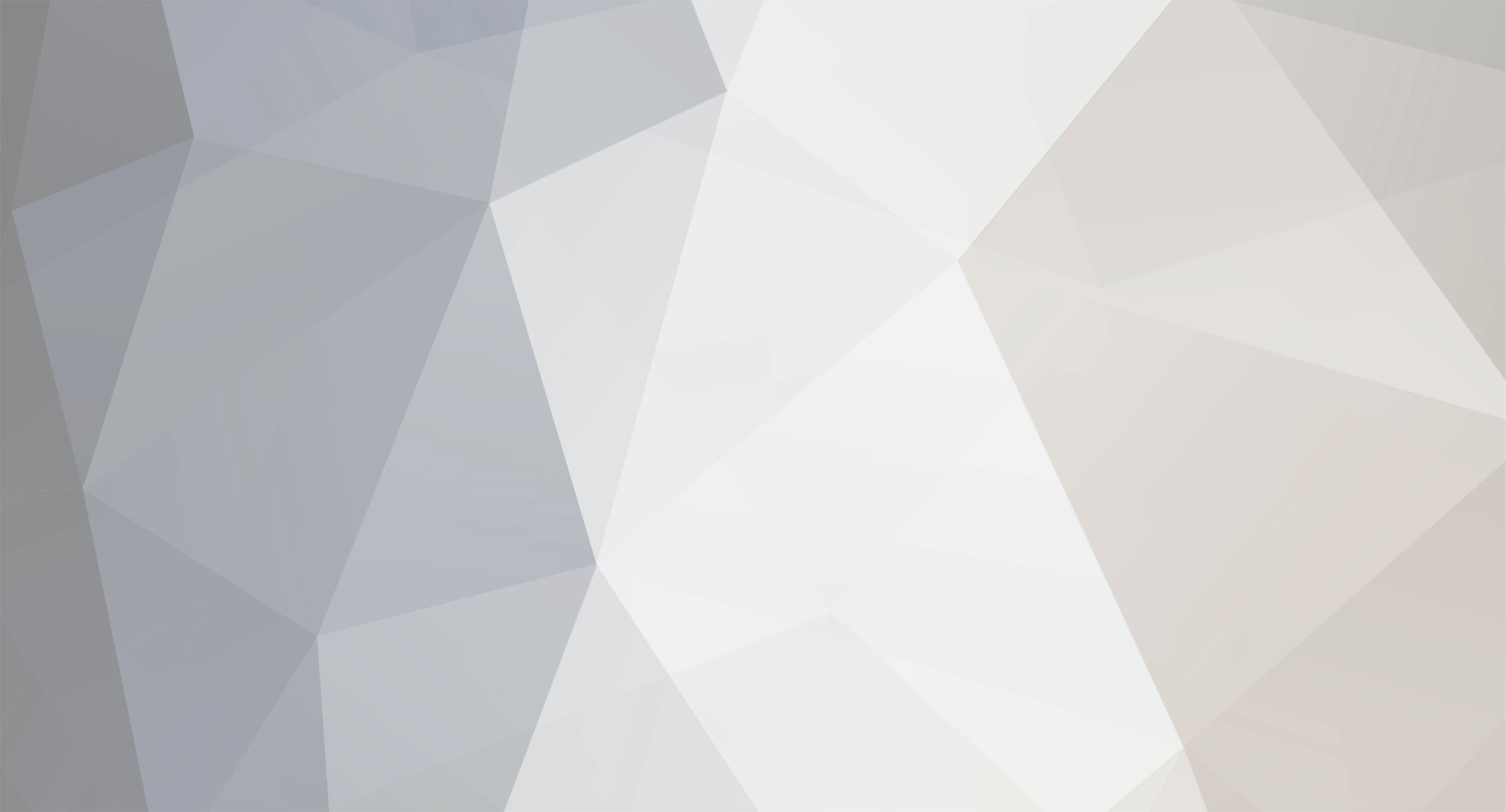
Spinny
Members-
Posts
381 -
Joined
-
Last visited
Personal Information
-
Location
UK
Recent Profile Visitors
The recent visitors block is disabled and is not being shown to other users.
Spinny's Achievements

Regular Member (4/5)
41
Reputation
-
They will be building over a lateral drain as they are building at the boundary. A lateral drain is considered part of the public sewer system and is the responsibility of the water company. According to the water company standard criteria, if you are building within 0.5m of a public sewer you will need a build over agreement. Whether they are aware of this, or the fact they cannot build over a gas pipe remains to be seen. When should a building notice be served ?
-
Thanks @kandgmitchell. Yes we can say it is 'their problem' however it has ramifications for us and for all future owners of both properties. IMO if you cannot afford to do the job properly then you shouldn't do it at all. We all know how these things work. Down the line if there is a drain problem they will be coming down our driveway to rod it, not taking up the nice floor they have laid over the top of their manhole. And if the drain blocks they will be laughing their heads off saying 'there is nothing we can do from our side' as 'stuff' emerges from our ground drains.
-
New extension DPC Tray Flat / Sagging - What to do?
Spinny replied to boxrick's topic in Brick & Block
I am no builder, but as I understand it the principle is that any water which might enter the wall cavity would move down the wall cavity under gravity. It would then encounter the 'cavity tray' with a slope towards the outer leaf, so that it could then find its way out via weep holes in the outer leaf. I think the reality is that this is a second order mechanism because you should not have water in the cavity in the first place. Obviously moisture could enter through the outer leaf, through the top of the wall if the roof/parapet/gutter leak, or I guess through some condensation process. But under normal circumstances this shouldn't occur. However when building things with long lives the non-normal needs to be considered. Others will be able to advise more, but I wonder have the works been seen by a building control person as I think DPC level is a normal inspection point ? I'd also like to say you have my sincere sympathies for your situation because I have been through the same process of having to terminate a builder's contract and I know how difficult and stressful things become and know you will find some good and very experienced people here. -
@mjc55 That is the same as what I said in different words. As the neighbours will be building over a lateral drain which is the responsibility of the sewer company, they will require agreement to do that from the sewer company in the form of a lateral build over agreement. Whether the sewer company will accept the neighbour's (IMO daft as a brush) wish to build over their only drain access and rodding point will be up to the sewer company. Any building regs will also apply, but it is still somewhat unclear to me whether they do apply in any way to private drains ?
-
@JuddlyFire No I don't believe it does imply that. My reading of it is that where a drain serves more than one property then it is a public sewer and it the responsibility of the sewer company. So this means the red extends to and includes the first chamber only. Nothing beyond that is used by more than one property. However the pipework between the neighbours private chamber and my public chamber is also the responsibility of the sewer company but only where it runs on my property. That is the section on my property is buff coloured and is a lateral drain. Therefore I believe the neighbour requires a lateral build over agreement from the sewer company. Presumably it will be up to the sewer company whether they will grant this when the neighbour plans to build over their chamber restricting the sewer company's ability to rod the lateral drain they own from the upstream side ?
-
It can and may well affect us in multiple ways. 1/ The chamber on our land has blocked several times in the past. Difficult to definitevely assign cause between the properties but has sometimes appeared to be caused by products used by the previous neighbour. 2/ When that shared chamber becomes blocked it causes backup down our drains because our property is about 1 meter lower than the neighbours. Anything from the neighbours drain that cannot then exit the chamber will back flow down our drains and in extremis emerge through our surface drains. 3/ Once built over, whatever the theory that they will lift a hatch in their floor, unseal their underfloor drain cover (releasing smells into their property), send a rodder under the floor to clean/inspect then reseal etc seems unlikely in practice. So any future drain issue on their property is likely to generate requests to service their drains from our property as they will have no ready access from their own chamber. 4/ They have no construction plans and have declined to answer any polite questions about the rainwater drainage arrangements which appear to include taking water from the main roof and extension and using downpipes at the boundary with no apparent drainage routes. 5/ Should they build without adhering to the regs, it may not just impact the saleability of their own property, but given the connection and being lower lying - our own property too once searches and questionnaires show the existence of the shared/public drain on our land. No building notice is registered yet despite work being imminent. Few, polite and straightforward questions were all rejected at the party wall stage - a truly ridiculous game of chinese whispers and obstruction. Odd, dishonest, and deceiving behaviour throughout. I accept it is 'up to them' to adhere (or not) to regs but given the circumstances remain extremely concerned.
-
Anyone know the answer here ? Do building regulations not apply to drains on private properties (i.e.most/many houses) because they don't appear on 'sewer maps' ?
-
Also note that none of these drains are shown on the 'sewer map' held by the local sewer company. Their map only shows the main sewer and does not show any of the chambers and pipework that connect all the properties to the main sewer. When I last spoke to the sewer company they said my chamber and the pipe to the boundary were indeed public sewers even though not shown on their map. Furthermore they said they did not need to be added to their map as all public sewers were their responsibility anyway. (Not sure now whether this might just be the sewer company avoiding extending their map ?) This seems like a huge hole in the building regulations...? (Is this really meant to mean you can do as you please with a drain/sewer not shown on a map - which presumably means millions around the country ?)
-
The neighbour's drain does not 'serve' my property, rather the neighbour's drain exits the inspection chamber at the side of his property then crosses the boundary and feeds into the inspection chamber on my property. My drain also feeds into the inspection chamber on my property. The inspection chamber on my property is then connected onwards to flow into the main sewer serving the houses on my side of the street. So unless there is some special meaning to the word serve, it would seem the inspection chamber on my property and the pipe that crosses the boundary onto my land to connect to it 'serves' his property. Therefore it seems he can build over it ? He says he will retain access to it via a hatch in the floor above it. Am I missing something ?
-
Please can anyone advise on building over a domestic drainage access/inspection chamber ? Is this permitted by building regulations ? (My neighbour has advised he plans to build an extension over the access/inspection chamber for his drain and install a floor hatch for access. (Sub floor void likely to be 60-75cm). This drain then crosses the boundary to join our drain and therefore as I understand it becomes a public drain at that point.)
-
I think with all things it can help to keep your eye on what is being done as it is occurring. Always difficult as few of us appreciate having people 'standing over us' while we do something. Even then it is easy to forget or miss things, but so much easier to adjust or correct work in progress than to get it corrected afterwards. I have probably become too obsessed with trying to work details out before the work takes place - and even then things can go awry - it sends you a bit loopy in the end. I would go around and check all the doors and windows at this stage - are they plumb, positioned ok in the aperture, matching heights around the rooms, compatible with your planned finished floor levels inside and out, will open properly and with relevant clearances. And then think long and hard about any issues you find because now is the time to get it corrected even if that means having to pay for the change/correction. I had to get one window cill changed because it blocked the opening of an adjacent window. (I have one door that opens against a wall and wanted it to open 90deg with clearance for the handle. Looks like it is going to be really tight now once plastered and may not open 90. Had I spotted it at the time I could have got the fitters to put it tight up against one side of the opening to give a few mm more clearance. Also had to buy and use a water level to prove that the fitters laser level was wrong and their measurements at fit were in disagreement with their measurements at survey. (Water levels actually rather useful for checking levels between inside and outside of buildings and around corners etc.) PS I think doors and windows are normally sized to be about 6mm all round smaller than the opening.
-
From memory - Approaching 3 years ago I paid around 12k + VAT for around 50sqm flat roof - VCL layer like you, 150mm PIR, different brand of single ply membrane - adhered like you rather than mechanically fixed. It was new build so nothing to strip off. Dressed to 3 rooflights plus 1 aperture, main house wall and with 3 rainwater outlets and, with membrane applied to line an internal gutter around the perimeter, 5 external corners, 2 internal corners. 15 year guarantee, membrane life in excess of 30 years. Down south. Add inflation, strip off/repair work, and factoring smaller area = higher cost rate then similar ball park I guess ?
-
You either played pro basketball, or you are employing persons of small stature to work on your site. ;0}
-
I have often found door hinge screws can work loose over time and you notice when the door starts catching on the frame. Then you tighten them up but they work loose again until the hole gets mashed up and it becomes a running battle. Is there an answer to this ? - Using 3 hinges ? - using longer screws ? - using special screws ? - using ball bearing hinges ?
-
You don't say how big the patio is ? You could perhaps put a slot drain somewhere within the length of the patio and then have a fall each way into this drain. For example a slot drain in the middle of the patio would produce an overall fall of zero.