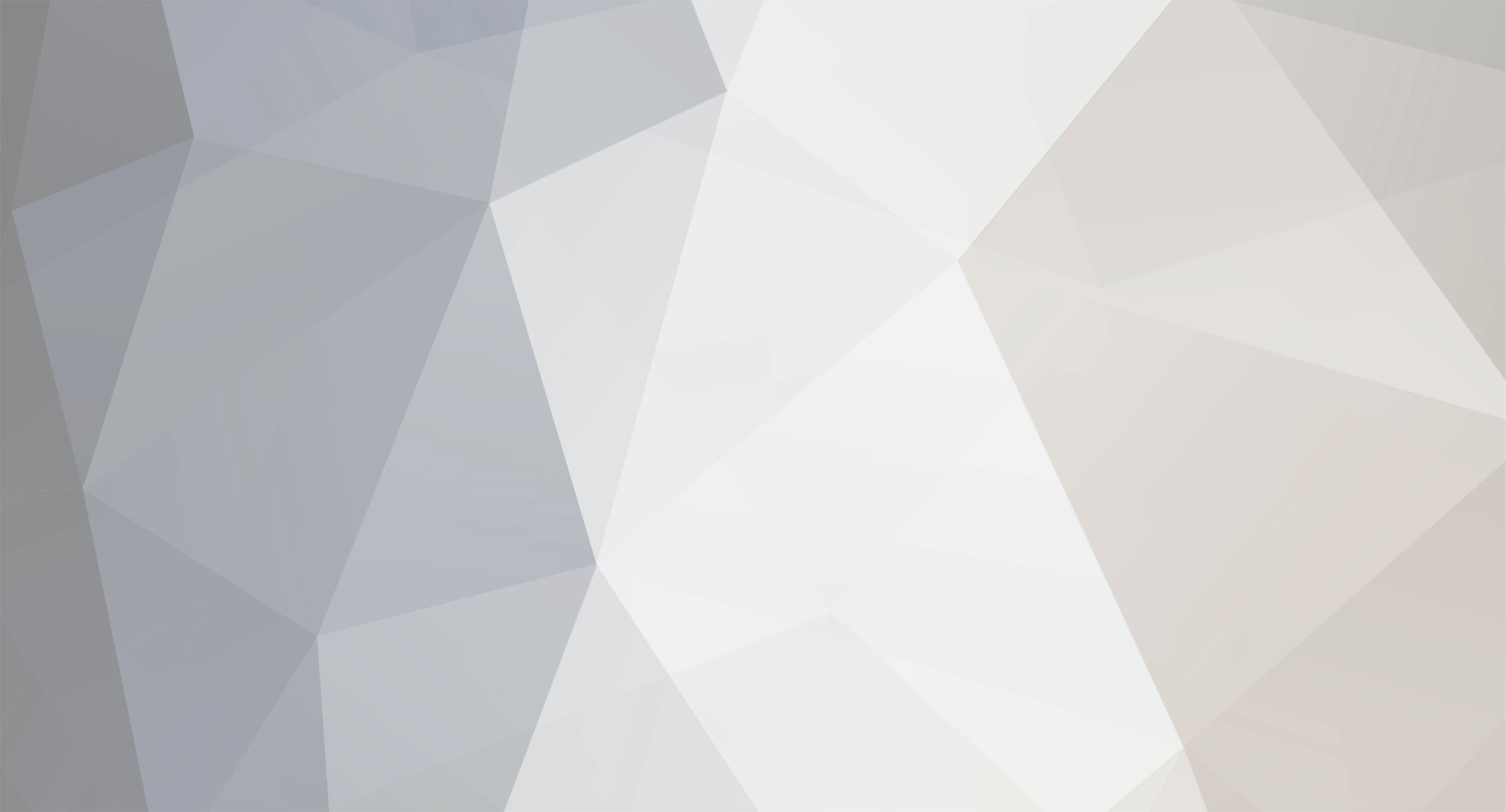
lookseehear
Members-
Posts
125 -
Joined
-
Last visited
Everything posted by lookseehear
-
Recommended manufacturers or Installers in the South West?
lookseehear replied to Lears's topic in Windows & Glazing
Have you been to the National Self Build & Renovation Centre in Swindon? You can see many of these brands windows side by side there which might help with making a decision. -
Fine tuning my IWI Solid wall (Warm Batten) design
lookseehear replied to Annker's topic in Heat Insulation
how was it with the sand mix vs sharp sand? -
@JohnMo thanks for all your input here, I really appreciate you taking the time. How big are the rads? If we’re going to have them in bedrooms I’d probably go for columns to save wall space. Is it feasible to run rads and ufh both from an ASHP in an open loop configuration? I assume the ufh would need to be mixed down to a lower temp. I’m also assuming that bedroom temperatures can still be controlled with TRVs on the radiators? From recommendations in my previous thread I want to keep things simple controls wise. One issue I can see is that we will get quite a lot of solar gain upstairs from roof lights, sliding doors being one open plan space which will have exposure throughout the day, whereas we won’t get a lot downstairs due to smaller windows and smaller spaces which only get sunlight at certain times of day. On a cold winter day with lots of sun, heating load upstairs will be reduced, but downstairs won’t be impacted as much, so any reduction in flow temperature overall could result in cold bedrooms.
-
This was my line of thinking too, but on the ground floor will also be a home office and kids bedrooms which will likely be occupied a lot more as they get into their teens, and hence will need to be able to be heated to 20-21 degrees to be comfortable. Here’s my new plan: Keep the boiler, because I don’t feel that I can economically run radiators off an ASHP Put in a thermal store (size?) and have radiators downstairs and ufh upstairs use some of the savings from not getting ASHP to relocate the oil tank or put in a smaller one Put in as much insulation in the floor downstairs as I can fit consider a separate air con unit for the living space upstairs. Even poorly insulated as it is, downstairs rarely overheats even in heat waves, so I don’t see any requirement for cooling downstairs electric UFH mats in bathrooms on timers/switches for comfort Does this seem sensible? I need to understand the thermal store bit a bit more though.
-
I understand the theory, but I assume that only works with ASHP rather than with oil boiler and thermal store because of how much more efficient UFH would run at constant low flow temps. If I’m using oil to run UFH via a thermal store it’s no more efficient than running radiators, so the ‘no insulation’ scenario means burning a lot more oil.
-
Ok this is definitely helping. The reason I was moving away from the idea of a thermal store is because of some comments on here suggesting that you get roughly half the amount of hot water storage in one compared to an UVC of the same size. That point aside I like the idea of using cheap electricity or solar PV to heat thermal store to contribute to either space heating or DHW. We have a 200l UVC currently and don’t use all that much of it, but the kids are still young and we are going to end up with four bath/shower rooms. Do I therefore need to be looking at 400l thermal stores? separately, if I’m thinking of UFH and can’t put much insulation in the refurb areas, should I be thinking about the no insulation option or would putting 25-40mm PIR be better. Assume for now that comfort is more important than heating costs.
-
You may have read my previous thread: I really need to make my mind up and I'm still struggling. As a refresher: We have an 18-25kW external condensing oil boiler and 1200L oil tank in the garden The house is 5 beds and detached and we're putting the living space on the first floor and bedrooms on the ground floor We're replumbing and rewiring the whole house Two extensions will be insulated to modern standards, as will the new roof The older parts of the house are harder to insulate substantially, but we will be putting in a thin layer of carefully installed and well detailed internal wall insulation and significantly improving the airtightness We're replacing all windows and doors with triple glazing/modern equivalents I'd estimate we would be averaging 50-70W/m2 peak heating requirement when all done but it's hard to tell because at this point we're chipping away at the project bit by bit Option 1: Stick with oil, new radiators everywhere (oversized) Pros Cheapest at the outset Easy to control room by room temp with TRVs Reduced oil usage compared to high flow temps and small rads Cons We commit to keeping burning oil No weather compensation The boiler is (I believe) oversized for what we need, so would need to make changes (buffer tank/TS?) to the installation or swap out for a smaller boiler We have to fit large radiators in each room Option 2: ASHP and radiators Pros Renewable factor and compatible with solar PV/battery Means we can remove the big, unsightly oil tank from the garden Can utilise the BUS to get the grant from the government Option of FCUs for cooling Cons Risk of high running costs due to high flow temperatures required running rads off an ASHP We have to fit large radiators in each room Less controllable room temperatures due to the time it takes to warm up a room using low flow temperatures, and counter-productive nature of using TRVs to throttle flow in an 'open loop' system Option 3: ASHP and UFH Pros Renewable factor and compatible with solar PV/battery Means we can remove the big, unsightly oil tank from the garden Can utilise the BUS to get the grant from the government No need to find space for radiators 'comfort factor' of having warmer floors than using radiators Likely lower running costs than Option 2 due to lower flow temps meaning higher SCOP Option of FCUs for cooling Cons Least controllable of all the options Requirement to find the headroom for some insulation (or not based on this thread) Most disruptive to install Likely most expensive up-front Most risks of getting a poor quality install (maybe?) A few other thoughts on UFH and the complexity of the specification Heat output is obviously restricted by some floor finishes, and we'd likely have carpet in bedrooms, but I think it can be mitigated if the pipes are within a chemical screed, heating is run continuously and small pipe spacing. I had thought an overlay system would work, but I realise that overlay systems just can't get the same heat output Some rooms downstairs will be occupied just at bedtimes and will be fine at 18-19 degrees, but our kids bedrooms will likely be occupied a lot more as they get into their teenage years, so those rooms will probably need to be 20-21 degrees. The above is just a brain dump really, but I'm really tearing my hair out trying to work out what the right option is, when we'll need to live with it for the next 20+ years. Any thoughts? How can I bring some clarity to the decision?
-
I'm particularly interested in this because we're moving our living space upstairs, so we're thinking about having UFH on both floors. In my head, there's zero (or negligible) heat loss when it's for the upstairs because all heat is within the envelope of the house (ie heat 'lost' downwards is still heating the house fabric).
-
His argument that UFH + ASHP work really well for uninsulated floors makes a lot of sense to me, and I imagine it would get more efficient through winter as the heat warms the ground gradually, but it's counter to what is often written on here that UFH doesn't work without at least 150mm insulation.
-
Vertical crack in extension through padstone under new steel
lookseehear replied to lookseehear's topic in Brick & Block
Nope, foundations were poured continuously for the whole length of this wall and the outer skin is unaffected which would indicate the foundations are probably fine. I think you're right - I'm not convinced the bearing is even on the padstone. We've sorted this out now - we chopped out the padstone plus one more block and poured in place a new reinforced padstone. The SE was happy with this solution. They are dense blocks which obviously does make it a bit more concerning, but the way I look at it it's now no different than having a little expansion joint. -
ASHP in uninsulated home?
lookseehear replied to PennineDave's topic in Air Source Heat Pumps (ASHP)
We looked at putting in a 'lightly used' oil boiler (2 years old) because a friend was getting rid of theirs in favour of an ASHP. None of the installers we spoke to (three in total) would install a second hand boiler due to (in their words) risks that it might be defective or have been removed incorrectly/without care. Our three quotes for a replacement oil boiler and a new unvented cylinder, as well as putting TRVs on 10 existing radiators was around £7k in total from all three installers, with the actual boiler and cylinder being around £2.5k of that (external Worcester Bosch model). Most of the cost was therefore in the installation and going second hand wouldn't have saved us all that much. -
Vertical crack in extension through padstone under new steel
lookseehear replied to lookseehear's topic in Brick & Block
The wall is about 8m with no expansion joint, so could be that maybe, but seems a bit odd that the crack goes directly through the padstone rather than around it or elsewhere. SE said to check foundation (couldn't see any issues) and replace the padstone but nothing else required if it's just a hairline crack and doesn't get any wider. We've decided to cast in a padstone instead and have put in some reinforcement too for good measure. The new padstone is also more evenly spaced under the steel so fingers crossed there's no more movement. -
Hi all, pretty crappy discovery this week of a very small crack running directly through a concrete padstone under a new steel beam picking up the one side of our new extension, running through mortar joints and blocks down to the slab (or as far as I can see). It's a concrete block sized padstone built into the inner skin of the wall built from dense concrete blocks. There's no crack evident on the outer skin and the foundation is probably 800mm thick there due to having to excavate all the soggy clay, so I don't think there's any issue with the foundation at this point. See link below for a video - apologies if it doesn't show it very well. The roof has been built to SE spec, and has been designed to potentially hold a 2.5t hot-tub on top. The bizarre thing is there's barely any load on there at the moment - just the steel beams themselves plus joists and plywood. Any ideas why this could have happened and likely remedial works required? I'm hopeful it will be just supporting the beam and chopping out and replacing the padstone.
-
Lime only mortar? (i.e. no cement)
lookseehear replied to Gibdog's topic in Bricklaying, Blockwork & Mortar
You also need to remember that there are different types of lime mortar. I'm not sure how familiar you are but broadly you have two types Natural Hydraulic Lime (NHL, available in 2, 3.5 and 5 in increasing strength and reducing free lime content) Non-hydraulic lime (also technically 'NHL' by name but no-one refers to it as that) also called air-lime or you might see 'lime putty' This can be in the form of quicklime which needs to be slaked, or as hydrated lime ('bagged lime' at the builders merchants) which has already been partially hydrated I don't actually know how low carbon the different lime mortars are, but my understanding is that they all require burning either pure limestone or some mix of limestone and other stones in a kiln at very high temperatures, and that energy has to come from somewhere, which could be burning coal I guess. I just asked ChatGPT about this and got the below summary. The issue here is that non-hydraulic lime sets very slowly and isn't very strong. It's the best thing for old buildings with solid walls and no DPC, so while there's carbon to be saved, it might not be something you can get sign off from a structural perspective. -
Flat roof VCL lapping against existing building
lookseehear replied to lookseehear's topic in Flat Roofs
Thanks for this, although it looks like your roof is a cold/hybrid given ventilation above it? I assume that doesn't matter in terms of the VCL, and that it probably needs to be chased in somehow. -
My VCL is going in on top of my plywood sub-deck, which butts up to the existing stone-faced external wall of the house. Where does the VCL go at the house side? The stone is uneven, so I don't think I'd get a good bond if I tried to adhere it to the external face of the house.
-
If you search for a 'Tony tray' you'll see that a lot of people have wrapped the ends of the joists in 600mm+ DPC, which can be taped to OSB and into the parge coat on the walls.
-
Frameless Glass Balasturade and Building Control
lookseehear replied to murat's topic in Windows & Glazing
We are putting a frameless glass balustrade around our roof terrace for our extension, but I'm also struggling on speccing what it should fix into. I spoke to Q railing who manufacture the profiles that the glass fits into, and they said that I need to speak to an SE to make sure whatever it fixes into can take a 0.74kN/m load at 1100mm, but wouldn't help beyond that. I spoke to the SE who has been designing the steelwork for our renovation/extension and he didn't want to touch it, saying that I need to go back to the manufacturer. I feel like the simplest answer is a reinforced concrete ringbeam sat on top of the outer blockwork, but I'm at a bit of a loss as to who can tell me whether or not this is compliant, or whether BCO will know that it's overspecified and sign it off. Maybe I need to find a new SE for this bit in particular? Any suggestions? -
You're specifying a warm roof, so no ventilated void, therefore the quoted post doesn't apply (unless I've missed something).
-
Builder needs to repair this hole which he still has the stones from (pic below). He wants to use a 'standard' mortar mix and is concerned mainly with it being structurally sound. It's worth noting we'll be taking some stone out below and adjacent to this to create a doorway, and that there'll be a block wall from the new extension butting up against this corner. He knows I would prefer lime where the old walls are concerned but that's more relating to pointing and plaster than the repair work. Any thoughts?
-
Just wanted to send a message to say you seem surprisingly chipper given the absolute sh*t show in evidence here. So many people would just accept this as 'what it is', so kudos to you to get sorting it! I hope you retained a significant chunk of the ££ against the builder.
-
That sounds interesting but I'm also not that keen on the idea of having to replace something after a few years to keep it watertight. I've come to the conclusion that the easiest option might be to cast a 200x100 ring beam on top of the outer skin as a mini parapet, which means I can fix posts or the balustrade channel (if we go frameless) into the concrete. I would cast drainage channels through the ringbeam at intervals and have single ply membrane run right through these into collector boxes, which avoids having the posts/channel in the drainage pathway. I did a sketch somewhere that I can dig out if you're interested.