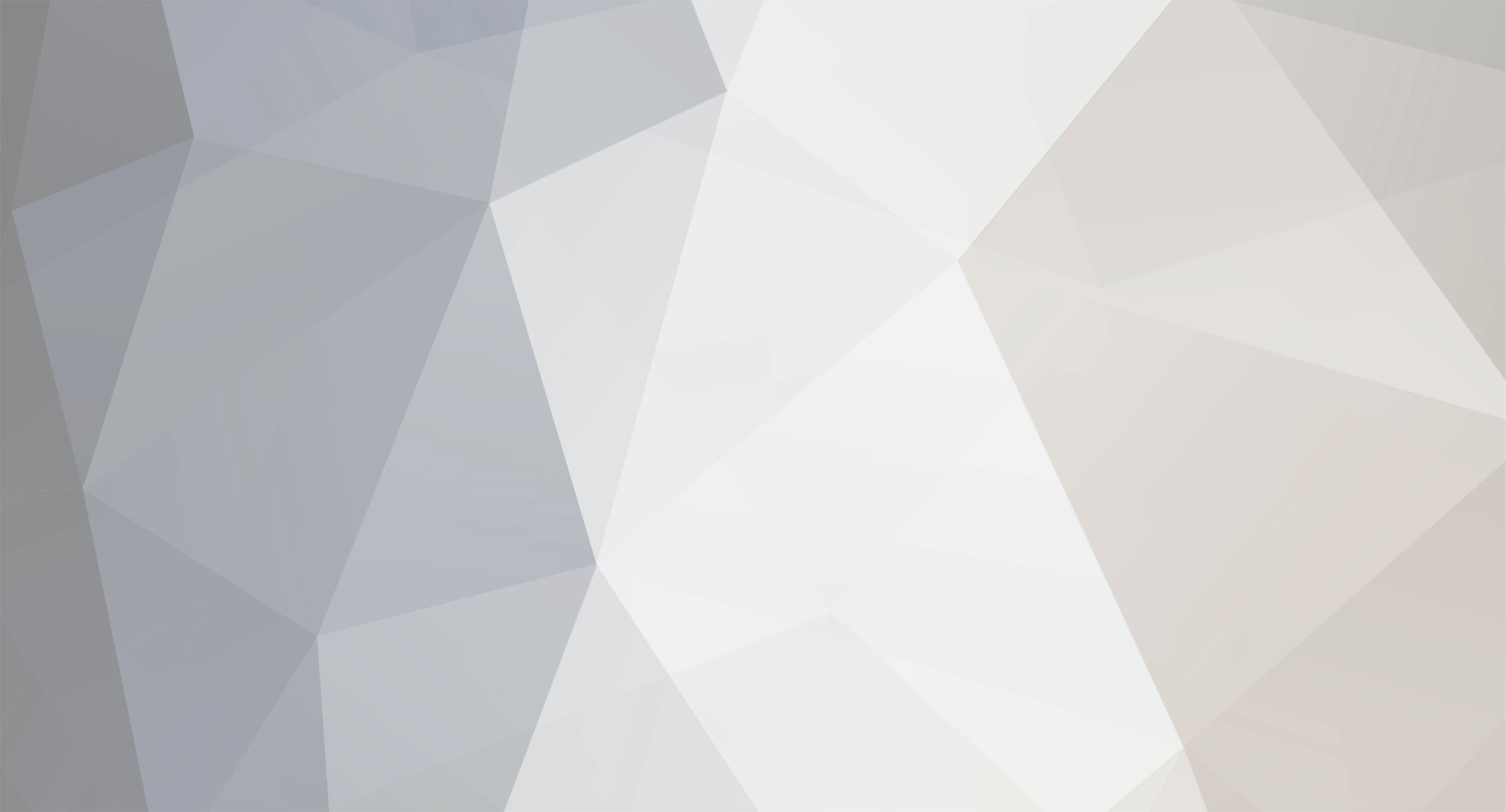
mistake_not
Members-
Posts
56 -
Joined
-
Last visited
Everything posted by mistake_not
-
Fine tuning my IWI Solid wall (Warm Batten) design
mistake_not replied to Annker's topic in Heat Insulation
Before I have just used contact matt as a mist coat, but realised with some modern paints to need to use the right base coat / primer as some folks have had issues with contact matt as a base coat and paints peeling. -
Fine tuning my IWI Solid wall (Warm Batten) design
mistake_not replied to Annker's topic in Heat Insulation
Slight tangent. What paint are you / folks finishing IWI like this with? I'm looking at using something breathable which rules out the normal vinyl Matt etc I think. -
Anyone got a WUFI Pro licence?
mistake_not replied to Drellingore's topic in General Self Build & DIY Discussion
If you do this run it in a VM. Cracks / keygens are a great place for "added value" -
Recharging R290 portable air con units
mistake_not replied to mistake_not's topic in General Plumbing
Then hopefully heat pump / fan coils next year 😄 -
Recharging R290 portable air con units
mistake_not replied to mistake_not's topic in General Plumbing
It's slowly lost effectiveness over the last 3 years, so if I can bodge this summer I'll be happy! -
Any body done it? Our portable air con unit that is only used a handful of times has been getting progressively less effective, and on turning it on tonight it is now ineffective. There seems to be inexpensive kits / gas you can buy, but interested if anybody has successfully recharged one with R290 propane.
-
@SpinnyDid you resolve this? Excuse my stupidity but was the actual door system ok and just had install? Or system flawed. Reason for asking as we are planning on an eclipse door system, but now may change our mind...
-
How to tell is textured ceiling is asbestos laden
mistake_not replied to Moonshine's topic in Plastering & Rendering
But - our house is 1980 and we were sure the only asbestos was the artrex -
How to tell is textured ceiling is asbestos laden
mistake_not replied to Moonshine's topic in Plastering & Rendering
We had it in our ground floor. Did a quick test by using a kit from https://www.asbestos-sampling.com/?srsltid=AfmBOoqDhxnHe7r9cDAYl9R1ZU-pZXzvw4H_uEjrNZ7Wa6WZeCDXLN47 whilst in full suit / face Welly. Came back as lowest grade. Was removed under non licenced notifiable work in a 2 day period across the entire ground floor a few weeks ago (which was empty at the time). Didn't need negative pressure etc, but lost of sheeting etc. Got air testing after (not a requirement for this work) but wanted for peace of mind. -
Not a solution but read this thread of the consequences and remedial action: I suppose options are: 1. Rip down bricks, replace the PIR with cavity bats / pump in eps. 2. Pump in eps from the outside 3. Pump in a closed cell foam. 4. Give up, do IWI / EWI and an airtightness barrier. 2 is probably easiest and cheapest. Depends on if you have enough residual cavity for the beads to properly flow.
-
In my renovation I have ripped off the window sill around my bay window and exposed the cavity underneath. It's had some failing glass foam insulation in it, so have emptied it all out. For context the wall is a traditional brick and block build, with the window sat on the outer brick leaf. I will seal to the window with insulation and air tightness, but am unsure what to re-fill the cavity with The cavity varies in size between 60 and 35mm, would seem obvious to use EPS beads. I thought maybe use an old bin to mix the beads and PVA and then out them in? Anyone got any experience or better ideas? It's only 1m high, and about 2m along.
-
Not yet- but working on it as part of renovation/ extension. Aim to be when I'm done. Mvhr going in as part of the same work.
-
Been searching and thinking and can't think of / find / work out how do air tightness well for my extension other than taping everything in sight like @plockhart is. The extension is going to be a warm flat roof attached to an existing cavity wall, with a new full fill cavity wall. Airtightness on new walls achieved with parge coat and old walls with wet plaster. Roof buildup so far is: - plasterboard - joists - OSB - VCL - Insulation - EPDM Can see how I can easily join the VCL to either wall, and therefore am I better just omitting it, and ensuring the OSB is vigorously taped to all joists / itself / the walls, or doing something different? I don't like the idea of the VCL below the OSB, as the OSB is then effectively sandwiched between 2 airtight layers and has a moisture risk. Grateful for wisdom / pointing me to the answer elsewhere.
-
I was pleased with the collingwood ones we had in our last place: https://www.collingwoodlighting.com/product-category/indoor/downlights/
-
Kingspan Kooltherm K103 Floor K108 Cavity wall 0.019 W/mK
mistake_not replied to Caroline's topic in Heat Insulation
Dodgy ubakus calc below. No idea what the aerated concrete blocks are I selected, and I changed the lambda value of the PIR to 0.019 to match k108. Note kingspans calculator suggests this as a way to hit u values, but no details on actual materials except the K108. @Caroline I'm assuming the celotex you were quoted is still a PIR board, so even though it's a bit cheaper, you still have a load of issues. As you say slightly bigger cavity. I.e. If you have a cavity of at least 130mm and do EPS or mineral wool batts you will save loads and have decent insulation. -
Kingspan Kooltherm K103 Floor K108 Cavity wall 0.019 W/mK
mistake_not replied to Caroline's topic in Heat Insulation
It does with super light blocks. You can technically hit 0.18 I value.... Sounds like a rubbish idea though hence I changed my spec. -
Kingspan Kooltherm K103 Floor K108 Cavity wall 0.019 W/mK
mistake_not replied to Caroline's topic in Heat Insulation
Yeah my builder specced the same. If you do a full fill cavity batt at 125mm you get basically the same u vale on paper: https://www.insulationsuperstore.co.uk/product/knauf-dritherm-32-125mm-cavity-wall-slab---2184m2.html * Note you might need to do something stupid like 130mm to pass building regs. Or just widen to 150mm. Side benefit, even at 150mm it's much cheaper than k108. At least half price. The same is true for EPS. Only issue I can see with EPS is the cosmetic element of holes. Not an issue if you are rendering though. Also see my discussion and calcs on it here: https://forum.buildhub.org.uk/topic/43093-cavity-insulation-and-air-tightness/ -
Ref airgap size: No idea. I'm a DIY builder and planning a warm roof. Just know an airgap is required. Aerogel: lambda value ranges from 0.015 to 0.023. So not much different to PIR. Another option is Vacuum insulation panels (aka VIP). They are a lambda value of 0.007 I think, made to measure and approx £200 a square meter. Would mean you stay between joists. Check out kingspan OPTIM-R. Re Q3. Not sure. Maybe. Re q4, it would be ok on 400centres. Much better than just taped (wet skim coat)
-
Mineral wool / EPS would increase your insulation depth required by 1/3. I.e. a total of 185mm. I think you are stuck with a cold roof buildup, so will need a ventilation gap no matter what.
-
Quick play using PIR if you just fill between rafters gives u value of 0.399. To hit the required Building Regs U value you need another 65mm of PIR. This assumes PIR of 0.023 R value. As I'm sure others will comment, it's great on paper, but really hard to do well unfortunately.
-
IWI options on extension and rennovation
mistake_not replied to mistake_not's topic in Heat Insulation
Here's my Ubaqus calcs, including a batten (wrongly sized) for metal. Metal first Then wood. Sizes based around 40*63 CLS. Also annoyingly discovered my existing cavity is 50mm, not 100mm, and the existing insulation in there isn't in great shape. -
IWI options on extension and rennovation
mistake_not replied to mistake_not's topic in Heat Insulation
For awareness: Done some quick u-value calcs. Using metal studs looks to be worse than wood studs due to thermal bridging. 0.2 vs 0.19 -
Silencers for mvhr
mistake_not replied to mistake_not's topic in Mechanical Ventilation with Heat Recovery (MVHR)
Awesome thanks for the detailed reply. Yeah was skeptical, hence the question. I got BPC to do a design, and they specced the semi flexible ones, didn't like the idea, so sought wisdom here. Thanks for validating my thoughts! Yes have oversized unit: it's capable of 375m3, but my max requirements from BR are approx 170, so hopefully running quiet. I'll probably try and get the 900mm version of these in then: https://www.blauberg.co.uk/blauberg-attenuating-silencer-duct-mounted