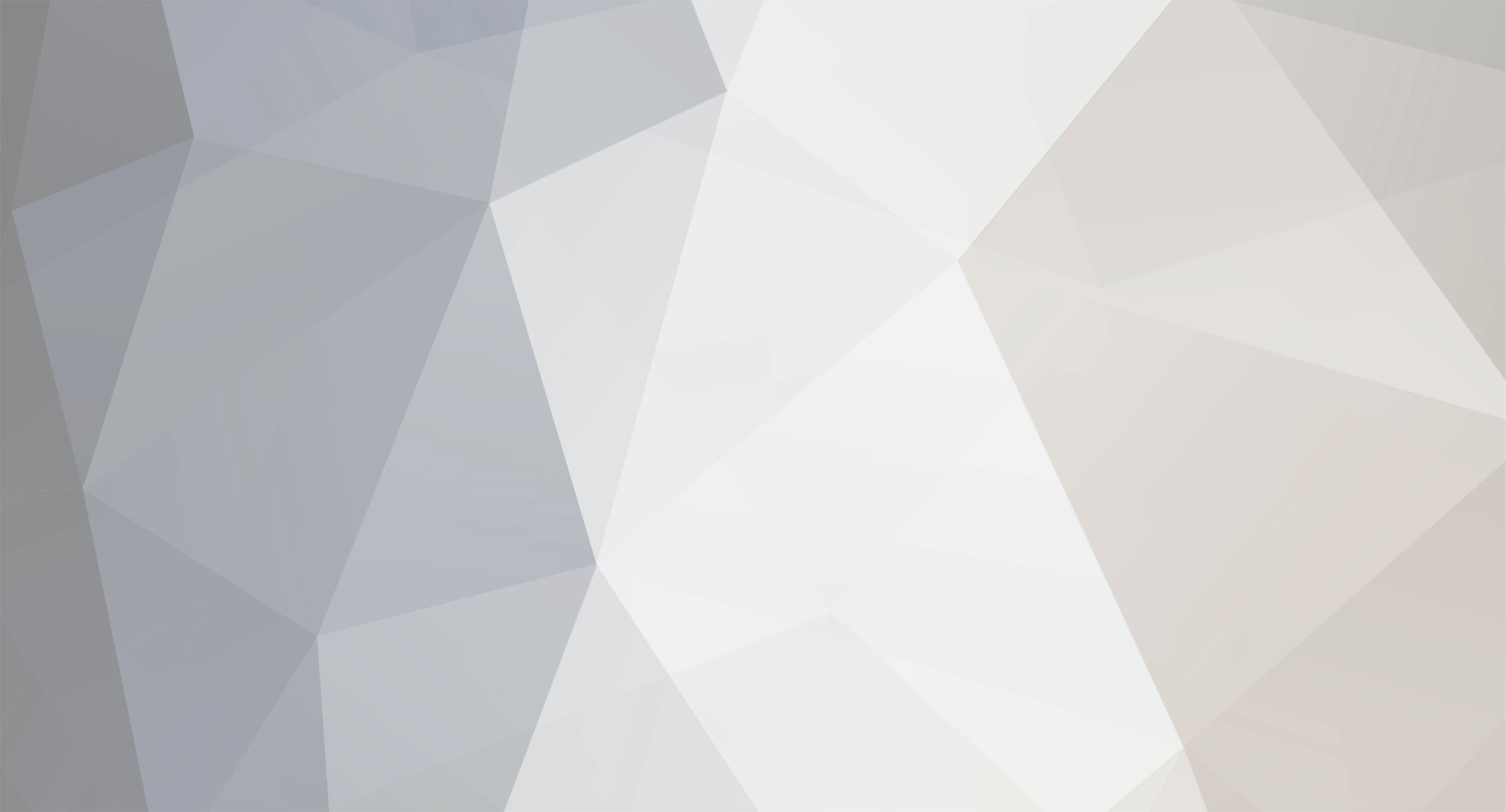
torre
Members-
Posts
222 -
Joined
-
Last visited
Personal Information
-
Location
West Midlands
Recent Profile Visitors
The recent visitors block is disabled and is not being shown to other users.
torre's Achievements

Regular Member (4/5)
93
Reputation
-
Architect and builders... where to start?
torre replied to Jack757's topic in New House & Self Build Design
Personally I prefer to choose architect and builder separately, on their own merits, so I'd treat this as a recommendation much as you would from someone else; consider them but don't feel you need to give them the initial brief in hope of securing the builder. I didn't quite understand this - do you mean the builder wants to charge you and they'd be engaging the architect? I definitely wouldn't consider that, I'd want to be engaging any architect directly at any stage. One of the challenging aspects of a self build is that yours is a one-time deal, whether for the architect, builder, or suppliers. Most will want to maintain their long term relationships with each other and the closer they regularly work together, the more that may mean they lean towards each other rather than to you when things crop up, big or small, that need a solution further down the line. -
Dot and dab versus 2 coat plaster on block walls
torre replied to Caroline's topic in Plastering & Rendering
I think the only advantage is for the developers, who can get away without the cost of installing MVHR -
Buying a hoist was probably the best £100 we spent and it sounds even better value now!
-
Converting Section of Front Garden to additional driveway/ parking.
torre replied to Charlotte22's topic in Driveways
I agree with @Redbeard this is likely to be amenity land you own but it's use is restricted, so clearing a large area and parking a car there may not be allowed. Could you remove a much smaller part of the hedge and park parallel with your existing drive& garage? They way you only pass over rather than park on that land. It does lose more garden but it's less likely anyone will kick up a fuss -
Impact on listed buildings - *any* harm is reason to refuse planning?
torre replied to Stu789's topic in Planning Permission
Helps preserve the listed building by financing necessary repairs, creates local employment are a couple. Did the planning officer give any indication of the public benefits they considering when weighing up? Does your council have an up to date local plan? If not that should tilt the balance further in your favour. It's good if you can already offer some mitigation for the points raised and your list of benefits already sounds good. It'll be harder for a planning officer to justify refusal of a full application then at the pre-app stage and I'd expect a planning consultant could get you over the line with this one. (We had to overcome less than substantial harm in a conservation area rather than re a listed building) -
What's your plan if family circumstances change and they need money back? If you may need a mortgage in future you'll need to budget for some sort of warranty, also if you end up needing to sell. Your house looks well suited to being built on a budget but you need to plan for worst cases and have contingency. What are ground conditions like and service access? So much money can go just getting out of the ground. It's an exciting plan and I want to sound cautionary not negative but if you risk running out of money an unfinished, unwarranted house may not be worth much more than the land it's sitting on.
-
Roller shutter door fitted just forward of the opening with the roller in your soffit space might be an option. The rear wall construction will be for stability of what's otherwise a tall half brick wall
-
victorian style skirting boards wanted
torre replied to lord mud of the flyes's topic in General Joinery
Search for "decorative mouldings" for example these -
Best practice - engineering bricks and standard facing bricks
torre replied to Lincolnshire Ian's topic in Brick & Block
We've used facing below DPC, but you have to check their frost resistance rating. You're looking for an F2 rating. -
Interesting idea but don't you need around 3600 cut lengths of pipe that size? If it's not available cut then I can't see it's worthwhile cutting pipes yourself. The compressive strength may well be questioned by BC. Maybe this would work better with pipes the length of your soakaway all laid the same way creating a stable honeycomb shape like you'll see when pipes are stored in a builders yard? (Around 100 pipes of 3.6m length) Either way you'll still need the whole thing wrapped in a membrane.
-
Why not fit 25mm insulation between the cross battens? Avoids any deformation and improves the insulation level.
-
T&G chipboard flooring fixing over ply diaphragm
torre replied to Rick734's topic in Floor Structures
Another alternative might be to fix the diaphragm to the underside of the joists, but you'd have to check with your SE.