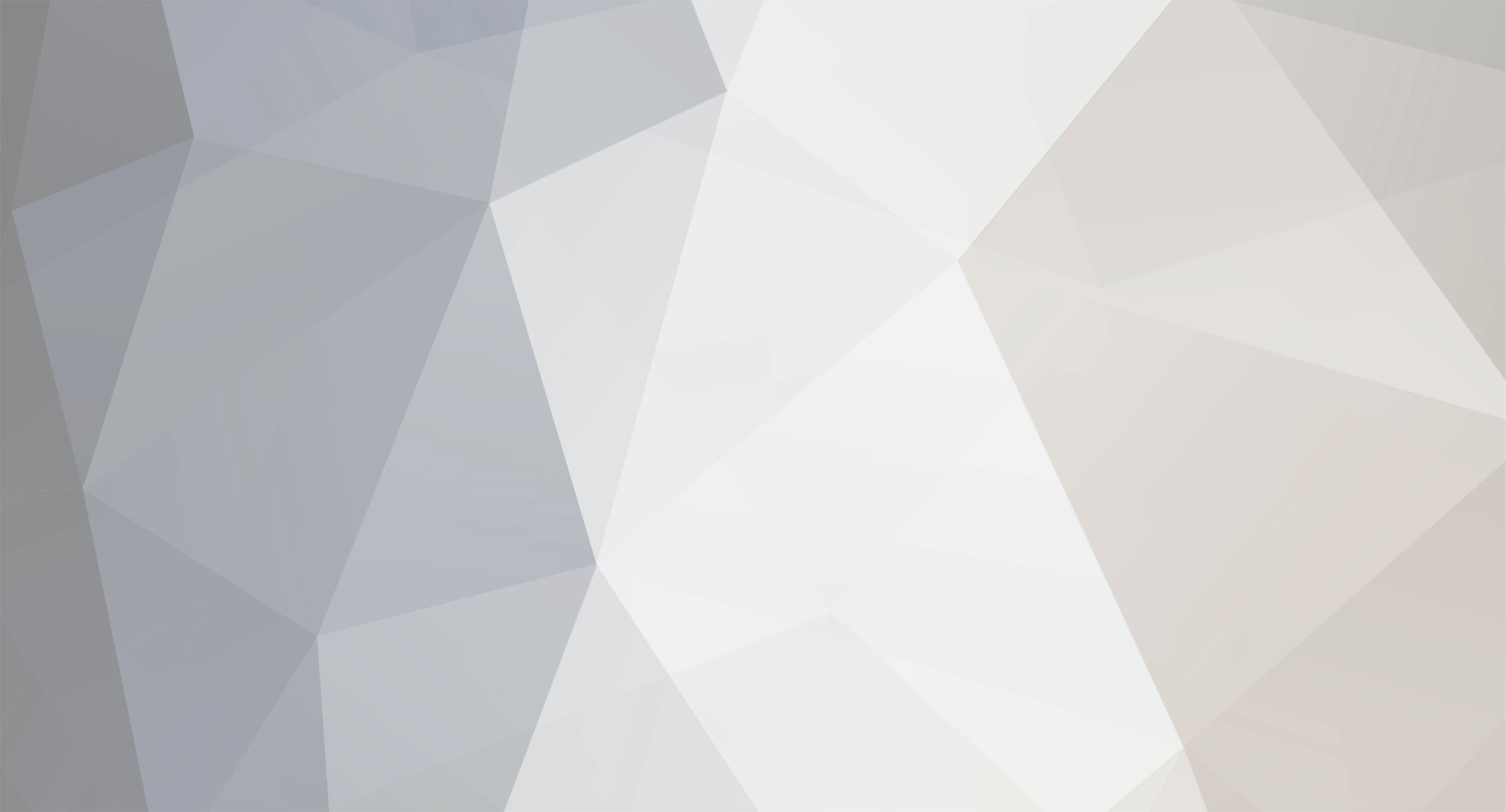
tuftythesquirrel
Members-
Posts
88 -
Joined
-
Last visited
About tuftythesquirrel
- Birthday 01/15/1957
Personal Information
-
Location
Narberth, Pembrokeshire
Recent Profile Visitors
tuftythesquirrel's Achievements

Member (3/5)
32
Reputation
-
Agree with @Nickfromwales and decided on a 75mm radial setup. I have a friend that has installed other (series) types, as a living, but said they are a PITA, when you find that the friggin big attenuator on the design, won't fit between the joists etc. I think you would have less acoustic issues with this type of install. I got my kit from Blauberg and designed and fitted it myself. At the time (about 2 years ago) some companies would give you a basic design but things seemed to have tightened up a bit since then. None of the companies wanted to supply/extract from hallways, cloakrooms and plant room etc. so I added this as I thought it was worthwhile. In the end I couldn't see the value of paying for their design, if they weren't going to follow my requirements. I read the Blauberg manual did more research and came up with a set of design rules: Place intake on north side of building. Keep AHU away from bedrooms. Do not place valves above showers (Outside shower area) Place the Kitchen Extract Valve near the sink, not above the cooker. Kitchen, Bathroom, En-Suite and Utility Valves require a double duct run. If the duct run is greater than 15m, double the ducting. If the duct run is greater than 20m, triple the ducting. If the room is greater than 20m2, the valve requires a double duct run. Do not exceed runs of 30m. Keep the AHU flow rate as low as practicable. I did a spreadsheet with the building regulations ventilation supply and extract rates plus the additional rooms I wanted and worked back to make sure the total wasn't more than 50-60% of the AHU's capacity. The general consensus on the forum seemed to be is that you can run at a lot less than BR supply rates in practice. @Jeremy Harris has kindly put a commissioning procedure on the forum (what a guy!).
-
Can the DNO cutout be located inside?
tuftythesquirrel replied to WisteriaMews's topic in Consumer Units, RCDs, MCBOs
@Nickfromwales Sorry about that, once I started I just sort of got hooked! Ended up doing the rest of the plant room and the open plan kitchen/diner (industrial coffee shop vibe, I am told). Fairly sure it’s back in stock now 👍 -
Can the DNO cutout be located inside?
tuftythesquirrel replied to WisteriaMews's topic in Consumer Units, RCDs, MCBOs
I bought a Brother PT-D600 on eBay for £80 and use the free P-Touch Editor on my PC. I get the heatshrink tapes on the NineLeaf store on Aliexpress, much cheaper than in the UK. The 25mm black on white ones are less than £5 and look reasonably professional. -
Can the DNO cutout be located inside?
tuftythesquirrel replied to WisteriaMews's topic in Consumer Units, RCDs, MCBOs
👍👏 Been thinking about pipes myself, ok I'm in 😁 -
Can the DNO cutout be located inside?
tuftythesquirrel replied to WisteriaMews's topic in Consumer Units, RCDs, MCBOs
Lets face it, the standard meter box is cr*p. A couple of years and the door hinges break, the door falls off and you can't replace it without smashing the old one to bits to get it off. Then you have to cut the back off the new one to fit it around the cut out. Even more problematic if it's recessed🤐. We have the cut out and meter in plant room, in an electrical enclosure, on Unistrut. I have an 3 phase old school RCAMY meter, due to be replaced with a (smaller) SMETS2 one. Will change the meter tails and put cable idents on when the new meter gets fitted. Am I the only one that labels every cable🤔 -
Rigid PIR boards in cavity Walls. DON'T DO IT.
tuftythesquirrel replied to Iceverge's topic in Heat Insulation
Hi, Give me a hands-on self-builder, with OCD any day 😜 -
Swapping existing supply to new build
tuftythesquirrel replied to Bancroft's topic in General Plumbing
Same here with Welsh Water. We converted a church hall and there was some very old 1950’s ½” copper pipe coming from the main road over our property. I removed it all and replaced it with 32mm MDPE right back to where our property meets the road. Never laid a hand on their stopcock, just threw it in the skip. We need a fire suppression system (Welsh Building Regs.) so required around 100 L/min flow rate and the remainder of the ½” pipe was restricting our flow. I used the fact that we now didn’t have a stop cock to our property and asked them to provide one. They agreed and dug the road up to install the stopcock and replace the ½” copper with 25mm MDPE without a problem. Weren’t interested in inspecting it, even though it was correctly installed. Our flow rate went from 60 L/min to over 100 L/min as a result. In doing so, saved the cost of a new supply. Since they have put the water rates up this year by 27%, not losing too much sleep over it. I think it was because they have so many departments. If you speak to the developers section the official line is they need to inspect it, but the maintenance guys don’t care. -
Hi, I've read Approved Document F and can't see where any reference is made to "an expert" or a "competent person". Appendix C provides a checklist for the commissioning engineer but there doesn't seem to suggest a competent person is mandatory. I was going to self cert. A lot of people seem to be 'DIY'ing the flow settings using the Buildhub anemometer, which made me think about how do you fill in the "Date of last UKAS calibration" column in the checklist, when using this. Has it been calibrated?
-
Recommend a shower tray please
tuftythesquirrel replied to Post and beam's topic in Bathrooms, Ensuites & Wetrooms
Hopefully not straying too far from the main thread, the auction site John Pye usually have these. Similar style to the picture, stone resin, perfect condition, 1800x900mm, we paid £15 for ours 😁 -
Sticky Sunday fun
tuftythesquirrel replied to Pocster's topic in General Self Build & DIY Discussion
This stuff is very good.... https://www.wickes.co.uk/HG-Sticker-Remover---300ml/p/249616?gclsrc=aw.ds&&utm_source=google&utm_medium=cpc&utm_campaign=PMAX Shopping||Cleaning&gad_source=1&gclid=CjwKCAiA5Ka9BhB5EiwA1ZVtvL0anOSPITsSrlKRC3q1jYkwJaBTBGpg637GNCGWsg-lsRfP_FWcoRoCLZUQAvD_BwE -
Hi guys, Could any of you tell me what happens when the Loxone server fails? I've been looking at other forums where the recommendation was that the installer kept a spare one in the van!
-
We went through this process around 2020-2021 so allow for inflation. We had quotes from 5 different architects and architectural technicians. We didn’t intend for there to be so many, however, after the initial quote, when I tried to establish some of the finer details before we appointed them, like, ”exactly where is the airtight barrier?...” “”– the realisation that they didn’t really understand my point, made us think that it was going to be difficult to get above the “we just do building regs.” threshold, rather than getting as near to passive house as possible. The prices ranged from £3k to £30k. The house is around 400 square metres. Our build cost will probably work out to be around £1000-£1200 per square metre. I can’t personally get my head around the basic concept of charging a “percentage of build cost”. Why would the architects fee triple, if our build costs were say £3000 per square metre? Our groundsmen, bricklayer, plasterer, electrician and plumber all charge by the metre or day rate, so why should the architects fee be any different? It makes no sense! The prices didn’t include the structural engineer. One of the architects said they used a specific engineer who lived 80 miles away from us. Since he charged by the hour, any site visits (even a very short one) were effectively a day out due to the traveling at £700/day. The weren’t flexible enough to use a local guy, so we would end up paying for his driving time with not much to show for it. These sort of costs can add up over time. I think the biggest reason for the variety in price, is what stage the architect is at, in their career path and their business model. The highest price we got was from a “design practice” that were a bigger outfit, with maybe a dozen people working for them. They had a scale of charges for various disciplines e.g. draftsman £55/hr. to £85/hr. for a partner. I sort of got the vibe from the quote, that any variations that were necessary after the initial design would have been charged at the specified rate (ad infinitum!). A significant portion of the fee would have been swallowed up by the practice overheads and the drawings were still in 2D. In the end, we went with a young chap that I presume, hadn’t been qualified that long. He was fully fluent in Autocad Revit (3D) and totally got the passive house “thing”. He worked from home and his price was at the lower end of the spectrum and not a lot of difference compared to the architectural technicians. Minor changes along the way were provided as part of the package. However (and probably most importantly), he was great for bouncing ideas off, which is so important at the outset. I think you need to get ensure you get value for money!
-
SVP through insulated roof (passiv house)
tuftythesquirrel replied to junglejim's topic in Waste & Sewerage
Hi @junglejim, There is no need to do this. It's an old-fashioned approach, and the last thing you would want to do is stick a great big "thermal bridge/ cooling tube" through your insulation layer. I had the same issue and found Jeremy's post below. (Subject - Air admittance valve / soil vent pipe). He clearly explains the reasoning and how to implement it.He clearly explains the reasoning and how to implement it, using AAV's. https://forum.buildhub.org.uk/topic/4459-air-admittance-valve-soil-vent-pipe/ -
Gas Boiler Flow and Return Pipes In Copper?
tuftythesquirrel replied to tuftythesquirrel's topic in Boilers & Hot Water Tanks
The answer is 2m then. He has to certify. The only paperwork I believe I will get is the gas safety record, which relates to the boiler and flue installation rather than the pipework. The pipework manufactures documents say a minimum of 1 meter. That’s why I wanted to see it written in a regulation somehow, rather than someone’s opinion. Unfortunately, on that quote he proposed a 40kW boiler and I’ve fitted an 11kW, since the house heat loss is only 4kW, hence I wasn’t completely convinced by his competency. Connection to boiler yes copper, I would do all the main connections on the cylinder in copper also. In an ideal world I would but you haven’t seen my pipe run😁, so I will probably stay with plastic. Are you doing proper Viessmann install. With priority demand hot water and weather compensation? So without mixers or additional pumps? Yes, PDHW and WC, but not a standard install. It’s a 100-W system boiler and I’m using the Viessmann Plusbus EM-EA1 interface to control the burner and implement the WC using an Idratek automation system via a 0-10V signal. When I bought the manifolds and they came with mixers and pumps and I wasn’t convinced I didn’t need them. However, now I’ve accumulated a bit more knowledge and experience, I suspect they might be removed in the future. If you haven't bought your cylinder, get a heat pump one, with a 3m² coil. Your flow temp will drop and your recovery really quick. Yes, good point, I have. Thanks.