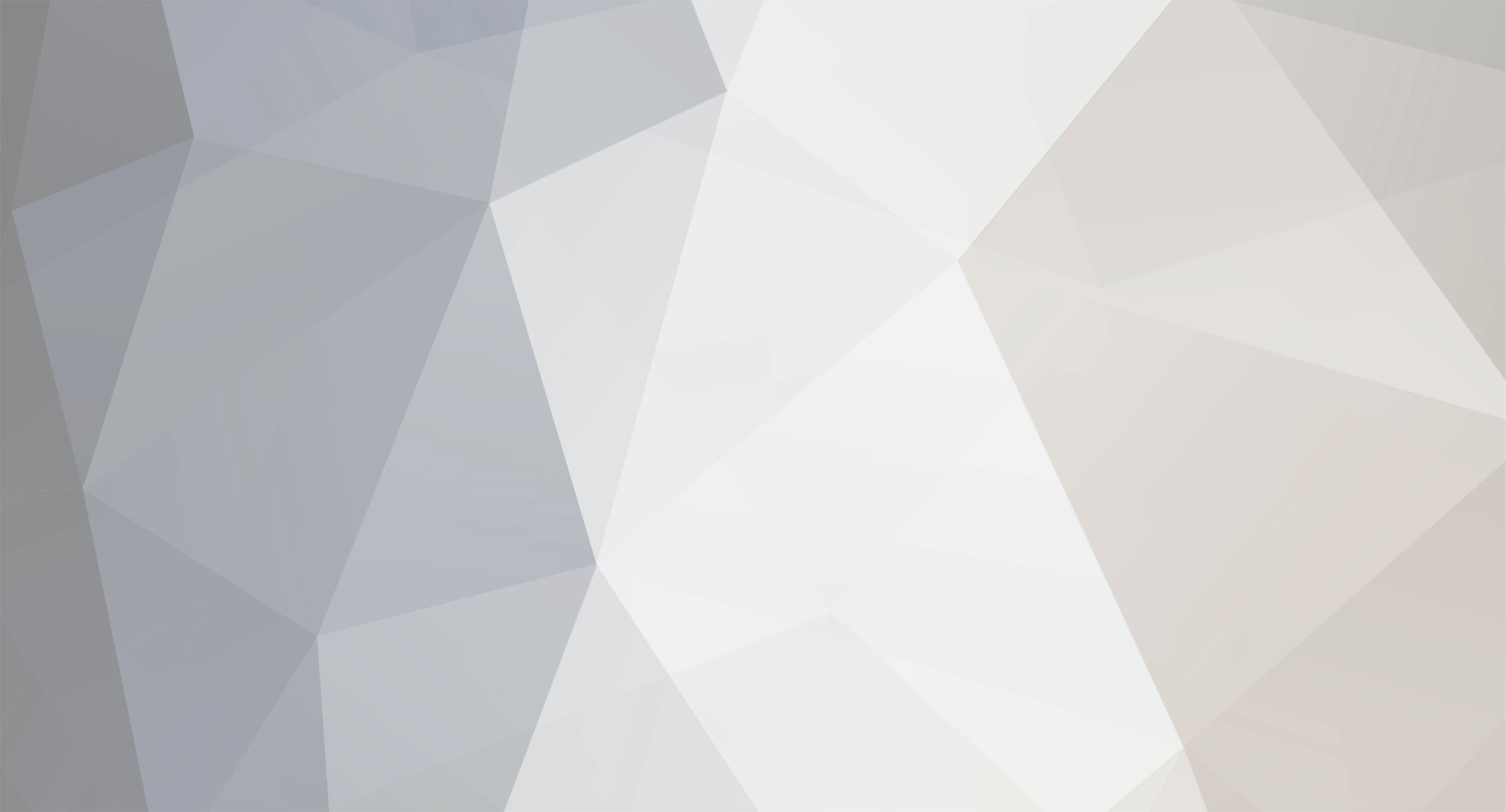
mjsx
Members-
Posts
25 -
Joined
-
Last visited
Personal Information
-
Location
N16
Recent Profile Visitors
The recent visitors block is disabled and is not being shown to other users.
mjsx's Achievements

Member (3/5)
1
Reputation
-
Oh, you mean there was a pattern you needed to recreate jigsaw puzzle-style?! Ok that is madness!
-
Plumber put together a thing … and I have concerns
mjsx replied to mjsx's topic in Boilers & Hot Water Tanks
An update to this tale. In summary, a gas safe engineer came out around 10 days after I reported a concern, spent a few hours at the property and found several problems. He wrote a 10 page report (boiler was classified as “At Risk” but not “Immediately Dangerous”), which was passed on to the plumber (I didn’t have to do anything), who was given around 3 weeks to fix all defects. There was no followup inspection. Overall I was satisfied though I am very surprised that the PRV discharge into a condensate pump is to spec. A few observations: 1. I wasn’t around when the inspector came around, but apparently there was quite a bit of checking manuals and so forth to see if the installation follows the manufacturer’s specifications. 2. The main things that ended up being changed/fixed: area around air brick where flue exits was sealed and tidied (including adding a “cage”); plastic PRV pipe replaced with copper and tundish added (though still discharges into condensate pump); insulation added to all pipe work; thermostat connected; benchmark commissioning checklist completed and local authority notified. 3. Some of the complaints are quite picky (inspector admitted this verbally), for example flagging a filling loop that was left connected, and an old uncapped gas pipe. 4. The report had multiple complaints about the flue—termination at both ends not to spec, and also insufficiently supported. Plumber did fix a few things, but assured me that the support was actually fine (it looks like two sections but is actually just one internally or something?). Mumbled something about going back to gas safe to argue that it was correct. I don’t know how this part of the process works. 5. Defects need to be fixed by the original plumber free of charge, but if you want someone else to do it, you have to pay for this separately. Gas Safe won’t help you get any money back from the plumber. 6. The inspection process was fairly swift, clear and (IMO) serious and competent. I’m glad I went through with it, and thanks to everyone here for encouraging me to do so in the face of some pushback from my builder. -
Plumber put together a thing … and I have concerns
mjsx replied to mjsx's topic in Boilers & Hot Water Tanks
All right, so I reported a concern with the gas safe registry. Thanks all for your info and advice. They say they’ll get back to me within 5 business days, and inspect within 10. Seems kinda slow but maybe it’s faster in practice… Will babysit the boiler for now… At least it’s Summer. -
Plumber put together a thing … and I have concerns
mjsx replied to mjsx's topic in Boilers & Hot Water Tanks
Thanks for the replies. Sounds like my concerns are at least somewhat justified, unfortunately… I have now received as Gas Safe Buildings Regulations Compliance certificate and it’s legit. Nothing on the cylinder though. Given your thoughts, I’ll put these questions directly to the plumber (so far most of the comms have been via the builder, who has more or less replied “I don’t know about the plumbing, the plumber is certified, what’s the problem?”). Might also approach another plumber to get it all checked—what’s a good way to phrase this? (How do they feel about checking another plumber’s work?) -
So in the cellar I now have a completely new system boiler (Vitodens 100-W) and unvented cylinder (Kingspan Albion Ultrasteel Horizontal Indirect). The system (see below) has a few properties I find … interesting. Apparently it’s all done according to building control etc. specifications but I have a few concerns: 1. Is it okay for the pressure relief valve to discharge downwards, via a plastic pipe, into a pump designed for condensate? (There’s no tundra has far as I can see.) 2. The flue currently passes through a hole cut into an air brick. Can it stay like this or does the flue need to be bricked up? 3. All of the cylinder pipe work is plastic all the way to the boiler. Does some of it need to be copper? 4. Finally, the system been set up so that I can control the flow temperature only via the ViCare app. I have a ViCare wireless thermostat but for some reason it wasn’t set up at the same time as the boiler, and now the plumber wants an additional payment to set this up. I find it strange that Viessmann even makes this possible—not a good experience for the consumer.
-
Bit of a long shot, but does any happen to have a Vitodens 100-W system boiler (type B1HF, so purchased in the last few years) combined with an EM-P1 pump extension module? Are you able to set and change the schedules for the time the recirculation pump activates via the app? I was expecting to see something like this (from the demo account mode): My plumber has installed this, together with a Grundfos COMFORT pump, but via my ViCare app I can only turn the pump on and off. Apparently the plumber's own app allows him to set and change schedules, but I'm not able to do this. Is this normal? Viessmann seems to have a slightly wacky system of only allowing accessories to be added by the plumber (even the thermostat seems to work like this) which seems pretty user-hostile.
-
Just moved into a new house, and my kitchen sink discharges into an "open" drain—have never seen this arrangement before! Is it possible to plumb the kitchen waste into the drain directly? (Don't want to make a food particles for critters to eat.) Is this a lot of work? The gutters also discharge into the same drain, as did the boiler overflow (now removed).
-
Connecting Shelly 1PM to Shelly Motion Sensors
mjsx replied to Adsibob's topic in Networks, AV, Security & Automation
@Adsibob What pump are you using, and how is it connected to the Shelly? I would like to do this, but couldn’t figure out what pump to use. The ones I found (Grundfos) don’t seem to directly support a separate relay. -
Seems like a Grundfos pump is the way to go but I can't figure out if/how to trigger via a relay or other external controller. Is that possible?
-
So I recently replaced a structural wall with an RSJ. All fine except some of the wooden joists are not actually resting on the RSJ. This is sort of expected in that the RSJ is perfectly level but the wall that was there before was not but it’s a bit strange you can slip paper through the gap. I guess they will eventually settle over time (only a few mm in it) but is that going to crack plaster or tiles something once decorated? Should it be shimmed or something?
-
Casambi Lighting Controls - Any Experience or Advice ?
mjsx replied to bob the builder 2's topic in Lighting
Also interested in Casambi. @bob the builder 2 what did you decide in the end? -
@Dave Jones Sorry, which tray did you mean? None of those seem suitable. I don't think there's any ventilation there.
-
What's the right way to insulate a Butterfly/London roof? It looks like this on the outside: And this on the inside: There's two parts I'm especially wondering about: 1. The red bit toward the bottom of the "valley", where the roof and the ceiling comes to a point. There's obviously not enough height to put a great deal of insulation here. Also, completely filling this area would block airflow. 2. The green bit that's the main rafter, at the very lowest point of the roof (under the gutter). This is cold, solid, wood bridge. I'm planning to board up the ceiling with insulated plasterboard so all areas have some (meagre) insulation. Is it worth filling the red area with insulation, or leave it unfilled, for better ventilation?
-
@Carrerahill Where did you tuck away the "extra" wires and the Shelly 1 bits?