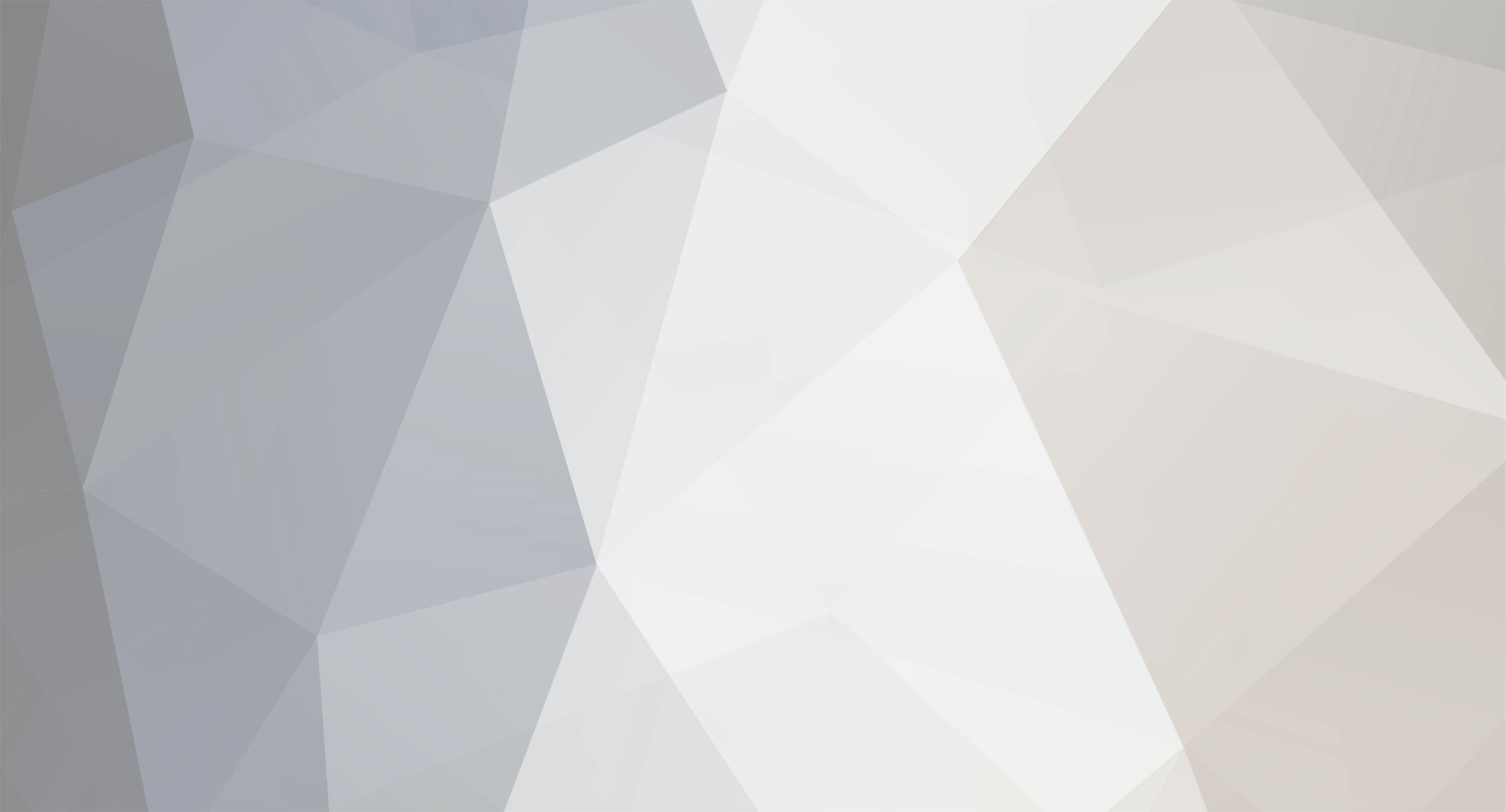
PhilC
Members-
Posts
27 -
Joined
-
Last visited
Everything posted by PhilC
-
Trying to work through this detail myself for a timber frame new build. @Great_scot_selfbuild who did you go with for the calculations? I take it most SAP assessors are not doing the calculations themselves, I would imagine it's down to the assessor but if I can point them in the direction of an accredited junction as per 4.18 section b, then they shouldn't need to do that particular junction right?
-
Timber Frame Wall build up for extension
PhilC replied to southcoastseagull's topic in New House & Self Build Design
Not a pro as I said but PIR is not breathable so if moisture gets into the frame and you have another non-porous layer VLC/PIR internally then the moisture can't escape anywhere. -
Hi Everyone, I am in a bit of a puzzle about how to detail the steelwork to support a 100mm block (rendered) wall (~2.5m height lightweight block). I could put the timber frame lintel or steel beam to carry the external block leaf lower down closer to the main beam but this creates a large thermal bridge in my mind, between the timber frame panel and the flat roof insulation. Raising the lintels up allows the PIR to come in underneath and prevent the thermal bridge. I did speak with my SE about it and in principle he thought this was ok. PIR of flat roof can come up to the frame under the masonry external leaf. Weather tightness, cavity tray etc would be above this to run out to the roof deck. The alternative is to bring the blockwork down to the steel, although this is an issue because the steel is 254mm high as are the metal web joists in the floor, so it takes the full-height plasterboard to T&G deck of the floor level so I cannot have a flat plate weld on it and as said, this seems to create a large thermal bridge even if the cavity is packed out with insulation below the cavity tray. I appreciate thoughts on this one, seems right to try to bring the flat roof insulation under and up to the frame. Render board is an option I guess but I went that route when planning our new 1st floor renovation rather than a new build, it seemed very expensive for the material and work and I think it may be difficult to match up with a rendered block ground floor. Also, I had virtually no interest in quoting for it, part of the reasoning for switching to a new build. Thanks.
-
Sketchup make 2017 free version
-
-
Thanks
-
Great stuff really helpful Liam! Hope the project is going well
-
Local authority or private?
-
Will see if i can get a conversation with a local BCO, thanks
-
Thanks Liam, much appreciated will take a look.
-
Timber Frame Wall build up for extension
PhilC replied to southcoastseagull's topic in New House & Self Build Design
Not a pro but the last one puts a non-breathable layer (external PIR) outside the timber frame so I would avoid that, water won't escape the frame even with a breather sheet on. I am looking to put thick option A in, albeit with differing stud sizes and PIR depths between and internally. -
Hi Everyone, Hoping for some advice on submitting a building control application. As background, we got planning permission to convert a detached chalet bungalow to a full house with a new closed panel timber frame 1st floor and rooms-in-roof design. Once we tried to get contractors for the conversion involved and ran the numbers it became clear it would be cheaper and simpler to knock down and do a new closed-panel timber frame build. Thread discussion about that here. We are not changing the footprint and the rebuild would look the same from the outside as the planning permission we obtained. I've spoken to a planning consultant and the officer who did our original planning permission and apart from the detail as to why the need to switch they did not see any particular reason against it. One main difference is we would do this on a self-build mortgage, we have discussed this with a provider and they have done their checks and are ready for us to provide planning/BC. We need a full BC application for financing. I did the original planning application and I have been building a detailed 3D model to provide the various plans, foundation, drainage, structure, plumbing, electrical, fire etc. I have a qualified SE provide me with beam calcs etc. I've never done a BC application and the requirements for the plans seem more opaque than planning and I am wondering if I am over/underworking the detail necessary. The timber frame and steel will all be provided by an STA provider who will validate their design anyway, although they have said my model will reduce any estimation and some design costs from the project. I've laid out most of the structure now apart from the roof, but I am wondering how detailed this really needs to be? I would prefer to complete the BC app independently of a provider as I will save the considerable upfront cost and be able to take the design to multiple parties to compete. Appreciate any experienced thoughts about this, I want to make sure I am employing my time in the right way. Happy to share model pics if you would like, Thanks, Phil
-
Hi Everyone, I'd appreciate any advice or guidance you can share. I've been putting together a project to convert our detached chalet bungalow into a house. We have householder development planning granted and I have a 3d structural design/SE calcs done (not a building control application completed, was looking to go via build notice) and quotations from timber frame suppliers and builders. The new first floor would be timber frame (or SIPS). It's been very hard to get builders engaged, I guess a state of the market generally but also I think because of the complexity of the build around matching the ground floor masonry to the timber frame 1st floor and handoffs between different people. The full costs of the quotes were way above our expectations and are not now realistic to our budget. We have spoken to the timber frame suppliers and received quotes for a full build for our design and it's only a small increase in the previous extension quote. When I factor in other aspects around the timber frame structure with industry per m2 rates for foundation, veneer wall, render, windows, roof etc, the build cost and VAT reclaim makes this look significantly cheaper and enables us to avoid complex retrofits of the ground floor to achieve the insulation/airtightness we are looking to get, so the new build seems a more viable route and probably a better outcome. I did do some reading on new build early in the project but dismissed it as too complicated and thought it would be cheaper to re-use the ground floor. Appreciate if any of you can share your advice on what I should be thinking about here I have a few areas I am researching but I am pretty sure I am missing important things I should consider. Thanks in advance for your time to respond.
-
I had a response from MCS saying they wont comment on how the wholesaler determines the COP of a product. But, they did confirm to become MSC certified the product has to be sent to a certification body, in this case the BBA. Its they who list the COP on the database. Your comment on having different COP in different regions makes sense, although the tests are performed with given air and water temperatures (which are the same on the Chofu details), so that still make we scratch my head, would have to dig down into specific testing details to understand. Its seems irrelevant though as long as the BBA is applying testing consistently and results for those products listed is relative, which I don't have any reason to doubt. Thanks for thoughts on volumizer/LLH etc. I've been watching the heat geek vids on utube mostly seems to suggest LLH are not great for efficiency and a lot of installs contain unnecessary stuff. I would like to just throw this issue to a heating engineer but i am dubious i would necessarily get the design that's in my best interest. Also i am looking at KNX and home assistant integration so i will need to understand the control points in enough detail to do that.
-
Researching grant Aerona as part of renovation, looking at that Chofu document the COP is different (4.30) on the 12XU ( I presume the 13kw grant unit). The grant lists this as COP 5.25 with the same air/water temp. The MCS site shows the SCOP listed in the grant document. At 5.4 SCOP the Aerona seems ahead of the field if I am understanding that right, but if the Chofu document is correct then its average to slightly subpar for the R32 based ASHP. Looking at the MCS test certification process it looks like they take evidence from the supplier rather than conduct tests themselves. I am misunderstanding something here or could the MCS details be wrong? I am hoping to use the system for some amount of cooling in the summer so would be interested Kevm how that would be best achieved in your view. Had a bit of a research on buffers/volumisers/LLH. If I have a large open loop in the system (probably ground livingroom+open plan kitchen area ~60m2) then would i not necessarily need one? Even if I have other controlled loops. As this is largest ground floor central space, its unlikely it would not need heating/cooling if the system was running.
-
Hi JohnMo, Thanks for the response and interest. I am not sure how that applies directly to my query though. I dont want to site the ringbeam on the inner leaf (1st picture i inserted) as it creates a large void over the cavity that has to be spanned somehow to present a flush finish with the ground floor, essentially will need another brick course outer leaf, something i would like to avoid. I would like to span the cavity with the floor joist if possible, then i can present the ring beam closer to the outside wall to batten/renderboard or woodfibre sheath and render. I guess you have no cavity to span with ICF?