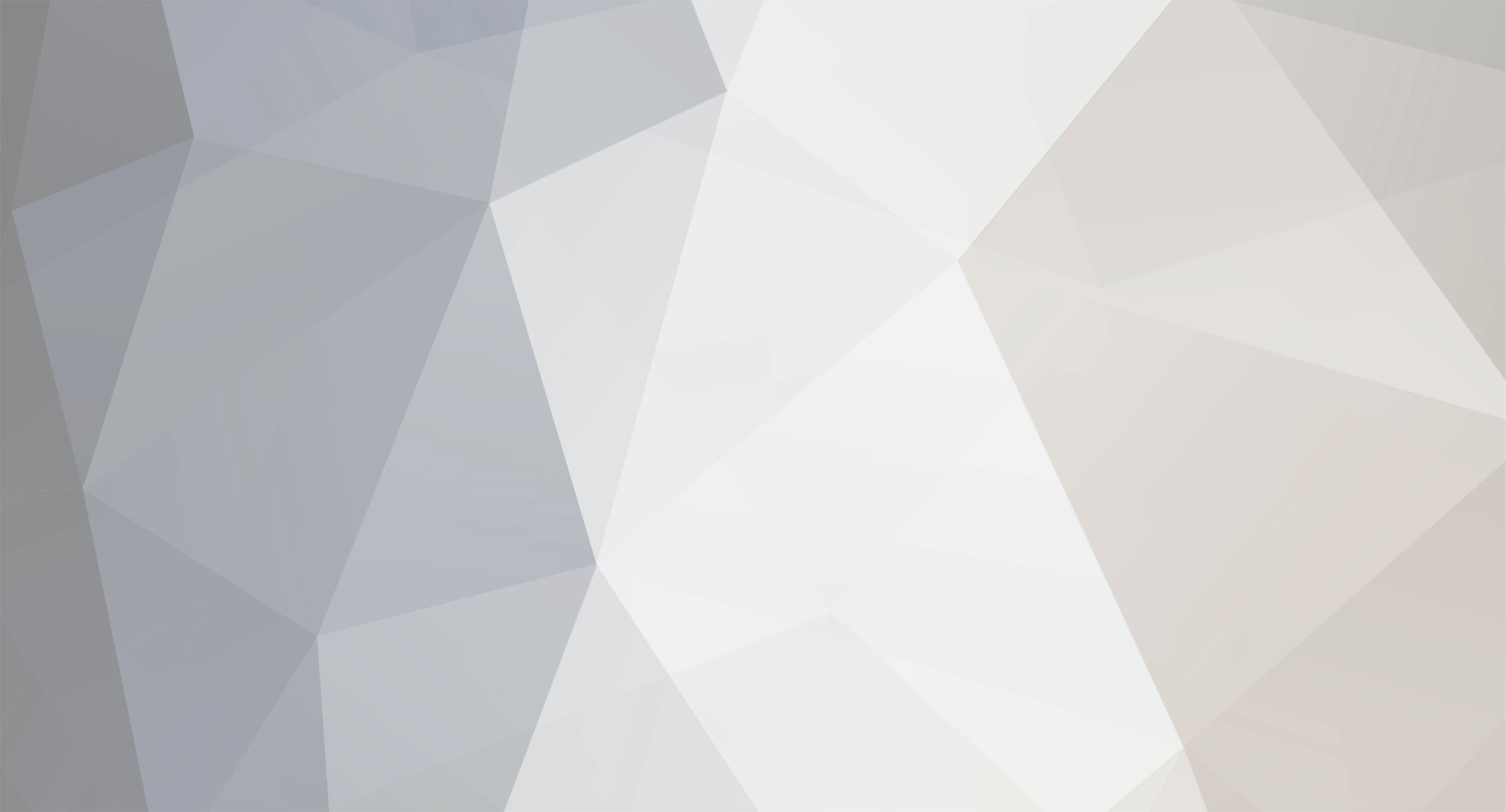
SBMS
Members-
Posts
932 -
Joined
-
Last visited
Everything posted by SBMS
-
Interesting that the 10 modulates lower than the 12 in heat mode (and outputs higher) but in cooling mode the maximum output is identical. (Page 5) makes me think it’s the same hardware but software is range setting in heating mode but allowing the compressor to run full speed in cooling mode. Which actually is a useful thing for me as there is no additional cooling output with the 12kW but the 10kW is possibly better suited for my heat loss requirements 🤷♂️
-
Does the 10kW modulate down to same level as the 12kW? What’s the point in going for the 10kW then??
-
It’s 9kW at -4 in total. Sorry - the installer originally sized 12kW but they werent accounting for heat recovery so had a higher heat loss. I thought you were saying the heat loss calculation was wrong. They don’t have the calcs yet for updated heat loss. Interestingly heatpunk which produced the same output picked the 12kW as well, not the 10… I guess I have to account for DHW as well
-
What is your current approach to cooling?
-
I think I’ve been pretty scientific in the heat loss calculations. I agree the cooling ones are not realistic. How are the heat loss calcs wrong though and producing oversizing?
-
I think the undercurrent point of mine here - despite some strong opinions on the rubbish job i am doing trying to navigate it - is that as we self builders spend more and more time on insulating our houses from the cold, there is disproportionate consideration given to overheating. I haven’t seen any DIY approachable method of coming up with a sensible cooling load model or calculation - but plenty of opinions that what I am producing is rubbish. I think as we hit hotter summers and temperatures increase this will become as important as the (much larger) emphasis on heat insulation and heat loss. I have noticed many other self builders that have overheating issues on here, and I do think it’s a problem that the part o overheating doesn’t fully address. I could just throw air con at it, but as anyone who has had an AC contractor round they (under their industry guidance) size for PEAK load. We’ve had two separate contractors who sized that we need a vrf system at 24kW output!! That is definitely madness. The answer as I see it now is a. size ASHP for heating and it’ll ‘probably be alright for cooling’ b. Get an oversized sub contracted ac system at double cost c. Pay for an independent cooling load assessment (if one exists) - that is more realistic than a peak load calculation! 🤷♂️
-
Checked with our SAP assessor and the house does pass under dynamic thermal modelling. Frustratingly they don’t have cooling load/heat gain calculations in their modelling software 🙄
-
Oversized for cooling or heating?
-
30mm is too much. You could put trim on and foam behind it.
-
You’re right rick and 1/3 of that glazing is actually underneath a covered canopy. I need to update the model to reflect that. We could also look at an extendable shade if needed - it is north facing though.. it does have quite large roof lights which don’t help - but again we could shade those as well to reduce the cooling demand on very hot days. I’ve asked the SAP assessor for their full report as well, never thought of that!!
-
Yes. We have passed under the dynamic thermal modelling process.
-
By doors we have a large set of sliders and bifolds, master bedroom bifolds and two sets of glazed French doors and a utility glazed door. So the ‘doors’ are actually mainly glass. Correct I haven’t attributed for shading and that’s a good point. Agreed on internal gains I used an estimated watts per m2 probably over estimated. I don’t know what you mean by How have we passed building regs? Our glazing is all high performance triple glazing average is 0.7 u value and 0.5 g value. What is ‘bad’ about the figures?
-
Have attached my full spreadsheet. First tab is the Cooling Load, which is a filtered view of the third tab which is the above but for every room. Cooling Load strips out room where cooling is not required. Second tab is my heat loss calculations just for completeness. Heat and Cooling Calcs v1.xlsx
-
I've tried to do a cooling calculation based on 30 degrees outside, 21 inside. I have more rooms but those won't be cooled. My absolute worst case peak cooling is around 21kW for the whole house (red columns). Appreciate this is unrealistic etc. I've looked around and a fair bit of wisdom indicates designing to around 75% of peak and I have done this (orange columns). This is around 16kW. This exceeds the heat pump, but then again 6kW of this is for the kitchen diner, which, when it is very hot, we are likely to have all doors open in any event, so any cooling in here is likely to be fairly pointless. This drops the design to around 10kW which a 12kW heat pump should be able to provide. In actual fact, the important rooms are master bedroom, living room, bedrooms 1 and 2 and the hallway, which only has a design cooling load of around 5kW. It has a peak load of around 9kW. I feel that an ASHP would deliver enough cooling for the house, but I do think that I'd need the FCUs on their own, cooler circuit - especially the cooling loads for the landing and halls which are driven by FCUs. Thoughts? Floor Room Orientation Floor Area (m2) UFH Available Area (m2) Cooled By Solid Ground Area - 0.10 (m2) External Wall Area - 0.15u (m2) Pitched Roof Area - 0.12u (m2) Flat Roof Area - 0.11u (m2) Window Area - 0.71u (m2) Door Area - 1.0u (m2) Velux Area - 1.0 u (m2) Rooflight Area - 0.6 u (m2) ACH Design Internal Temp Glazed Doors? Cooling Required G Value of Doors/Windows Heat Gain - External Wall (watts) Heat Gain - Pitched Roof (watts) Heat Gain - Flat Roof (watts) Heat Gain - Windows (watts) Heat Gain - Doors (watts) Heat Gain - Veluxes (watts) Heat Gain - Rooflights (watts) Heat Gain - Uncontrolled Infiltration (watts) Heat Gain - Internal (watts) Total Heat Gain (kW) Wall Gain (Design W) Pitched Roof Gain (Design W) Flat Roof Gain (Design W) Window Gain (Design W) Door Gain (Design W) Velux Gain (Design W) Rooflight Gain (Design W) Ventilation Gain (Design W) Internal Gain (Design W) Total Gain (Design kW) Ground Hallway* South 22.73 19.00 UFH 22.73 11.70 0.00 0.00 2.73 2.73 0.00 0.00 0.50 21 No Yes 0.346 15.80 0.00 0.00 755.66 0.00 0 0.00 8.223714 136.38 0.92 13.43 0.00 0.00 566.75 0.00 0.00 0.00 6.58 109.10 0.70 Ground Living Room* South 26.39 23.90 UFH 26.39 26.23 0.00 0.00 3.08 0.00 0.00 0.00 0.50 21 Yes 0.346 35.42 0.00 0.00 852.54 0.00 0 0.00 9.547902 263.90 1.16 30.10 0.00 0.00 639.41 0.00 0.00 0.00 7.64 211.12 0.89 Ground Gym* West 26.55 26.55 UFH 26.55 14.79 0.00 26.55 0.00 0.00 0.00 0.00 0.50 21 Yes 0.346 19.97 0.00 26.28 0.00 0.00 0 0.00 9.60579 318.60 0.37 16.98 0.00 22.34 0.00 0.00 0.00 0.00 7.68 254.88 0.30 Ground Open Plan Living* North and East 41.00 40.00 UFH 41.00 38.17 0.00 41.00 0.00 25.62 0.00 7.28 0.50 21 Yes Yes 0.504 51.53 0.00 40.59 0.00 6456.24 0 1310.40 14.8338 410.00 8.28 43.80 0.00 34.50 0.00 4842.18 0.00 982.80 11.87 328.00 6.24 Ground Kitchen* East 38.00 25.00 UFH 38.00 4.03 0.00 0.00 0.00 0.00 0.00 0.00 0.50 21 Yes 0.504 5.44 0.00 0.00 0.00 0.00 0 0.00 13.7484 380.00 0.40 4.62 0.00 0.00 0.00 0.00 0.00 0.00 11.00 304.00 0.32 Ground Utility/Boot Room East 12.00 6.60 UFH 12.00 20.88 0.00 0.00 0.00 1.89 0.00 0.00 0.50 21 Yes Yes 0.346 28.19 0.00 0.00 0.00 392.36 0 0.00 4.3416 72.00 0.50 23.96 0.00 0.00 0.00 294.27 0.00 0.00 3.47 57.60 0.38 Ground Snug/Playroom* East 14.39 12.70 UFH 14.39 7.93 0.00 0.00 0.00 3.15 0.00 0.00 0.50 21 Yes Yes 0.346 10.71 0.00 0.00 0.00 653.94 0 0.00 5.206302 86.34 0.76 9.10 0.00 0.00 0.00 490.46 0.00 0.00 4.17 69.07 0.57 Ground Study* South and East 10.90 9.90 UFH 10.90 19.66 0.00 0.00 1.43 3.15 0.00 0.00 0.50 21 Yes Yes 0.346 26.54 0.00 0.00 247.39 544.95 0 0.00 3.94362 65.40 0.89 22.56 0.00 0.00 185.54 408.71 0.00 0.00 3.15 52.32 0.67 First Floor First Floor Gallery Landing* South 28.00 FCU 0.00 11.70 0.00 0.00 6.70 0.00 0.00 0.00 0.50 21 Yes 0.346 15.80 0.00 0.00 1854.56 0.00 0 0.00 9.7083 168.00 2.05 13.43 0.00 0.00 1390.92 0.00 0.00 0.00 7.77 134.40 1.55 First Floor Bedroom 2* 21.00 FCU 0.00 26.49 0.00 0.00 5.23 0.00 0.00 0.00 0.50 21 Yes 0.346 35.77 0.00 0.00 905.48 0.00 0 0.00 7.281225 105.00 1.05 30.40 0.00 0.00 679.11 0.00 0.00 0.00 5.82 84.00 0.80 First Floor Bedroom 1* North and West 20.00 FCU 0.00 27.04 0.00 0.00 5.36 0.00 0.00 0.00 0.50 21 Yes 0.346 36.50 0.00 0.00 927.97 0.00 0 0.00 6.9345 100.00 1.07 31.03 0.00 0.00 695.98 0.00 0.00 0.00 5.55 80.00 0.81 First Floor Master Bedroom (incl gable)* North 23.20 FCU 0.00 39.44 24.00 0.00 8.90 0.00 0.00 0.00 0.50 21 Yes 0.504 53.24 25.92 0.00 1121.40 0.00 0 0.00 8.04402 116.00 1.32 45.25 22.03 0.00 841.05 0.00 0.00 0.00 6.44 92.80 1.01 First Floor W/W* South 9.68 None 0.00 12.35 0.00 0.00 1.43 0.00 0.00 0.00 0.50 21 Yes 0.346 16.67 0.00 0.00 395.82 0.00 0 0.00 3.356298 58.08 0.47 14.17 0.00 0.00 296.87 0.00 0.00 0.00 2.69 46.46 0.36 Second Floor Second Floor Gallery Landing* South 25.40 FCU 0.00 9.90 39.67 0.00 0.00 0.00 2.14 0.00 0.50 21 Yes 0.346 13.37 42.84 0.00 0.00 0.00 471.68 0.00 8.806815 152.40 0.69 11.36 36.41 0.00 0.00 0.00 353.76 0.00 7.05 121.92 0.53 Second Floor Bedroom 4* 40.00 FCU 0.00 29.39 62.47 0.00 0.00 0.00 4.02 0.00 0.50 21 Yes 0.346 39.67 67.47 0.00 0.00 0.00 884.4 0.00 13.869 200.00 1.21 33.72 57.35 0.00 0.00 0.00 663.30 0.00 11.10 160.00 0.93 Second Floor Bedroom 5* 31.45 FCU 0.00 17.51 58.00 0.00 0.00 0.00 2.63 0.00 0.50 21 Yes 0.346 23.64 62.64 0.00 0.00 0.00 577.808 0.00 10.9045 157.25 0.83 20.09 53.24 0.00 0.00 0.00 433.36 0.00 8.72 125.80 0.64
-
Thanks Nick - that post was from 2022 and our current build - we're going again, so different house.
-
What did you do in the end? Separate ac units?
-
Yes it’s large around 480sqm internal space (rooms in roof). To be fair they’ve calculated a higher heat load using their standard MCS calculator of around 10kw. Heatpunk calculated 9.8kw. I will work it with them, would rather not switch and they’re a good outfit and we used them on last build. any advice on calculating an average cooling demand?
-
Worth saying that these are just the output capacity of the fan coils not the cooling/heating demand for the room.
-
We touched on this before on another thread where I got ripped apart as my cooling load was enormous as I had done it on a worst case basis which I think you’d said wasn’t realistic. Heat loss is around 7kW (it’s a big house). Installer is sizing for an 12kW arotherm I think - and that’s probably sensible with DHW and a bit of headroom. Will probably need it this large for cooling. I’m going to do some more work on this cooling demand and try and get an average cooling load demand - I have a heat loss calculation which is fine but must admit am struggling to model the average heat gain on the worst day. Any hints on how to easily model this?
-
Thanks - does The heat pump need to be aware of multiple circuits or is this done via manifolds and blending etc?
-
Still getting my head around all this so be kind..! As I understand it, I’m pushing cool water round the system. My thinking is to have UFH downstairs and then around 7 fan coil radiators in bedrooms and landing spaces. I will lag all pipes to the FCUs (possibly prelagged piping). Don’t know size had assumed 15mm (standard?). I can have a single circuit when cooling but the temperature of the water in that circuit is going to be dictated by the UFH and danger of dew/condensation so consensus seems to be to run that at 15 degrees. If I had one single circuit my FCUs would also receive 15 which inhibits their cooling capacity a fair amount. I think that some heat pumps (we are probably going for an aroTherm) support cooling two circuits. The first circuit would do the UFH at 15 and the second would do the FCUs at 10 degrees. I assuming the ASHP would be producing 10 degree water and it would be blended to warm it for the UFH circuit. All of the above is my assumption and about the limit of my understanding without yet speaking to the installer.
-
I’m at the stage of specifying the system and I’d need to decide whether to run two circuits or not, at this stage? The fan coil units I am looking at output 1.6kw cooling for example with an input temp of 10 degrees. If I run these at 15 or 16 I assume that output will drop something like 20%? Hence wondering if I should run two circuits
-
If lagging pipes why not run fan coils at a lower temperature, and ignore dew point?
-
Is it necessary to get a heat pump that can run two independent circuits when doing cooling? One for UFH and one for fancoils - to run at different temperatures? If so, are there any downsides to this setup when it comes to heating?
-
Posi joist - This install feels rubbish, thoughts?
SBMS replied to boxrick's topic in Roofing, Tiling & Slating
One challenge is the builder often takes you to a 'satisfied' customer. That customer might have been totally hands off, not inspected work, and have no clue as to what issues are lurking in the building fabric...