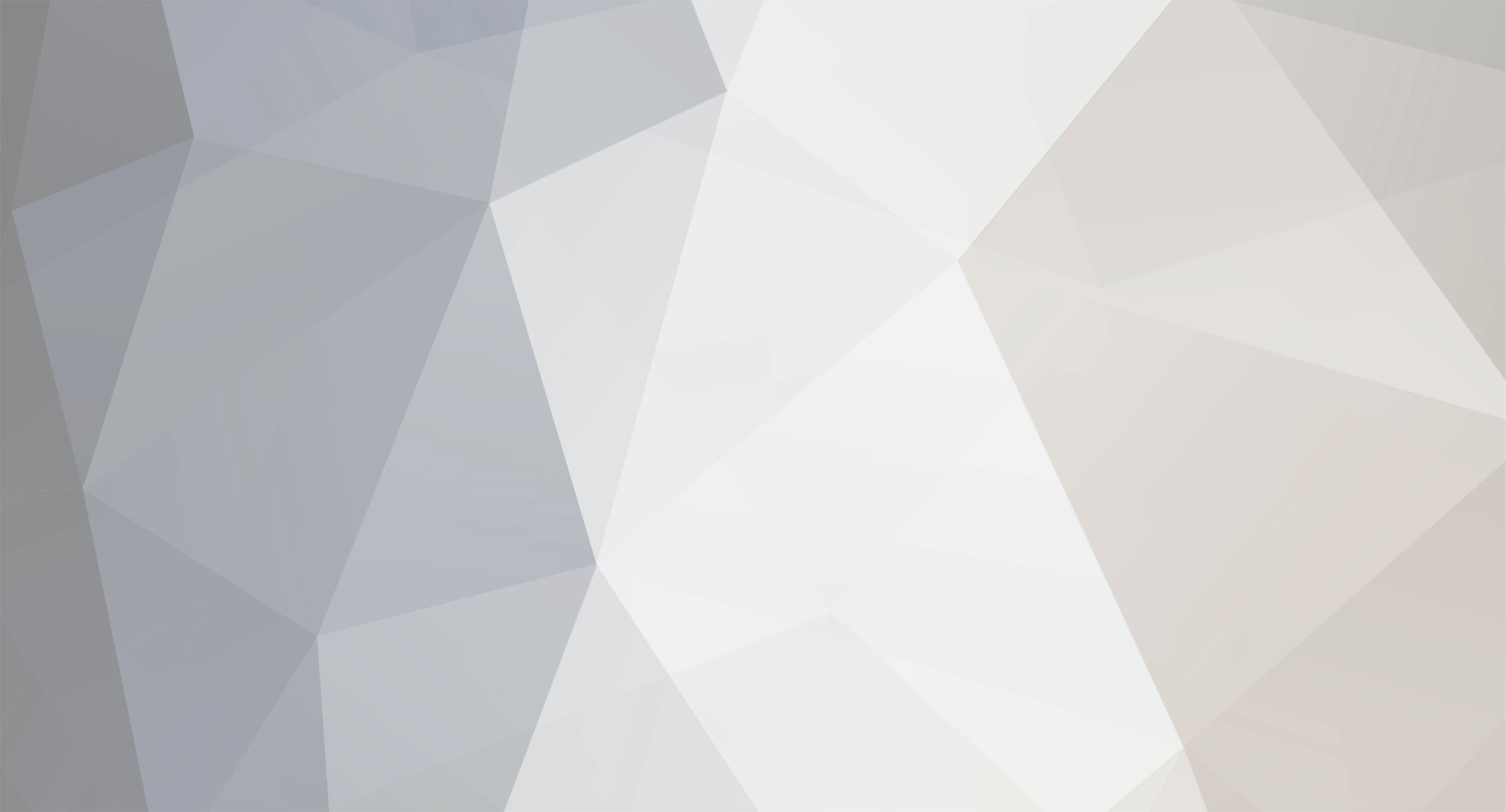
Fraser Lamont
Members-
Posts
34 -
Joined
-
Last visited
Recent Profile Visitors
The recent visitors block is disabled and is not being shown to other users.
Fraser Lamont's Achievements

Member (3/5)
0
Reputation
-
Hi, thanks for your reply. I haven't heard it act the same way when the DHW cycle is on, will check this out though when I can. Usually it happens on the Rad Heating, and usually for about half a minute. It only does it for extended periods of time if there is a greater difference between the required temp from NEST (21) and the actual temp of the house (23). I don't have a 'cooling unit' with my system - should the 'indoor zone' on the controller be on 'cool & heat' or 'heat only'? My installer left the system on the 'cool & heat' setting. I think the installer just left everything on the default settings, back up heat is switched off and twice throughout the winter, I ran out of hot water. Should I have the back-up heat on? Many Thanks!
-
Here's a link to YOUTUBE https://youtu.be/OO3Y82QilH0
-
and here's a video of the system running. Say the temp in the house is 23, I increase the temp on the NEST up to 24 to bring the system on, then lower it to say, 21, to turn it off, the bigger the difference between the required temp (in this case 21 on the NEST Controller), the actual temp in the house (in this case 23) - the longer the increase in speed/noise occurs in the pumps. That's why I'm wondering if the SAMSUNG GEN 6 setting for 'INDOOR ZONE' should be 'HEAT ONLY' instead of 'HEAT & COOL'. I tried using the 'HEAT ONLY' but I didn't restart the Controller, it behaved in the same way. There is only 1 zone in the house, all radiator valves are manual and open. JOULE (UK) told me there are actuators instead of of a 3-way valve and the actuators stay in the final position of what was last running (DHW/RAD). The Tech at JOULE wasn't sure if the pumps were cycling for something to do with the Heat Exchanger in the External Unit. Link to video where the pump speed and noise increases for a longer time where there was a bigger difference between required Heat (21) and actual temp (23) https://www.glenhaultin.co.uk/off-and-on.mp4
-
-
Hi, I phoned JOULE, they told me the system uses actuators instead of a 3 way valve, and these stay in the last position when the system finishes whatever cycle it's on. I have just plain manual TRV's which are always open. The NEST only controls one zone on the controller, just 1 circuit on the heating system. The settings on the WILO-PARA circulation pumps are a bit confusing. The pumps can be set as 'constant' or 'variable' speeds. They are set at 'constant' speed but the speed definitely increases just before the heating turns off. It's very strange.
-
Sorry, forgot to mention, there are no other valves on my system other than what is included with the JOULE Pre Plumbed Cylinder. Thanks
-
Thank you for your reply. I have got photographs of the 2 pumps, the flow and the return. I thought the settings were on CONSTANT SPEED and the correct CURVE (III). The noise is definitely from the Pumps speed increasing - this happens when the thermostat temperature has been reached and the heating is turning off. The noise of the pumps doubles as the speed increases. Can this be from an external (SAMSUNG GEN6 Controller) sending another signal to the pumps? I went through some of the settings, the installer obviously didn't. I only have heating, no AIRCON with the system - should my Controller be set to HEAT ONLY? The setting on the machine just now is HEAT & COOLING. I changed it to HEAT ONLY and activated the heating, then turned it off and the pumps still increased the speed/noise. Should I restart the Controller if I change that setting, if so, how? Another thing. Twice during the winter I ran out of Hot Water. I checked the machine and the setting for BACKUP HEAT was turned off. I have another property with a GSHP and the default setting for that is on (6kw), so I'm confused why I'd run out of Hot Water with the ASHP. Is that the correct setting for the electric water heater to help boost the hot water when it's very cold? Many Thanks
-
Hi, thanks for your reply. I put the video online, using my own website as the host. There's a problem with the video - but the sound is there. This was captured at a distance of approx 1000mm using a phone camera. The sound in the video has already increased considerably by the time I started filming it. Link is www.glenhaultin.co.uk/noise.mp4
-
Thanks for your reply. Don't think there are any zone valves on the system. I understand this machine uses actuators instead of a 3 port valve, the Tech guy from Joule told me whatever state the machine shuts down, it stays like that, ie, no default setting. So if the rad heating closes down, it stays on that setting, it doesn't change for domestic hot water until that's required. It's a strange one
-
Hi folks, I have a problem with a SAMSUNG GEN6 Controller. The Cylinder was provided by JOULE (UK) with a SAMSUNG GEN 6 Control. There are 2 WILO pumps connected for flow/return to the external 12kw unit. Once the rad heating is finished, for approx 20 - 30 secs, it sound like a jet is about to take off. The noise increases from what I can only imagine is the pumps before clicking then turns off. I have used the NEST controller, increased the temp to bring on the rad heating, then turned it back down. Every time the rad heat turns off - the pump noise increases again for about half a minute before turning off. I phoned the supplier technical, sent them a video and they have never heard of this - just wondering if anyone here has. The guy did say, it might be sending a blast of liquid through to the external unit for the heat exchanger - I can't understand for what though. Many thanks
-
yes, the cavity is ventilated.
- 4 replies
-
- u value
- insulation
-
(and 1 more)
Tagged with:
-
Hi, anyone have any links to good u value calculators? Tried some from PIR manufacturers - unfortunately not all options are listed. I'm renovating a house and the spec seems stricter in Scotland than elsewhere regarding u-values for new builds, refurbishments, extensions etc. Building Control have specified my walls to be within this spec which is 0.22. The house is built with double block, outer leaf rendered 15>20mm, dense block. There is a 75mm cavity with inner leaf dense block. The entire structure will have a certain value before I add the insulation etc. I will be going down the route of installing PIR directly onto the inner face of inner leaf, taping then battening and dry lining the walls (warm batten). I'm looking for a calculator which will allow me to enter all these details if there is one out there. I have been looking at 100mm PIR but if I can reduce this even a wee bit, I'd be delighted. No biggie if I can't. Thanks
- 4 replies
-
- u value
- insulation
-
(and 1 more)
Tagged with:
-
it is a temporary measure, however I'll be reinstating the load bearer once the slab is down. The top of the slab will be level with the dwarf walls which gives me about 150-160mm, enough for 100mm PIR, underfloor heating and a screed - the floor will be approx the same level as it is now. I've bolted the new joists (150 x 47) at 600mm centres, I will be firing nails in at 400 centres to keep everything knitted together. The span is a few mm over 3600, I guess I'm hoping the paired joists will be ok at that distance. To be honest, the upstairs has been used for decades with no obvious problems. If I have to add new joists in between I'll have to go down the route of 75x175 or similar, any higher and the upstairs gable window would look daft.
- 9 replies
-
- ceiling ties
- first floor joists
-
(and 1 more)
Tagged with:
-
No, I'm doing that anyway (removing the central load bearer), to get the ground floor done. Problem I have is the load bearer sits on doubled up Ground floor Joists, the load bearer is approx 50mm offset from the dwarf wall. I have to remove the load bearer to get the floor joists out. I would have been able to sort all of this in situ if the load bearer was not offset - by cutting the floor joists and packing between the dwarf and the load bearer but I don't have that option. Once the ground floor void is filled and with a new slab at dwarf wall level, the load bearer will be put back up again
- 9 replies
-
- ceiling ties
- first floor joists
-
(and 1 more)
Tagged with:
-
hardly any. Timber from the 70's seems a lot harder than the stuff we get now. Here's an image of the front half of the house, from front wall to load bearer. I bolted through the original joist connector pieces, the bolts are approx 200mm spacing over the load bearer, then 600mm for the remainder of the span. This is the image I sent to my engineer and he is satisfied with it.
- 9 replies
-
- ceiling ties
- first floor joists
-
(and 1 more)
Tagged with: