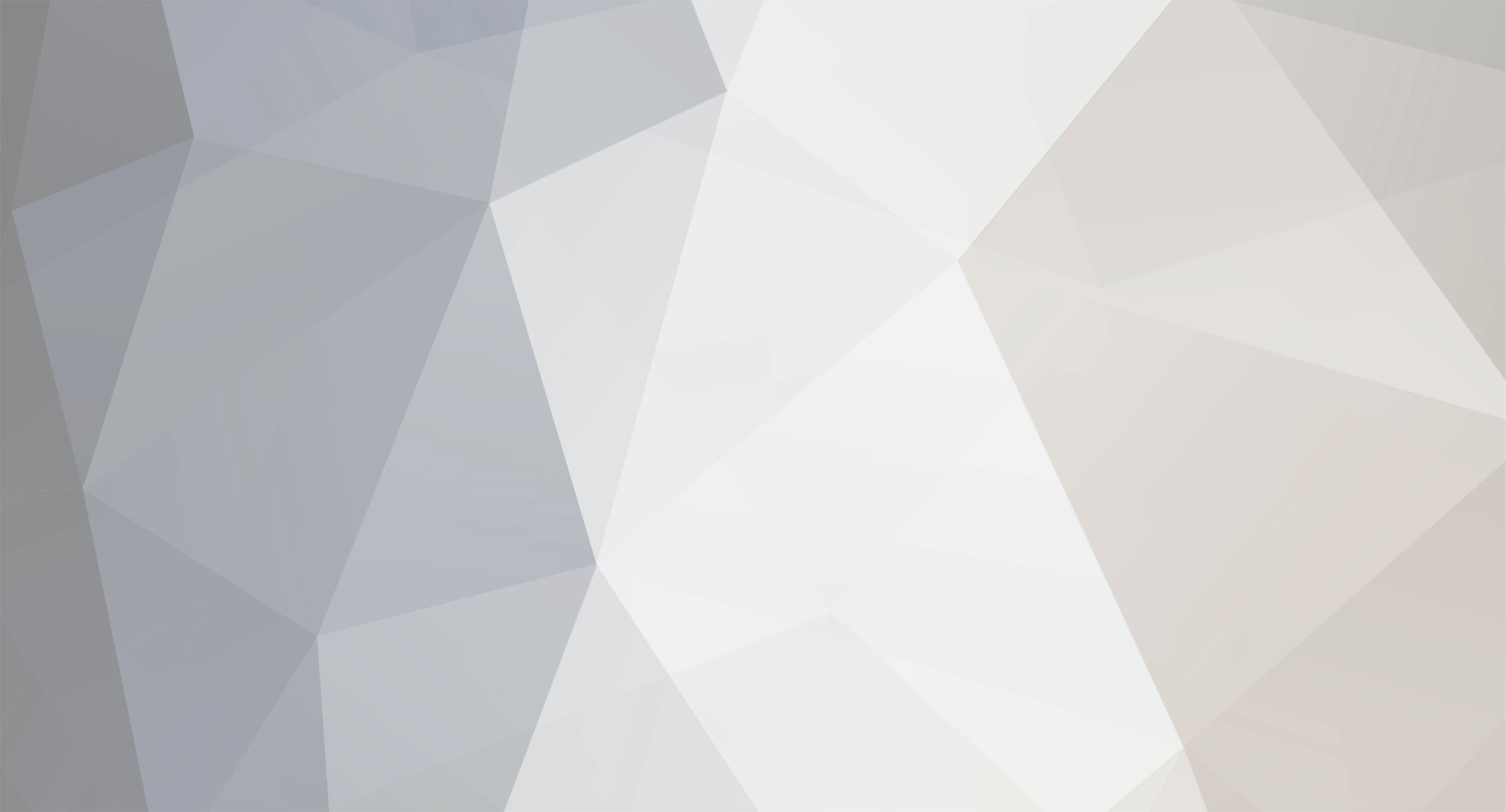
Tetrarch
Members-
Posts
151 -
Joined
-
Last visited
Personal Information
-
Location
Hartley
Recent Profile Visitors
The recent visitors block is disabled and is not being shown to other users.
Tetrarch's Achievements

Regular Member (4/5)
34
Reputation
-
Mounting frame of recessed light gone in ceiling - can't get down
Tetrarch replied to Question's topic in Decorating
You'll have to fold both springs down. I'd try to bend both down, using a screwdriver to wedge them against the bottom and then use a zippy-strip to hold them in situ - that should let you get the whole thing out Regards Tet -
Thank you for the candid feedback. Fat finger: That deflection is 16mm not 160mm This is entirely my typographical error - for which I apologise One piece of hitherto unprovided information. The North/South beam is 8m long, so there is a significant load on the centre of the East/West beam. This install will definitely need significant professional input. I would still like to know the answer to my original question though...... Regards Tet
-
Hi Nick, The beam required to span the gap was ~800kg. The deflection is 160mm which is significantly more than the door supplier specifies I understand that I am out of my depth, but my intuition is that there are multiple compromises with a single beam which can be entirely offset by a single compromise of a single supporting pillar IF I am correct, then the size of the pillar becomes the entirety of the compromise - hence my question. I'm only interested in the comparison between vertical supports Regards Tet
-
This must be a common situation but I'd like some comment on alternatives. The below picture is just to illustrate the install and there has been no structural calcs yet so the proposed steels are not to scale. The plan is to open up the back of the house and install a 6.5m fully-opening patio door and remove the internal wall the currently runs North/South. It's a two-storey house so both beams will be replacing supporting walls above. Accepting that some kind of vertical support will be needed. Aesthetically, my view is that a circular pillar (indicated by the yellow circle) is far less obtrusive than a square or raw I-beam. Is there a way to find a comparison between round, square and circular vertical supports cross-section vs compressive load. The actual numbers are not as important as the relative cross-sectional area Regards Tet P.S. Asking for a friend.
-
I would suggest that trying to slide this upstairs sounds attractive, but sounds hellishly dangerous for the guys UNDERNEATH I like the idea of a genie. The trouble with a genie is the weight transfer when you try shift it laterally. I had a large problem trying to move a 75kg skylight through its own "hole" - up was fine - it was just the transition from vertical to horizontal that was a challenge. Removing the glass would make things enormously easier. You can then genie the whole bath and fix some scaff boards across the diagonal to take the weight straight off the genie Very best of luck Regards Tet
-
They're all different FH Brundle do a great range and very keen prices. Big fan of the company, their products and their flawless customer service https://www.fhbrundle.co.uk/handrailing-and-balustrade/frameless-glass-balustrade?via_sb=true Regards Tet
-
Leak coming in around roof light EPDM issue
Tetrarch replied to nmh's topic in Roofing, Tiling & Slating
That detail looks very odd. My spec was 100mm of waterproof upstand as a minimum (see below) I used EPDM rather than the architects lead spec and they (generally) don't use 45-degree flashing anymore for EPDM. I would wholeheartedly agree with the other critics of your roofer's advice. In my experience traditional felt roof guys are always only really happy with felt, some rave about liquid coverings, but most rail against EPDM. I'd get an EPDM specialist to have a look at your particular install and go from there Regards Tet -
Removing soil through the house - do you have a direct line through the house, navigating through and around door ways will be the real challenge. In my experience, wheelbarrows are difficult to control consistently when loaded, I found a four-wheeled pull trolley easier to manage although a soil conveyor would be optimal - hence the first question......... Regards Tet
-
Thank you for the link. It looks as though I should have spent longer on the FH Brundle website.......there is a specific pre-made (but MUCH more expensive) panneled version called zenturo available: https://www.fhbrundle.co.uk/fencing-and-security/super-gabion-fencing https://www.wireland.gr/en/products/steel-wire/rockfall-mesh/item/toixos-apo-sirmatokivotia-zenturo The sizing on this is bigger mesh than mine but it comes up in maximum two metre panels Regards Tet
-
I intend to use a drainpipe to insert stones slowly rather than dropping from a height It's just a stone wall, (plus design proof of concept for a more substantial curved retaining wall planned for the drive). I started with the idea of a wall that was 9" at one end and 6" at the other. It's only when offering up the mesh that I realised that this would be costly Agree with both these. I have plenty of hooks. As it's decorative rather than structural then the thinner it is the less it will bulge. I have some 1" box-section aluminium that I could use as guide bars to give the structure some support Do you guys think that a 4" thickness would be suitable - ultimately if it doesn't quite work then I can always make it thicker Regards Tet
-
I've created a space that I want to fill with a gabion wall. I've chosen 1" x 1" x 10g galvanised wire mesh sheets and they are fixed at the ends and to the bottom. I have a number of gabion ties (double-ended hooks) to hold the walls together before filling. The "filling" itself will be ~30mm pebbles of some sort. The overall size is approximately 3.1m x 1.7m. The post at the right hand end is 6" across and I have a 9" brick wall at the other My question is how thick should I make the wall? The thicker it is the heavier it will be, the more the pebbles will cost and the more likely it will to bow the gabion itself The thinner it is the less stable it will be Any advice welcome, pics below Regards Tet
-
With the right kind of standoffs you secure the standoffs to the beam and then fit the glass to the standoffs in an entirely separate process. I found this on youtube to give you an idea: Just to note I have NOT installed these, but just came across this when doing my reseaach Regards Tet
-
You don't need these. For a standoff in a glulam (is there a better screw substrate?) you could use a regular coach screws - the biggest that you can safely insert Regards Tet