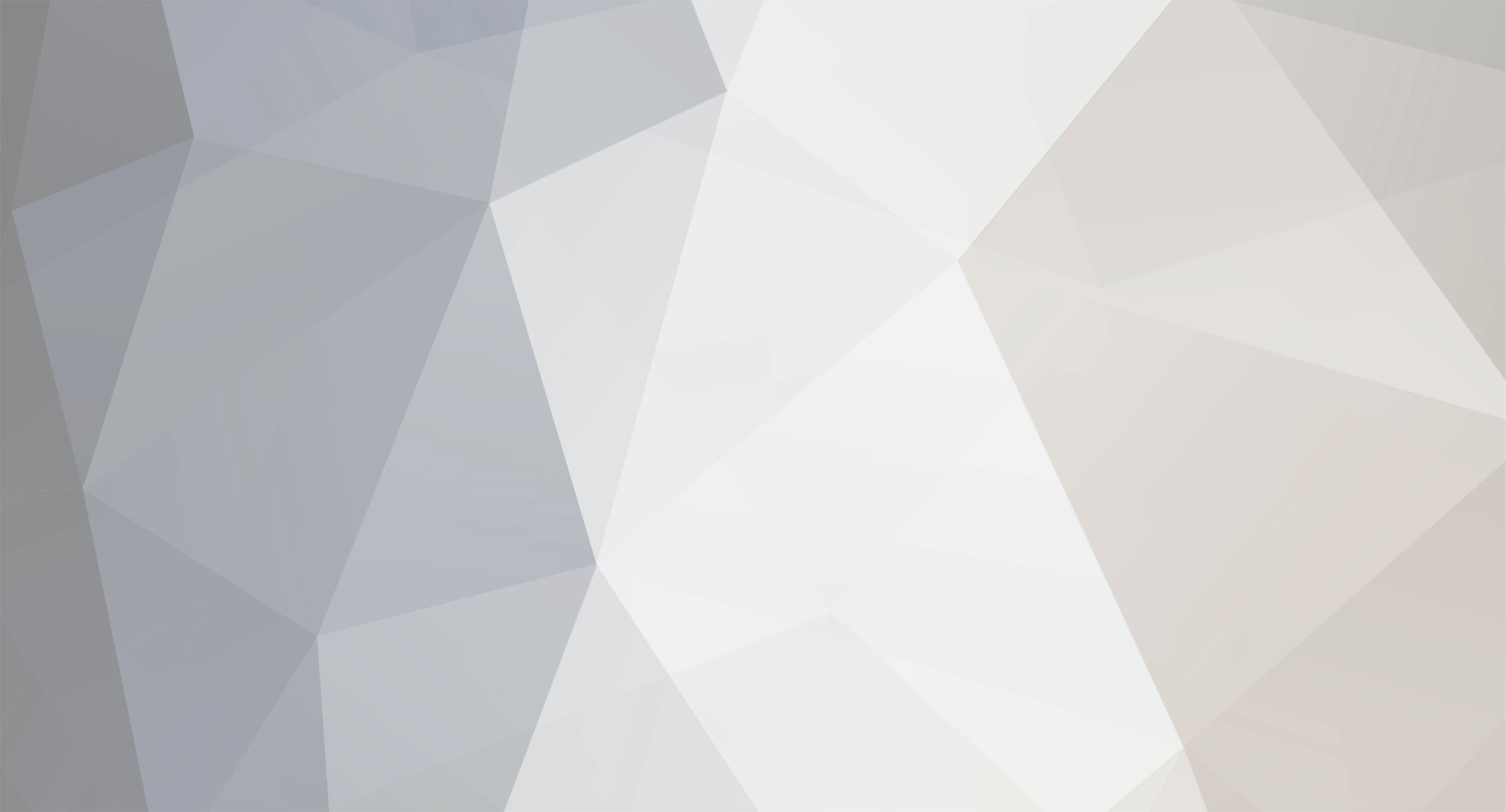
larry
Members-
Posts
169 -
Joined
-
Last visited
Recent Profile Visitors
The recent visitors block is disabled and is not being shown to other users.
larry's Achievements

Regular Member (4/5)
30
Reputation
-
Thanks. OK, great. I'll read up on those. We are small isolated town. I think neighbours in all directions have them and personally never mind the smell. The old coal fires, on the other hand, are/were something else. If I'm honest I doubt we'd use it loads. Just slightly comforting to have a backup source of heat...... And we are I guess going to do a lot of the labour anyway so if we do now is the time. I guess time to make some calls to get some prices as there's no way I'll be the one putting the liner down! Thank you!
-
Hello So, I've just finished with a full refurb of one of my downstairs rooms. I'm about to move onto the other - floor up, walls back to plaster, new suspended floor, wood fibre insulation on walls (1920s solid wall) is the plan. I'm not sure what to do about the fireplace. Obviously our approach will be different depending on whether or not we want to stick a log burner in (either now or in future), and if I'm honest I'm ambivilant on that. I also won't know what size the opening is I guess until I start pulling stuff back (at the moment there's just a panel covering up what I expect to be a slew of mummified pigeons). I've never had a wood burner before so this is new territory. Preumably, if we go down the wood burner route we'd need to get somebody to fit a liner down the chimney, which would then be insultated with Vermiculite held back in place with a closure plate? But in that case, how do we insulate the back wall of the fire place - behind the stove? (the external chimney is built half way out of the solid wall). Thank you for feedback and sorry if an obvious question - just trying to think this through
-
Ours scraped a C rating partly based on insulated cavity walls. We have solid walls. To be fair, the house survey made the same mistake.
-
Missing insulation in vaulted ceiling
larry replied to d87francis's topic in Lofts, Dormers & Loft Conversions
The other dimension here of course is the environmental one. Not just the pointlessness of manufacturing celotex which then just goes into the loft basically for storage, but the gap between how well we think a building will perform based on design and what happens in practice. Think of the potential extra fuel you'd use over the next 20 years or so whilst being potentially convinced you've got an efficient modern house. Bad workmanship has huge potential to influence the carbon footprint of our housing stock whilst likely also leaving us to get the maths wrong about what that footprint is. The reflections in this thread highlight what a key part good BC processes are to any drive to reduce emissions. -
Single glazing? Wooden frames?
-
I'm just doing mine with 100mm rockwool, decided against celotex for reasons you mentioned. And also I had a shedload already... Ended up being a far bigger job than anticipated, boards were impossible to lift so cut out, then joist ends rotten and sleeper walls crumbling so have replaced whole lot. And of course not enough ventilation. Did mean I've put slightly thicker joists (4" Vs 3"). Need to get it back down before it gets too cold!!
-
Not completely clear but looks like a solid not a cavity wall? If so please don't coat it with sealant or damp resistant paint. Lots of info online but if a solid wall you do need to tread carefully to not cause further problems. (We had similar issue with render and knocked it all off easily, but consequently soft bricks below were very spalled. Had it redone in lime. Painted now with silicate paint. Very happy and so far so dry.)
-
Hello We have three salt glaze pipes that run under our driveway to the drains. House is approx 100 years old and presume these are original. I had a CCTV drain survey and the chap said they were in remarkably good condition. No concerns at all. Which was nice! I'd now like to dig up the driveway and replace with gravel grids on compacted MOT and Terram. I've done this on half the driveway already and really happy with it. But that half hasn't got any pipes under. How careful do I need to be about the pipes under the driveway? We have sandy soil. If I wasn't being careful is use an electric compactor etc to do it properly. Advice greatly received.
-
And thanks, sorry I didn't make clear in original post i wasn't keeping old cable under new floor.
-
Thank you both. Just for context: Loads of problems with the setup when we moved here but mostly new circuits upstairs wired to a new CU. All tested and all good. I could make a list of the horrors unpicked for entertainment value but might need a new thread. The ground floor bit I'm looking at hasn't been touched for years and the bits I'm adding will be with new wire. I won't be using old wire. It's this I want to make sure I'm clipping/securing right. Whilst the first socket in this room will be connected with the existing old wire for a time, once we do the other room it'll be easy to then get this section also replaced as easy access to the boards near the CU. Just want to do this section right before I fix boards back again ...as ProDave I do not want to have to lift this again as I am indeed insulating. Any other advice always welcomed of course...
-
Thanks so much. Perfect.
-
I'm looking at extending an existing radial circuit whilst I am working on a ground floor suspended floor. Current cable is sat on the soil. Presumably it is better practice to clip this to underside of joists? Or even use a ventilated cable tray, or is this overkill? Circuit is on a 20A RCBO. Currently serves two rooms with no high demand appliances. Plenty of space in the CU, would there be a benefit to asking a sparky to split the radial in half so each room is a separate circuit (currently single circuit with two cables at the RCBO). Thanks
-
I suspect others can impart more wisdom than me but I'd just follow the advice on the cement packet. I thought 5 to 1 was standard for cement (I have a older 1920s house with lime mortar so have used an NHL lime mix with no cement) Does the damp inside correspond with the lower part of the wall? Is the mortar crossing the DPC? I would not use any sealants personally.