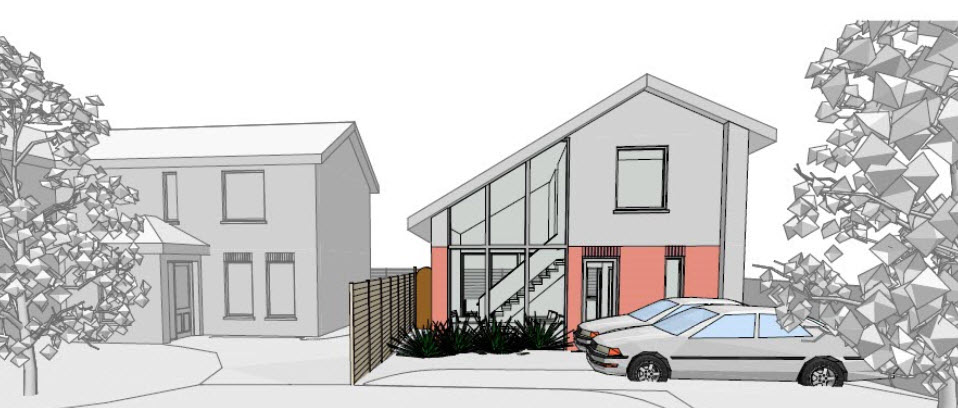
mike2016
Members-
Posts
621 -
Joined
-
Last visited
-
Days Won
3
mike2016 last won the day on March 15 2024
mike2016 had the most liked content!
Personal Information
-
About Me
https://passiveirishhome.blogspot.com.
-
Location
Ireland
Recent Profile Visitors
The recent visitors block is disabled and is not being shown to other users.
mike2016's Achievements

Regular Member (4/5)
167
Reputation
-
With a few hot days I decided to plunge into fixing the outside drainage. These had been marked the wrong way around on the surveyors map which carried onto the Architects drawings which made its way into the construction drawings and the groundsworker dutifully connected up as per these last year. It was only a few months ago I noticed backflow of sewage in what I thought was the storm drain and discovered the difference between 4" sewer lines and 6" storm drain lines!! Unfortunately the 4,000 litre rainwater tank is already installed and the invert levels between the two systems are very close to each other so I was going to have to bring the rainwater overflow under the sewer line. That's what I started tackling today. The shores are to the left and the rainwater tank is to the right. The sewer is to the top of the picture so I can now connect that up next. I've also allowed for a direct feed into the storm drain from the front drains (more likely to get oil/car wash soap/contaminants in it) and the overflow from the rainwater filter (only 40% of the rear roof will make it into the tank through this filter, the rest is discarded via this overflow). The U bend might be hard to clean out later but I'm looking for a sump for the front aco drains to minimise sediment, similarly the rainwater filter should block leaf debris from the rear roof. The Wet Room work is being undertaken by a contractor so they have been hard at work all week. Just waiting on my plumber to finish a few bits and the tilers to get started. I've been painting the ceilings in advance so I don't mess up the tiles later and I've been asked to cover the marine ply boxing I've done with backer board 6mm so I'll do that shortly. I've also been busy using 2 tonnes of Fermacell, 100 one man boards (900mm x 1200mm) fitting out the 3 bathrooms and utility room. You install by placing, gluing, screwing, joint filling, fine surface finishing then priming and painting with some sanding thrown in. I bought a plasterboard lifter which has been great for the ceilings. Even these board sizes are over 19kg each. I'm getting better results as I go. The cutting is messy and playing havoc with my plunge saw and I've stocked up on vacuum bags and filters to help. I've multi tooled the sockets and holesawed the led lighting sockets without issue. Nice to see a room looking like a room and not a set of wooden partitions for a change! The collated screwgun has been a charm once I figured out I was accidentally setting it in reverse and it wasn't working! Very annoying for the first crucial screw per board! Stairs is ordered for July. Holding off on doors for now but considering one with a frosted glass center section for the main bathroom to let some light into the hallway. Kango'ing out the concrete for the downstairs shower was very tough on the guys. 3 days instead of 1 as the concrete was well cured. They stuck at it though fair play to them. Lots of dust! They also moved a drain so its no longer sticking out of the floor of the master bathroom so the finish will be improved. The tiling boss was over on Friday checking things over and keeps close tabs on the process. There was an issue with a Schluter heating cable being too long so rather than run it up the wall, I rush ordered a shorter one from the UK and have it on hand for next week. Will have to ebay the old one! You can't cut these to length and I'd rather not pay to heat a wall I don't want hot so that's how that went! Still discussing with the original supplier as the same kit was ordered for both bathrooms even though one is 1/2 the size. These things happen though and it was only picked up on this week as it's been sat in a box for months! Hindsight! The Brise Soleil have been amazing and I've had all windows and doors open all week to help with the heat but it's never climbed above ambient outside, some of the bathrooms can be a little hotter as the windows don't open and there no airflow there yet. So next is the tiling, more outside foul drain work, finish painting the Utility Room and then I plan to prep the kitchen area so it can be measured and ordered. The 6 meter high vaulted ceiling will be fun to plasterboard but will see how it goes. I think I'll need more Fermacell at the rate I'm going, I've lots of offcuts, saving them but who knows if they will be used or not. No date on delivery of mains water or electricity unfortunately but hopefully soon. Be nice to get some power, they don't do temporary supplies easily in Ireland....! That's it for this post!
-
Week 2 - Foundations
mike2016 commented on Benpointer's blog entry in Contemporary build in north Dorset
I hate chasing companies to do their job and get me a quote too, often looking elsewhere and finding a better proposition to boot! Annoying though! -
I purchased a bare DeWalt first fix nail gun after trying to drive a single nail into a 45 x 45 baton. Glad I did. I only made it 1/2 way in - maybe the nails were too large a gauge but wow. Been using the nail gun for months and haven't looked back. Why it made sense to me was I've 2 x 5.0 amp DeWalt batteries already and didn't need a case / charger etc. Unless you wait for the sales have you any existing big batteries for a particular brand? Otherwise look for a deal with 2 x large batteries and a cordless screwdriver and then go for the nail gun after that. the bare unit is €385 currently in screwfix for me (DeWalt). The nails aren't cheap but you get loads in a box for @ €50. Hope this helps. Since bought a second fix nailgun (bare) for the next phase!! For the number of nails involved, rent, buy or borrow!! The only downside is I now have tennis elbow from the weight of the gun!!
-
Great job - really at the coal face and making good progress!!
-
Two Weeks Holidays and I only got to see 1 movie.....
mike2016 posted a blog entry in The Fun Irish (House)
I took two weeks holidays to catch up on some house building work and get some material onsite. Sometimes that worked, sometimes not!! The Plumber has already been and performed most 1st fix items and I'm centralizing everything back to central manifolds: Should make replacing taps etc a lot easier in the future I hope!! I was outside during the recent sunny spell and noticed my Brise Soleil doing their thing - the shadow modelling looks spot on for this time of year: I got a digger and driver for a day to dig out the front driveway and had 20 tonnes of 804 delivered to prep for backfilling around the house and to grade the driveway subbase. I ran the Electrical and Water service pipes / conduits at this time. While I was upstairs I did 1st fix on the MVHR outside vents using 150mm EPS conduit, realized the 92mm radial pipes to the rooms are going to make access to the manifolds difficult for commissioning later (restrictor rings are placed inside the manifold, not at the outlet/inlet). Will have to cut an access hole to reach in from the other side, will post pics once all is in place and hope it works! Will be a big of a spaghetti junction once everything is connected up! 4 pallets of tiles arrived but I had help from the merchant with those but I got a phone call that my plasterboard was arriving the day after. The Buildhub favourite - Fermacell !!! I hear your screams!! The only problem is how do I handle these on my own? A full size board is over 40 kgs, nearing 50, I'm over 50 and not that strong! So I ordered one man boards 900mm x 1200mm and it took a few weeks but I have 400 boards onsite, there's 50 per Pallet and 5 pallets arrived day 1 and 3 on day 2. Weather was thankfully good throughout. I purchased a plasterboard hoist for installation but I also needed to move them inside to keep them dry and safe. I googled and bit and found a wonderful DeWalt trolley and successfully moved 2 tonnes of Fermacell per day (each pallet is just under 1000 kgs!) 4 days later job done! About 5 boards per run was my limit, you need to keep an eye on the vertical alignment as you load up and offload or it will fall over, but as you move it the side clamp the sheets and it's rock solid. Perfect for brining them side in as at 900mm wide my old truck/trolley wouldn't let them past my front door, this dolly however made the heavy lifting much easier! I had to visit my Chiro one evening on day 1 but that was it! I've acoustic insulation arriving tomorrow hopefully, I'm ordering Luxaflex honeycomb blinds for tilt and turn windows on just one bedroom to see how they look / perform and how they fit. My window installer didn't recommend anything that inserts into the rubber seal, preferring limited drilling/screws or ideally 3m glue fixings. To find out which they use as the youtube video I saw showed gluing them on. Electrician 1st fix starts in a week so I've to get the MVHR vents in place as it's easier for him to route wire around vent pipes than it is for me to reroute 92mm vent pipe after electrical is run. I'm still digging out the sewer line to connect it to the correct outlet/shore and fix the fall. Tried getting a labourer for a day or two to help but failed. It's slow hard going but I'll get there! My site insurance runs out shortly so I've to extend that and plan for socket locations, figure out landing lighting (electrician doesn't like led fixtures in the service void beside the insulation) and get to grips with Fermacell in earnest!! Happy May 2025 !! Oh, and I went to see Warfare in the Cinema for a well earned rest!! -
Good point - I'm querying this with the supplier to see if there are studies / recommendations as smoke is my worry rather than fire. I'm going to opt for battery powered smart blinds so they will work even in a power outage / fault as I want to ensure the bedroom escape route through them is available as the blackout blinds have tracks either side so could be difficult to rip open if smoke gets into the bedroom without a tool / torch etc. Plus smart switches to turn on all the bedroom lights if power exists to help light the way down the stairs or find the smart blind remote control to get out the window onto the porch roof. I'm doubting much benefit for oxygen control / combustion, but positive pressure to keep smoke out of the bedrooms would be welcome except if its possible for an extract or other bedroom to start propagating smoke to other areas through the MVHR unit or manifold (nightmare scenario: no light, no power, blinds down, can't find controls to blinds and stairs blocked by smoke/flame, smoke coming in supply vent into bedroom, retreat into ensuite but all my ensuites have no windows openings so it's wet a blanket time and run or rip open the blind and jump). I think I've watched backdraft too many times!! I'm sure you can, or your calendar linked to an IFTT response, if detect temps > 600oC on the phone, pop a reminder the next day to check the MVHR filter!! If you can find it in the rubble of the house!
-
Bought the Aico EI128RBU relay module base battery back up and directed the electrician spec to install 4 core wire. RadioLink is not standard in Aico's so you have to pay for one as an additional item for each alarm to get all to sound together. Aico have their own landlord relay / smart system but it's proprietary and not linkable to Home Assistant. Any smart relay would do the job, I'm just using Shelly as I'm using them for outside security lighting integrated with CCTV human detection and other use cases and also want to power off my MVHR if the alarm sounds. Just working out how to use smart blinds if power goes to still escape out of a bedroom, but that's a topic for another day!
-
It's a fight with the body and the mind, each day! I find any day off site and shopping in builders providers is a nice diversion and taking a day deliberately out really releases the pressure but you always feel guilty you're falling behind where you need to be as other trades come onsite and you're trying to keep ahead of them! After full time work and then heading to site for 2-3 hours, coming home to a hot shower and bed with a hot water bottle on my back is bliss!!
-
The VSL is at the rafters. I changed the insulation type from Kooltherm to Gutex requiring extra depth. Might be missing a step worth of landing too, hadn't noticed that before! It's quite a long room so may just push back the wardrobes but will see....plumber arrives Tuesday so all eyes on that now!!
-
Thanks all - the photos cut off the landing a bit so I'm sure it's wide enough as the Architect did it!! Putting the hinge on the stairs side of the opening would match what TerryE did although my plan to put wardrobes on the back wall would be more limited but it is a long room so maybe that would work too?
-
I've 1 door upstairs and my insulation is encroaching on the door to one side at the top edge. This bedroom is at the top of the stairs so the best place for hinges in on the side closest to the OSB wall to allow easier room entry and not kill anyone coming up the stairs! Plus I plan to install wardrobes on that wall. I could do a pocket door or trim the insulation back 800mm and use a standard door but any other options? Thanks!
-
They look very well - what a journey! I spent 8 years looking for mine! Hope you like the tilt and turn (same type I went for). Just have to figure out privacy vs sun block blinds for working vs sleeping although your views are much nicer than mine! Congrats!!
-
There are two shores on my land that are the highest point in the run for the row of houses. The builder last year knocked into these shores to connect up my drains. My house in feeding in from the bottom and the mains are off to the top of the pictures. I plan to dig out the existing pipe to correct the fall and extend from the storm drain to the foul drain. Was curious about the sharp bend, once I excavate I'll have a better picture and agree any sharp corners are to be avoided although the concrete rainwater harvesting tank limits the bend radius a bit but will work to improve it. Cheers
-
I had a survey done a few years back and they misidentified the two drains at the rear of my self build property. This fed into the Architects drawings then used by the builder last year and I've only now discovered while trying to install rat flaps that I'm plumbed into the wrong one for sewerage. I've yet to lay the storm drains myself. I measured the distance and depths and have come up with the diagram below. I think I'm just about ok - currently the foul drain connects to the deeper storm drain and I just need to extend it to connect to the shallower foul drain. It's a sharp 90 degree bend then. Any advice / gotchas / am I ok / will this work? No experience with this so just checking my homework here! Thanks.
-
Well, it's been a busy month. I'm taking weekly Pilates to keep my back in check and so far so good. This is the first week I've taken off without any incidents to progress the house. This is the list of what I'm managing currently just to tickle my brain in a years time! Plumbers due to start any day - prep bathroom fixtures - a lot of boxes onsite! Met Electrician to get quote Electrician recommended kitchen design be finalized - booked appointment in showroom Went to get sample of Moso bamboo flooring but they stopped making their natural product. Wanted to use sample to choose kitchen door colour. Contacted the bamboo flooring company so they do ship to Ireland, working out how to get samples and if I'll float / glue and use natural or strand woven downstairs (have a bedroom downstairs to transition between if I mix) I think my foul drainage is connected to the storm drain outlet and visa versa - contacted Irish Water rep to check as plans say I'm right but the smell and sludge says otherwise! Insulation - started Gutex under roof install, walls 90% finished Getting ready to order MVHR but my preferred spot is very busy and could be too tight for all the pipes! Japanese Bath arrived, looks very nice! Bought spa reheating setup and pump Got next bank drawdown after single digit typo held up cheque requisition for a week Cracked a tooth, 50/50 if filling will hold or I'll need removal and root canal treatment! Find out in a week! Installed Rat flap 4" fine but the other pipe appears to be a 6", flushed out pipes with some water. For the external walls (internal buildup) I'm using a 40mm gap and a further 2x6 wall inside. I fill the gap with 50mm rockwool as a thermal break (220mm timber frame) and then add 100mm Moy Metac to hit my U values. I've to use Gutex under the roof in a 60+80mm offset layer with ejot screws & washers and then a 2x4 stud to hold it all in place. Both setups give me a 40-45mm service cavity although the 92mm MVHR pipes will need more carving out of the Gutex when they are installed. I installed Cellecta Screedboard 28 upstairs to provide soundproofing on the floor. You glue these together and leave a 12mm gap around the room edges for some yellow foam they provide. I ran out of boards and had to get some other boards (5) for the landing as I'd miscalculated and they only ship pallets. I also left a 925mm square gap for the ensuite shower. The boards are heavy (18kg each) - I had 42 of them but needed another 5 for the 33m2 area I wanted to cover. I might still add sound insulation between the Pozi joists but for now, I'm happy! My poor car has been taking a lot of runs to the dump lately, offcuts and waste just builds up. I finally got rid of 20 or so pallets lying around so the driveway is clear for work next month. Just need a working toilet to get rid of the tufloo! So, about to start first fix and have a lot of stuff on order / about to order to get me through that. Am choosing Fermacell but can get 2500x600 sizes locally. Finally - I nearly paid the 8K heating deposit to a Nigerian who had got in between the communication between me and the supplier. They asked me to send to a GB CoOp bank IBAN which I thought odd and then followed up that the invoice person was on leave and had I sent the payment yet, everything was ok their end and they were waiting. Luckily I phoned the supplier and we realized what was going on so nearly 8K lost, goes to show! I got lucky as the delay in getting my next cheque from the bank meant I didn't have 8K to send anyway! If something does add up - ring!