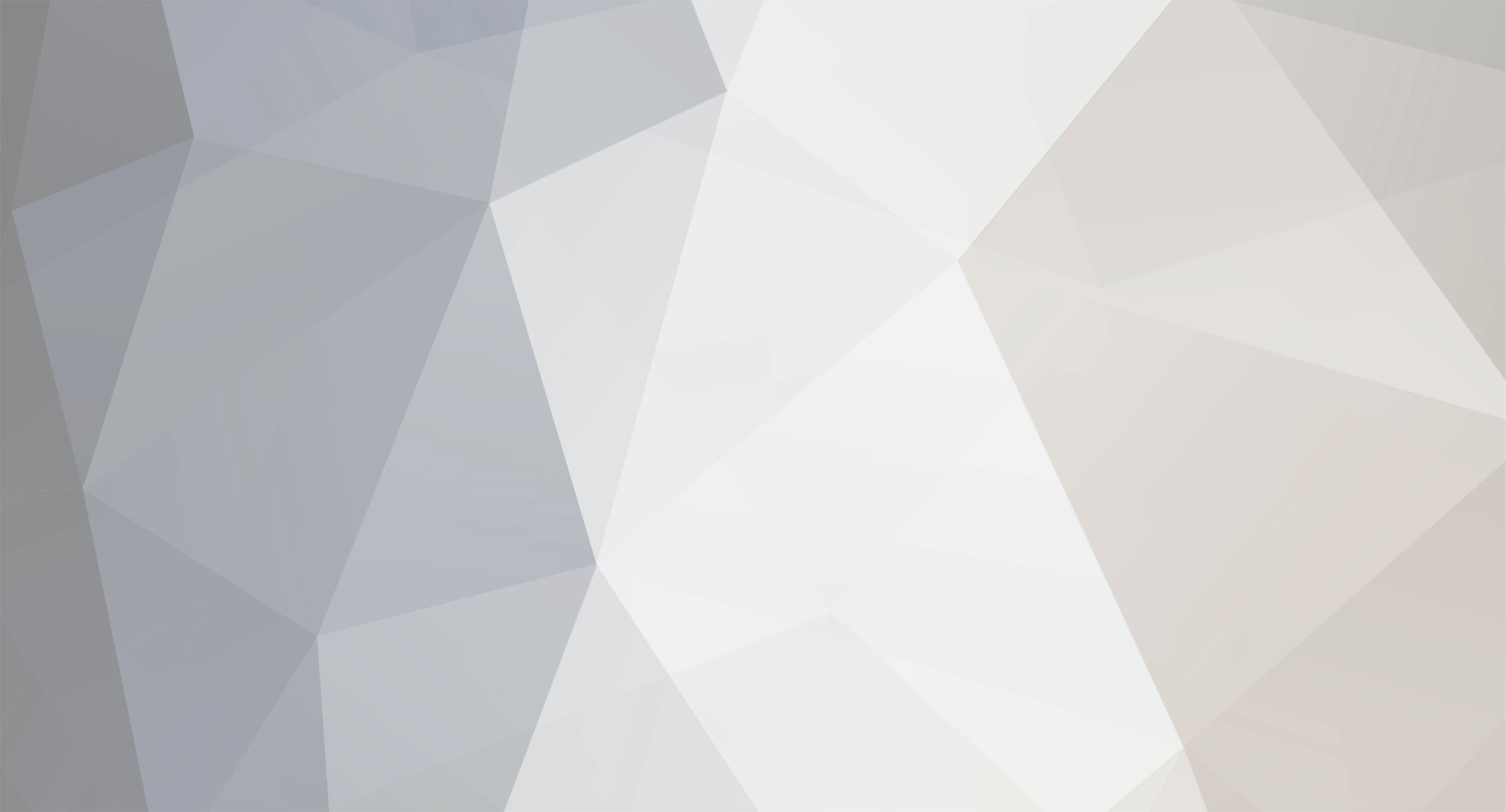
FM2015
Members-
Posts
152 -
Joined
-
Last visited
FM2015's Achievements

Regular Member (4/5)
66
Reputation
-
No restrictions really but at a certain stage and under specific conditions, an engineer might move towards steel lintels rather than cast in place.
-
ICF How much more expensive ?
FM2015 replied to Dave Jones's topic in Insulated Concrete Formwork (ICF)
As someone who has built my own house from start to finish, AND work for an ICF contractor I can safely say that there are very few self builders who become repeat business. I'll never build another house for myself, I've got one! Overheads do obviously contribute to the cost of service, whether that be advertising, equipment, office staff (🤫) or profit(🤫🤫) but a significant factor is also the uniqueness of every job. Architect's first time, owner's blue sky thinking and the idyll is generally not just off a trunk road with ample parking. Cost is therefore reduced by simplification and duplication and adoption of ICF for these sort of projects is critical for bringing product costs down for individual consumers. As a contractor, approaching developers comes with it's own set of overheads; h&s being a massive one and the corner most likely cut by a self builder. Not to be dangerous but there is no commercial risk attached to not having a risk assessment or all the other paperwork. And that costs. Therefore a reputable ICF contractor aspiring to deliver commercial multi unit projects is always going to be more expensive than someone with little experience or not concerned about working for the larger clients. The irony is that plenty of developers see ICF as a self build product and not a serious mass build option. Compounded by a potential labour force made up for first or part time ICF contractors. Until large scale opportunities exist nationally, offering repeat business, this isn't going to change. Chicken or the egg? There's a massive difference between too expensive and unaffordable and if a contractor quote comes back as high, it's important to acknowledge why; too expensive or just unaffordable, all risks covered? There is a reason why nearly 30% of the new housing stock in Ireland is ICF. It is because once economies of scale are reached, cost ceases to be the prominent factor. And anyone quoting embodied carbon stats as a reason not to use ICF needs to give their head a wobble. Rant over -
Several systems available in France.
-
Nudura external retaining wall
FM2015 replied to alayton's topic in Insulated Concrete Formwork (ICF)
Which ICF did you use? -
Although I appreciate that this is a largely self build forum and ICF is predominantly advertised as a self build product, there are are a number of benefits achievable through using an experienced contractor for ICF works. The main one, and especially pertinent to this thread, is the relationship. A contractor will have long term relationships in place which aren't necessarily based on "sell sell sell". My main point is that everyone has a bad customer experience story from self building but that shouldn't be counted against the product. In our experience, ICF distributors offer different levels of service dependent on location and personnel. It does hold the industry back. Putting a professional between yourself and the manufacturer is a safety net. Try ringing up ideal standard about a bath. You'll get more joy from the supplier more often than not.
-
Are brick slips dearer? Let's see!
FM2015 replied to John Keith's topic in Insulated Concrete Formwork (ICF)
So you don't have any evidence of your treble costs? We have a QS partner but this isn't worth bothering them about. Essentially you've got to build a wall for less than £100/M2 to compete with the OP's wall. Can't be done. -
Are brick slips dearer? Let's see!
FM2015 replied to John Keith's topic in Insulated Concrete Formwork (ICF)
By that rationale, 100m2 of complicated wall is the same price as 100m2 of simple wall. With ICF, 100m2 of 150mm core would be different from 100m2 of 200mm core. Simply not the case. I've already shown that the labour can be more for just the blockwork than ICF and haven't mentioned the weather. Factor in the labour of membranes and insulation and you probably have a 50% premium on the labour, minimum. I'm not being deliberately obtuse, I'm saying each job is different and we try and stay away from broad brush figures. With the figures that would we use and the approach that we take, we are broadly competitive and in no way close to double or treble the alternative. The moot point is quality and performance of the end unit. ICF converts will point to structural airtightness over membranes, and how so many stages are achieved in one product. I think if you have been quoted double prices for ICF, you need to go elsewhere. If it's what you've heard doing the rounds, it's a falsehood. -
Are brick slips dearer? Let's see!
FM2015 replied to John Keith's topic in Insulated Concrete Formwork (ICF)
What finish? What steel spec? How many corners? How many levels? What performance level? Access? Where is it? Define normal build? Stick or masonry? I have never hidden that I work in the industry and know full well that I could give you a meterage rate for a notional ICF build which would bare no relevance to the real world. Locally, in the last 6 months, we have had clients quoted £2.30/4" block labour only and £3. That in itself is higher labour rates than ICF. Add materials, insulation, cavity details, dpc, windows etc. The only true comparison is a rate inclusive of labour. I tell you what, you price up the OP's build in an alternative and I'll get it done in ICF and we'll see. Proper BoQ style, cards on the table. I'll plant a tree for every 10% price difference in your favour. Although I know that I can't plant half a tree. -
Are brick slips dearer? Let's see!
FM2015 replied to John Keith's topic in Insulated Concrete Formwork (ICF)
As with all things, warranty, regulation and manufacture all provide guidelines/stipulations and then there is the hierarchy to consider. Regulation and warranty both trump the manufacturer. @Dave Jones finished shell meterage prices are a bit of a misnomer. Generally speaking, to get to exactly the same state, the cost will not be dissimilar. I could provide a rate for a complicated ICF build in Enfield and someone could have a price for a simple stick build in Preston. Even the same building would have different costs in those areas. -
Are brick slips dearer? Let's see!
FM2015 replied to John Keith's topic in Insulated Concrete Formwork (ICF)
These numbers don't stack up! Single digit percentage premium on price for a far superior, longer lasting product. As per my earlier comment, if a house has 3, professionally fitted bathrooms and a professionally fitted kitchen to a medium spec, the client will spend more on these than the shell. All four will probably be changed within 15 years. You need a shell that will last that long. You can build a shell for less, agreed, and ICF doesn't suit everyone, but saying it is at least double the cost for negligible performance gain is poppycock. -
Are brick slips dearer? Let's see!
FM2015 replied to John Keith's topic in Insulated Concrete Formwork (ICF)
102 or 152 surely? It would be useful to give more build details to make the 20k/30k relevant to other users. Have you built this? One thing that I find nuts, no matter what the build system is, is that you can spend 30% on a veneer. Everyone seems to chase the structure down to lowest sum only to "splash the cash" on finishes. Previously had a client argue about £1000 (about 2%) before spending 67k(!!) on a rotating bath tub. -
ICF for a large detached garage - in the right forum!
FM2015 replied to graham-l's topic in Insulated Concrete Formwork (ICF)
@saveasteading you live in a 100 year old timber frame house? I'd always assume anything built in 1920 was better than it's 2020 equivalent. Not always true but we cut a lot of corners now. Timber is much lower quality product nowadays. I have nothing against timber frame. How old was the roof on the Notre Dame before it burned down? No steel or concrete in that. I also know about the struggles to find quality timber for it's rebuild. -
ICF for a large detached garage - in the right forum!
FM2015 replied to graham-l's topic in Insulated Concrete Formwork (ICF)
And it's a fair point. Although EPS manufacturing is actually done with a waste byproduct so you could argue it is better to make EPS than not make EPS -
ICF for a large detached garage - in the right forum!
FM2015 replied to graham-l's topic in Insulated Concrete Formwork (ICF)
Only if an engineer says so. There are a couple of products out there peddling this "truth". Ultimately, if an engineer says it needs rebar, it needs rebar. As far as sustainability is concerned. Saveasteading is right about the end of life options for an ICF build but bare in mind that 1, the life of the ICF build is at least twice that of a stick build, if not four times; 2, tree farming is one of the least sustainable farming practices on the planet and 3, an ICF done correctly will need less maintenance throughout our it's life.