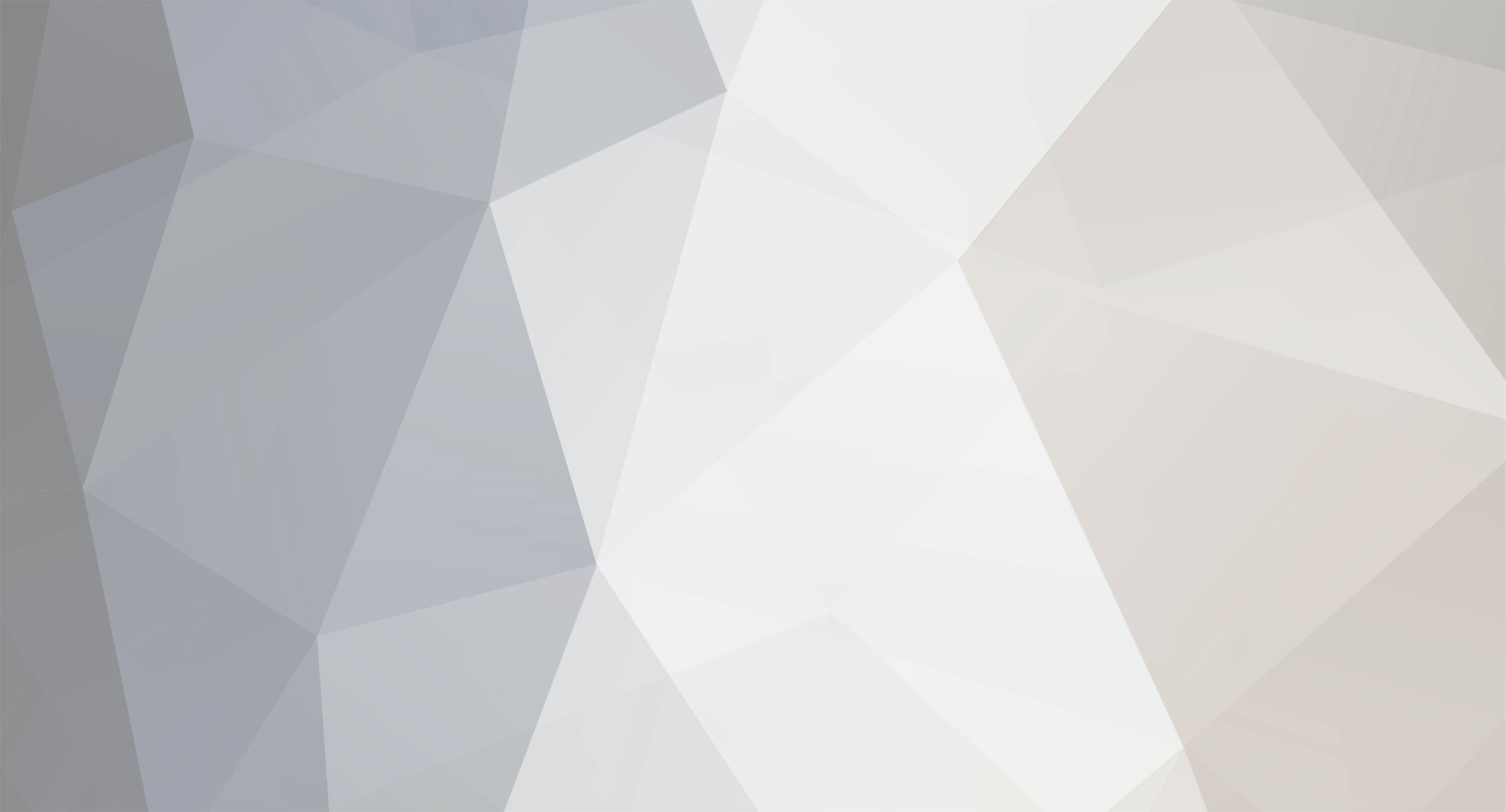
MG-Wales
Members-
Posts
29 -
Joined
-
Last visited
Personal Information
-
Location
Brecon
Recent Profile Visitors
The recent visitors block is disabled and is not being shown to other users.
MG-Wales's Achievements

Member (3/5)
7
Reputation
-
I am resurrecting this thread as I am in the same position as you: pocket door required to be FD30 as part of a protected staircase (3 storey house). What did you go for in the end? I am looking at Rocket Door Frames, however their FD30 frames are (at £410) more than 3 times the price of the normal ones (£145). They also require double plasterboard. Did you find out if it is possible to buy fire door seals and use them with a standard pocket door frame? How do these seals look like? The absurd thing is that we are in Wales and have mandatory fire suppression system which has already been installed, however the Regs still require the protected staircase. There is a sprinkler head within a metre of the door on each side!
-
I think they are the same broker in the insurance market. The company address is also the same. We had the quote from Buildstore automatically as we mortgage through them. I then requested a quote from Self Build Zone and the policy they suggested and the price was different. Also enquired Protek and Proaktive (Aviva) at the time but ended up buying from Selfbuild.uk.com which is backed by Zurich. Quoted prices for 18 months were between £1400 and £2300, with Selfbuild.uk.com at the lower end and Buildstore at the higher, all the others in between. I've also just discussed the renewal with Selfbuild.uk.com and the renewal price seems fair, so I will renew with them for another 9 months.
-
SIPS - Minimal eaves (no soffit and no fascia)
MG-Wales replied to Stephen23's topic in Structural Insulated Panels (SIPs)
Not sure if you're still after some advice on this topic. I design and engineer SIPS for different manufacturers and installers. Most SIP systems out there come with the panels machine cut and pre-rebated for the so called end timbers (typically between 40 and 50mm wide) to be fitted to facilitate the connection between individual panels and between elements, e.g. walls and roof. In your sketches you show one of the 2 OSB "skins" projecting. To achieve this would be considered non standard, and would probably require a manual cut and manual rebate of the panels, so, if at all possible, probably very time consuming and expensive to perform. Nonetheless, your design intention is achievable by simply fixing a timber fillet to the end timber, or an end timber shaped like a fillet, rather than relying on the continuity of the OSB. On top of this fillet an OSB strip can be fixed to make the top all at a consistent level. So, yes, I believe your details are achievable, but the individual elements of the SIPS would look slightly different. -
Update on the discussion about the day work with my stonemasons: they were claiming 22 hours total (for the last 7 days of work, so about 3 hours per day) and I've negotiated and settled for 16 hours in the end as there were some bits with the insulation behind the block/stone which they didn't do right and I will need to remediate from the inside. Overall I am happy they didn't claim an extortionate amount and I was able to get something out of it. In the end, I see this as a price to pay for not negotiating a contract and being there all the time to sort out issues with the site - both things would have costed me more in time anyway. First time self-builder, so some lessons learnt for the future stages.
-
Perfectly understand. I think I will pay some of the extra they claim for lifting, but will try to negotiate down whatever they are claiming. I just want to understand what is a fair amount. Do you know if it is true that bricklayers and stonemasons get 24/7 access to mechanical lifting (forklift/telehandler) in all sites (including private sites) these days? My worry with forklift hire was the hire cost for days in which they could not work because of bad weather, but even when I enquired about hiring one to finish the job there was a problem with the maximum covered for hired plant by my insurance. Surely this is a common issue? Next time (if it ever happens again!) I will surely look into electrical hoist hire as Russell Griffiths suggests and agree beforehand all lifting strategy and costs.
-
We are doing on a trade by trade basis. The only part for which we felt a contract was needed were the groundworks, as the value of the contract was quite big. Timber frame, windows and PV system were coming with their own T&Cs (which are effectively contracts?), so we could not force anything through but we were at least bound by a set of rules. For all the other trades (scaffolder, roofer, stove installer, carpenters and bricklayers - that's the list so far) I felt that a few email/messages with inclusions/exclusions/rates on top of (sometimes) a formal quotation would be enough. Everything else, e.g. extra work, I've always discussed and agreed as the work progressed. I've found that many trades try to force some extras at the end, whether it is some extra concrete poured in the foundations, the slates and halves installed on the roof, or the lifting of mortar buckets. I think it is unavoidable unfortunately - a sort of bad construction practice fee - , but they give it a go as they know that private client tend to pay rather than ending into arguments or disputes. I don't think they can do this with developers/main contractors. I think I will look into minor works contracts for electrician and plumber, as I see these producing a fair bit of extras as the works progress.
-
The cavity at foundation level is usually required if you are building a timber frame with masonry outer leaf or at least a brick plinth/dwarf wall on the outside of the timber frame, below the cladding. If you are saying you plan to use render board or other cladding directly to the timber frame, and there is no brick plinth/dwarf wall at the base, then I would say that the cavity construction below the DPC is not required. The other suspicious thing is that you say that the cavity is 150mm which is more typical of masonry construction (because of insulation applied on the outside of the inner masonry) than timber frame where the cavity is typically 60mm only (50mm clear cavity plus 10mm allowed for the sheathing). What size of blocks has the architect specified on the inside of the cavity? If it is 100mm then it sounds like it has been detailed for masonry, rather than timber frame. For timber frame he would have specified a 140mm wide block. In any case, I suggest you speak with your local building inspector about it. As a timber frame designer, I see many times buildings detailed for masons at Building Regs stage that suddenly turn into timber frame construction. Both systems are very well known, and for a small extension I am sure Building Control will be sympathetic with whichever system you want to use and able to advise on the specific requirements.
-
Yes, I agree. I don't want to piss them off, mainly to avoid a bad reputation as a client as they are local like many of my other contractors. Funny enough, they don't seem to be too keen to take on the pointing at this time. I think it is too weather dependent and I already said that I don't want to pay them on day work for that but I would only agree a fixed price. I might have already pissed them off actually! Has anyone here done the pointing themselves? It seems a meticulous but not particularly difficult job, but maybe it is one of those things one shouldn't even consider trying to do without any experience. When we discussed the lifting at the beginning of the month, it sounded like the forklift for the stone was essential and lifting the mortar was a secondary issue for which "they might get a pulley or something". Only 2 weeks ago - after nothing was done about it - it became a massive issue which was slowing them down significantly. I suspect they are trying to recover some lost money from earlier in the job (blockwork). Anyway, if I had to do it again I would definitely do it with a clear agreement on lifting all the material up. As soon as they mentioned the issue, I kept a diary of what was happening of site day after day, so I will check if their breakdown of hours matches what I've been recording and assuming.
-
The main stonework bit is finished, there is a small area of stone in the garage which will be built later in the spring / summer, but this could be done by others as well as a dwarf boundary wall. I also suspect it is to make up for time lost, especially during the blockwork part which was slowed down by bad weather back in December. I don't want to refuse outright as I think they did a good job, but I will try to negotiate if they go too high with their requests.
-
There was no mention of lifting on the quote, just the rates for labour. Very old school, but I find many contractors work like this and then is down to me to point out every condition on emails (which I admit wasn't done very thoroughly for this stage, lesson learnt!). My understanding was that heavy lifting, access (scaffold), water, power, would be down to me. I assumed lifting of the stone up the scaffold would be enough so I paid for the telehandler when required to lift 3 bags at a time and just at the very end they mentioned there would be an issue on lifting the mortar up as well. I considered to hire a permanent forklift / telehandler for them to operate, which would have been of similar cost (£600) to these extra they are claiming + the occasional telehandler with driver hire I had instead, but the barrier was the limit for hired plant on my site insurance as these machines cost more than £10K. So yes, I think they are trying to claim some of the money I saved by not having a forklift there for the 2 weeks, but - assuming that theirs is a fair request, as all the stone and some of the mortar was lifted at my expense - I want to make sure I am not overcharged / charged unfairly for it. For instance, for the blockwork part, I only paid out of my own pocket to lift the blocks, all the mortar was lifted up by the bricklayers without extra cost as part of their labour rate.
-
Hi everyone, just after some quick advice to check if the extra costs I've been told by our brickies do stack up. The stonemasons have finally finished working on the front elevation of our new build house, this is done with 150mm cropped stone (outside of timber frame & surecav) without pointing (too cold/wet for it at the moment). We're really happy with the quality of the work they've done, which was agreed on a m2 rate for labour only and us buying all the material. It was all good until they were working off the ground, however for the work done from the first lift of scaffold up (approx. 40m2 for which they took 7 days for 2-3 stonemasons plus 1-2 labourers) they started complaining and mentioning day work / extra hours they had to put in for lifting all the mortar up because of lack of mechanical lifting. Despite working without a formal contract, I do appreciate all lifting and access is down to me as they are paid for mixing and laying. All the stone was lifted mechanically with a telehandler to a loading bay on the first lift (approx. 24 sqm of wall) and then directly on the top lift (area 16 sqm) together with a decent amount of mixed mortar, but this happened only on 3 of the 7 days for an hour or so at the time so that left the mortar to be lifted manually for the rest of the time. They claim that this operation, which was done with fairly big buckets lifted up to the different levels, took up to 4 hours each day so about 30 hours total, which they want to bill me at £15ph labourer rate (this rate wasn't agreed beforehand). Their labourer are youngsters who are 18-19 years old, so I'm not sure if this is a fair rate, I can see that the average is about £12 and we are in mid Wales (not an expensive part of the country). They say that in all sites they worked on, this is the first one where they didn't have lifting equipment, which I struggle to believe. I can see private sites not having lifting equipment there all the time, surely this is more common for big sites? Is it possible that it takes so long to lift mortar up to the first lift and then second lift of the scaffold? I struggle to visualise how it can take hours to move mortar up and down, however I am sure stonework does require quite a lot of mortar. For instance, I think they used about 15-20 bags of cement and a couple of bags of sand for the mixes from the first lift up. I would appreciate some advice from more expert people here. :)
-
Thanks. It was done keeping in mind having a few cross ventilation options, and of course escape windows for the bedrooms. But most of the small ones will be fixed as we have MVHR and we are trying to be as airtight as possible.
- 29 replies
-
- 1
-
-
Thanks to everyone for the suggestions & help, we have decided to go with Norrsken in the end. Price has come down a bit when we changed half of the windows (all the front elevation) to outward opening instead of tilt and turn (both on their "300" frame series), still more than £850/m2 installed - however we do have small windows, so a relatively high frame to glazing ratio. Rationel were more or less the same price for a like for like specification and in my opinion they had the advantage of the frames looking sleeker and more of similar design between outward and inward opening, however Norrsken had better U-Values (0.81 vs 0.95 average based on areas) and glazing specification (low-e glass).
- 29 replies
-
I'm resuscitating this thread as I think we are narrowing down our windows suppliers' choice to these 2 companies (Rationel Aura Plus, via a distributor, and Norrsken). We have about 32 sqm of glazing (excluding rooflights, including one 3.6m wide lift and slide door to the rear) and although many windows are small (more frame than glazing), there are several which are fixed frames so cheaper. We have asked for all the openable ones to be tilt and turn because we like the idea of the double opening style and convenience of cleaning from the inside. We have now received both quotes and the prices are comparable. At the moment we are around £950-£1000/sqm for supply and install (which seems a bit high, definitely over our initial budget). We are thinking of changing all the front elevation ones and the ones on the gable to outward opening (a bit more traditional and apparently frames should be 10-15% cheaper with a similar U-Value), while keeping inward opening on the garden elevation. Norrsken seem be slightly better performing windows than Aura Plus (some 0.05 less in U-Values on average), probably down to the frames as both come with 48mm triple glazing. One big difference is Norrsken's lift and slide door which has 52mm glazing achieving 0.87 U, while Aura Plus has 42mm glazing on the openable panel, but only 36mm on the fixed panel which gives an overall 1.15 U which is a bit disappointing. Has anybody had recent experience with one of these 2 windows manufacturer? Are prices in line with what others have been paying?
- 29 replies
-
Help with drainage locations - slab being poured next week
MG-Wales replied to MG-Wales's topic in Waste & Sewerage
Thanks for your reply, that's what we're planning to do. I think it may be wise to add the additional drain under the utility sink as you suggest, this can also be an alternative drain for the toilet shower if it is unpractical to connect to the toilet svp. The cost of adding a drain run to the inspection chamber at this stage should be around £200 and it's not worth risking having issues with connections later on. The floor is going to be 253mm deep metal web joists (159mm space in between the flanges). Taking in consideration the span and spacing of the joists, I've modelled the drains and it should be ok to connect WC and bath in the family bathroom to the nearest SVP across the corridor. If this is not possible for unforeseen reasons, there is the option of dropping the ceiling over the kitchen and part of the dining, but I hope this will not be needed. The WC (and everything else) in the ensuite on the left hand side could also connect to a continuation of the SVP from the downstairs tolilet. This would be located roughly where the wall between the 2 ensuites is, which is non loadbearing. I think this may be a more practical solution than running the pipe all the way to the SVP in the vertical shaft.