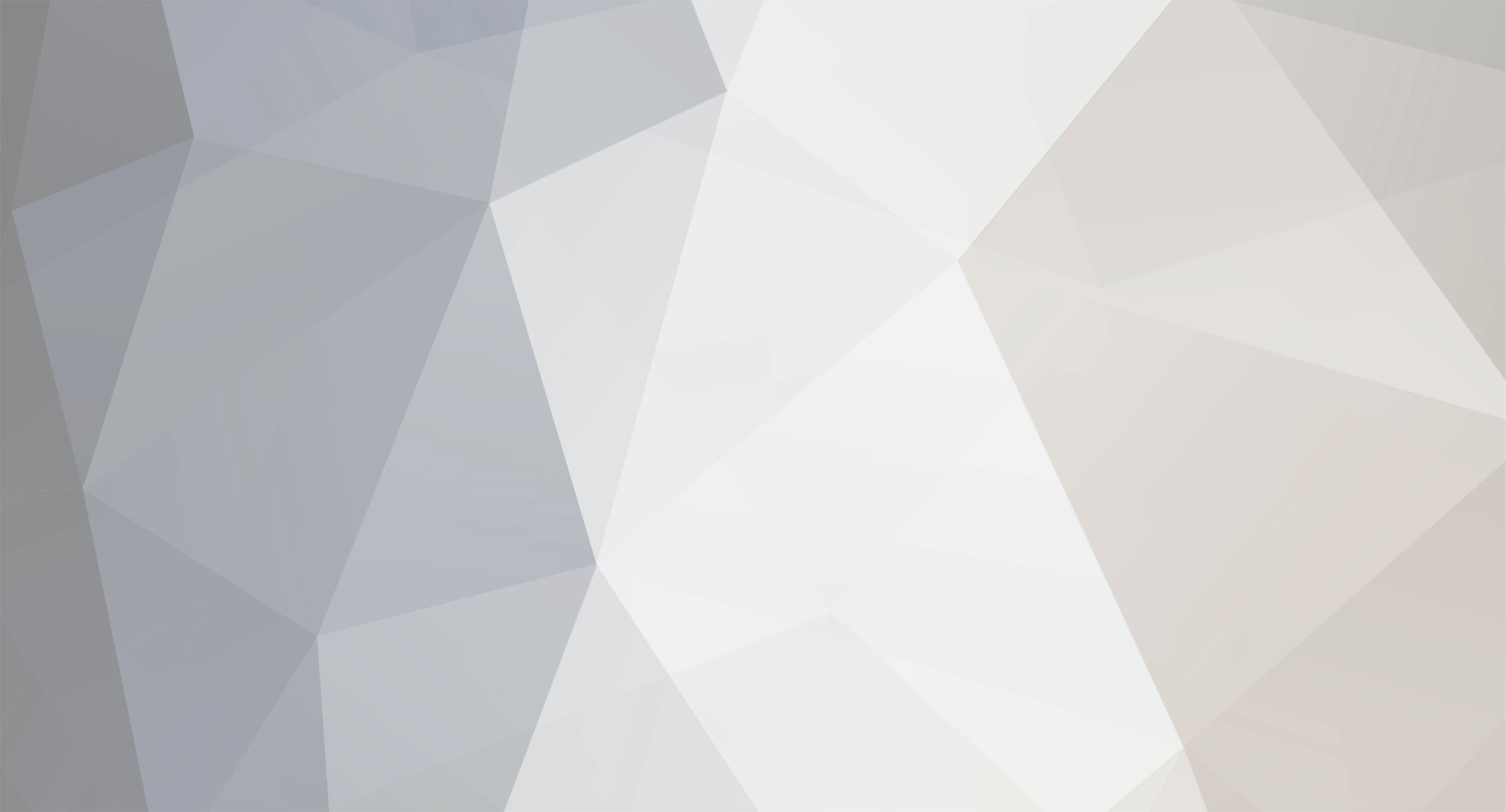
Reetster
Members-
Posts
11 -
Joined
-
Last visited
Reetster's Achievements

Member (3/5)
0
Reputation
-
Thanks for your reply Dave. The screed is laid on 22mm chipboard on 600mm spaced easy joists (253mm depth) I guess the thinking was although the ply is only fixed to the battens, as they are flush with the screed I didn't expect the movement we are seeing. I have heard some people lay underlay then carpet straight on the dry screed. The positive thing is that we haven't laid the flooring yet, so worst case could rip the ply up before we do.
-
Morning everyone Our house build is progressing nicely and we have recently had the ufh installed both downstairs in the traditional way (stapled to insulation, screed on top) and also on the first floor, in 25mm in between batons etc. We then screwed and glued 6mm ply to the batons to protect the screed and provide a sound surface for tiling/flooring. Although the dry screed was swept and hoovered before the ply was laid The problem we are now finding is a 'crunching' noise when you walk around, between the ply and the screed. Has anyone who has used this system experienced similar problems? Does it go in time? I don't want to get to a position of getting carpets etc down and still hearing the annoying crunch. Any advice/experience gratefully received. Many thanks
-
got a quote from them back in April, about 225msq worked out at about £20/sqm Plus delivery Plus extras I like the system, but my builder wasnt familiar with it and I went for a biscuit screed over chipboard in the end which I hope will give a similar feel
-
Cheapest most efficient way of insulating external walls
Reetster replied to Reetster's topic in Heat Insulation
@Mr Punter Thanks. Yes, Rockwool slab seems to make the most sense, probably best value too. How would you fasten it to the wall? Will it stay in place, total wall height will be approx 4.5m Cheers -
Cheapest most efficient way of insulating external walls
Reetster replied to Reetster's topic in Heat Insulation
@Hobbiniho yes, the 150mm timber frame will be insulated and will achieve building regs for insulation. Just seems a good opportunity to add another layer if not too expensive etc Plan view sketch attached Thanks for your thoughts.. Wall Plan view.docx -
Evening everyone. I am building a substantial framed barn conversion. Walls, built on a reinforced slab, are 150mm , insulated with a skin of 12mm ply, then felted. There is then about a 150mm cavity before a further 4x2 frame which will support the timber cladding. Im hoping to add another layer of insulation to this cavity, as it seems the right thing to do. What do we think will be the cheapest most efficient way of doing this? I was thinking of 100mm sheets screwed into the back of the plywood, whilst maintaining a 50mm air gap. Do I just plumb for a celotex type product, wood fibre or even a polystyrene board? Many thanks!
-
Thats what I need, thank you Now to investigate costs Thanks again
-
Thanks Don't have a drawing, but will get a sketch down. Slab is already cast so to use a system such as this we would need to drill into it. An piece of angle steel would work in theory though. Cheers
-
All ideas welcome I am progressing a barn conversion with the wall structure as follows. Timber framed house built on 300mm reinforced slab (450mm toe) within the footprint of a 28m x 9m existing timber barn, Posts of existing barn sits on existing separate pad foundation, so in effect we are building a house within the barn. Wall construction to be (from inside out) Plasterboard, 150mm insulated frame, 12mm ply, felt, secondary skin in between posts of barn - 100mm frame sitting on a brick plinth, which will have more insulation, ply, felt then batten ready for cladding. The problem we are having is what to sit the brick plinth on. To put in a small strip foundation we will need to underpin the existing barn pads, which are very deep. There has also been talk of using brick slips mounted to the existing new build frame, but Im now overly excited by this. Is there a way we can drill into the new reinforced slab, in between each bay (about 4.3m) to support some sort of steel or lintel on which we can build our plinth, and then 2nd skin wall above? Understandably, building regs don’t want to put any additional weight onto the existing original timber posts Any ideas welcome
-
Its done now, 2 layers of mesh with a ring beam and cross sections also. At least if I ever want to add a few storeys on top I'll be ok... Will know more about the roof tomorrow when Im meeting the guy along with my builder. Will probably need to add strength to the existing timbers (currently supporting Big 6 asbestos) Im hoping to have a raised seam look about it, similar to the Kingspan KS500-100 zip. Perhaps Sips was the wrong term to use, more like metal clad insulated panels.
-
Morning everyone. Great to have signed up at last, I have been following posts and threads as a guest for quite a while and found it very interesting. We have finally sold our house after Covid delays and just started our barn conversion in Essex. Its a timber frame 1960's built barn. Big, about 29m x 9m plus a single storey extension of about 11m x 5m. We have dug the floor down about 1m to give the upstairs more head room. Fortunately we have enough land to dispose of the 350 cubic meters of spoil! Foundation wise, rather than the expensive option of raising the barn up on scaffolding whilst we dig the strips around the edge, we are putting a reinforced raft inside. Anticipated it to be about 200mm deep, but structural engineer insisted on 300mm deep slab with 450mm toes and cross sections. Structure is going to be timber frame with a brick/block plinth and sips panel roof. Will be looking to ask lots of questions about heating, ASHP's, solar and much more Cheers