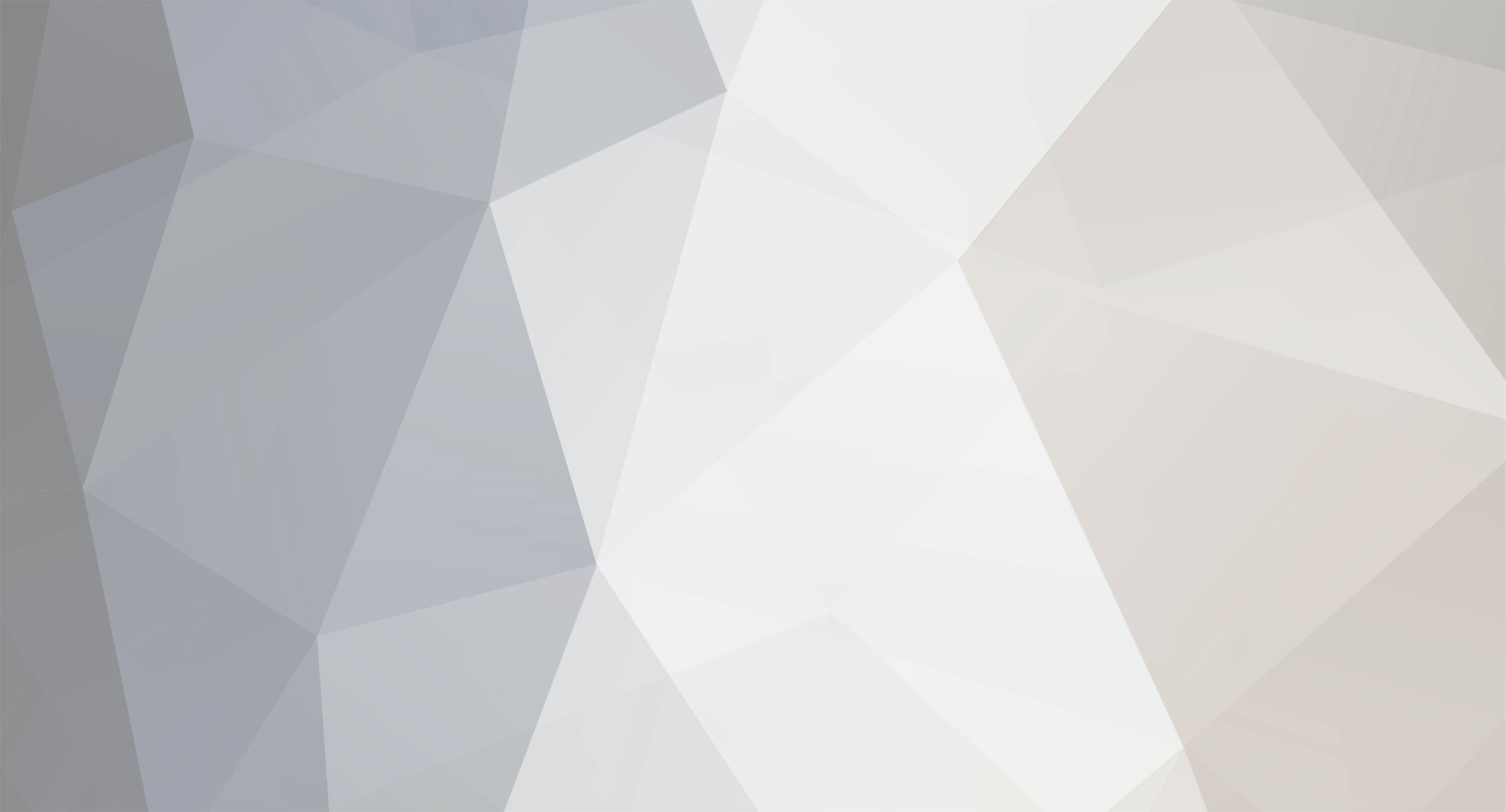
Jeremy
Members-
Posts
65 -
Joined
-
Last visited
Recent Profile Visitors
The recent visitors block is disabled and is not being shown to other users.
Jeremy's Achievements

Member (3/5)
2
Reputation
-
I've got a slope behind our house, which is just a few inches high at the lowest (East) point, rising to about 3-4' above the floor height in the house at the highest point (the Westernmost side of the back wall). The soil behind is gathering water which comes down off the hillside and we're getting various kinds of seeping (sometimes more!) ingress through the bricks behind into the houe. The obvious solution to this is to trench out the soil along that wall outside and install a french drain. I have in mind to trench out about 12" wide so that I can install the drain about 6" away from the wall with a slight slope directing water off the house to be safe. The question is, how deep should I go? I *can* go all the way down to 4' at the highest part of the slope, but I'm wondering if this might be overkill? Do I just scrape off the gravel and dig down to the end of topsoil? Should I try to get to bottom of subsoil?
-
It's Welsh hillside, so freely-draining loamy soil with grass on top, and hedging along the side above. Not a very extreme grade once I take the sloped part out, probably 3%, which I'll be smoothing to flat. Part of my reason for terracing the walls was to get a nicer visual impact and also keep the geotechnical engineering minimal. I'm imagining that 225mm thick will probaby be sufficient, provided I can get a decent angle for gravity mass, or pour a foundation with some rebar in it to take the pressure. I didn't include those details, as I gather the different kinds of block have different sort of engineering that goes with them. But the short version is, not massively complex for a wall, so not needing special kids of technology. Yeah, I'm doing gabions behind the house on another much bigger wall, but aiming for something a bit more in keeping with the structure (1830s Brick Victorian terrace). Was originally planning post and plank, but shifting to masonry, thus my query here to see if anyone else had tried blocks. It seems like some of the prefab blocks even have lego-like marks for stacking at the proper angle.
-
I'll be excavating some soil from a hillside in front of our house in order to add a driveway in front, so will be installing a retaining wall to hold up the soil. After surveying various options, I'm leaning towards using pre-cast concrete blocks for the build, either in a cantilever style or gravity mass wall. We'll be hoping to either add brick fronting, or get a block with a pattern on the front (like here: https://retainingwallsolutions.co.uk/retaining-wall-blocks/). I've found it difficult to find a lot of options online, though I gather there are many manufacturers. So I'm wondering what people on the forum have used, overall cost per m2 (I'm doing two walls at 900mm tall by 12m wide) and your experience working with the "technology".
-
I've got a 120cm range fitting inside a fireplace / under the chimney in our kitchen. Range is all wired up and ready to go, but I need to sort out what to do about the chimney and extraction. My original plan was to run it up the chimney, but after reviewing a few forums it seems like the amount of air I'd have to move to use this as a pathway for extraction is nearly impossible. The other limitation that I'm working with is that my partner wants extraction as quiet as possible - she hates the noise of kitchen fans (fair enough). So I'm looking at either running a recirculation / unvented fan in the chimney above the range (I've already got a low noise always-on Vent Axia Low Carbon Tempra going 24x7 in the kitchen) or, I guess I could run an inline ducted setup, which would have the benefit of being very quiet. But if I go with the latter, then what would I put in above the stove to install it? Just make a slimline box and paint it? Also 120cm range extractors are pretty expensive, so interested in creative options here as it seems like £1k is a lot to spend on an appliance that half the family will avoid turning on ever. All ideas welcome!
-
@ProDave Did you mortar in the slabs when you installed that?
- 11 replies
-
- ashp
- cement use
-
(and 3 more)
Tagged with:
-
That's what I was considering (something a bit like this: http://www.primagem.org/how-to-install-a-floor-drain-in-concrete-slab/) - can you detail how you tied into the rainwater pipes? My slight concern here is how to get gravity working for me on the drain if it goes below the slab. Does yours sit above ground level like @joe90 ?
- 11 replies
-
- ashp
- cement use
-
(and 3 more)
Tagged with:
-
Heh, that's the ASHP installer's problem. I just need to bring the supply to the install location... But probably out the wall, as there's a sewer/waste pipe just outside the cellar wall
-
That's new (but helpful) information to me - was planning on insulating around the hot pipes at 19mm with Polyethylene Foam, but it's pretty cheap stuff, so easy to do both. Is insulating cold pipes under suspended floors to prevent freezing? I hadn't thought about insulating the sleeve through the wall as well. Is that absolutely necessary? 40mm is getting to be a pretty big hole! Any good ideas about what to use for sleeving? Was originally going to just do a 28mm pipe... One wall is double brick, I think, so may need to think my way through how to get out a brick ...
-
Good point - it's funny what you don't think about even when you're staring straight at it! So I'll excavate down a bit (maybe 6"?) put down hardcore (how much? maybe 3"?), compact it, and then put down sand (1" maybe?). Manufacturer requirement is 150mm (6") away from the wall, so maybe I will also move the site further forward from the wall than that (maybe 12"?). General consensus that it's not worth trying to run a pipe for drainage?
- 11 replies
-
- ashp
- cement use
-
(and 3 more)
Tagged with:
-
I'm delivering water feeds (via Speedfit 22mm) for a newly installed unvented cylinder in a cellar under the front sitting room to a utility room in the back of the house also on the ground floor. This will involve four separate 22mm feeds (cold supply, hot return, and supply/return for radiators). The most sensible route for this is under floorboards as we have suspended timber floors over bare earth in the two front rooms, and then (as the house is built into a slight slope of hillside) an earth floor with quarry tiles. I need to drill through two separate masonry walls (somewhere between 5-9" thick) to get this route to the cellar, and am thinking it would probably be wise to run pipes through a sleeve, so we're looking at four 30mm holes in a row for just over 5 inches wide. I'm wondering if there is a more efficient way to create the gap for the pipes aside from simply drilling four adjacent holes with a 30mm SDS+ bit? Should I just remove a brick? This is my first renovation, so not really sure what options are out there! Any advice most welcome -
-
- 11 replies
-
- ashp
- cement use
-
(and 3 more)
Tagged with:
-
I'm installing a 16kw air source heat pump next week, and need to put in a spot to anchor it. I'm wondering if people can comment on how they've installed them and what has worked? I'm aware this ASHP will put off a lot of water (60-100l a day) and there's an inlet for sewer/waste water (it's a combined one system) about 4ft away from the installation point I've chosen. Should I put down some combination of sand, gravel and top off with cement? Or just small cement bits for the footings for the ASHP mount points? And what about water drainage? I can run some 40mm pipe from top of the pad, or a kind of soakaway. I'm just not quite sure whether 100l is too much to just drain in place. The ASHP is downslope slightly from the sewer inlet which is only about 2" below ground, so it's likely I'd need to run pipes above ground from ASHP. Would love to hear what you've done, and what has worked - and photos if you have 'em!
- 11 replies
-
- ashp
- cement use
-
(and 3 more)
Tagged with:
-
Lovely. I've even heard reports of subfloor made of a mix that included small bones! Were there any consequences of these random mixes that I might need to attend to? I'm planning to sift out earthworms and insects (though I suppose stone walls and quarry tile will provide a natural barrier) and then mix with clean sharp sand, but otherwise seems like the earth will sort itself out. Would love to hear from folks about what the best use of modern materials for a "cap" might be. Lime screed? Extra sand blind? Simply smooth it all out with a 2x4?
-
I'm renovating an 1880s Victorian house - it's solid brick masonry walls with (in most cases original) lime plaster on the interior, and in most places suspended timber floors over earth. It's a lovely breathable structure with some unwise modifications that have been added over time and have caused some problems, particularly for the mitigation of water vapour. I'm adding an air source heat pump with oversized radiators, to be powered eventually by solar PV to keep the house warm, and adding some individual mechanical ventilation with heat recovery devices to improve air circulation. There are air bricks in place which seem to be providing excellent ventilation to the subfloor where floors are suspended timber (no signs of rot after 100+ years). My current project is to address some serious damp/mold problems in the back of the kitchen, which rotted out the bottom/back of the previous cabinets (all now removed / recycled). The brick wall is partially buried underground, but also for some reason a former occupant installed a plastic membrane and concrete slab, presumably as part of a renovation on the cheap. The rest of the bottom floor is quarry tiles on bare earth. I'd like to remove the slab and membrane and reinstate the earth floor that was previously in place with quarry tiles on top. Here's my key question: what sort of soil should I install for the subfloor? I've been working my way through Crimmel and Thomson's Earthen Floors book to try and get a sense of things, and gather this should be a good mix of (mostly = 50-70%) sand, clay and soil (at 20% or less) and maybe fibres as well. I could easily excavate the soil necessary for this from outside the house and mix with sand, but wonder if there would be a need to address the biology in the soil? Also, for folks who have done this kind of flooring, what sorts of top layer have worked? I could do a thin lime screed on the new section, but the rest of the house is bare compacted earth, so am not sure if this is necessary. There's also some long term potential here for removing soil which is against the house and replacing it with gravel and a french drain, and improving guttering to the rear of the house but that's a way off for now. The back wall is quite damp and was producing mold (wet to touch at any given time) and I can't imagine the hydrostatic pressure from the current setup is helping that. My thinking is that if I open up the floor, it will at least allow for some additional evaporation which will be taken out by the active fan ventilation and by extension take some pressure off the back wall. I totally agree there will be more moisture in the air in the kitchen, but I think I've addressed this with the introduction of more active ventilation. Are there other possible problems that I'm not thinking of? Worth noting that I am planning to fix a membrane to the back wall, with 1" battens, woodwool boards and lime plaster skim as well to keep moisture away from the new cabinets I'm installing. Here's a visual showing the two different foundations in the room (seems likely there was originally a wall and the pad represents an extension added some decades ago, or a reeconfiguration of the room with an internal wall removed): View from behind:
-
19th century bathroom rebuild - what insulation/wallboard?
Jeremy replied to Jeremy's topic in Bathrooms, Ensuites & Wetrooms