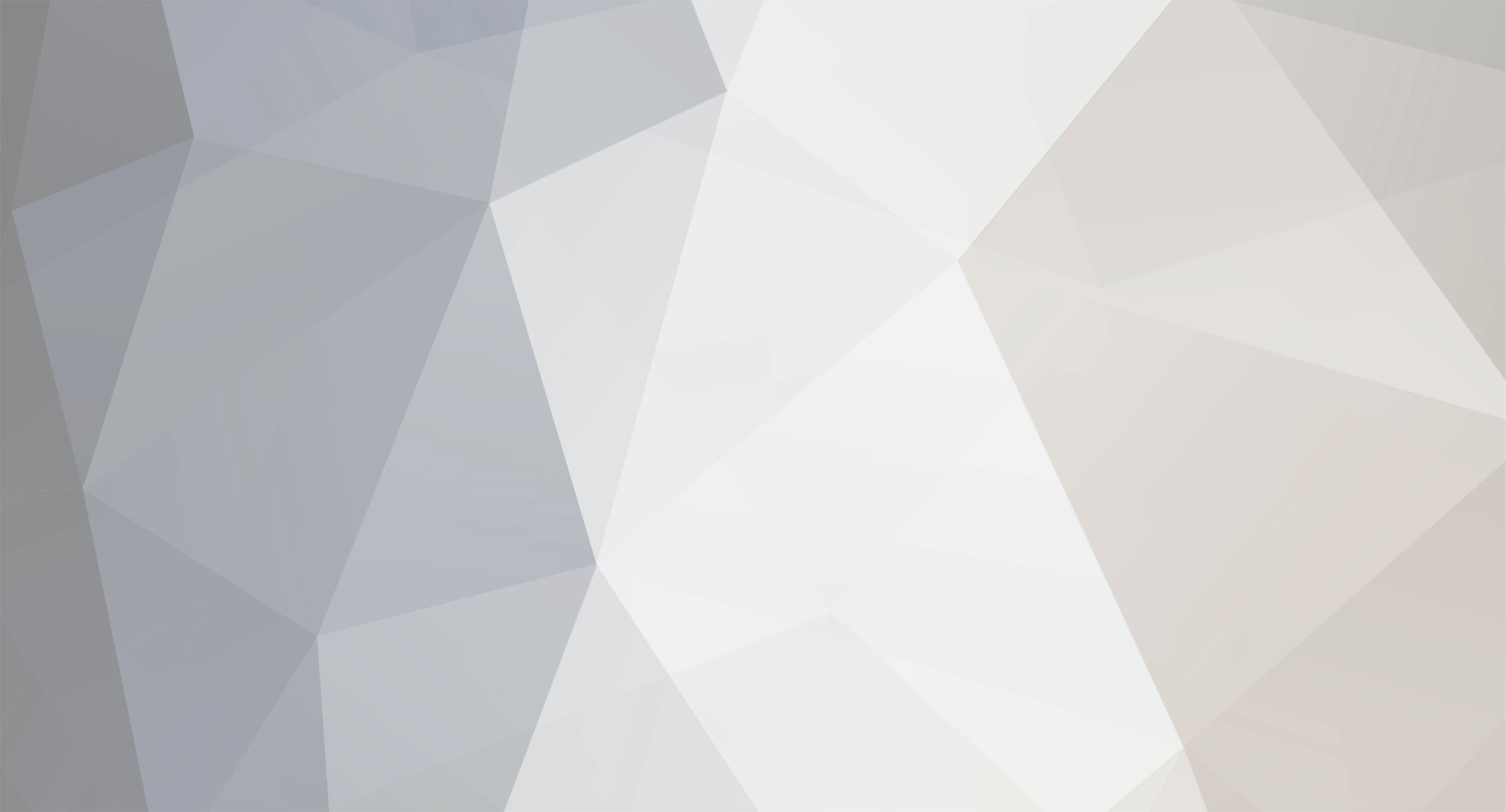
cbk
Members-
Posts
88 -
Joined
-
Last visited
Personal Information
-
Location
Shropshire
Recent Profile Visitors
8786 profile views
cbk's Achievements

Member (3/5)
5
Reputation
-
BCO has provided a checklist of paperwork required in order to get a completion certificate and the part J is included . I guess I just complete Appendix A myself and see if that’s OK,
-
I’m nearly at the end of my buil and this included a DIY install for a wall hung bio ethanol fireplace. But in order to get a Completion certificate I need a Building Regs part J checklist signed by a competent person. Any ideas on how to get a checklist completed and who is supposed to sign it?
-
I was planning to bury so UV may not be an issue, but not very deep so frost might be an issue. Also not sure which type I have as was left behind by plumbers. Is there an easy way to tell PEX from pert-al-pert pipe? Also can you get pipe fittings to join to MDPE for above ground sections with taps etc,
-
Hi, I’ve ended up with 3 part coils of UFH pipe and wondered if I could use it instead of MDPE pipe to distribute rainwater from my harvesting tank around the garden.
-
I tried the MCS guys and it turns out that my installer was not up to date with registration fees at the time of my install so no luck there. DNO has confirmed they will issue me an approval for export connection. So my best option seems to be to sign up to the Octopus list znd hope they invite me to join trial. I get the feeling that MCS are putting pressure on Octopus to shut down the trial.
- 20 replies
-
- 1
-
-
- feed in tariff
- octopus outgoing
-
(and 1 more)
Tagged with:
-
I’ve been trying to sign up now for several weeks and after initially saying all they needed was the G99 declaration ( which I sent) they now insist on an MCS cert as well. My installer has left the market and can’t issue a certificate so I’m stuck.
- 20 replies
-
- feed in tariff
- octopus outgoing
-
(and 1 more)
Tagged with:
-
That seems to make sense. The original announcement was more marketing than a real commitment to offer a new option to join an export tariff. Seems I will have to find an alternative route to get an MCS or Flexi Orb certificate .
- 20 replies
-
- feed in tariff
- octopus outgoing
-
(and 1 more)
Tagged with:
-
Hi, I have a DIY install for PV that I was happy to use a non MCS accredited installer to save cost as the SEG tariff was so low. However I read in Aug that Octopus Energy were going to offer 15p as a fixed outgoing tariff AND would accept just the EREC G99 declaration, as submitted to the DNO by the installer, to allow you to join up. Ive been trying now for several weeks to actually join up but get rejected and it seems there has been a change of policy at Octopus and only MCS or Flexi Orb certified installs are being accepted. They are suggesting as an alternaitive that I can add my name to a list for a £250 admion fee for future consideration withou any commitment as to when. Has anybody else managed to join an outgoing tariff without MCS certification? Is there a way to get a system retrospecitively certified by an MCS registered installer? Any ideas much appreciated.
- 20 replies
-
- 1
-
-
- feed in tariff
- octopus outgoing
-
(and 1 more)
Tagged with:
-
Ah good point. Will add Hardie backer on the floor as well.
-
Thanks for feedback guys. Good to know I've got the LiFePO4 type batteries which seem much safer. Additionally my loft space is a fully insulated warm roof so wont suffer extremes of temperature. But just to be safe I still plan to line roof with fireproof plasterboard or would it be better to use the HardieBacker fireprrof board which would save the need to plaster skim the board.
-
I've ended up installing my Inverter and batteries in a plant room created in the loft space. This is an insulated space and also includes the MVHR. Batteries are Pylon US5000 and I currently have two but hope to add a further two in the future. I plan to line the walls and roof with fire proof plasterboard and the access door will be FD30. If a fire was to occur this should contain things and the room has a smoke detector fitted, but as the MVHR is in the same space and ductwork is plastic this could easily cause smoke etc. to spread throughopuit the house. Should I aim to enclose the inverter and battery setup somehow to reduce the risk of fire spread? Or would this increase the risk of overheating and create more problems than it solves? Or is it a better optiopn to enclose the MVHR and keep it seperated from the Batteries? Any advice much appreciated.
-
Hi guys I’ve discovered that dpm layer under slab should have been a Radon barrier and looks like a regular 1200g membrane was used. Trying to figure out best option to resolve and keep BCO happy. UFH and screed have been laid but not yet the finished floor of porcelain tiles. Is there an option to put radon barrier on top of screed and under tiles? I’ve also read that if you have MVHR then this can be sufficient to remove any potential Radon and avoid the need for a Radon barrier under the slab. Any advice appreciated.
-
I've installed standard door linings to first floor bedrooms and plans are approved without need of fire doors. But new BCO is insisting that because I've put a staircase in to reach the loft space, then this now means all first floor doors opening to stairwell need to be rated FD30. Loft space is a mix of plant room and a gym/kids play room so not classified as habitable space. But BCO is arguing that it could be turned into bedroom space in future and hence I need to comply with regs for haitable space just in case. I'm at first fix stage so linings are in and plasterboard is nearly complete. I can add FD30 doors no problem but is there any way to upgrade the frame? Or must these be replaced? Or can I just argue that approved plans are for non habitable space and any change of use would need to address FD30 requirements in the future? Any ideas welcome.
-
Ive ended up with surplus EPS insulation - 25mm thick and now need to buy some soundproofing to fill stud work walls and first floor ceiling. Can I use up the EPS as sound proofing layer (even a double layer) instead?
-
Problems with how to finish reveal with aluclad windows
cbk replied to cbk's topic in Plastering & Rendering
I think it is 5mm for each edge but as supplier has gone bust I can't be sure. Will find out when the fitter starts to install. ✌ Thanks ProDave. Pics look a neat solution and I can see how this avoids the problem. WIll discuss with the renderer to make sure they follow the advice and I make sure they don't use any silicone either. I also have some timber clad walls which can easily follow the same principle. One wall is clad in stone slips which are about 15mm thick and will be pointed up with sand and cement. Will need to find a bead deep enough to cope with the depth.- 7 replies
-
- silicone render
- window reveal
-
(and 1 more)
Tagged with: