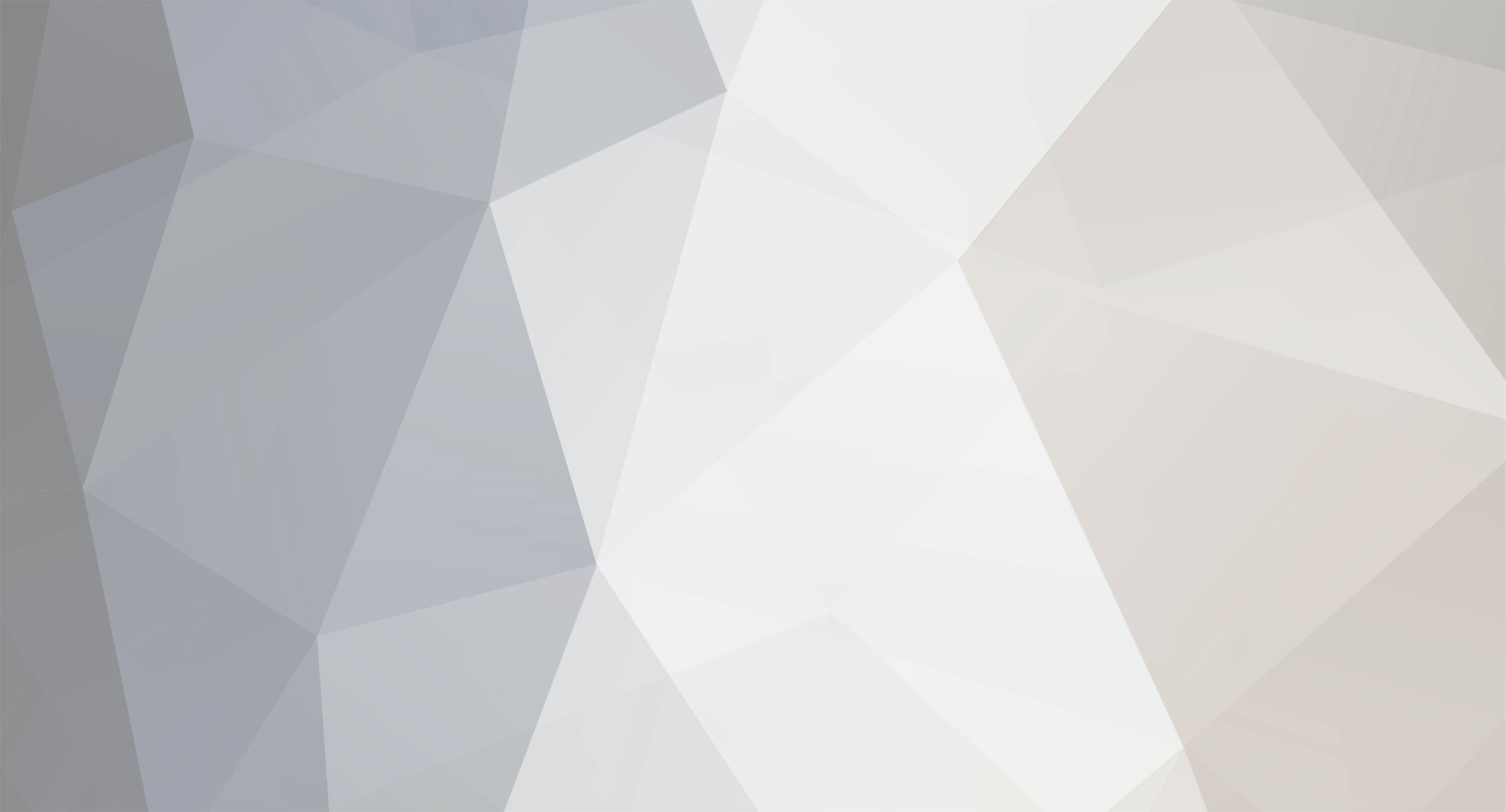
Barnacles
Members-
Posts
44 -
Joined
-
Last visited
-
Days Won
1
Barnacles last won the day on January 6 2020
Barnacles had the most liked content!
About Barnacles
- Birthday 07/21/1973
Personal Information
-
About Me
Serial renovator, carpenter, helicoper pilot, cabinetmaker, engineer and more... I have a passion for older houses and a desire to bring them into the 21st century.
-
Location
Forest of Dean
Recent Profile Visitors
The recent visitors block is disabled and is not being shown to other users.
Barnacles's Achievements

Member (3/5)
8
Reputation
-
New Home - "Upgrade" to Weather Comp or OpenTherm??
Barnacles replied to Barnacles's topic in Central Heating (Radiators)
I was going to launch into doing the switch to OpenTherm this morning but I got the look from my wife that says "it's really cold outside, if you mess this up and leave us without central heating....." 😄. Perhaps I'll wait until the weather isn't so harsh.- 19 replies
-
- 2
-
-
- central heating
- weather comp
-
(and 2 more)
Tagged with:
-
New Home - "Upgrade" to Weather Comp or OpenTherm??
Barnacles replied to Barnacles's topic in Central Heating (Radiators)
- 19 replies
-
- central heating
- weather comp
-
(and 2 more)
Tagged with:
-
New Home - "Upgrade" to Weather Comp or OpenTherm??
Barnacles replied to Barnacles's topic in Central Heating (Radiators)
Do you generally find the WC works well? Is your house usually at a comfortable temperature? Do you have radiators or UFH?- 19 replies
-
- central heating
- weather comp
-
(and 2 more)
Tagged with:
-
New Home - "Upgrade" to Weather Comp or OpenTherm??
Barnacles replied to Barnacles's topic in Central Heating (Radiators)
Good point, I'll be sure to know exactly what everything needs to do before I change anything. My understanding of OT is that there are just a pair of wires from my Honeywell control box to the boiler and they do the "triggering" of the boiler and presumably some sort of PWM signal to tell the boiler what temp to heat the CH water to. If that's the case then I can't see zone valve microswitches have any purpose. Hmmm, I'm off to find the instruction book for the Honeywell kit. 😃- 19 replies
-
- central heating
- weather comp
-
(and 2 more)
Tagged with:
-
New Home - "Upgrade" to Weather Comp or OpenTherm??
Barnacles replied to Barnacles's topic in Central Heating (Radiators)
And another thought. As most of my radiators have TRVs fitted, presumably I just set them to their maximum setting? Or remove the heads completely??- 19 replies
-
- central heating
- weather comp
-
(and 2 more)
Tagged with:
-
New Home - "Upgrade" to Weather Comp or OpenTherm??
Barnacles replied to Barnacles's topic in Central Heating (Radiators)
Yes, there are two zone valves. I'll check the docs on the Honeywell control box to see if it has info about whether the valves should be disconnected (electrically) when using OT. I suppose I could disconnect them and use the levers on the valves to open them permanently.- 19 replies
-
- central heating
- weather comp
-
(and 2 more)
Tagged with:
-
New Home - "Upgrade" to Weather Comp or OpenTherm??
Barnacles replied to Barnacles's topic in Central Heating (Radiators)
Sorry, I forgot to say that the house has radiators all round. They seem to be specced about right for the room sizes given the fairly decent insulation.- 19 replies
-
- central heating
- weather comp
-
(and 2 more)
Tagged with:
-
Hi All, We have recently bought a newly built "dolly house" which is equipped with an Ideal Combi ESP1 35 boiler with 2 zones (upstairs and downstairs) managed by Honeywell T6R wireless thermostats. I have been looking into heating controls for friend and got around to the learning a bit about OpenTherm and weather compensation. Then it dawned on me to check my own CH system and I was not entirely surprised to find that although both my boiler and thermostats support OpenTherm it wasn't being used! Clearly the plumbers weren't ready to embrace the new technology. I then learned that my boiler also has the option of weather comp too and this got me thinking. As it would cost very little and take minimal effort to modify my system to use either OpenTherm or weather comp would one have any significant benefits over the other? If it were your house which would you choose? The Honeywell control box is right next to the boiler so running a cable for OpenTherm would be a doddle and I can easily run a cable from the boiler to a north-facing wall for a temperature sensor for weather comp so either way would take no more than 30 minutes work.
- 19 replies
-
- central heating
- weather comp
-
(and 2 more)
Tagged with:
-
Yeah, I have a local sparky who I've worked with in the past. He's happy for me to do the work and he'll inspect it and sign off if he's happy. I just don't like to pester him as I appreciate that he's a busy bloke. I'd rather go to him with a plan of what I intend to do and know that I'm on the right track than ask him to spec the whole job for me. There's no info at all on the specs regarding the startup current. We had an ASHP 10+ years ago (at our old place) that was non-inverter and pulled about 6kw when running. I dread to think what the startup current was on that but the neighbours did wonder why their lights kept dimming and certain times of the day! We swapped it out for a gas boiler and never looked back. ASHPs have come on a bit since then I believe. Reading about compressors and their startup currents they usually quote a SLA (Starting Load Amps) of around 2-5x the normal running current and RLA (rotor locked amps) at nearer to 10x. But, I gather that if it's drawing anywhere near it's RLA it is probably not much longer for this world. It's actually a wood-fired hot tub with a small in-line electric heater. I'm doing away with the stove (fine in the summer, a right pain in the winter!) and probably the heater too so I'll just have two 50mm pipes sticking out of the side that I can connect the pump/filter/ASHP to. Should be pretty straightforward - famous last words! If I was starting from scratch I would do just that but I already have a 1.5mm2 SWA to the tub for the lights and the small existing heater. It's not a huge job to replace it I suppose but I'd prefer not to if I can get away with it 😀.
-
Hi All, We have a small hot tub and I've decided to add a ASHP to reduce running costs. The unit that I've bought is rated at up to 8kW heat output and the electrical draw is rated at 1.32kW. It isn't an inverter model so there will be a bit of a thump when the compressor fires up. The cable run is about 10m. I've read a lot about it but I can't find a definitive answer; do I need to go larger than 1.5mm2 SWA to supply the ASHP? Obviously the start up current will be fairly substantial but will it be more than the 1.5mm cable (rated at 27A when clipped and in free air) can safely handle? I'm leaning towards using a 10A D-curve mcb, would that be sensible? The only specifications supplied in the manual are: Input Power 1.32 kW Power Supply 220-240V / 50Hz Current Rating 5.9 AMP Thanks, Paul.
-
ASHP with RHI - Restrictions on Other Heat Sources?
Barnacles replied to Barnacles's topic in Air Source Heat Pumps (ASHP)
The house is a 3 bedroom cottage that has recently been completely renovated. There is a MVHR system and the whole place was extensively re-insulated and underfloor heating installed. I'd say it still isn't super air-tight but for an old house I'd say it should perform reasonably well. I have no idea what the actual energy consumption was in terms of kWh but I could ask and find out, she did say that her electricity price was fairly standard so I'd assume around 30p per kWh. That makes sense. So if she installed a small stove in one room and used it for 3 or 4 months of the year, in theory her RHI shouldn't be affected too much and as long as she declares it on her annual declaration she should be all good. -
ASHP with RHI - Restrictions on Other Heat Sources?
Barnacles replied to Barnacles's topic in Air Source Heat Pumps (ASHP)
Thanks for the replies everyone. It didn't make sense to me that she shouldn't be allowed to have a stove or PV installed. I'm going to nip over tomorrow and give her the good news, she'll be delighted. I'll mention the solar thermal too, I've a feeling that she may have a spare coil on her cylinder to accommodate it. I think the person who set up the ASHP should be flogged! Last winter she was paying over £1500 per month to run her ASHP and it's not even a large house. I went and had a look at it and found that it was set to output water at 23 deg C so it had been running virtually the whole day without actually heating the house. The DHW was set to come on for 30 minutes at midnight so it had been using the immersion to heat the water instead. The room thermostats were all set badly too so we configured all of those. She's now paying more like £300 per month but that still sounds very high to me. I think she needs to get an expert to set the system up properly. -
Hello all, I was just chatting to my neighbour and we got on to the subject of her ASHP. She's had it operational for about 2 or 3 years and qualified for RHI for which she is receiving her payout from Rishi & Co. We'd been talking about firewood and I asked if she needed any, she said that she wasn't allowed to have a wood-burning stove (or any alternative source of heating!) under the conditions of the RHI agreement. Does that sound right? She mentioned how much she was spending on electricity each month to run the ASHP and I almost passed out! I suggested that she should consider PV panels to help power the ASHP and again she said that under the RHI agreement she couldn't install a PV system. This seems utterly illogical to me, is my neighbour misinformed? Thank you, Paul.
-
Hi All, We are building an extension to our kitchen and as part of the works we are looking to relocate the CU, electric meter, incoming supply fuse etc. I would like to install a new recessed meter box into the wall of our boiler room (it's an oil fired boiler) which is constucted of a single skin of 4" solid blocks. The CU has a new location in the house but everything else will be in the new meter box (including a KMF switch as CU will be some distance away from the meter). Our DNO have said that we can locate the new meter box anywhere on the gable end of our house that suits our works. Firstly is it acceptable to install a recessed box into a 4" wall as the back of the box will be stuck right though the wall? Secondly, is there any problem with being relatively close to the boiler. I've searched the web and can't find any reference to oil boiler and/or flue distance to meter box. Is there a regulation for it? The meter box would be approximately 300mm horizontally away from the flue and there would be about 150mm between the back of the meter box and the case of the boiler. Any advice would be much appreciated.
-
Construction Method and Lintel Advice Please
Barnacles replied to Barnacles's topic in House Extensions & Conservatories
Thanks All. At this point I'm seriously considering doing it myself but I'll sleep on it a while longer and see how the hunt for a builder goes.