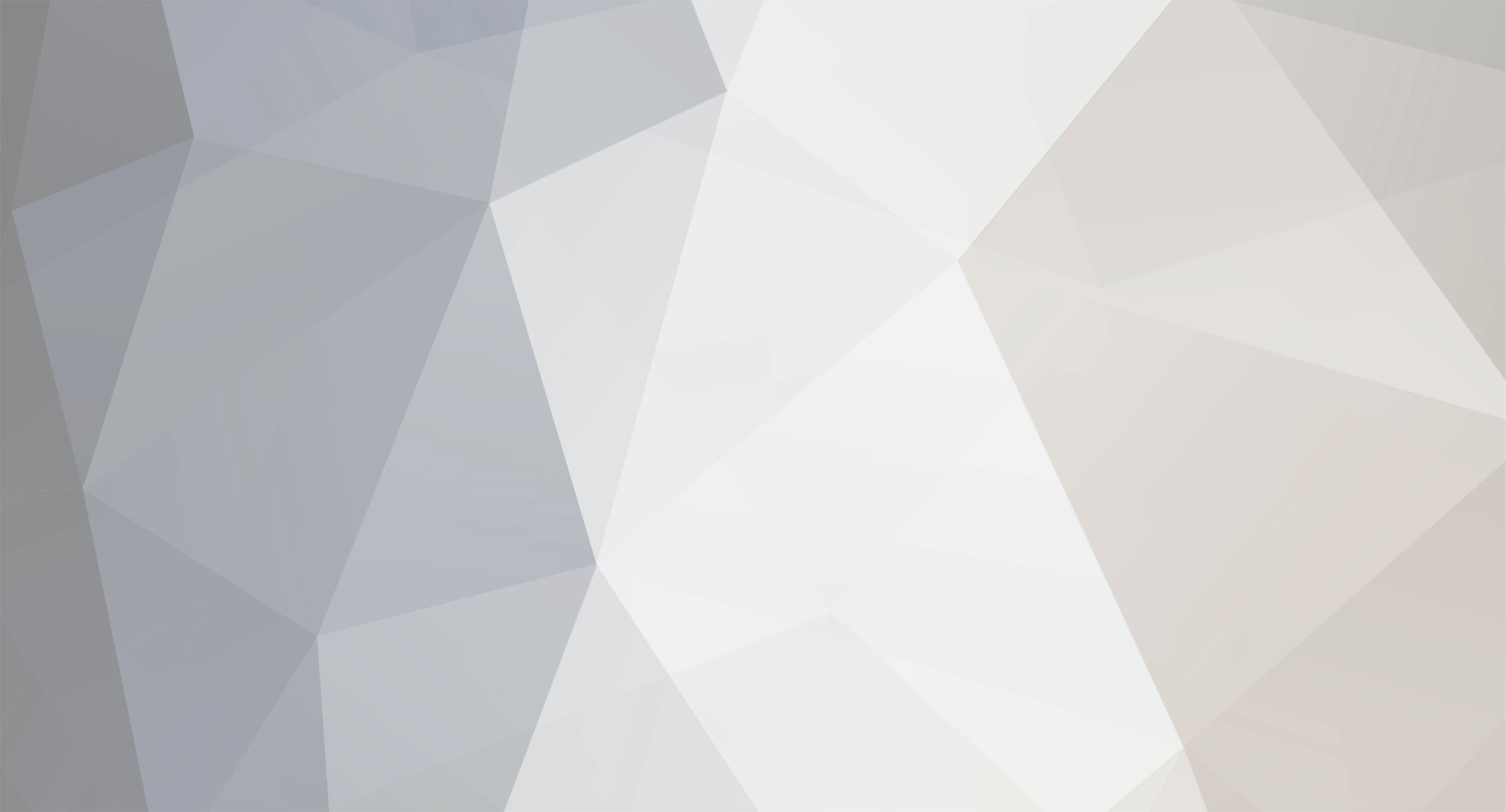
davejura
Members-
Posts
106 -
Joined
-
Last visited
Recent Profile Visitors
The recent visitors block is disabled and is not being shown to other users.
davejura's Achievements

Regular Member (4/5)
3
Reputation
-
Just jumping on to here rather than starting a new topic! We have attic trusses in our new build with the intention of converting a few years down the track. Our builder is saying we should put fire doors in now. But, our house is on a sloping site so we have an entrance on the first floor and ground floor. This means you would only be 1 storey away from an exit door if you are in the attic. Just trying to find out if we still need fire doors? Or maybe just on the first floor (which is the living area). We are in Scotland if that makes any difference.
-
The porch will be insulated. The main wall connecting the porch to the house is insulated and will have the airtight membrane right to the door.
-
I could probably have the airtight seal up to the internal door as long as the door had a good seal. I guess it could be taped for the airtightness test? Just think I'm going to struggle to make the porch airtight.
-
The main advice I need is regarding the porch which is on steel columns. Do i try and get that airtight or have an airtight door into the main house?
-
I don't, but I do think things have gone a bit OTT regarding airtightness! I am doing all the airtight membrane and taping, it's just some things he has done has made it a bit more awkward than it could have been. He is a very good builder and very thorough in other aspects. I'm using class O tape from Toolstation which I am finding fine. I see some people are spending £20-£30 per roll on fancy tapes. Are they really that much better? Will you ever recoup the extra money in savings on bills? Prodave, thanks for the advice. I will eventually do the loft as you have suggested but it's good to know we won't need the airtightness test for temporary habitation. That will help us get in a lot quicker as we can leave the loft for later.
-
I have a few questions about achieving an acceptable level of airtightness in our new build. Bear with me while I explain my issues! 1 - We have attic trusses and Velux windows, but our loft space is currently "storage". We will convert it in the future, but at the moment the priority is getting in. We are having all the walls and ceilings skimmed, so was wondering if the upstairs ceiling being skimmed would be airtight enough to pass? The builder seems to think so. All the walls have airtight membrane taped, so would just be the upstairs (living area) ceiling. Ii realise there will be light cables and spot lights. Is there a way to seal around these? 2 - My builder is old school and thinks the air tightness is a lot of nonsense (I agree with him to a certain extent) but I keep telling him you have to play the game. One of the joists is hard against the internal wall down the one edge creating a void that I cannot get insulation into (the other side had a gap that I stuffed wool into). Not sure whether to drill it and fill with foam (will take a good few cans) or just put a layer of 30mm PIR and the membrane over it? 3- We have a porch on steel stilts. The architect didn't specify how we are to deal with this regarding airtightness. Obviously it will be insulated, but am wondering if we could get a door that is well sealed between the porch and the hallway which would deal with this? Or do we need to wrap the whole porch with membrane. We have upped the insulation from what was required (from 100m to 140mm between and 25mm to 30mm on the inside) so will this help if we fail the airtight test? We just want to get in, even if it is on a temporary habitation certificate. I will then have the time to deal with the attic space and get it insulated and sealed properly. Any advice appreciated!
-
Our architect has specified the following make up inside the OSB of the kit. 100mm rigid insulation (we have upped it to 140mm), VCL, 25mm rigid insulation (we have upped to 30mm), 38mm sw batten service void, 12mm plaster board. My query is should the VCL not be on the warm side of the 30mm rigid insulation instead of the "cold" side? We are using Glidevale Protect and the picture on the packaging shows it directly below the battens (but doesn't show the extra 30mm of insulation). Just wondering if it actually matters which way it is done? Thanks.
-
Sorry, should have said there is a 12mm OSB backing board below Cromar vent 3 felt.
-
Hi folks. My roofer told me to get treated 19 x 38 timber for counter battens, then graded (stamped) 25 x 50 battens. Batten size is right according to the tile manufacturer and NHBC, but the architect specified 38 x 50. There was no specification for the counter battens. So the question is, are we OK with the non stamped 19 x 38 counter battens? And I can't see any reason not to use 25 x 50 battens, unless anyone can give me a good reason. Tiles are Northstone Donard on 45 degree pitch. Thanks!
-
Thermal insulation between occupied floors
davejura replied to Crowbar hero's topic in Heat Insulation
I'm now going with the Fastwarm Duo panels. They gave me a really good price on them to go with the UF heating, so is going to make life a lot simpler! -
Any recommendations for sealing round doors / windows plus filling gaps in insulation? Was just thinking Everbuild fix and fill unless anyone has any better ideas, without breaking the bank! Thanks.
-
Thermal insulation between occupied floors
davejura replied to Crowbar hero's topic in Heat Insulation
I'm now looking at battening the chipboard flooring, laying the UF heating pipes in screed and laying 20mm engineered flooring directly above. Would just have acoustic insulation below the chipboard between the joists. This is on the first floor (living area). Would this meet building regs in Scotland or do I need 25mm PIR board as well? -
Sounds like good advice. My fault for not researching acoustic properties of PIR boards! I would probably batten the 22mm P5 then lay 20mm engineered flooring directly on top with UF pipes in screed below. Should only raise the floor about 50mm. it's all a learning curve!
-
We are looking at installing a wet UF system all round in our new build. First floor is living area and I am planning on using a screed pug mix on 100mm PIR insulation. I was thinking that between the 30mm screed and the PIR, I would have enough acoustic insulation between the floors, but am now doubting this. Any thoughts? We have also temporarily put down 22mm chipboard flooring on the first floor to give a work platform. I have now read that the maximum floor thickness for efficiency of the UFH should be no more than 25mm. We are planning on engineered (probably oak) flooring and am wondering if we would be better going for 20mm planks and laying them straight on the joists. Again, looking for thoughts or experience! (Potential £1200 of chipboard flooring wasted!) Finally, heated towel rails in the bathrooms. Is it worth integrating them or just have electric ones? Don't want to be turning the system on (ASHP) just to dry a few towels. Just getting my head around everything again today after a couple of weeks away from it, and my head is fit to burst already! 🤣
-
Thermal insulation between occupied floors
davejura replied to Crowbar hero's topic in Heat Insulation
Crowbar Hero, just looking at your floor make up. We are doing the same, having a wet UF system on the first floor which will be the living area. I have just gone for 100mm PIR which will be supported by battens (no ply as the 100mm should be strong enough to take the pug mix and pipes). I haven't allowed for any acoustic insulation though, as thought that between the 100mm PIR and the 30mm pug mix, that should do the trick. Any thoughts anyone?