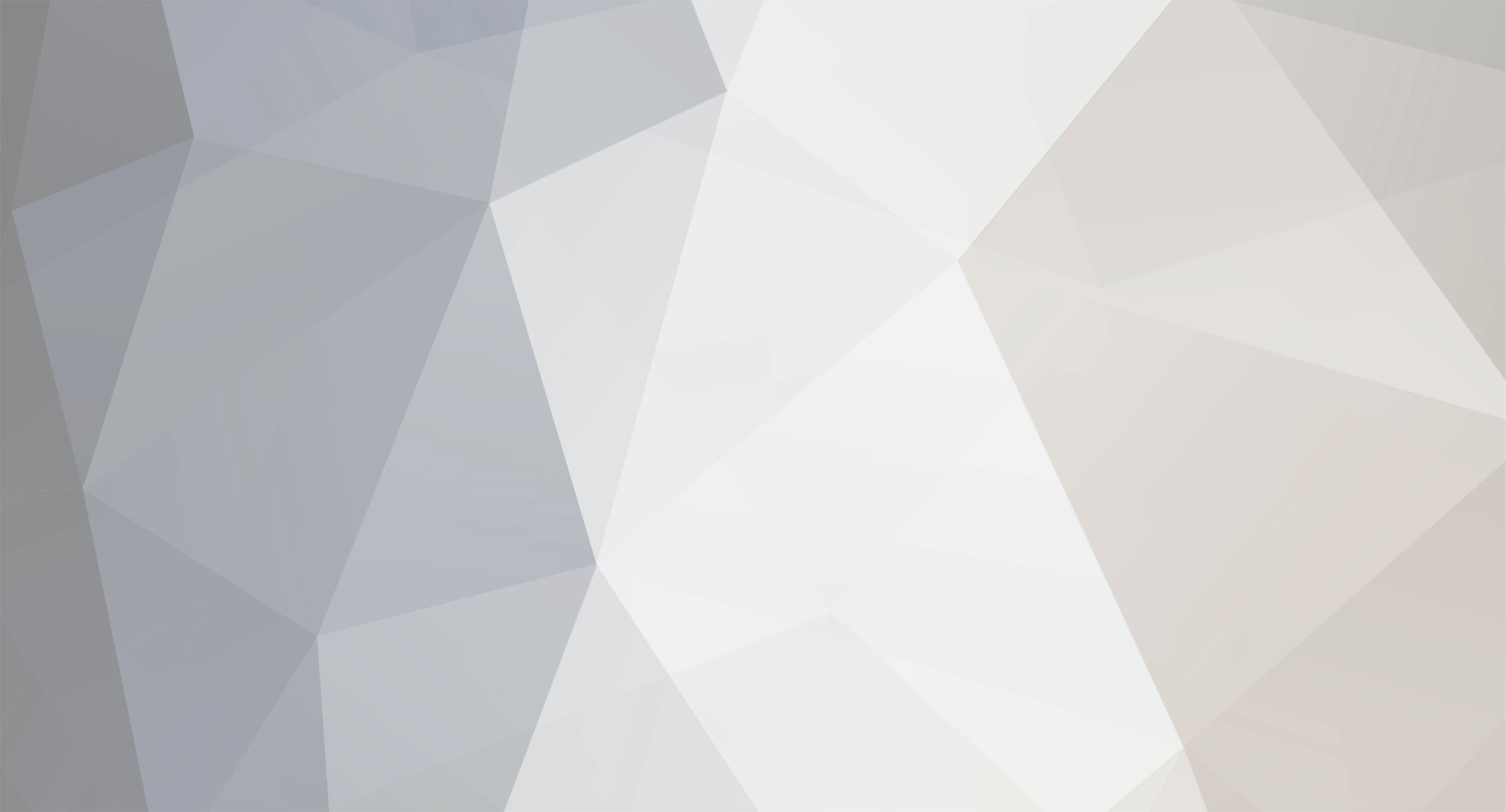
Smallholdertoo
Members-
Posts
33 -
Joined
-
Last visited
Personal Information
-
Location
Shropshire
Recent Profile Visitors
670 profile views
Smallholdertoo's Achievements

Member (3/5)
2
Reputation
-
Thanks you both. I was coming to the same conclusion which was confirmed when I saw a friend is currently building a passivhaus. We will still take the three pipes, via the roof cavity, straight up adjacent to the north gable. The pipes will exit near to the top of the roof into a space between the flat ceiling of bed 1 and the roof, From there they will pass above the flat ceiling of the bathroom roof with one going above the ceiling in bed 2. As the ceilings don't yet exist i will need to cut off the pipes at the required lengths and initially leave them dangling! I still propose that the ducts to pass through 95mm holes within boards attached to the rafter when entering and leaving the airtight roof space, to aid the taping of the ducts and ensuring that the membrane does not rip.
-
We are in the process of building our new house a 1.5 storey, well insulated house with MVHR. The timber framers are finishing the roof structure (400mm metal web rafters to be filled with cellulose fibre) and sarking is about to be fitted. MVHR ducts must be fitted next week per the framers ! We have a design for the MVHR which assumed that we could have ducts passing though the 400mm deep rafters, as suggested by the framing company early in the project. Unfortunately, the structural engineer added glulams that not only block ducts passing from the plant room to the south end of the house both in the joists and the roof joists . For most ducts we can bypass the glulams by moving from the joists up and over them within the boxed in section adjacent to the FF eaves. This sorts the down stairs ducts and all but 3 of the upstairs ducts. These relate to beds 1 and 2 as well as the bathroom. They will have to pass from the joists, within the boxed in eaves and through the roof rafters sometimes more than once (see photo). I am concerned that from an airtightness POV this will be a nightmare, as the roof airtight layer is Intello which will attached to the rafters and held in place by 50x25battens (to be covered by plaster board later). I have nightmares of long cuts or even worse – rips and endless airtightness tape. I can reduce the risk noted above by trying to persuade my wife that the vents could be on the sloping part of the ceiling or even the low wall that boxes in the eaves rather than the small flat area of ceiling in the bedrooms (-any thoughts). The use of the small wall would be easiest and would reduce the number of times the ducts will have to pass into the roof and therefore be sealed. I am also thinking of using offcuts of smartply with holes cut for the duct to be attached where the ducts will join and leave the roof to help with airtightness and to reduce the risks of rips. Although the plan shows a floor vent in the FF gable at the front of the house, We will revert to the original design of having supply 2 feeding the ground floor area within the front gable . My wife does not fancy a grill in the floor of her 'snug' Any suggestions would be appreciated? I will add photos of the roof shortly
-
We are due to pour our insulated reinforced raft next Friday. It is all ready except for 1) sealing and tying down a block of XPS attached to the waste pipe to give a void for the shower waste. - Do I need to cover in DPM?, - PU foam around the pipe to seal concrete out - Is tying down the XPS with wire OK. - Should I lift it up from the rebar mesh using concrete "mars bars" to help continuity of concrete and 2) How to protect the pipes under the manifold from over energetic power float operators! Possibly boxing out the area with plywood? Any suggestions on the above or the pour generally would be gratefully received.
-
Ground works for our new timber frame house starts in a weeks time. The highly insulated 1.5 storey house with a footprint of c.80m2 will be on an insulated reinforced raft, 270mm deep concrete with wet UFH attached to the mesh. The concrete will be power floated to provide a surface for tiling. The water temperature in the UFH should be quite low due to the low heating demand (2kw when outdoor temperature is -9C.) ASHP. I have to order my windows and doors early next week and need spacers under the door threshold to provide for finished floor level. We therefore need to work out an appropriate depth of these spacers to retain a reasonably flat threshold to comply with Part M. We intend using large format porcelain tiles (as yet not chosen) throughout most of the ground floor - except the shower room but am unsure whether I need to allow for decoupling membrane (as recommended by tilers). Taking account of this , how many mm should we allow for the finished floor? The tiler has suggested 17-20mm. Also , how long will it be before I can get it tiled as it is a very thick raft? and should I put the UFH on first. I would appreciate your thoughts as to anything else I should be considering? Many thanks in advance
-
Suitable sun tunnels for a bathroom
Smallholdertoo replied to Smallholdertoo's topic in Skylights & Roof Windows
In a word No! Although it s only a periscope of sorts , it needs to be a1rtight and thermally functional and aesthetically attractive both internally and out. Maybe worth the effort if i needed 5. Thanks for your help. -
Suitable sun tunnels for a bathroom
Smallholdertoo replied to Smallholdertoo's topic in Skylights & Roof Windows
Contacted Monodraught. They agreed that their Sunpipe is not designed to be airtight, Solatube however do have a passiv house standard version of their product that has 0.5w/m2k u-value and gaskets to ensure that airtightness. So I am probably going down this route. -
Suitable sun tunnels for a bathroom
Smallholdertoo replied to Smallholdertoo's topic in Skylights & Roof Windows
Many thanks I will contact them on Monday